Glühen ist ein Wärmebehandlungsprozess, der die Härte von Materialien, insbesondere von Metallen, erheblich beeinflusst. Der Prozess besteht darin, das Material auf eine bestimmte Temperatur zu erhitzen, es über einen bestimmten Zeitraum auf dieser Temperatur zu halten und es dann mit kontrollierter Geschwindigkeit abzukühlen. Der Haupteffekt des Glühens besteht darin, das Material weicher zu machen, wodurch es duktiler und weniger hart wird. Dies wird erreicht, indem innere Spannungen reduziert, die Kornstruktur verfeinert und Versetzungen im Metall ermöglicht werden, sich neu anzuordnen. Die Reduzierung der Härte ist häufig bei Materialien wünschenswert, die bearbeitet, geformt oder geschweißt werden müssen, da sie die Bearbeitbarkeit verbessert. Das Ausmaß, in dem das Glühen die Härte beeinflusst, hängt jedoch von Faktoren wie der Zusammensetzung des Materials, der Glühtemperatur und der Abkühlgeschwindigkeit ab.
Wichtige Punkte erklärt:
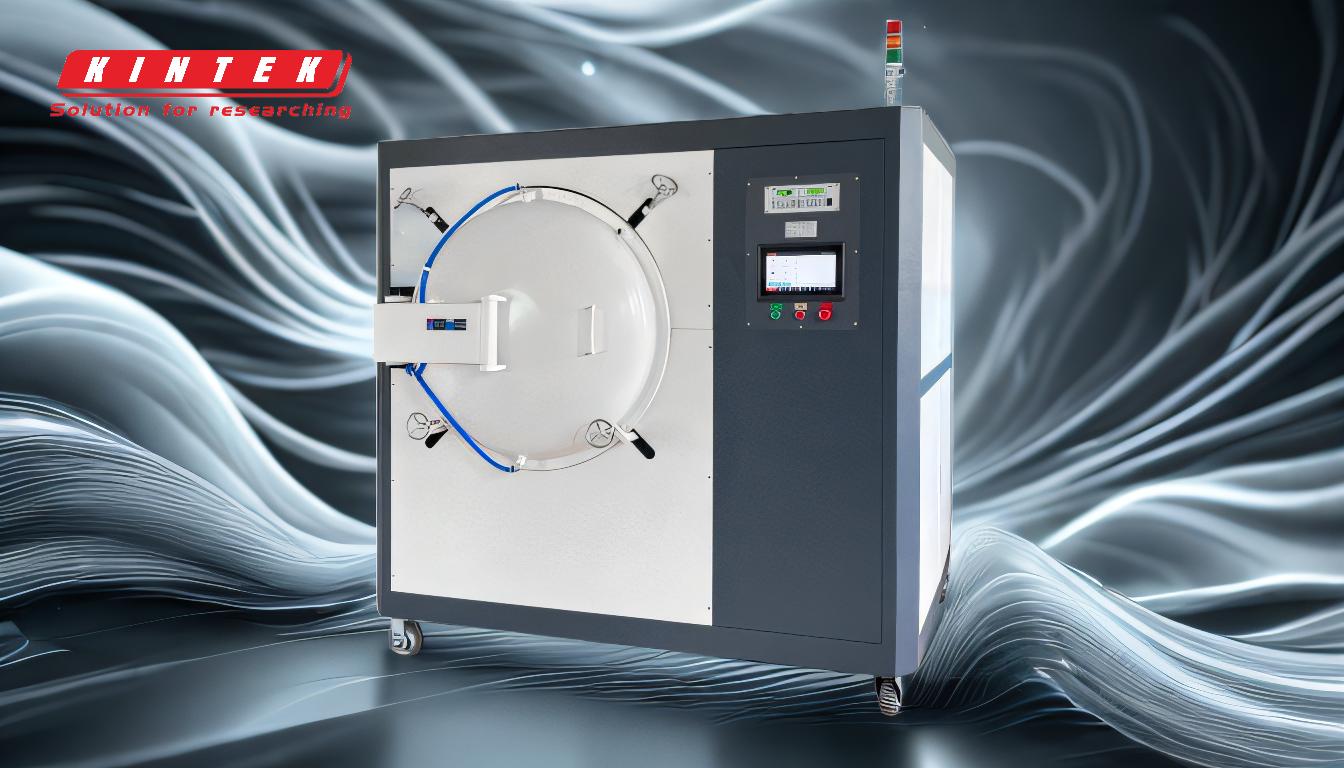
-
Mechanismus des Glühens:
- Beim Glühen wird das Material auf eine Temperatur erhitzt, bei der sich seine Mikrostruktur ändern kann. Diese Temperatur liegt typischerweise unter dem Schmelzpunkt, ist aber hoch genug, damit sich Atome bewegen und neu anordnen können.
- Dabei werden Versetzungen (Defekte in der Kristallstruktur) reduziert und die Kornstruktur gleichmäßiger. Dies führt zu einer Abnahme der Härte und einer Zunahme der Duktilität.
-
Auswirkung auf die Härte:
- Der Haupteffekt des Glühens ist eine Verringerung der Härte. Dies geschieht, weil der Prozess innere Spannungen abbaut und es dem Material ermöglicht, in einen stabileren, weniger belasteten Zustand zurückzukehren.
- Die Reduzierung der Härte ist für Werkstoffe, die bearbeitet werden müssen, wie z. B. Bearbeitung, Umformung oder Schweißen, von Vorteil, da sie sich dadurch leichter formen lassen und weniger anfällig für Risse sind.
-
Einflussfaktoren auf das Glühen:
- Materialzusammensetzung: Verschiedene Materialien reagieren unterschiedlich auf das Glühen. Beispielsweise haben Stahl, Aluminium und Kupfer jeweils unterschiedliche Glühtemperaturen und Abkühlraten, die sich auf ihre Endhärte auswirken.
- Glühtemperatur: Die Temperatur, bei der das Glühen stattfindet, spielt eine entscheidende Rolle. Bei zu niedrigen Temperaturen kann es sein, dass das Material nicht ausreichend weich wird. Bei einem zu hohen Wert kann das Material zu weich werden oder sogar schmelzen.
- Kühlrate: Die Geschwindigkeit, mit der das Material nach dem Glühen abgekühlt wird, beeinflusst auch die Härte. Langsames Abkühlen führt im Allgemeinen zu einem weicheren Material, während schnelles Abkühlen zu einer erhöhten Härte führen kann.
-
Anwendungen des Glühens:
- Glühen wird häufig in Branchen eingesetzt, in denen Materialien für die Weiterverarbeitung erweicht werden müssen. Beispielsweise wird bei der Herstellung von Stahlbauteilen häufig Glühen eingesetzt, um das Material für die Bearbeitung oder Umformung vorzubereiten.
- Es wird auch bei der Herstellung von Drähten, Blechen und anderen Metallprodukten verwendet, bei denen Duktilität und Bearbeitbarkeit von entscheidender Bedeutung sind.
-
Kompromisse:
- Während das Glühen die Härte verringert, kann es auch die Festigkeit und Verschleißfestigkeit verringern. Daher ist es wichtig, den Bedarf an Weichheit mit den erforderlichen mechanischen Eigenschaften des Materials in Einklang zu bringen.
- In einigen Fällen kann nach dem Glühen ein sekundärer Wärmebehandlungsprozess, wie z. B. Anlassen, eingesetzt werden, um das gewünschte Gleichgewicht zwischen Härte und Zähigkeit zu erreichen.
-
Mikrostrukturelle Veränderungen:
- Das Glühen führt zu erheblichen Veränderungen in der Mikrostruktur des Materials. Die Körner werden größer und gleichmäßiger, wodurch sich die Anzahl der Korngrenzen verringert. Diese Änderung trägt zu einer erhöhten Duktilität des Materials und einer verringerten Härte bei.
- Bei manchen Werkstoffen, beispielsweise Stahl, kann das Glühen auch zur Bildung neuer Phasen führen, beispielsweise Perlit oder Ferrit, die die mechanischen Eigenschaften des Werkstoffs weiter beeinflussen.
Zusammenfassend lässt sich sagen, dass das Glühen ein kritischer Wärmebehandlungsprozess ist, der die Härte verringert, indem er die Mikrostruktur des Materials verändert. Dieser Erweichungseffekt wird durch den Abbau innerer Spannungen, die Kornverfeinerung und die Neuanordnung von Versetzungen erreicht. Das Ausmaß der Härtereduzierung hängt von verschiedenen Faktoren ab, darunter der Materialzusammensetzung, der Glühtemperatur und der Abkühlgeschwindigkeit. Während sich das Glühen positiv auf die Verbesserung der Bearbeitbarkeit auswirkt, ist es wichtig, die Kompromisse hinsichtlich Festigkeit und Verschleißfestigkeit zu berücksichtigen.
Übersichtstabelle:
Aspekt | Einzelheiten |
---|---|
Primärer Effekt | Reduziert die Härte, erhöht die Duktilität und verbessert die Bearbeitbarkeit. |
Mechanismus | Entlastet innere Spannungen, verfeinert die Kornstruktur und ordnet Versetzungen neu. |
Schlüsselfaktoren | Materialzusammensetzung, Glühtemperatur und Abkühlgeschwindigkeit. |
Anwendungen | Wird bei der Bearbeitung, Umformung, dem Schweißen und der Herstellung von Drähten und Blechen verwendet. |
Kompromisse | Reduzierte Festigkeit und Verschleißfestigkeit; können Nachbehandlungen erforderlich sein. |
Mikrostrukturelle Veränderungen | Größere, gleichmäßigere Körner; Bildung neuer Phasen wie Perlit oder Ferrit. |
Benötigen Sie Hilfe bei der Optimierung Ihrer Materialeigenschaften durch Glühen? Kontaktieren Sie noch heute unsere Experten für maßgeschneiderte Lösungen!