Obwohl die Vakuumverdampfung bei der Dünnschichtabscheidung weit verbreitet ist, hat sie einige bemerkenswerte Nachteile, die ihre Effektivität und Anwendbarkeit in verschiedenen Industrie- und Forschungsbereichen beeinträchtigen können. Zu diesen Nachteilen gehören Schwierigkeiten bei der Abscheidung bestimmter Materialien, eine schlechte Oberflächenabdeckung bei komplexen Geometrien, eine begrenzte Kontrolle über die Schichteigenschaften, eine geringe Materialeffizienz und hohe Betriebskosten aufgrund des Bedarfs an großen Vakuumkammern und Spezialgeräten. Darüber hinaus schränken das Kontaminationsrisiko, die schlechte Stufenbedeckung und die mögliche Beschädigung durch Elektronenstrahlverdampfung den Nutzen weiter ein. Das Verständnis dieser Einschränkungen ist entscheidend für die Auswahl der geeigneten Abscheidungsmethode für bestimmte Anwendungen.
Die wichtigsten Punkte werden erklärt:
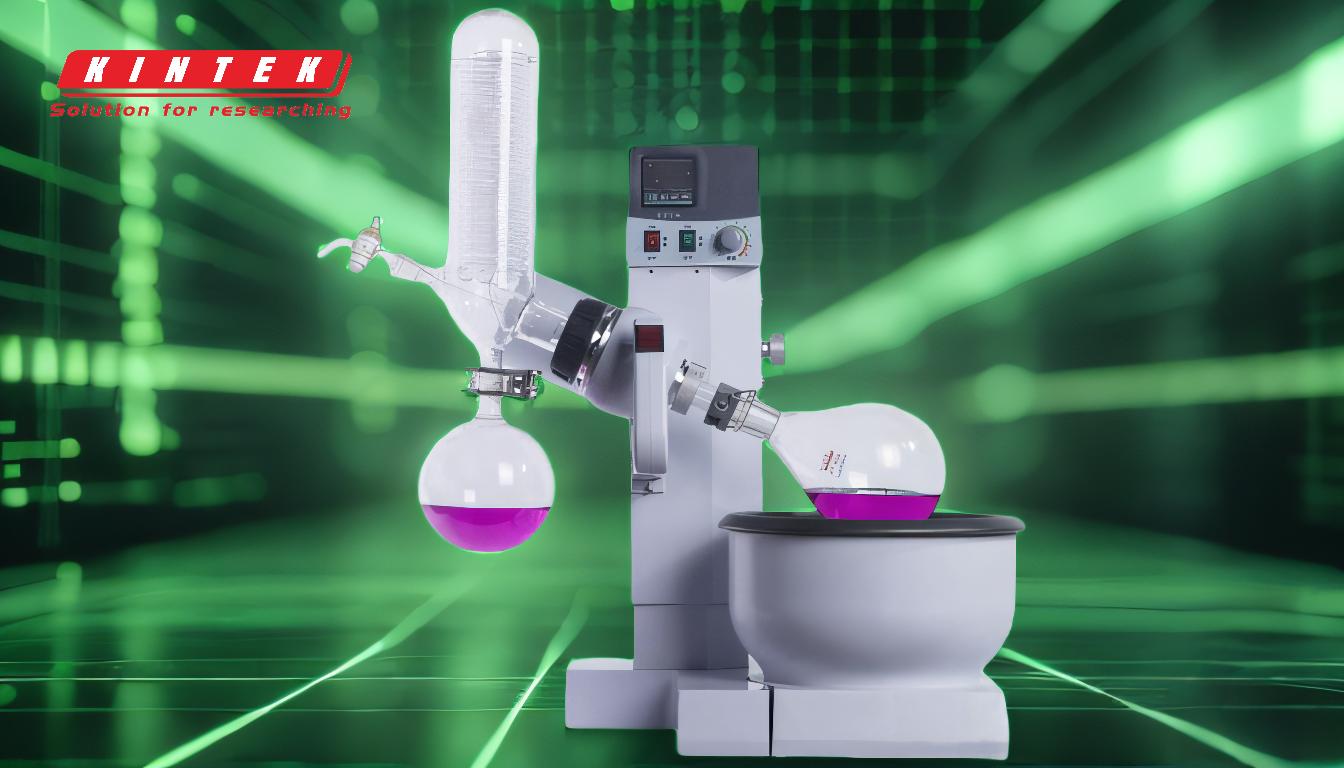
-
Schwierigkeiten bei der Abscheidung von Verbindungen und Legierungen
- Die Vakuumverdampfung hat Probleme bei der Abscheidung vieler Verbindungen und Legierungen aufgrund der unterschiedlichen Dampfdrücke der einzelnen Elemente. Dies kann zu uneinheitlichen Zusammensetzungen in der abgeschiedenen Schicht führen, so dass sie für Anwendungen, die eine genaue Stöchiometrie erfordern, ungeeignet ist.
-
Schlechte Oberflächenabdeckung auf komplexen Oberflächen
- Ohne geeignete Vorrichtungen führt die Vakuumverdampfung häufig zu einer schlechten Oberflächenabdeckung auf komplexen oder dreidimensionalen Substraten. Dies liegt daran, dass das Verfahren auf der Sichtlinie beruht, wodurch schattige Bereiche unzureichend beschichtet werden können.
-
Schlechte Gleichmäßigkeit der Filmdicke über große Flächen
- Das Erreichen einer gleichmäßigen Schichtdicke auf großen Substraten ist bei der Vakuumverdampfung eine Herausforderung. Schwankungen des Abstands zwischen Quelle und Substrat und der Verdampfungsraten können zu uneinheitlichen Beschichtungen führen, was bei Anwendungen, die eine genaue Kontrolle der Dicke erfordern, problematisch ist.
-
Begrenzte Verarbeitungsvariablen für die Kontrolle von Filmeigenschaften
- Im Vergleich zu anderen Abscheidungsmethoden wie dem Sputtern bietet die Vakuumverdampfung weniger Variablen zur Steuerung von Schichteigenschaften wie Dichte, Spannung und Haftung. Dies schränkt die Fähigkeit ein, Schichten für bestimmte Anwendungen maßzuschneidern.
-
Geringe Quellmaterialnutzung Effizienz
- Die Vakuumverdampfung ist im Hinblick auf die Materialausnutzung weniger effizient. Ein erheblicher Teil des Ausgangsmaterials kann verschwendet werden, was die Kosten in die Höhe treibt, insbesondere bei der Verwendung teurer oder seltener Materialien.
-
Hohe Strahlungswärmebelastungen
- Das Verfahren erzeugt eine hohe Strahlungswärme, die temperaturempfindliche Substrate beschädigen kann oder zusätzliche Kühlsysteme erfordert, was die Einrichtung komplexer und teurer macht.
-
Bedarf an großvolumigen Vakuumkammern
- Die Vakuumverdampfung erfordert große Vakuumkammern, um die erforderliche Niederdruckumgebung aufrechtzuerhalten. Diese Kammern sind teuer im Bau, in der Wartung und im Betrieb, so dass das Verfahren für kleine oder kostengünstige Anwendungen weniger wirtschaftlich ist.
-
Risiken der Kontamination
- Verunreinigungen durch Verunreinigungen in den Tiegeln oder der Verdampfungsquelle können die Filmqualität beeinträchtigen. Hochreine Tiegel sind teuer, und bei Hochtemperaturverfahren können Graphittiegel eine Verunreinigung durch Kohlenstoff verursachen.
-
Schlechte Schrittabdeckung
- Die Vakuumverdampfung eignet sich schlecht für die Beschichtung von Stufen oder Merkmalen auf Substraten, da ihr die Richtungskontrolle und die Bombardierungseffekte fehlen, die beim Sputtern auftreten. Dies macht es weniger geeignet für Anwendungen, die konforme Beschichtungen erfordern.
-
Röntgenschädigung durch Elektronenstrahlverdampfung
- Die Elektronenstrahlverdampfung, eine gängige Variante der Vakuumverdampfung, kann Röntgenstrahlen erzeugen, die empfindliche Substrate oder Bauteile beschädigen können, was ihren Einsatz bei bestimmten Anwendungen einschränkt.
-
Hohe Verunreinigungsgrade und Filme mit geringer Dichte
- Die Vakuumverdampfung führt häufig zu Schichten mit höherem Verunreinigungsgrad und geringerer Dichte im Vergleich zu anderen PVD-Verfahren. Die ionenunterstützte Abscheidung kann zwar die Dichte verbessern, erhöht aber die Komplexität und die Kosten des Prozesses.
-
Mäßiger Filmstress
- Durch Vakuumverdampfung abgeschiedene Schichten können mäßige Spannungen aufweisen, die die Haftung und langfristige Stabilität beeinträchtigen können. Dies ist ein Problem für Anwendungen, die dauerhafte und robuste Beschichtungen erfordern.
-
Keine In-Situ-Substratreinigung
- Im Gegensatz zum Sputtern fehlt beim Vakuumverdampfen die Möglichkeit der In-situ-Substratreinigung, was zu einer schlechteren Haftung und einem erhöhten Kontaminationsrisiko führen kann.
Wenn die Anwender diese Nachteile kennen, können sie fundierte Entscheidungen darüber treffen, ob die Vakuumverdampfung für ihre speziellen Anforderungen geeignet ist oder ob alternative Abscheidungsmethoden besser geeignet sind.
Zusammenfassende Tabelle:
Nachteil | Auswirkungen |
---|---|
Schwierigkeiten bei der Abscheidung von Verbindungen/Legierungen | Uneinheitliche Zusammensetzungen, ungeeignet für präzise Stöchiometrie |
Schlechte Oberflächenabdeckung auf komplexen Oberflächen | Unzureichend beschattete Flächen |
Schlechte Gleichmäßigkeit der Schichtdicke | Inkonsistente Beschichtungen, problematisch für die genaue Kontrolle der Dicke |
Begrenzte Kontrolle über Filmeigenschaften | Weniger Variablen für Dichte-, Spannungs- und Adhäsionskontrolle |
Geringe Materialeffizienz | Hohe Materialverschwendung, erhöhte Kosten |
Hohe Strahlungswärmebelastung | Beschädigt temperaturempfindliche Substrate, erfordert Kühlsysteme |
Bedarf an großen Vakuumkammern | Hohe Betriebs- und Wartungskosten |
Kontaminationsrisiken | Verschlechterung der Filmqualität, erfordert hochreine Tiegel |
Schlechte Stufenabdeckung | Ungeeignet für konforme Beschichtungen |
Röntgenschäden durch Elektronenstrahlverdampfung | Beschädigt empfindliche Substrate |
Hohe Verunreinigungsgrade und Filme mit geringer Dichte | Weniger dichte und unreinere Filme |
Mäßige Folienbelastung | Beeinträchtigt die Haftung und Langzeitstabilität |
Keine In-situ-Substratreinigung | Schlechtere Haftung, erhöhtes Kontaminationsrisiko |
Benötigen Sie Hilfe bei der Auswahl der richtigen Abscheidungsmethode für Ihre Anwendung? Kontaktieren Sie unsere Experten noch heute !