Die Sputterbeschichtung ist eine weit verbreitete Technik in verschiedenen Branchen, darunter Elektronik, Optik und Materialwissenschaften, zur Abscheidung dünner Filme auf Substraten. Die Notwendigkeit eines Vakuums bei der Sputterbeschichtung ist von grundlegender Bedeutung für den Erfolg des Prozesses. Eine Vakuumumgebung stellt sicher, dass aus dem Zielmaterial ausgestoßene Atome ungehindert zum Substrat gelangen können, wodurch Kollisionen mit Gasmolekülen minimiert werden, die andernfalls die Atome zerstreuen und die Qualität der Beschichtung beeinträchtigen könnten. Darüber hinaus ist die Aufrechterhaltung des richtigen Drucks entscheidend für die Aufrechterhaltung des zum Sputtern erforderlichen Plasmas. Ein zu niedriger Druck führt zu unzureichenden Kollisionen, um das Plasma aufrechtzuerhalten, während ein zu hoher Druck zu übermäßigen Kollisionen führt und verhindert, dass Elektronen genügend Energie gewinnen, um Atome effektiv zu ionisieren. Dieses Gleichgewicht ist für die Erzielung qualitativ hochwertiger, gleichmäßiger Beschichtungen unerlässlich.
Wichtige Punkte erklärt:
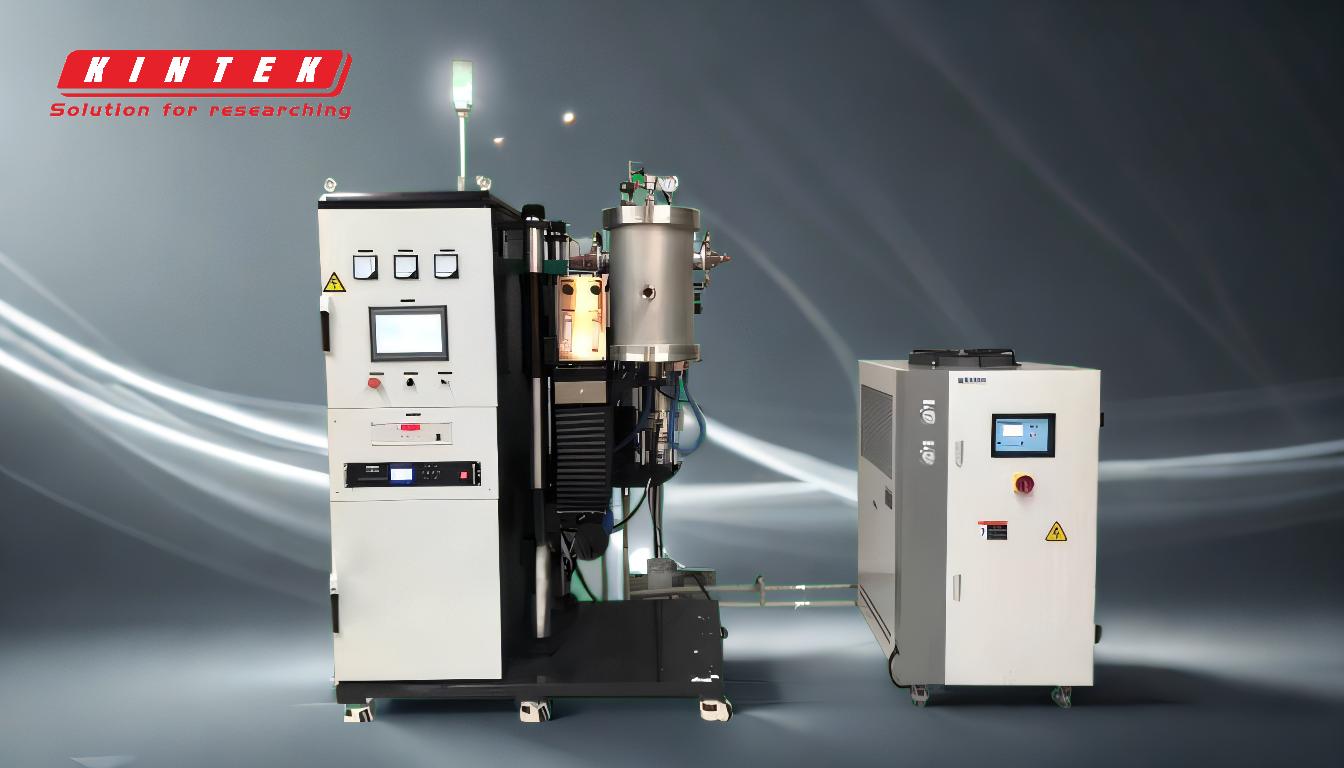
-
Minimierung der Atomstreuung:
- Im Vakuum wird die mittlere freie Weglänge der aus dem Sputtertarget ausgeworfenen Atome deutlich erhöht. Dies bedeutet, dass Atome direkt zum Substrat wandern können, ohne von Gasmolekülen gestreut zu werden. In einer Umgebung ohne Vakuum würden häufige Kollisionen mit Luftmolekülen dazu führen, dass die Atome von ihrer vorgesehenen Bahn abweichen, was zu ungleichmäßigen oder minderwertigen Beschichtungen führen würde.
-
Plasma aufrechterhalten:
- Die Sputterbeschichtung beruht auf der Erzeugung eines Plasmas, einem stark ionisierten Gas, das freie Elektronen und Ionen enthält. Das Plasma ist für den Beschuss des Zielmaterials mit Ionen unerlässlich, wodurch Atome herausgeschleudert werden. Eine Vakuumumgebung trägt zur Aufrechterhaltung des Plasmas bei, indem sie sicherstellt, dass Elektronen ausreichend Energie gewinnen können, um Gasatome zu ionisieren. Wenn der Druck zu hoch ist, verlieren Elektronen durch übermäßige Kollisionen Energie, was es schwierig macht, das Plasma aufrechtzuerhalten.
-
Kontamination verhindern:
- Eine Vakuumumgebung reduziert das Vorhandensein von Verunreinigungen wie Sauerstoff, Wasserdampf und anderen reaktiven Gasen erheblich. Diese Verunreinigungen können mit den gesputterten Atomen reagieren und Oxide oder andere Verbindungen bilden, die die Qualität des Dünnfilms beeinträchtigen. Durch den Betrieb im Vakuum bleibt die Reinheit des abgeschiedenen Materials erhalten, was zu einer besseren Leistung des beschichteten Produkts führt.
-
Kontrolle der Ablagerungsrate:
- Die Vakuumumgebung ermöglicht eine präzise Steuerung der Abscheidungsrate des Dünnfilms. Durch Anpassen des Drucks und der auf das Ziel ausgeübten Leistung können Bediener die Geschwindigkeit, mit der Atome auf dem Substrat abgeschieden werden, genau einstellen. Diese Kontrolle ist von entscheidender Bedeutung für Anwendungen, die bestimmte Dicken oder Eigenschaften der Beschichtung erfordern.
-
Verbesserung der Filmeinheitlichkeit:
- Gleichmäßigkeit ist bei vielen Anwendungen der Sputterbeschichtung von entscheidender Bedeutung, beispielsweise bei der Herstellung optischer Beschichtungen oder Halbleiterbauelemente. Ein Vakuum sorgt dafür, dass die gesputterten Atome gleichmäßig über das Substrat verteilt werden, was zu einem konsistenten und gleichmäßigen Film führt. Aufgrund der unvorhersehbaren Streuung der Atome ist diese Gleichmäßigkeit in einer Umgebung ohne Vakuum schwer zu erreichen.
-
Verbesserung der Haftung:
- Die Haftung des dünnen Films am Substrat ist ein weiterer kritischer Faktor, der von der Vakuumumgebung beeinflusst wird. Im Vakuum kann die Substratoberfläche effektiver gereinigt werden, häufig durch Ionenbeschuss, wodurch jegliche Verunreinigungen oder Oxide entfernt werden. Diese saubere Oberfläche ermöglicht eine bessere Bindung zwischen dem Substrat und dem abgeschiedenen Film und verbessert so die allgemeine Haltbarkeit und Leistung der Beschichtung.
Zusammenfassend lässt sich sagen, dass die Vakuumumgebung bei der Sputterbeschichtung von entscheidender Bedeutung ist, um die Qualität, Gleichmäßigkeit und Leistung der abgeschiedenen Dünnfilme sicherzustellen. Es minimiert die Atomstreuung, erhält das Plasma aufrecht, verhindert Kontaminationen, kontrolliert die Abscheidungsraten, verbessert die Gleichmäßigkeit des Films und verbessert die Haftung. Zusammengenommen machen diese Faktoren das Vakuum zu einer entscheidenden Komponente des Sputterbeschichtungsprozesses.
Übersichtstabelle:
Schlüsselfaktor | Rolle bei der Sputterbeschichtung |
---|---|
Minimierung der Atomstreuung | Stellt sicher, dass Atome direkt zum Substrat wandern, wodurch Kollisionen reduziert werden und gleichmäßige Beschichtungen entstehen. |
Plasma aufrechterhalten | Erhält die Plasmastabilität, indem es Elektronen ermöglicht, Gasatome effektiv zu ionisieren. |
Kontamination verhindern | Reduziert reaktive Gase und bewahrt die Reinheit und Leistung des Dünnfilms. |
Kontrolle der Ablagerungsrate | Ermöglicht eine präzise Abstimmung der Beschichtungsdicke und -eigenschaften. |
Verbesserung der Filmeinheitlichkeit | Gewährleistet eine gleichmäßige Verteilung der Atome für konsistente, hochwertige Beschichtungen. |
Verbesserung der Haftung | Bietet eine saubere Substratoberfläche für bessere Haftung und Haltbarkeit. |
Möchten Sie hochwertige Sputterbeschichtungen erzielen? Kontaktieren Sie noch heute unsere Experten für maßgeschneiderte Lösungen!