Das feldunterstützte Sintern (FAST/SPS) bietet erhebliche Vorteile gegenüber herkömmlichen Sinterverfahren, insbesondere in Bezug auf Verarbeitungseffizienz, Materialeigenschaften und Kosteneffizienz.Bei dieser fortschrittlichen Technik werden elektrische Ströme und mechanischer Druck genutzt, um eine schnelle Verdichtung von Materialien bei niedrigeren Temperaturen und kürzeren Zeiten als beim herkömmlichen Sintern zu erreichen.Zu den Vorteilen gehören eine bessere Kontrolle über die Mikrostruktur, verbesserte mechanische und thermische Eigenschaften und die Möglichkeit, schwierige Materialien zu verarbeiten.Im Folgenden werden die wichtigsten Vorteile des feldunterstützten Sinterns im Detail erläutert.
Die wichtigsten Punkte erklärt:
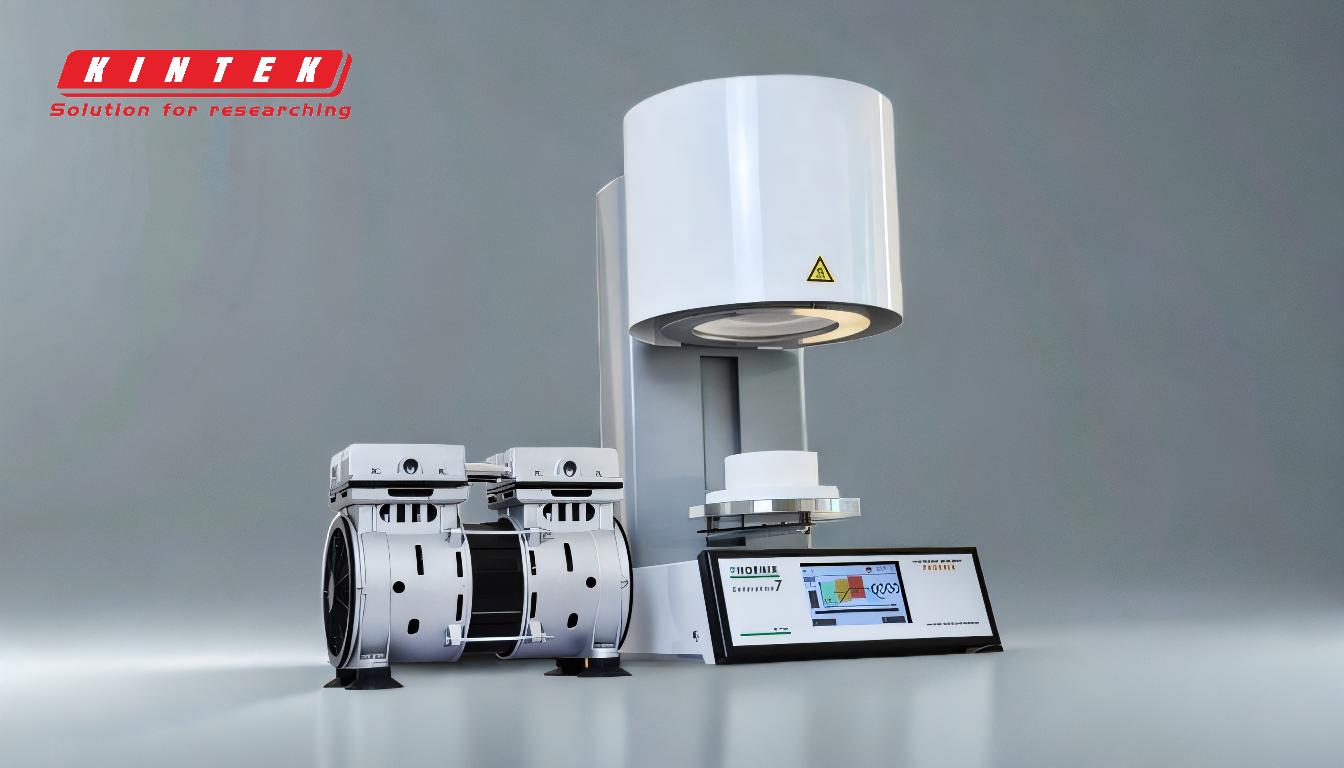
-
Niedrigere Verarbeitungstemperaturen und kürzere Zeiten
- FAST/SPS reduziert die erforderliche Sintertemperatur und -zeit erheblich und ermöglicht so schnellere Produktionszyklen und Energieeinsparungen.
- Dies ist besonders vorteilhaft für Werkstoffe mit hohen Schmelzpunkten, wie hochschmelzende Metalle und Keramiken, die mit herkömmlichen Verfahren nur schwer zu verarbeiten sind.
- Durch die geringere thermische Belastung wird das Kornwachstum minimiert, so dass feinkörnige Mikrostrukturen erhalten bleiben, die die Festigkeit und Haltbarkeit des Materials verbessern.
-
Verbesserte Kontrolle über das Mikrogefüge
- Das feldunterstützte Sintern ermöglicht eine präzise Steuerung des Verdichtungsprozesses, was zu einer gleichmäßigen und feinkörnigen Mikrostruktur führt.
- Dieses Maß an Kontrolle verbessert die Materialeigenschaften wie Festigkeit, Härte und Verschleißfestigkeit und ist damit ideal für Hochleistungsanwendungen wie Turbinenschaufeln und Schneidwerkzeuge.
- Das Verfahren ermöglicht auch die Herstellung von Nichtgleichgewichtsmikrostrukturen, die einzigartige Eigenschaften aufweisen können, die durch herkömmliches Sintern nicht erreicht werden können.
-
Verbesserte mechanische und thermische Eigenschaften
- FAST/SPS erzeugt Materialien mit überlegenen mechanischen Eigenschaften, einschließlich höherer Festigkeit, Zähigkeit und Ermüdungsbeständigkeit.
- Das Verfahren erhöht die thermische und elektrische Leitfähigkeit durch Verringerung der Porosität und Verbesserung der Partikelbindung, wodurch es sich für Anwendungen in der Elektronik und im Wärmemanagement eignet.
- Die gleichmäßige Verdichtung, die durch FAST/SPS erreicht wird, gewährleistet eine gleichbleibende Materialleistung bei großen Produktionschargen.
-
Energieeffizienz und Umweltfreundlichkeit
- Die niedrigeren Verarbeitungstemperaturen und kürzeren Sinterzeiten führen zu einem geringeren Energieverbrauch und machen FAST/SPS zu einer nachhaltigeren Option.
- Das Verfahren minimiert Oxidation und Verunreinigung, verbessert die Produktqualität und reduziert den Bedarf an Nachbehandlungen.
- Diese Vorteile für die Umwelt entsprechen der wachsenden Nachfrage nach umweltfreundlichen Herstellungsverfahren.
-
Vielseitigkeit bei der Materialverarbeitung
- FAST/SPS ist in der Lage, eine breite Palette von Werkstoffen zu verarbeiten, darunter Metalle, Keramiken, Verbundwerkstoffe und Nanomaterialien.
- Es eignet sich besonders gut für schwer zu sinternde Werkstoffe, z. B. solche mit hohen Schmelzpunkten oder niedrigen Diffusionsraten.
- Das Verfahren kann auch zur Herstellung komplexer, nahezu endkonturierter Bauteile eingesetzt werden, was den Materialabfall und die Bearbeitungskosten reduziert.
-
Kosteneffizienz und Einfachheit
- Die Verwendung einfacher Geräte und der geringere Energiebedarf machen FAST/SPS zu einer kostengünstigen Alternative zu herkömmlichen Sinterverfahren.
- Die Möglichkeit, mit minimalen Verarbeitungsschritten hochwertige Ergebnisse zu erzielen, senkt die Gesamtproduktionskosten.
- Dank ihrer Skalierbarkeit eignet sich die Technik sowohl für kleine Forschungsprojekte als auch für groß angelegte industrielle Anwendungen.
-
Anwendungen in der Hochleistungsindustrie
- FAST/SPS wird in vielen Branchen eingesetzt, in denen Hochleistungswerkstoffe benötigt werden, z. B. in der Luft- und Raumfahrt, der Automobilindustrie, der Elektronik und der Biomedizintechnik.
- Beispiele sind die Herstellung von Turbinenschaufeln, Schneidwerkzeugen, Kühlkörpern und medizinischen Implantaten, bei denen hervorragende Materialeigenschaften entscheidend sind.
- Die Fähigkeit des Verfahrens, Werkstoffe mit maßgeschneiderten Eigenschaften herzustellen, eröffnet neue Möglichkeiten für modernes Materialdesign und Innovation.
Zusammenfassend lässt sich sagen, dass das feldunterstützte Sintern (FAST/SPS) eine überzeugende Kombination aus Effizienz, Präzision und Vielseitigkeit bietet, was es zu einer hervorragenden Wahl für die moderne Materialverarbeitung macht.Seine Fähigkeit, qualitativ hochwertige Werkstoffe mit verbesserten Eigenschaften bei geringeren Kosten und Umweltauswirkungen herzustellen, macht es zu einer Schlüsseltechnologie für den Fortschritt in der Materialwissenschaft und -herstellung.
Zusammenfassende Tabelle:
Vorteil | Wesentliche Vorteile |
---|---|
Niedrigere Verarbeitungstemperaturen und -zeiten | Schnellere Produktion, Energieeinsparungen, minimiertes Kornwachstum |
Verbesserte Kontrolle des Mikrogefüges | Gleichmäßige, feinkörnige Strukturen; verbesserte Festigkeit, Härte und Verschleißfestigkeit |
Verbesserte mechanische und thermische Eigenschaften | Höhere Festigkeit, Zähigkeit und thermische/elektrische Leitfähigkeit |
Energieeffizienz und Nachhaltigkeit | Geringerer Energieverbrauch, weniger Oxidation und Verschmutzung |
Vielseitigkeit bei der Materialverarbeitung | Effektive Verarbeitung von Metallen, Keramiken, Verbundwerkstoffen und Nanomaterialien |
Kosteneffizienz & Einfachheit | Niedrigere Geräte- und Energiekosten, skalierbar für Forschung und industrielle Nutzung |
Leistungsstarke Anwendungen | Luft- und Raumfahrt, Automobilbau, Elektronik und Biomedizintechnik |
Sind Sie bereit, Ihre Materialverarbeitung mit FAST/SPS zu verbessern? Kontaktieren Sie uns noch heute um mehr zu erfahren!