Das Vakuumhärten ist ein spezielles Wärmebehandlungsverfahren zur Verbesserung der mechanischen Eigenschaften von Metallwerkstücken, wie Härte, Verschleißfestigkeit und Festigkeit, bei gleichzeitiger Minimierung von Oberflächenoxidation und Verunreinigung.Bei diesem Verfahren wird das Werkstück in einer Vakuumumgebung auf eine bestimmte Temperatur erhitzt, auf dieser Temperatur gehalten, um eine gleichmäßige Erwärmung zu erreichen, und dann unter Verwendung von Inertgasen schnell abgekühlt.Die Vakuumumgebung gewährleistet eine saubere, oxidationsfreie Oberfläche, die für die Erzielung hochwertiger Ergebnisse entscheidend ist.Der Prozess ist hochgradig kontrolliert und nutzt fortschrittliche Vakuumsysteme, Heizmechanismen und Kühltechniken, um Präzision und Konsistenz zu gewährleisten.
Die wichtigsten Punkte werden erklärt:
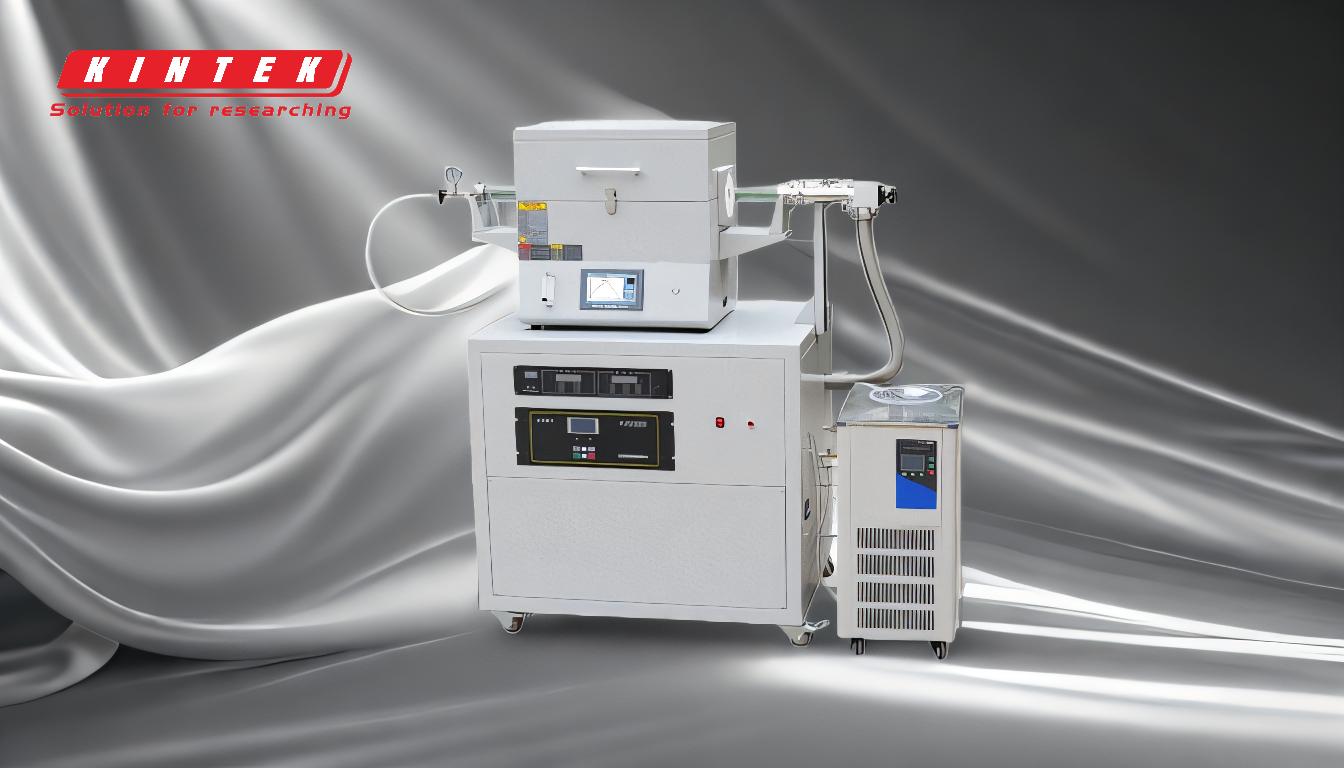
-
Vakuum-Umgebung Erzeugung:
- Der Prozess beginnt mit der Erzeugung eines Vakuums im Vakuum-Härteofen .Dies wird durch eine Kombination von Vakuumpumpen erreicht, darunter mechanische Pumpen, Druckerhöhungspumpen und Diffusionspumpen.
- Mechanische Pumpen werden zunächst eingesetzt, um den Druck von atmosphärischen Werten (etwa 105 Torr) auf etwa 10 Torr zu senken.Unterhalb von 20 Torr sinkt der Wirkungsgrad der mechanischen Pumpen, und es werden Booster-Pumpen eingesetzt, um den Druck weiter zu senken.
- Dann werden Diffusionspumpen eingesetzt, um ein Höchstvakuum zu erreichen, das in der Regel bei etwa 7 × 10^-3 Pa liegt und für die Vermeidung von Oxidation und Verunreinigung während der Heizphase unerlässlich ist.
-
Aufheizphase:
- Die Erwärmung in einem Vakuumofen erfolgt hauptsächlich durch Strahlung.Das Werkstück wird gleichmäßig erwärmt, indem der richtige Abstand innerhalb der Ofenkammer eingehalten wird.Dies verhindert eine ungleichmäßige Erwärmung und gewährleistet gleichbleibende Materialeigenschaften.
- Die Temperatur wird mithilfe automatischer Temperaturkontrollinstrumente sorgfältig gesteuert.Das Werkstück wird je nach Material und gewünschten Eigenschaften auf eine bestimmte Temperatur erhitzt und für eine bestimmte Zeit auf dieser Temperatur gehalten, um eine gleichmäßige Wärmeverteilung zu gewährleisten.
-
Abkühlungsphase:
- Nach der Erwärmungsphase wird das Werkstück schnell abgekühlt, um die gewünschte Härte zu erreichen.Dazu wird ein Inertgas, z. B. Argon, in die Vakuumkammer eingeleitet.Das Gas wird mit einer kontrollierten Geschwindigkeit hineingepumpt, um eine präzise Abkühlung zu gewährleisten.
- Der schnelle Abkühlungsprozess, auch Abschrecken genannt, ist entscheidend für das Erreichen der gewünschten Mikrostruktur und der mechanischen Eigenschaften des Werkstücks.Das Inertgas sorgt dafür, dass der Abkühlungsprozess frei von Oxidation und Verunreinigung ist.
-
Leckmanagement und Wartung:
- Die Aufrechterhaltung der Integrität der Vakuumumgebung ist entscheidend für den Erfolg des Prozesses.Jedes Leck im Ofen kann das Vakuum beeinträchtigen und zu Oxidation oder Verunreinigung führen.
- Vorübergehende Lecks können mit Hochtemperatur-Dichtmitteln abgedichtet werden, während der Ofen in Betrieb ist.Sobald der Ofen jedoch abgeschaltet ist, sollte eine gründliche Inspektion und Reparatur durchgeführt werden.Dazu gehören das Schweißen gerissener Teile, das Ersetzen gealterter oder beschädigter Dichtungen und Sprengringe sowie das Nachziehen loser Schrauben.
-
Prozessautomatisierung und -steuerung:
- Der gesamte Prozess des Vakuumhärtens ist hochgradig automatisiert, mit präziser Steuerung der Temperatur, des Vakuumniveaus und der Abkühlgeschwindigkeit.Dies gewährleistet die Wiederholbarkeit und Konsistenz des Wärmebehandlungsprozesses.
- Automatisierte Systeme überwachen und justieren die Parameter in Echtzeit und stellen sicher, dass das Werkstück genau die Behandlung erfährt, die erforderlich ist, um die gewünschten Eigenschaften zu erzielen.
-
Anwendungen und Vorteile:
- Das Vakuumhärten wird in vielen Branchen eingesetzt, in denen Hochleistungskomponenten benötigt werden, z. B. in der Luft- und Raumfahrt, der Automobilindustrie und der Werkzeugherstellung.Das Verfahren ist besonders vorteilhaft für Werkstoffe, die anfällig für Oxidation sind oder ein hohes Maß an Präzision bei der Wärmebehandlung erfordern.
- Zu den wichtigsten Vorteilen des Vakuumhärtens gehören eine bessere Oberflächenqualität, verbesserte mechanische Eigenschaften und ein geringerer Verzug im Vergleich zu herkömmlichen Wärmebehandlungsmethoden.
Durch Befolgung dieser Schritte und Nutzung der Möglichkeiten eines Vakuum-Härteofens können Hersteller hervorragende Ergebnisse bei der Wärmebehandlung erzielen und sicherstellen, dass ihre Bauteile den höchsten Qualitäts- und Leistungsstandards entsprechen.
Zusammenfassende Tabelle:
Schritt | Beschreibung |
---|---|
Erzeugung von Vakuum | Verwenden Sie mechanische, Booster- und Diffusionspumpen, um ein hohes Vakuum zu erreichen. |
Erwärmungsphase | Gleichmäßige Erwärmung des Werkstücks durch Strahlung in einer kontrollierten Vakuumumgebung. |
Abkühlungsphase | Schnelles Abkühlen mit Inertgasen wie Argon, um die gewünschte Härte zu erreichen. |
Leckage-Management | Inspektion und Reparatur von Leckagen zur Aufrechterhaltung der Vakuumintegrität. |
Automatisierung und Kontrolle | Nutzen Sie automatisierte Systeme für eine präzise Temperatur-, Vakuum- und Kühlungssteuerung. |
Anwendungen | Ideal für die Luft- und Raumfahrt, die Automobilindustrie und den Werkzeugbau. |
Entdecken Sie, wie das Vakuumhärten Ihre Metallkomponenten aufwerten kann. Kontaktieren Sie uns noch heute für fachkundige Beratung!