Die chemische Gasphasenabscheidung (CVD) ist eine vielseitige und weit verbreitete Technik für das Aufbringen dünner Schichten und Beschichtungen auf Substrate.Bei diesem Verfahren werden flüchtige Verbindungen in reaktive Stoffe zerlegt, die dann auf der Substratoberfläche reagieren und einen festen Film bilden.Die Qualität und die Eigenschaften des abgeschiedenen Materials hängen von mehreren Schlüsselparametern ab, darunter Temperatur, Druck, Gasdurchsatz, Gaskonzentration und die Wahl des Katalysators.Das Verständnis dieser Parameter ist entscheidend für die Optimierung des CVD-Verfahrens, um die gewünschten Schichteigenschaften wie Reinheit, Kristallinität und Dicke zu erreichen.
Die wichtigsten Punkte werden erklärt:
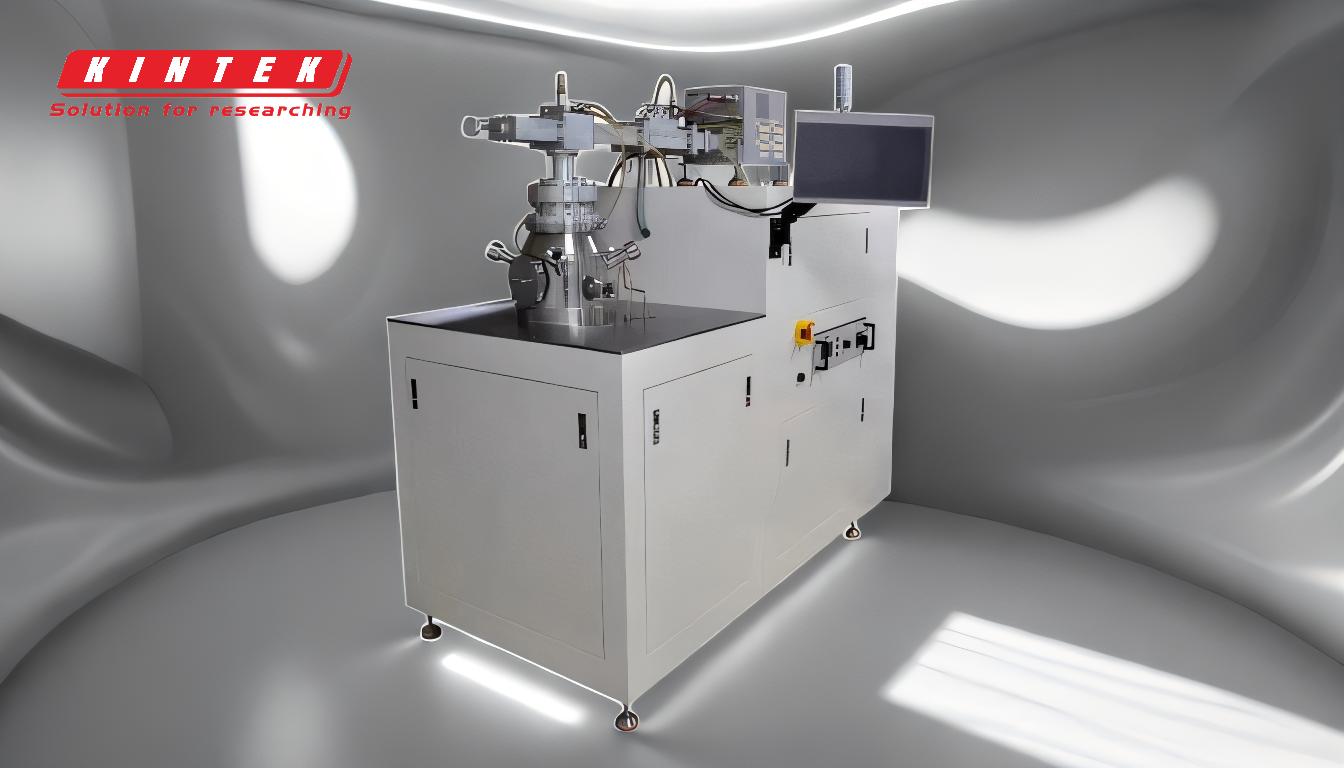
-
Temperatur:
- Die Temperatur ist einer der wichtigsten Parameter bei der CVD.Sie beeinflusst die Geschwindigkeit der chemischen Reaktionen, die Zersetzung der Vorläufergase und die Mobilität der Atome auf der Substratoberfläche.
- Höhere Temperaturen erhöhen im Allgemeinen die Reaktionsgeschwindigkeit und verbessern die Kristallinität der abgeschiedenen Schicht.Übermäßig hohe Temperaturen können jedoch zu unerwünschten Nebenreaktionen oder zur Zersetzung des Substrats führen.
- Der optimale Temperaturbereich hängt von dem jeweiligen Material, das abgeschieden werden soll, und den verwendeten Vorläufergasen ab.So erfolgt das Wachstum von Graphen auf Kupferkatalysatoren in der Regel bei Temperaturen um 1000 °C.
-
Druck:
- Der Druck in der Reaktionskammer beeinflusst die mittlere freie Weglänge der Gasmoleküle, die Geschwindigkeit der Gasphasenreaktionen und die Gleichmäßigkeit der abgeschiedenen Schicht.
- Die Niederdruck-CVD (LPCVD) wird häufig eingesetzt, um hochwertige Schichten mit hervorragender Gleichmäßigkeit und Stufenbedeckung zu erzielen.Im Gegensatz dazu ist die Atmosphärendruck-CVD (APCVD) einfacher und kostengünstiger, kann aber zu weniger gleichmäßigen Schichten führen.
- Die Wahl des Drucks hängt von den gewünschten Schichteigenschaften und der spezifischen CVD-Variante ab, die verwendet wird.
-
Gasdurchsatz:
- Die Durchflussrate der Vorläufer- und Trägergase steuert die Versorgung der Substratoberfläche mit reaktiven Substanzen.Sie beeinflusst die Wachstumsrate, die Schichtdicke und die Gleichmäßigkeit.
- Eine höhere Durchflussrate kann die Abscheidungsrate erhöhen, kann aber auch zu unvollständigen Reaktionen oder zur Bildung von Defekten führen.Umgekehrt kann eine niedrigere Durchflussrate zu einem langsameren Wachstum, aber zu einer besseren Schichtqualität führen.
- Die genaue Steuerung der Gasdurchflussrate ist für reproduzierbare Ergebnisse und die Optimierung der Filmeigenschaften von entscheidender Bedeutung.
-
Gas-Konzentration:
- Die Konzentration der Vorläufergase in der Reaktionskammer bestimmt die Verfügbarkeit der reaktiven Spezies für das Schichtwachstum.Sie beeinflusst die Stöchiometrie, die Zusammensetzung und die Eigenschaften des abgeschiedenen Materials.
- Beim CVD-Wachstum von Graphen zum Beispiel ist das Verhältnis von Methan (CH₄) zu Wasserstoff (H₂) entscheidend für die Anzahl der Graphenschichten und die Qualität des Films.
- Die Anpassung der Gaskonzentration ermöglicht die Synthese sowohl reiner als auch komplexer Materialien mit maßgeschneiderten Eigenschaften.
-
Katalysator:
- Katalysatoren spielen bei vielen CVD-Verfahren eine wichtige Rolle, insbesondere beim Wachstum von Materialien wie Graphen und Kohlenstoff-Nanoröhren.Sie senken die Aktivierungsenergie für chemische Reaktionen und fördern die Bildung hochwertiger Schichten.
- Übergangsmetalle wie Kupfer und Nickel werden aufgrund ihrer Kosteneffizienz und ihrer Fähigkeit, die Zersetzung von Vorläufergasen zu erleichtern, häufig als Katalysatoren verwendet.
- Die Wahl des Katalysators und seine Oberflächeneigenschaften (z. B. Kristallorientierung, Rauheit) haben erhebliche Auswirkungen auf die Keimbildung und das Wachstum des Films.
-
Reaktionsatmosphäre:
- Die Zusammensetzung der Reaktionsatmosphäre, einschließlich des Vorhandenseins reaktiver oder inerter Gase, beeinflusst die chemischen Reaktionen und die Qualität der abgeschiedenen Schicht.
- So wird beispielsweise Wasserstoff häufig als Reduktionsmittel verwendet, um Oxidation zu verhindern und die Bildung reiner Materialien zu fördern.Im Gegensatz dazu kann Sauerstoff oder Wasserdampf zugeführt werden, um Oxidationsreaktionen zu erleichtern.
- Die Reaktionsatmosphäre muss sorgfältig kontrolliert werden, um die gewünschten Filmeigenschaften zu erzielen und eine Verunreinigung zu vermeiden.
-
Vorbereitung des Substrats:
- Die Oberflächenbeschaffenheit des Substrats, einschließlich Sauberkeit, Rauheit und Kristallorientierung, beeinflusst die Keimbildung und das Wachstum des Films.
- Eine ordnungsgemäße Vorbereitung des Substrats, z. B. Reinigung und Glühen, ist für die Erzielung hochwertiger Schichten mit guter Haftung und Gleichmäßigkeit von wesentlicher Bedeutung.
- In einigen Fällen wirkt das Substrat selbst als Katalysator oder ist an den chemischen Reaktionen beteiligt, was die Bedeutung der Substratauswahl und -vorbereitung noch unterstreicht.
-
Abscheidungszeit:
- Die Dauer des CVD-Verfahrens bestimmt die Dicke der abgeschiedenen Schicht.Längere Abscheidungszeiten führen im Allgemeinen zu dickeren Schichten, können aber auch das Risiko von Defekten oder Verunreinigungen erhöhen.
- Die optimale Abscheidungszeit hängt von der gewünschten Schichtdicke und der Wachstumsrate ab, die durch andere Parameter wie Temperatur und Gasdurchsatz beeinflusst wird.
-
Entfernung von Nebenerzeugnissen:
- Die effiziente Entfernung gasförmiger Nebenprodukte aus der Reaktionskammer ist entscheidend für die Aufrechterhaltung einer stabilen Beschichtungsumgebung und die Vermeidung von Verunreinigungen.
- Dies wird in der Regel durch eine Kombination von Gasfluss- und Diffusionsprozessen erreicht, die sicherstellen, dass Nebenprodukte kontinuierlich von der Substratoberfläche und der Reaktionskammer entfernt werden.
Durch die sorgfältige Kontrolle dieser Parameter können Forscher und Ingenieure das CVD-Verfahren optimieren, um hochwertige Dünnschichten mit maßgeschneiderten Eigenschaften für eine breite Palette von Anwendungen herzustellen, von der Elektronik und Optik bis hin zur Energiespeicherung und Katalyse.
Zusammenfassende Tabelle:
Parameter | Schlüssel Einfluss | Beispiel/Betrachtung |
---|---|---|
Temperatur | Reaktionsgeschwindigkeit, Kristallinität und Substratintegrität | Graphenwachstum auf Kupfer: ~1000°C |
Druck | Schichtgleichmäßigkeit und Gasphasenreaktionen | LPCVD für hochwertige Schichten, APCVD für kostengünstige Lösungen |
Gasflussrate | Wachstumsrate, Schichtdicke und Gleichmäßigkeit | Höhere Durchflussraten erhöhen die Abscheidung, können aber Defekte verursachen |
Gaskonzentration | Stöchiometrie, Zusammensetzung und Materialeigenschaften | CH₄:H₂-Verhältnis entscheidend für die Kontrolle der Graphenschicht |
Katalysator | Verringerung der Aktivierungsenergie und Filmqualität | Kupfer und Nickel für das Wachstum von Graphen und Kohlenstoff-Nanoröhren |
Reaktionsatmosphäre | Chemische Reaktionen und Reinheit des Films | Wasserstoff für die Reduktion, Sauerstoff für die Oxidation |
Vorbereitung des Substrats | Keimbildung, Haftung und Gleichmäßigkeit des Films | Reinigung und Glühen für optimale Oberflächenbedingungen |
Abscheidungszeit | Schichtdicke und Defektrisiko | Längere Zeiten erhöhen die Dicke, können aber zu Verunreinigungen führen |
Entfernung von Nebenprodukten | Ablagerungsstabilität und Kontaminationsvermeidung | Kontinuierliche Entfernung durch Gasfluss- und Diffusionsverfahren |
Sind Sie bereit, Ihren CVD-Prozess zu optimieren? Kontaktieren Sie noch heute unsere Experten für maßgeschneiderte Lösungen!