Die chemische Gasphasenabscheidung (Chemical Vapor Deposition, CVD) ist ein hochentwickeltes Verfahren, mit dem durch chemische Reaktionen in einer kontrollierten Umgebung dünne Materialschichten auf ein Substrat aufgebracht werden.Bei diesem Verfahren werden gasförmige Ausgangsstoffe in eine Reaktionskammer eingeleitet, durch Wärme, Plasma oder andere Energiequellen aktiviert und auf der Substratoberfläche zur Bildung der gewünschten Beschichtung reagieren gelassen.Der Prozess gliedert sich in mehrere Schlüsselschritte, darunter die Einleitung der Reaktanten, die Aktivierung, die Oberflächenreaktion und die Entfernung der Nebenprodukte.CVD-Anlagen bestehen aus verschiedenen Komponenten wie Reaktionskammern, Gaszufuhrsystemen, Heizsystemen und Vakuumsystemen, die alle zusammenarbeiten, um eine präzise und hochwertige Abscheidung zu gewährleisten.Der Prozess wird von Faktoren wie Temperatur, Druck und der Art der verwendeten Energiequelle beeinflusst, was ihn für verschiedene industrielle Anwendungen äußerst vielseitig macht.
Die wichtigsten Punkte werden erklärt:
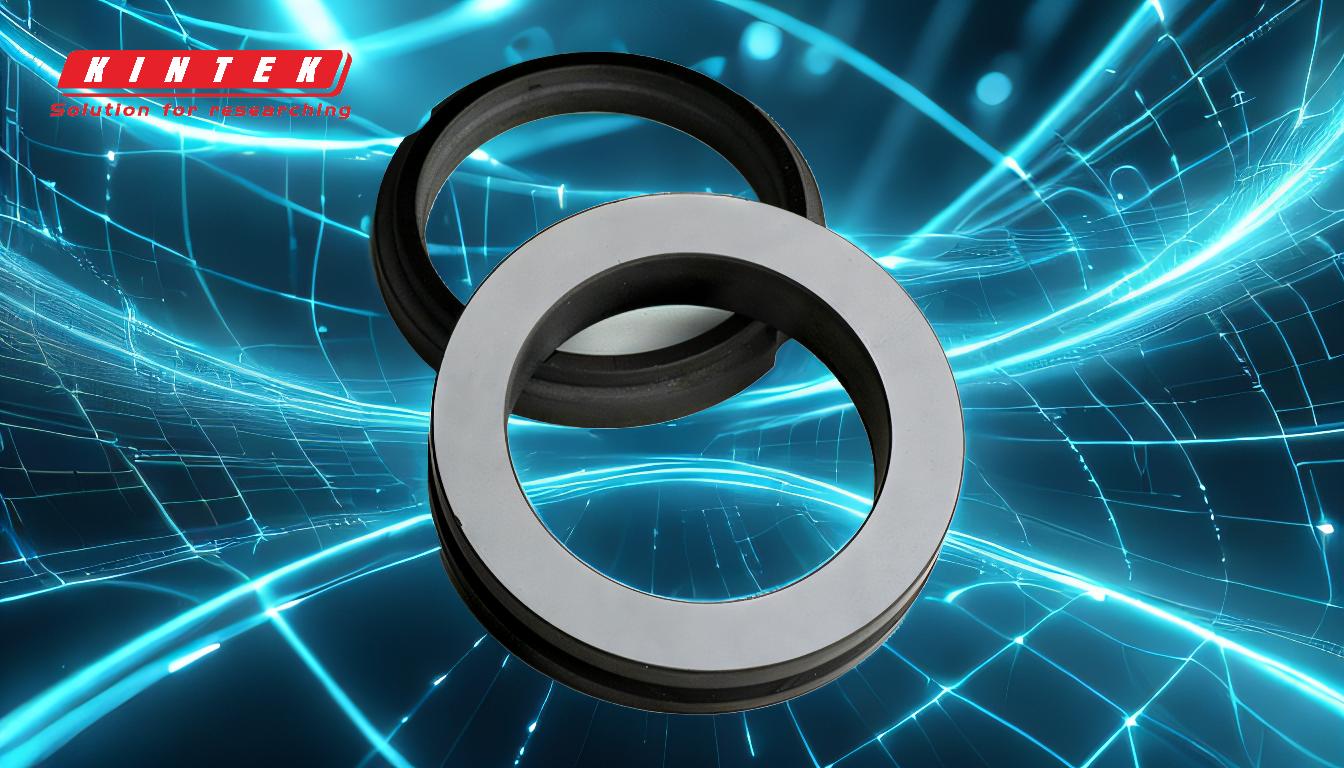
-
Einführung der Reaktanten:
- Prozess:Gasförmige oder flüssige Vorläufer, die die Elemente des gewünschten Films enthalten, werden in die Reaktionskammer eingeleitet.
- Einzelheiten:Bei diesen Vorläufern handelt es sich in der Regel um flüchtige Verbindungen, die leicht verdampfen und sich mit anderen Gasen in der Kammer vermischen können.Die Einleitung wird durch Massendurchflussregler gesteuert, um eine genaue Dosierung der Gase zu gewährleisten.
- Bedeutung:Die genaue Steuerung der Reaktantenzufuhr ist entscheidend für eine gleichmäßige Schichtabscheidung und die gewünschten Materialeigenschaften.
-
Aktivierung der Reaktanten:
- Prozess:Die Grundstoffe werden durch thermische Energie, Plasma oder Katalysatoren aktiviert, um die chemischen Reaktionen einzuleiten.
- Einzelheiten:Die Aktivierung kann durch verschiedene Methoden erfolgen, z. B. durch Erhitzen der Kammer auf eine bestimmte Temperatur, durch den Einsatz eines Plasmas zur Ionisierung der Gase oder durch die Einführung von Katalysatoren zur Senkung der für die Reaktion erforderlichen Aktivierungsenergie.
- Bedeutung:Eine ordnungsgemäße Aktivierung gewährleistet, dass die Vorläufer in den richtigen reaktiven Zustand versetzt werden, um das gewünschte Material auf der Substratoberfläche zu bilden.
-
Oberflächenreaktion und Abscheidung:
- Prozess:Die aktivierten Vorläufer reagieren an der Substratoberfläche und bilden das gewünschte Material, das sich dann als dünner Film abscheidet.
- Einzelheiten:Die Reaktion umfasst den Abbau von Vorläufermolekülen und die Bildung neuer chemischer Bindungen auf der Substratoberfläche.Der Abscheidungsprozess wird durch Faktoren wie Oberflächenkinetik, Diffusion und Desorption beeinflusst.
- Bedeutung:Die Qualität und Gleichmäßigkeit der abgeschiedenen Schicht hängt von der Effizienz der Oberflächenreaktion und der Kontrolle der Abscheidungsparameter ab.
-
Beseitigung von Nebenprodukten:
- Prozess:Die bei der Reaktion entstehenden flüchtigen oder nichtflüchtigen Nebenprodukte werden aus dem Reaktionsraum entfernt.
- Einzelheiten:Bei den Nebenprodukten kann es sich um Gase oder feste Rückstände handeln, die abgesaugt werden müssen, um die Reinheit der Beschichtungsumgebung zu erhalten.Dies wird in der Regel durch ein Vakuumpumpsystem und ein Waschsystem zur Reinigung der Abgase erreicht.
- Bedeutung:Die wirksame Entfernung von Nebenprodukten verhindert Verunreinigungen und gewährleistet die Unversehrtheit des abgeschiedenen Films.
-
System-Komponenten:
- Reaktionskammer:Das Kernstück, in dem der Abscheidungsprozess stattfindet.Es ist so konzipiert, dass es hohen Temperaturen und Drücken standhält.
- Gaszufuhrsystem:Umfasst Quellen für Vorläufergase, Zuleitungen und Massendurchflussregler, um präzise Gasmengen in die Kammer zu leiten.
- Heizsystem:Liefert die notwendige Wärmeenergie zur Aktivierung der Vorläuferstoffe und zur Aufrechterhaltung der Reaktionstemperatur.
- Vakuum-System:Hält die für den CVD-Prozess erforderliche Niederdruckumgebung aufrecht und gewährleistet einen effizienten Gasfluss und die Entfernung von Nebenprodukten.
- Kontrollsystem:Überwacht und regelt verschiedene Parameter wie Temperatur, Druck und Gasfluss, um eine gleichmäßige und hochwertige Abscheidung zu gewährleisten.
- Abgassystem:Entfernt Nebenprodukte und überschüssige Gase aus der Reaktionskammer, oft einschließlich eines Waschsystems zur Reinigung der Abgase vor der Freigabe.
-
Beeinflussende Faktoren:
- Temperatur:In der Regel sind hohe Temperaturen erforderlich, um die Ausgangsstoffe zu aktivieren und die chemischen Reaktionen einzuleiten.Die genaue Temperatur hängt von den verwendeten Materialien und Vorläufern ab.
- Druck:Niedrige Drücke werden häufig verwendet, um die Gasdiffusion zu verbessern und unerwünschte Nebenreaktionen zu reduzieren.Der Druck wird durch das Vakuumsystem gesteuert.
- Energiequelle:Die Art der Energiequelle (thermisch, Plasma usw.) wirkt sich auf die Aktivierung und die Reaktionskinetik aus und beeinflusst die Qualität und die Eigenschaften der abgeschiedenen Schicht.
- Vorbereitung des Substrats:Die Beschaffenheit der Substratoberfläche, einschließlich Sauberkeit und Temperatur, spielt eine entscheidende Rolle für die Haftung und Gleichmäßigkeit des abgeschiedenen Films.
-
Anwendungen und Vielseitigkeit:
- Vielseitigkeit:CVD wird in verschiedenen Industriezweigen eingesetzt, z. B. in der Halbleiterherstellung, in der Optik und bei Schutzbeschichtungen, da sich damit eine Vielzahl von Materialien mit hoher Präzision abscheiden lässt.
- Kundenspezifische Anpassung:Das Verfahren kann durch Anpassung von Parametern wie Temperatur, Druck und Zusammensetzung des Ausgangsmaterials an spezifische Anforderungen angepasst werden und eignet sich daher für verschiedene Anwendungen.
Zusammenfassend lässt sich sagen, dass das CVD-Verfahren eine sehr kontrollierte und vielseitige Methode für die Abscheidung dünner Schichten mit präzisen Eigenschaften ist.Es umfasst eine Reihe genau definierter Schritte und stützt sich auf ein komplexes System von Komponenten, um hochwertige Ergebnisse zu erzielen.Das Verständnis der wichtigsten Schritte und der Faktoren, die den Prozess beeinflussen, ist für die Optimierung der CVD für bestimmte Anwendungen unerlässlich.
Zusammenfassende Tabelle:
Hauptaspekt | Einzelheiten |
---|---|
Einführung von Reaktanten | Die Ausgangsstoffe werden unter genauer Kontrolle in die Reaktionskammer eingeführt. |
Aktivierung | Die Ausgangsstoffe werden durch Hitze, Plasma oder Katalysatoren für Reaktionen aktiviert. |
Oberflächenreaktion | Aktivierte Ausgangsstoffe bilden einen dünnen Film auf der Substratoberfläche. |
Entfernung von Nebenprodukten | Nebenprodukte werden entfernt, um die Reinheit der Ablagerung zu erhalten. |
Systemkomponenten | Umfasst Reaktionskammer, Gaszufuhr, Heizung, Vakuum und Kontrollsysteme. |
Beeinflussende Faktoren | Temperatur, Druck, Energiequelle und Substratvorbereitung. |
Anwendungen | Verwendung in Halbleitern, Optik und Schutzbeschichtungen. |
Sind Sie bereit, Ihren Dünnschichtabscheidungsprozess zu optimieren? Kontaktieren Sie noch heute unsere Experten für maßgeschneiderte CVD-Lösungen!