Einführung
Inhaltsverzeichnis
Einer der wichtigsten Prozesse bei der Herstellung hochwertiger Keramikbauteile ist das isostatische Pressen. Diese Technik gewährleistet die Gleichmäßigkeit und Präzision, die für die Herstellung von Keramik für verschiedene Industriezweige erforderlich sind. Beim isostatischen Pressen müssen die Presspulver sorgfältig ausgewählt und die Werkzeuge gesteuert werden, um die gewünschte Gleichmäßigkeit zu erreichen. Ein weiterer Schlüsselfaktor in diesem Prozess ist die Optimierung des Sinterprozesses, der einen großen Einfluss auf die physikalischen Eigenschaften der Keramik hat. Durch das Verständnis des Prozesses des isostatischen Pressens können Hersteller die Produktion von Keramik sicherstellen, die den strengen Standards für Maßgenauigkeit und Leistung entspricht.
Der Prozess des halbisostatischen Pressens
Bedeutung der Presseinheitlichkeit
Beim halbisostatischen Pressverfahren werden Produkte in einen geschlossenen, mit Flüssigkeit gefüllten Behälter gegeben und auf allen Oberflächen dem gleichen Druck ausgesetzt. Diese Hochdruckumgebung erhöht die Dichte der Produkte und verleiht ihnen die gewünschte Form. Halbisostatische Pressen werden häufig bei der Formung von feuerfesten Hochtemperaturmaterialien, Keramik, Hartmetall, Lanthan-Permanentmagneten, Kohlenstoffmaterialien und seltenen Metallpulvern eingesetzt.
Rolle der sorgfältigen Auswahl von Presspulvern und Werkzeugsteuerungen
Beim halbisostatischen Pressen ist eine sorgfältige Auswahl der Presspulver und Werkzeugkontrollen erforderlich, um das gewünschte Ergebnis sicherzustellen. Im Gegensatz zu anderen pulvermetallurgischen Verfahren bietet das halbisostatische Pressen mehrere Vorteile, darunter eine gleichmäßige Verdichtung in alle Richtungen und eine gleichmäßigere Enddichte der Komponenten. Allerdings müssen Hersteller die Eigenschaften des im Prozess verwendeten Metallpulvers sorgfältig charakterisieren, um optimale Endeigenschaften des Bauteils zu erzielen. Die Materialcharakterisierung ist entscheidend, um die gewünschte Qualität und Leistung des Endprodukts sicherzustellen.
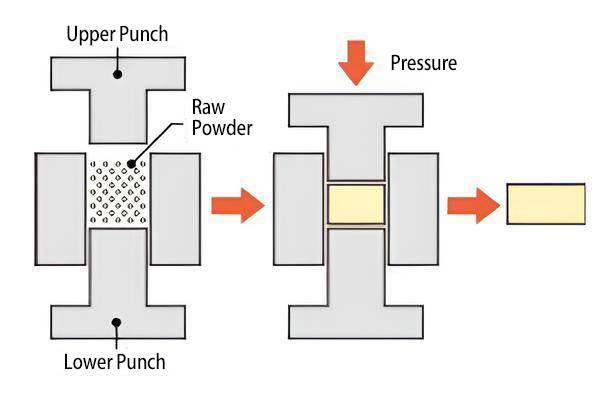
Einfluss eines optimierten Sinterprozesses auf die physikalischen Eigenschaften
Der optimierte Sinterprozess bestimmt maßgeblich die physikalischen Eigenschaften der semiisostatisch gepressten Bauteile. Isostatisches Pressen ermöglicht die Herstellung verschiedenster Werkstoffe aus Pulverpresslingen durch Reduzierung der Porosität der Pulvermischung. Die Pulvermischung wird durch isostatischen Druck verdichtet und verkapselt, wobei der Druck aus allen Richtungen gleichmäßig ausgeübt wird. Dieser Einschluss des Metallpulvers in einer flexiblen Membran oder einem hermetischen Behälter gewährleistet eine gleichmäßige Verdichtung und Dichte innerhalb des verdichteten Teils.
Das isostatische Pressverfahren hat sich im Laufe der Jahre weiterentwickelt und wird heute in verschiedenen Branchen eingesetzt, darunter Keramik, Metalle, Verbundwerkstoffe, Kunststoffe und Kohlenstoff. Es bietet einzigartige Vorteile für Keramik- und Feuerfestanwendungen, ermöglicht eine präzise Formgebung der Produkte und reduziert den Bedarf an kostspieliger Bearbeitung. Der beim isostatischen Pressen ausgeübte Rundumdruck sorgt für eine gleichmäßige Verdichtung und Dichte und räumt Bedenken hinsichtlich Dichteschwankungen bei herkömmlichen Verarbeitungsmethoden aus. Isostatisches Pressen eignet sich besonders für die Herstellung größerer Teile, Teile mit einem hohen Verhältnis von Dicke zu Durchmesser und Teile, die hervorragende Materialeigenschaften erfordern.
Es gibt zwei Hauptkategorien des isostatischen Pressens: kaltisostatisches Pressen (CIP) und heißisostatisches Pressen (HIP). Beim CIP wird isostatischer Druck auf das lose Pulver bei Raumtemperatur ausgeübt, während beim HIP isostatischer Druck auf das Pulver ausgeübt wird, wenn es in einer Verpackung erhitzt wird. HIP nutzt ein Inertgas als Druckübertragungsmedium. Beim heißisostatischen Pressverfahren wird das Pulver in einen Hochdruckbehälter gegeben, einer hohen Temperatur und einem ausgeglichenen Druck ausgesetzt und zu kompakten Teilen gesintert. Im Vergleich zu anderen Verfahren wie dem Heißpressen bietet das heißisostatische Pressen niedrigere Sintertemperaturen und eine höhere Produktdichte.
Zusammenfassend lässt sich sagen, dass das halbisostatische Pressverfahren einzigartige Vorteile hinsichtlich der Gleichmäßigkeit des Pressens und der endgültigen Bauteildichte bietet. Eine sorgfältige Auswahl der Presspulver und Werkzeugsteuerung sowie die Optimierung des Sinterprozesses sind entscheidend für das Erreichen der gewünschten physikalischen Eigenschaften. Das isostatische Pressverfahren hat sich in verschiedenen Branchen zu einem wertvollen Werkzeug entwickelt und ermöglicht die Herstellung hochwertiger Komponenten mit präzisen Formen und hervorragenden Materialeigenschaften.
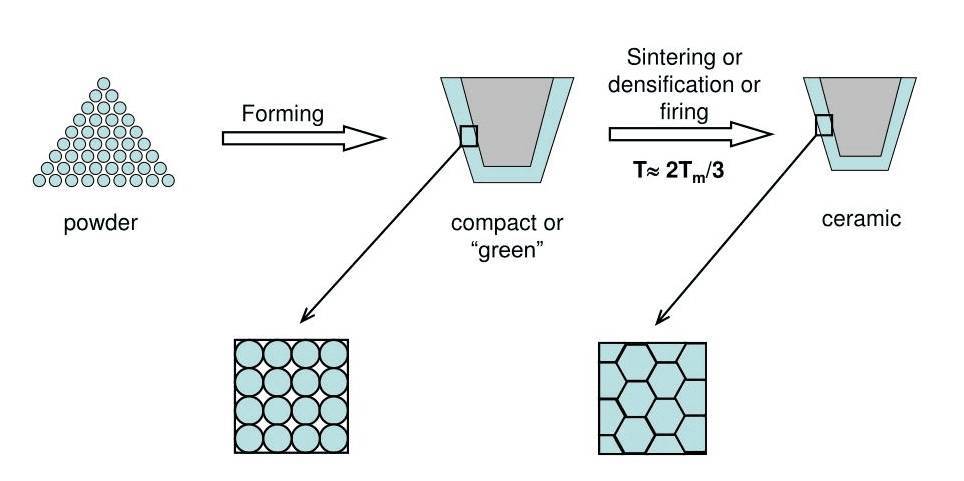
Rolle maßgeschneiderter Sintertechniken
Erreichen von Linearität und Konzentrizität
Das Sintern ist ein entscheidender Prozess bei der Herstellung keramischer Bauteile. Maßgeschneiderte Sintertechniken spielen eine entscheidende Rolle bei der Erzielung von Linearität und Konzentrizität dieser Komponenten.
Ein Vorteil des Sinterns bei Raumtemperatur besteht darin, dass es die Herstellung großformatiger Targets ermöglicht, ohne durch die Gerätegröße eingeschränkt zu sein. Diese Methode bietet außerdem geringe Investitionen in die Ausrüstung, niedrige Produktionskosten, eine hohe Produktionseffizienz, eine hervorragende Zielleistung und eine einfache industrielle Produktion. Es eignet sich besonders für die Leistungsanforderungen beschichteter Targets für High-End-Displays.
Allerdings hat das Sintern bei Raumtemperatur auch seine Schwächen. Es gilt im Vergleich zu anderen als das schwierigste Sinterverfahren. Um einen dichten Sinterkörper zu erreichen, wird häufig ein Sinterhilfsmittel zugesetzt. Das Entfernen des Sinterhilfsmittels aus dem Sinterkörper kann jedoch eine Herausforderung sein, was zu einer geringeren Produktreinheit führt. Darüber hinaus müssen strenge Anforderungen an Form, Partikelgröße und Partikelgrößenverteilung des Pulvers erfüllt werden. Zur Erfüllung dieser Anforderungen werden üblicherweise Pulververarbeitungstechniken wie Kugelmahlen, Strahlmahlen und Sedimentationsklassierung eingesetzt. Schließlich sind die durch Sintern bei Raumtemperatur hergestellten Targets im Allgemeinen dünn.
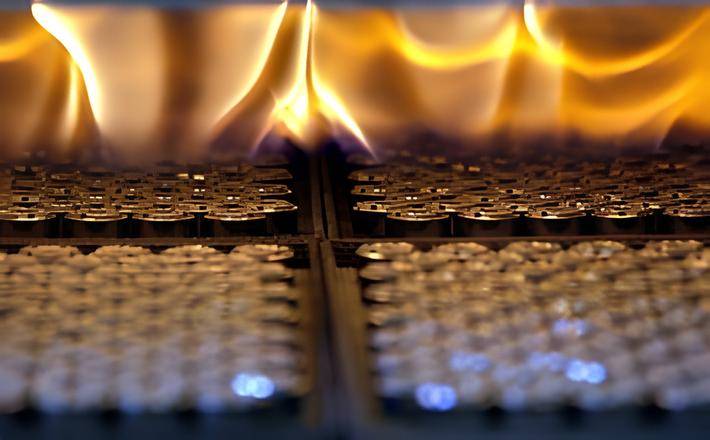
Eignung zur Herstellung verschiedener Keramikbauteile
Sintern ist ein vielseitiges Verfahren, das bei der Herstellung keramischer Bauteile mehrere Vorteile bietet. Hier sind einige wichtige Vorteile:
Komplexe Formen : Das Sintern von Metall ermöglicht die Schaffung komplexer Formen, die mit anderen Methoden nur schwer oder gar nicht herzustellen wären. Diese Fähigkeit eröffnet Möglichkeiten für innovative Designs und funktionale Komponenten.
Hohe Maßgenauigkeit : Sintern bietet eine hohe Maßgenauigkeit und stellt sicher, dass das Endprodukt genau der gewünschten Form entspricht. Diese Präzision ist entscheidend bei Anwendungen, bei denen enge Toleranzen erforderlich sind.
Zuverlässigkeit und Wiederholbarkeit der Großserienproduktion : Sintern ist ein zuverlässiger Prozess, der konsistente Endprodukte produziert. Dies macht es ideal für Großserienproduktionen, bei denen es auf Konsistenz und Einheitlichkeit ankommt.
Selbstschmierung : Durch Sintern können Teile mit selbstschmierenden Eigenschaften entstehen. Das verdichtete Pulver bildet eine dichte Bindung zwischen den Partikeln und reduziert so Reibung und Verschleiß. Diese Eigenschaft ist bei Anwendungen wertvoll, bei denen die Schmierung schwierig oder unerwünscht ist.
Einzigartige und isotrope Materialien : Durch Sintern werden einzigartige isotrope Materialien hergestellt, was bedeutet, dass sie in allen Richtungen die gleichen Eigenschaften besitzen. Diese Materialien zeichnen sich durch eine hohe Haltbarkeit und hervorragende Festigkeit aus und eignen sich daher für Anwendungen, die Robustheit erfordern.
Grüne Technologie : Sintern gilt als umweltfreundliche Technologie, da es keine schädlichen Emissionen erzeugt. Dies macht es zu einer umweltfreundlichen Wahl für Unternehmen, die ihre Umweltbelastung reduzieren möchten.
Vibrationsdämpfung : Durch Sintern können Teile mit vibrationsdämpfenden Eigenschaften hergestellt werden. Das verdichtete Pulver bildet eine dichte Verbindung, wodurch Vibrationen und Lärm reduziert werden. Diese Eigenschaft ist bei Anwendungen von Vorteil, bei denen die Vibrationskontrolle von entscheidender Bedeutung ist.
Verschiedene Keramikteile
Das Sintern von Metallen findet in verschiedenen Branchen Anwendung, darunter in der Herstellung elektrischer Komponenten, Halbleiter und optischer Fasern. Es erhöht die Festigkeit, Leitfähigkeit und Lichtdurchlässigkeit von Metallen und macht sie für diese Branchen geeignet.
Beim Keramiksintern wird das Verfahren zur Herstellung von Keramikgegenständen, einschließlich Töpferwaren, eingesetzt. Dabei wird das Material verfestigt, die Porosität verringert und die Dichte erhöht. Keramische Rohstoffe benötigen vor dem Sintern häufig organische Zusätze zur Verbesserung der Plastizität. Hohe Temperaturen, Druck oder elektrische Ströme treiben den Sinterprozess voran.
Für die Herstellung von Grünkörpern aus Keramik und Metallen wurden moderne Methoden der Pulverformung wie isostatisches Pressen, Schlickergießen, Extrudieren, Bandgießen und 3D-Drucken entwickelt. Anschließend wird der Grünkörper durch einen Sinterprozess erhitzt, wodurch die Porosität verringert und die Dichte erhöht wird.
Sinterprozesse werden durch thermisch aktivierte Festkörperdiffusionsmechanismen gesteuert. Diese Mechanismen können durch die Entwicklung von Sintermodellen mithilfe von Instrumenten wie Schubstangendilatometern quantifiziert werden.
Mikrowellen-Sintergeräte werden in industriellen Anwendungen häufig zum Sintern verschiedener hochwertiger Keramiken eingesetzt, darunter Lithiumkobaltoxid, Siliziumnitrid, Siliziumkarbid, Aluminiumoxid, Aluminiumnitrid, Zirkoniumoxid, Magnesiumhydroxid, Aluminium, Zink, Kaolin, Kobaltsulfat und Kobalt Oxalat und Vanadiumoxid. Es wird auch beim Sintern elektronischer Keramikgeräte wie piezoelektrischer PZT-Keramik und Varistoren verwendet.
Insgesamt spielen maßgeschneiderte Sintertechniken eine entscheidende Rolle bei der Erzielung von Linearität und Konzentrizität in Keramikbauteilen. Sie bieten zahlreiche Vorteile, darunter die Fähigkeit zur Herstellung komplexer Formen, hohe Maßgenauigkeit, Zuverlässigkeit in der Großserienproduktion, Selbstschmierung, einzigartige isotrope Materialien, umweltfreundliche Technologie und Dämpfung von Vibrationen. Metallsintern findet in verschiedenen Branchen Anwendung, während Keramiksintern in der Töpferei und anderen Keramikherstellungsprozessen eingesetzt wird. Mikrowellen-Sintergeräte werden in industriellen Anwendungen häufig zum Sintern verschiedener Keramiken und elektronischer Keramikgeräte eingesetzt.
Dimensionsfähigkeit und Präzision
Standardbereich an Abmessungsmöglichkeiten
Die Dimensionierungsfähigkeiten eines Beschichtungssystems spielen eine entscheidende Rolle bei der Bestimmung seiner Eignung für verschiedene Anwendungen. In Forschungs- und Entwicklungsumgebungen ist Flexibilität ein Schlüsselfaktor. Das System sollte in der Lage sein, verschiedene Materialien, Substratgrößen, Temperaturbereiche, Ionenflüsse, Abscheidungsraten, Frequenzen, Endpunkte und Druckbetriebsbereiche zu bewältigen. Dies ermöglicht das Experimentieren und die Anpassung an sich ändernde Prioritäten. Darüber hinaus spielen auch Budgetaspekte eine Rolle, da die Kosten für Systeme je nach Technologieoptionen erheblich variieren können.
Präzision im gebrannten Zustand
Präzision ist ein entscheidender Faktor bei Depositionssystemen. Beispielsweise wird Diamant aufgrund seiner extremen Härte und Dimensionsstabilität häufig bei der Mikrobearbeitung oder bei Ultrapräzisionsanwendungen als Werkzeugmaterial eingesetzt. Bei der Betrachtung der Präzision im gebrannten Zustand ist zu beachten, dass der Innendurchmesser innerhalb derselben Produktionscharge eine Toleranz von +/- 0,02 mm bei einer Wiederholgenauigkeit von weniger als 10 µm aufweisen kann.
Präzision nach dem Diamantschleifen
Das Diamantschleifen ist ein Prozess, der die Präzision bei Bearbeitungsanwendungen erheblich steigern kann. Nach dem Diamantschleifen kann die Länge des Werkstücks eine Toleranz von +/- 0,03 mm aufweisen, während der Außendurchmesser eine Toleranz von +/- 0,01 mm aufweisen kann. Darüber hinaus beträgt die erreichbare Mindestwandstärke 0,3 µm. Diese Präzision sorgt für hochwertige Werkstückergebnisse.
Diamantschneidwerkzeuge können entweder mit massivem Diamant (Einkristall, CVD-Diamant, PKD) oder mit Diamantbeschichtungen hergestellt werden. Standard-Diamant-Schleifwerkzeuge werden durch das Aufkleben von Diamant-Einkristallen auf einen Grundkörper hergestellt. Alternativ gibt es eine neue Schleifschichttechnologie, bei der mikrokristalline Diamantschichten mit scharfen Kristallitspitzen chemisch aufgedampft werden. Diese scharfen Kanten tragen zur Effektivität des Schleifprozesses bei.
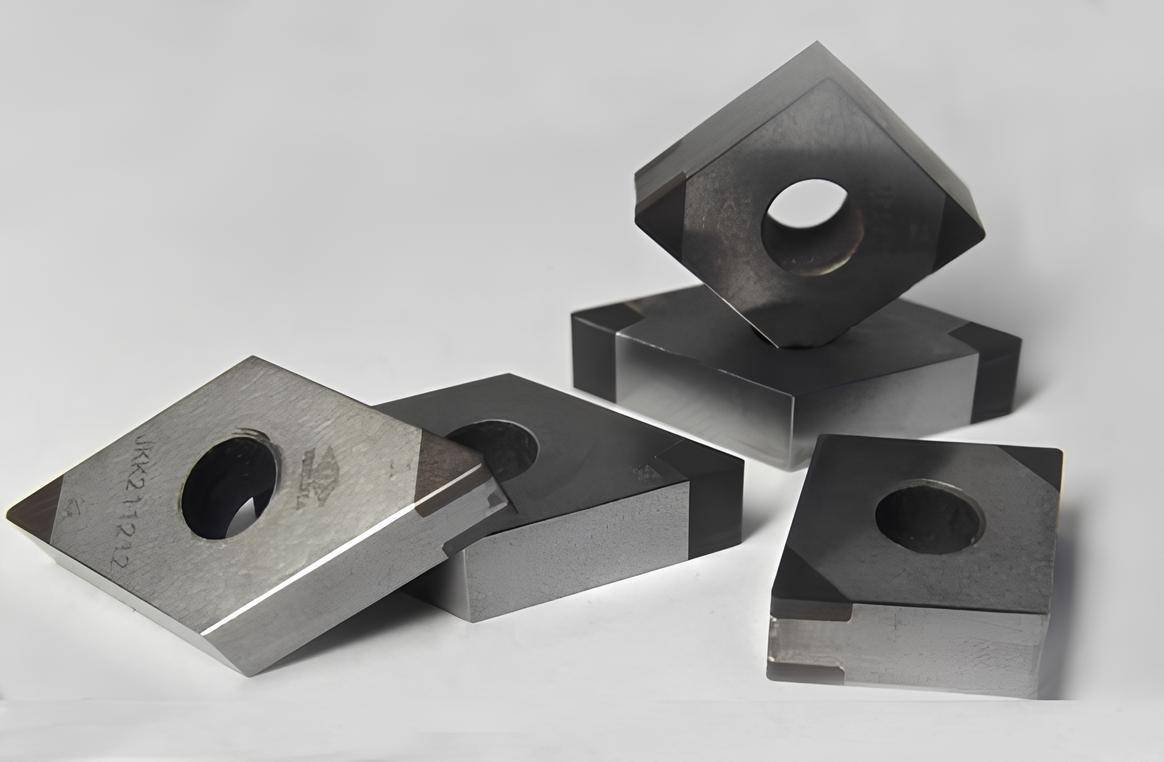
Mit der gleichen Beschichtungstechnologie können auch Mikroschleifwerkzeuge wie Schleifstifte und Frässtifte hergestellt werden. Selbst sehr kleine Werkzeuge mit Durchmessern von 50 mm wurden erfolgreich getestet.
Zusammenfassend lässt sich sagen, dass die Dimensionierungsfähigkeiten und die Präzision eines Beschichtungssystems entscheidende Faktoren sind, die in Forschungs- und Entwicklungsumgebungen berücksichtigt werden müssen. Das System sollte Flexibilität bieten und Experimente sowie die Anpassung an sich ändernde Prioritäten ermöglichen. Diamantschleifen kann die Präzision bei Bearbeitungsanwendungen erheblich verbessern und qualitativ hochwertige Ergebnisse gewährleisten. Ganz gleich, ob es sich um ein Standardspektrum an Abmessungsmöglichkeiten oder um die Präzision nach dem Diamantschleifen handelt, diese Faktoren tragen zur Gesamteffektivität und Effizienz des Beschichtungssystems bei.
Abschluss
Zusammenfassend lässt sich sagen, dass isostatisches Pressen ein entscheidender Prozess in der Keramikherstellung ist, der die Gleichmäßigkeit und Präzision von Keramikkomponenten gewährleistet. Durch die sorgfältige Auswahl der Presspulver und die Steuerung der Werkzeuge können Hersteller die gewünschte Gleichmäßigkeit der Presskeramik erreichen. Darüber hinaus werden durch die Optimierung des Sinterprozesses die physikalischen Eigenschaften der Keramik weiter verbessert. Maßgeschneiderte Sintertechniken spielen eine entscheidende Rolle bei der Erzielung von Linearität und Konzentrizität im Endprodukt, wodurch es für verschiedene Anwendungen geeignet ist. Darüber hinaus können die Abmessungsfähigkeiten und die Präzision von Keramiken standardisiert und eventuell erforderliche Anpassungen durch Diamantschleifen vorgenommen werden. Insgesamt sind isostatisches Pressen und maßgeschneiderte Sintertechniken für die Herstellung hochwertiger und präziser Keramikbauteile unerlässlich.
Wenn Sie an unseren Produkten interessiert sind, besuchen Sie bitte unsere Unternehmenswebsite: https://kindle-tech.com/product-categories/isostatic-press , wo Innovation seit jeher Priorität hat. Unser Forschungs- und Entwicklungsteam besteht aus erfahrenen Ingenieuren und Wissenschaftlern, die die Branchentrends genau verfolgen und ständig die Grenzen des Möglichen erweitern. Unsere Laborausrüstung ist mit modernster Technologie ausgestattet, um sicherzustellen, dass Sie bei Ihren Experimenten genaue und wiederholbare Ergebnisse erhalten. Von hochpräzisen Instrumenten bis hin zu intelligenten Steuerungssystemen bieten Ihnen unsere Produkte unbegrenzte Möglichkeiten für Ihre experimentelle Arbeit.
Kontaktieren Sie uns für eine kostenlose Beratung
Die Produkte und Dienstleistungen von KINTEK LAB SOLUTION werden von Kunden auf der ganzen Welt anerkannt. Unsere Mitarbeiter helfen Ihnen gerne bei allen Fragen weiter. Kontaktieren Sie uns für eine kostenlose Beratung und sprechen Sie mit einem Produktspezialisten, um die am besten geeignete Lösung für Ihre Anwendungsanforderungen zu finden!