Das Magnetronsputtern ist ein weit verbreitetes Verfahren zur Dünnschichtabscheidung, dessen Erfolg von der Optimierung mehrerer kritischer Parameter abhängt.Zu diesen Parametern gehören die Leistungsdichte des Targets, der Gasdruck, die Substrattemperatur, die Abscheiderate und geometrische Faktoren wie der Abstand zwischen Target und Substrat.Darüber hinaus spielen Plasmaparameter wie die Ionenenergie und die Elektronenheizung eine wichtige Rolle bei der Bestimmung der Schichtqualität und -gleichmäßigkeit.Auch die Wahl des Stromversorgungssystems (Gleichstrom, Hochfrequenz oder gepulster Gleichstrom) beeinflusst den Prozess.Durch sorgfältiges Einstellen dieser Parameter lassen sich die gewünschten Folieneigenschaften wie Gleichmäßigkeit, Haftung und Dichte erzielen, während gleichzeitig Defekte und Schäden minimiert werden.
Die wichtigsten Punkte werden erklärt:
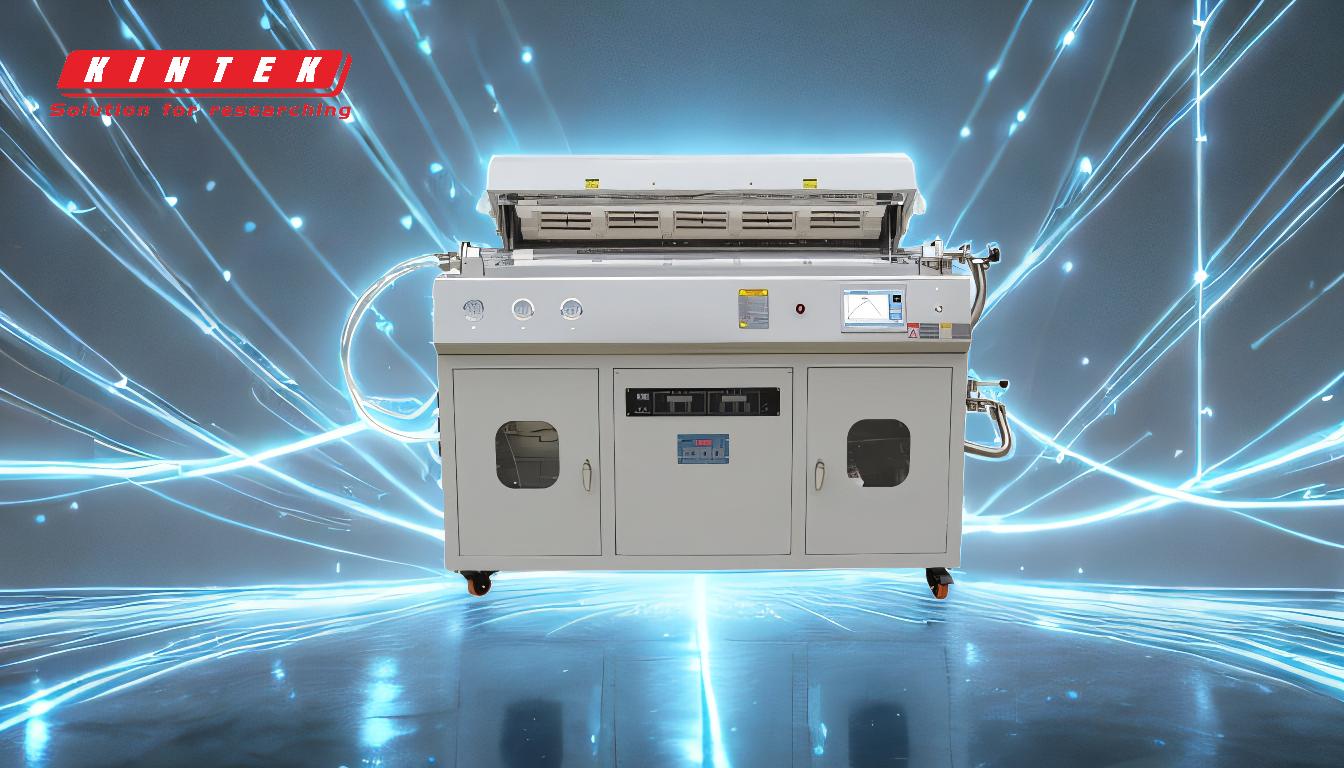
-
Ziel Leistungsdichte:
- Die Leistungsdichte des Targets wirkt sich direkt auf die Sputterrate und die Energie der ausgestoßenen Atome aus.Höhere Leistungsdichten erhöhen die Anzahl der Ionen im Plasma, was zu einer höheren Abscheiderate führt.
- Eine zu hohe Leistungsdichte kann jedoch zu einer Überhitzung oder Beschädigung des Targetmaterials führen, so dass sie optimiert werden muss, um ein Gleichgewicht zwischen Abscheiderate und Schichtqualität herzustellen.
-
Gasdruck:
- Der Gasdruck beeinflusst die mittlere freie Weglänge der gesputterten Atome und Ionen.Niedrige Drücke führen zu weniger Kollisionen, so dass die Atome das Substrat mit höherer Energie erreichen können, was die Schichtdichte und die Haftung verbessert.
- Höhere Drücke können die Gleichmäßigkeit verbessern, aber die Filmdichte aufgrund der verstärkten Streuung der gesputterten Partikel verringern.
-
Temperatur des Substrats:
- Die Substrattemperatur beeinflusst die Mikrostruktur, die Haftung und die Spannung der Schichten.Höhere Temperaturen fördern die Beweglichkeit der Atome, was zu dichteren und gleichmäßigeren Schichten führt.
- Zu hohe Temperaturen können jedoch unerwünschte Diffusion oder Phasenveränderungen in der Schicht oder dem Substrat verursachen.
-
Abscheiderate:
- Die Abscheiderate wird durch die Leistungsdichte des Ziels, den Gasdruck und das Zielmaterial beeinflusst.Eine höhere Abscheiderate ist aus Produktivitätsgründen wünschenswert, muss aber mit der Filmqualität in Einklang gebracht werden.
- Hohe Abscheidungsraten können zu Defekten oder schlechter Haftung führen, wenn sie nicht richtig kontrolliert werden.
-
Geometrische Parameter:
- Ziel-Substrat-Abstand:Dieser Abstand beeinflusst die Gleichmäßigkeit der Schicht und die Energie der abgeschiedenen Atome.Ein kürzerer Abstand kann die Abscheiderate erhöhen, kann aber aufgrund von Abschattungseffekten zu ungleichmäßigen Schichten führen.
- Ziel-Erodierbereich:Das Erosionsprofil des Targets beeinflusst die Verteilung des gesputterten Materials.Ein gleichmäßiges Erosionsprofil gewährleistet konstante Schichteigenschaften.
-
Plasma-Parameter:
- Ionen-Energie:Höhere Ionenenergien verbessern die Schichtdichte und die Haftung, können aber auch das Substrat beschädigen, wenn sie zu hoch sind.
- Elektronenheizung und Erzeugung von Sekundärelektronen:Diese Prozesse halten das Plasma aufrecht und beeinflussen die Ionenerzeugung, die für ein effizientes Sputtern entscheidend ist.
-
Stromversorgungssystem:
-
Die Wahl des Stromversorgungssystems (Gleichstrom, HF oder gepulster Gleichstrom) wirkt sich auf die Plasmastabilität, die Ionenenergie und die Abscheiderate aus.Zum Beispiel:
- DC-Magnetron-Sputtering:Geeignet für leitende Targets, aber nicht für isolierende Materialien.
- RF-Magnetronzerstäubung:Ideal für isolierende Targets, da es den Aufbau von Ladungen verhindert.
- Gepulste DC-Sputterung:Verringert die Lichtbogenbildung und verbessert die Schichtqualität bei reaktiven Sputterprozessen.
-
Die Wahl des Stromversorgungssystems (Gleichstrom, HF oder gepulster Gleichstrom) wirkt sich auf die Plasmastabilität, die Ionenenergie und die Abscheiderate aus.Zum Beispiel:
-
Basisvakuum und Sputtergasdruck:
- Ein hohes Grundvakuum gewährleistet eine saubere Umgebung und minimiert die Kontamination.
- Der Sputtergasdruck (in der Regel Argon) muss optimiert werden, um ein Gleichgewicht zwischen Plasmadichte und Sputtereffizienz zu erreichen.
-
Gleichmäßigkeit und Qualität der Schicht:
- Die Gleichmäßigkeit wird durch den Abstand zwischen Target und Substrat, den Gasdruck und die Erosionsfläche des Targets beeinflusst.
- Die Schichtqualität kann durch Optimierung der Ionenenergie, der Substrattemperatur und der Abscheidungsrate verbessert werden, um Defekte zu minimieren und die Haftung zu verbessern.
Durch eine sorgfältige Kontrolle dieser Parameter kann die Dünnschichtabscheidung mittels Magnetronsputtern zu hochwertigen, gleichmäßigen Schichten mit maßgeschneiderten Eigenschaften für verschiedene Anwendungen führen.
Zusammenfassende Tabelle:
Parameter | Auswirkung auf die Filmqualität |
---|---|
Leistungsdichte des Targets | Beeinflusst die Zerstäubungsrate und die Energie der ausgestoßenen Atome; eine hohe Dichte erhöht die Abscheidungsrate. |
Gasdruck | Beeinflusst die mittlere freie Weglänge der Atome; ein niedrigerer Druck verbessert die Dichte und Haftung. |
Temperatur des Substrats | Höhere Temperaturen verbessern die Beweglichkeit der Atome und führen zu dichteren und gleichmäßigeren Schichten. |
Abscheiderate | Höhere Raten steigern die Produktivität, müssen aber ausgewogen sein, um Defekte zu vermeiden. |
Ziel-Substrat-Abstand | Kürzere Abstände erhöhen die Abscheiderate, können aber die Gleichmäßigkeit verringern. |
Ionenenergie | Verbessert die Filmdichte und Haftung, kann aber bei zu hoher Energie die Substrate beschädigen. |
Stromversorgungssystem | Gleichstrom, Hochfrequenz oder gepulster Gleichstrom beeinflusst die Plasmastabilität und die Abscheidungsrate. |
Basis-Vakuum | Sorgt für eine saubere Umgebung und minimiert die Kontamination. |
Gleichmäßigkeit des Films | Beeinflusst von Target-Substrat-Abstand, Gasdruck und Targeterosionsfläche. |
Optimieren Sie Ihren Magnetron-Sputterprozess für hervorragende Ergebnisse - Kontaktieren Sie unsere Experten noch heute !