Das PVD-Prozessgas (Physical Vapor Deposition) ist eine entscheidende Komponente bei der Abscheidung dünner Schichten auf Substraten.Das primär verwendete Gas ist Argon, das inert ist und den notwendigen Impuls liefert, um Atome aus dem Zielmaterial zu lösen.Zusätzlich werden reaktive Gase wie Sauerstoff, Stickstoff und Methan zugeführt, um mit dem verdampften Material Verbindungen zu bilden, die zu Beschichtungen wie Metalloxiden, Nitriden und Karbiden führen.Das Verfahren findet in einer Vakuumumgebung statt, in der das Gas ionisiert wird, um ein Plasma zu erzeugen, das die Abscheidung von Atomen auf dem Substrat erleichtert.Diese Methode wird häufig zur Verbesserung von Oberflächeneigenschaften wie Härte, Oxidationsbeständigkeit und Reibungsreduzierung eingesetzt.
Die wichtigsten Punkte werden erklärt:
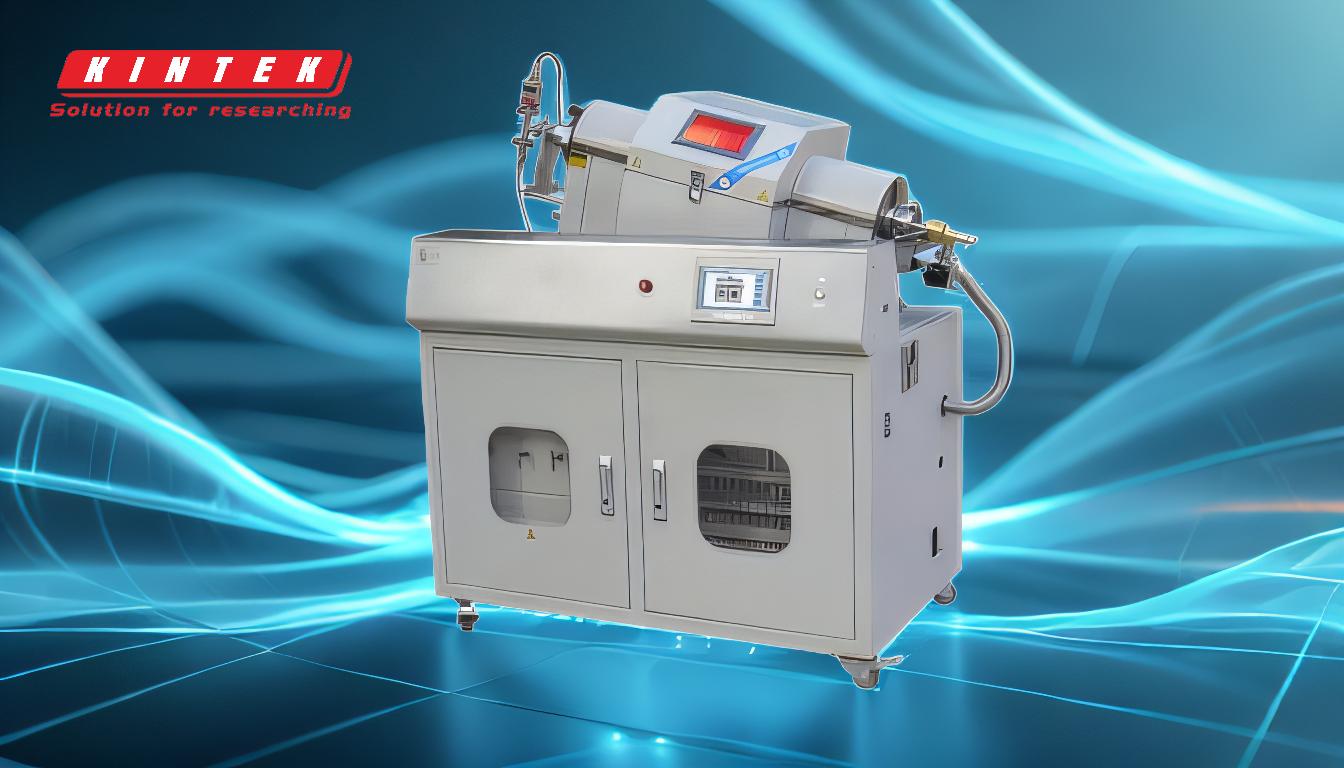
-
Primäres Prozessgas - Argon:
- Argon ist das am häufigsten verwendete Gas im PVD-Verfahren, da es inert ist und einen ausreichenden Impuls zum Sputtern von Atomen aus dem Zielmaterial erzeugen kann.
- Es wird in der Anfangsphase verwendet, um eine Plasmaumgebung zu schaffen, die das Gas ionisiert und eine effiziente Energieübertragung auf das Zielmaterial ermöglicht.
- Argon spielt eine entscheidende Rolle beim Sputtern, bei dem es das Zielmaterial beschießt, wodurch Atome herausgeschleudert werden und sich anschließend auf dem Substrat ablagern.
-
Reaktive Gase - Sauerstoff, Stickstoff und Methan:
- In der Transportphase des PVD-Verfahrens werden reaktive Gase zugeführt, die mit den verdampften Metallatomen reagieren.
- Sauerstoff wird zur Bildung von Metalloxiden verwendet, die die Oxidationsbeständigkeit und andere Oberflächeneigenschaften verbessern können.
- Stickstoff wird zur Herstellung von Metallnitriden verwendet, die für ihre Härte und Verschleißfestigkeit bekannt sind.
- Methan wird zur Herstellung von Metallkarbiden verwendet, die wegen ihrer hohen Härte und thermischen Stabilität geschätzt werden.
- Diese reaktiven Gase spielen eine wichtige Rolle bei der Anpassung der Eigenschaften der endgültigen Beschichtung an die spezifischen Anwendungsanforderungen.
-
Plasmaerzeugung und Ionisierung:
- Das PVD-Verfahren beginnt mit der Erzeugung eines Plasmas aus dem Prozessgas, häufig unter Verwendung einer induktiv gekoppelten Plasmaquelle (ICP).
- Die hochenergetischen Elektronen im Plasma stoßen mit den Gasmolekülen zusammen, wodurch diese in Atome und Ionen dissoziieren.
- Dieser Ionisierungsprozess ist für die effiziente Energieübertragung und die anschließende Abscheidung des Beschichtungsmaterials auf dem Substrat unerlässlich.
-
Vakuum Umgebung:
- Das PVD-Verfahren wird unter Vakuumbedingungen durchgeführt, um Verunreinigungen zu minimieren und eine kontrollierte Umgebung für die Abscheidung von dünnen Schichten zu gewährleisten.
- Die Vakuumumgebung ermöglicht eine effiziente Bewegung der verdampften Atome vom Target zum Substrat ohne Störung durch atmosphärische Gase.
- Der niedrige Druck trägt ebenfalls dazu bei, eine gleichmäßige und hochwertige Beschichtung auf dem Substrat zu erzielen.
-
Abscheidung und Beschichtungsbildung:
- Die verdampften Atome oder Moleküle wandern durch die Vakuumkammer und lagern sich auf dem Substrat ab, wo sie kondensieren und einen dünnen Film bilden.
- Der Abscheidungsprozess kann durch die Einführung reaktiver Gase beeinflusst werden, die mit dem verdampften Material reagieren und Verbindungen mit spezifischen Eigenschaften bilden.
- Die resultierenden Beschichtungen können je nach den Anforderungen der Anwendung von nanoskaligen bis zu sichtbaren Dicken reichen.
-
Anwendungen und Vorteile:
- PVD-Beschichtungen werden in verschiedenen Industriezweigen eingesetzt, um die Leistung von Bauteilen durch Verbesserung von Eigenschaften wie Härte, Verschleißfestigkeit und Oxidationsbeständigkeit zu verbessern.
- Die Möglichkeit, verschiedene Materialien einzubringen und die Beschichtungseigenschaften anzupassen, macht PVD zu einer vielseitigen und wertvollen Technik in der Oberflächentechnik.
- Das Verfahren ist außerdem umweltfreundlich, da keine gefährlichen Chemikalien verwendet werden und nur wenig Abfall entsteht.
Zusammenfassend lässt sich sagen, dass das PVD-Prozessgas, in erster Linie Argon, zusammen mit reaktiven Gasen wie Sauerstoff, Stickstoff und Methan, eine entscheidende Rolle bei der Abscheidung von Dünnschichten mit maßgeschneiderten Eigenschaften spielt.Der Prozess wird in einer Vakuumumgebung durchgeführt, in der die Plasmaerzeugung und Ionisierung die effiziente Übertragung des Materials vom Target auf das Substrat erleichtern.Die daraus resultierenden Beschichtungen bieten erhebliche Vorteile in Bezug auf die Oberflächeneigenschaften und werden in verschiedenen Branchen eingesetzt.
Zusammenfassende Tabelle:
Hauptaspekt | Einzelheiten |
---|---|
Primärgas (Argon) | Inertes Gas, das zum Sputtern und zur Plasmaerzeugung verwendet wird. |
Reaktive Gase | Sauerstoff, Stickstoff und Methan bilden Metalloxide, Nitride und Karbide. |
Plasmaerzeugung | Durch Ionisierung von Gas entsteht ein Plasma für eine effiziente Energieübertragung. |
Vakuum-Umgebung | Gewährleistet eine kontaminationsfreie, gleichmäßige Beschichtung. |
Anwendungen | Verbessert die Härte, Verschleißfestigkeit und Oxidationsbeständigkeit von Beschichtungen. |
Entdecken Sie, wie PVD-Prozessgase Ihre Oberflächentechnik optimieren können. Kontaktieren Sie unsere Experten noch heute !