Die Dicke von Beschichtungen, die durch chemische Gasphasenabscheidung (CVD) und physikalische Gasphasenabscheidung (PVD) abgeschieden werden, variiert aufgrund unterschiedlicher Abscheidungsmechanismen, Betriebsbedingungen und Anwendungen erheblich. Im Allgemeinen sind PVD-Beschichtungen dünner (0,2 bis 5 Mikrometer) und werden häufig für dekorative oder funktionale Zwecke verwendet. Im Gegensatz dazu sind CVD-Beschichtungen dicker, typischerweise zwischen 5 und 10 Mikrometer, und werden für Anwendungen bevorzugt, die eine hohe Reinheit und Dichte erfordern. Die Wahl zwischen CVD und PVD hängt von Faktoren wie den gewünschten Beschichtungseigenschaften, dem Substratmaterial und den spezifischen Anwendungsanforderungen ab.
Wichtige Punkte erklärt:
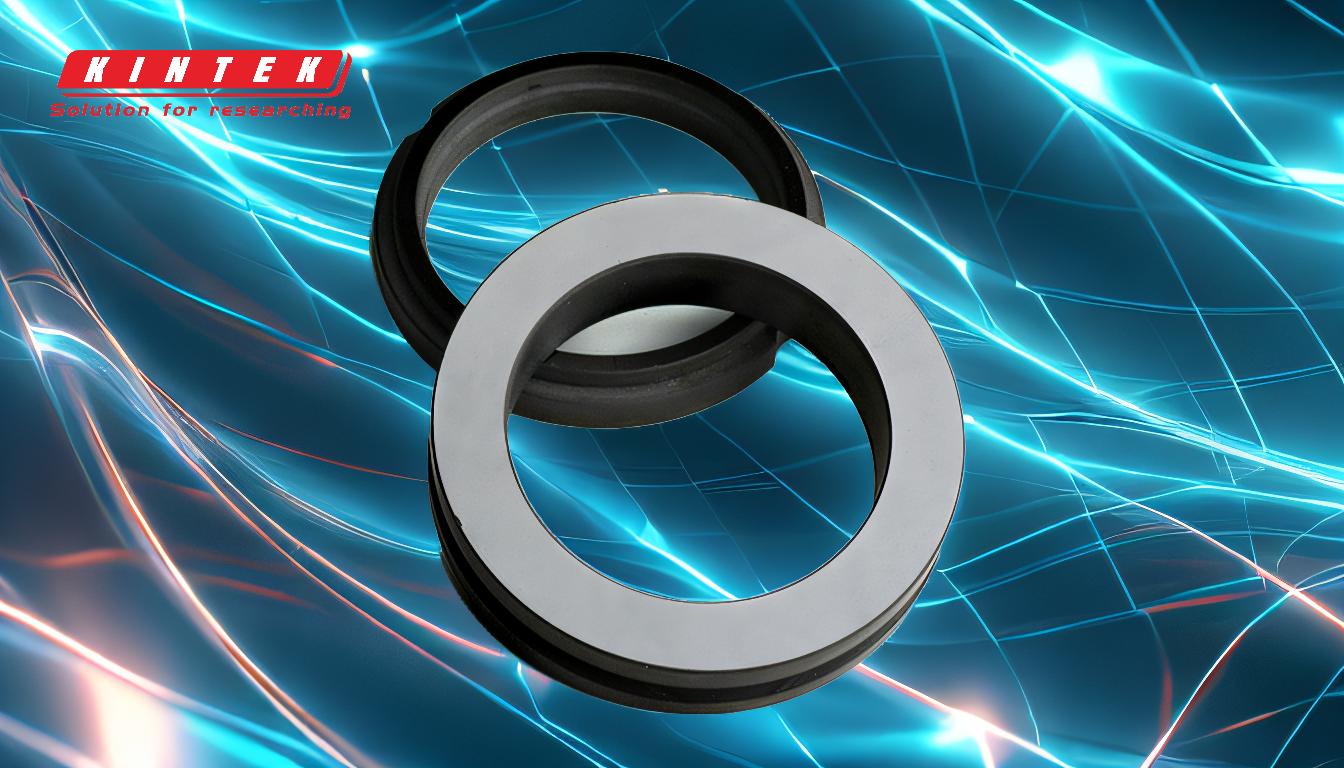
-
Ablagerungsmechanismen:
- PVD: Beinhaltet die physikalische Verdampfung fester Materialien, die dann direkt auf dem Substrat abgeschieden werden. Dieser Prozess beinhaltet normalerweise keine chemischen Reaktionen.
- CVD: Beinhaltet chemische Reaktionen zwischen gasförmigen Vorläufern und dem Substrat, die zur Bildung einer festen Beschichtung führen. Dieser Prozess ist multidirektional und kann komplexe Geometrien besser abdecken.
-
Beschichtungsdicke:
- PVD: Beschichtungen sind im Allgemeinen dünner und liegen zwischen 0,2 und 5 Mikrometern. Dadurch eignet sich PVD für Anwendungen, bei denen dünne, gleichmäßige Beschichtungen erforderlich sind, beispielsweise für dekorative Oberflächen oder Funktionsschichten in der Elektronik.
- CVD: Beschichtungen sind dicker, typischerweise zwischen 5 und 10 Mikrometer. Diese Dicke ist vorteilhaft für Anwendungen, die robuste, langlebige Beschichtungen erfordern, beispielsweise in der Halbleiterfertigung oder Schutzschichten in rauen Umgebungen.
-
Betriebstemperaturen:
- PVD: Funktioniert bei niedrigeren Temperaturen, typischerweise zwischen 250 °C und 450 °C. Dadurch eignet es sich für Untergründe, die hohen Temperaturen nicht standhalten.
- CVD: Erfordert höhere Temperaturen im Bereich von 450 °C bis 1050 °C. Diese Hochtemperaturumgebung erleichtert die für die Beschichtungsbildung notwendigen chemischen Reaktionen, schränkt jedoch die Arten der verwendbaren Substrate ein.
-
Gleichmäßigkeit und Dichte der Beschichtung:
- PVD: Beschichtungen sind im Vergleich zu CVD weniger dicht und weniger gleichmäßig. Allerdings können PVD-Beschichtungen schneller aufgetragen werden, was sie zu einer bevorzugten Methode für Anwendungen mit hohem Durchsatz macht.
- CVD: Erzeugt dichtere und gleichmäßigere Beschichtungen. Die beim CVD beteiligten chemischen Reaktionen führen zu einer besseren Haftung und Abdeckung, insbesondere bei komplexen Geometrien.
-
Anwendungen:
- PVD: Wird häufig für dekorative Beschichtungen, verschleißfeste Schichten und in der Elektronikindustrie zur Dünnfilmabscheidung verwendet.
- CVD: Weit verbreitet in der Halbleiterindustrie, zur Herstellung von Schutzbeschichtungen und in Anwendungen, die hochreine und hochdichte Filme erfordern.
-
Materialbereich:
- PVD: Kann ein breiteres Spektrum an Materialien abscheiden, darunter Metalle, Legierungen und Keramik. Aufgrund dieser Vielseitigkeit eignet sich PVD für eine Vielzahl von Anwendungen.
- CVD: Normalerweise auf Keramik und Polymere beschränkt. Die chemische Natur von CVD schränkt die Arten von Materialien ein, die effektiv abgeschieden werden können.
Zusammenfassend lässt sich sagen, dass die Wahl zwischen CVD und PVD von den spezifischen Anforderungen der Anwendung abhängt, einschließlich der gewünschten Beschichtungsdicke, Gleichmäßigkeit, Dichte und der Art der beteiligten Materialien. PVD wird im Allgemeinen für dünnere, dekorative oder funktionelle Beschichtungen bevorzugt, während CVD für dickere, haltbarere und hochreine Anwendungen bevorzugt wird.
Übersichtstabelle:
Aspekt | PVD | CVD |
---|---|---|
Beschichtungsdicke | 0,2 bis 5 Mikrometer | 5 bis 10 Mikrometer |
Betriebstemperatur | 250°C bis 450°C | 450°C bis 1050°C |
Gleichmäßigkeit der Beschichtung | Weniger einheitlich | Sehr gleichmäßig |
Beschichtungsdichte | Weniger dicht | Dichter |
Anwendungen | Dekorativ, elektronisch, verschleißfest | Halbleiter, Schutzbeschichtungen |
Materialbereich | Metalle, Legierungen, Keramik | Keramik, Polymere |
Benötigen Sie Hilfe bei der Auswahl zwischen CVD und PVD für Ihre Anwendung? Kontaktieren Sie noch heute unsere Experten!