Das Sintern ist ein entscheidender Prozess in der Materialwissenschaft und der Fertigung, bei dem pulverförmige Materialien durch Anwendung von Wärme und Druck in dichte, feste Körper umgewandelt werden, in der Regel unterhalb des Schmelzpunktes des Materials.Zu den wichtigsten Parametern, die den Sinterprozess beeinflussen, gehören Temperatur, Verweilzeit, Druck, Partikelgröße, Zusammensetzung und die Gasatmosphäre.Diese Parameter werden sorgfältig kontrolliert, um die gewünschten Eigenschaften des Endprodukts wie Dichte, Festigkeit und Haltbarkeit zu erreichen.Die Wahl der Sinterbedingungen hängt von der Art des zu verarbeitenden Materials und den spezifischen Anforderungen an das Endprodukt ab.Das Verständnis und die Optimierung dieser Parameter sind für die Herstellung hochwertiger Sinterwerkstoffe, die in verschiedenen Industriezweigen wie der Metallurgie, der Keramik und der Kunststoffindustrie verwendet werden, von wesentlicher Bedeutung.
Die wichtigsten Punkte werden erklärt:
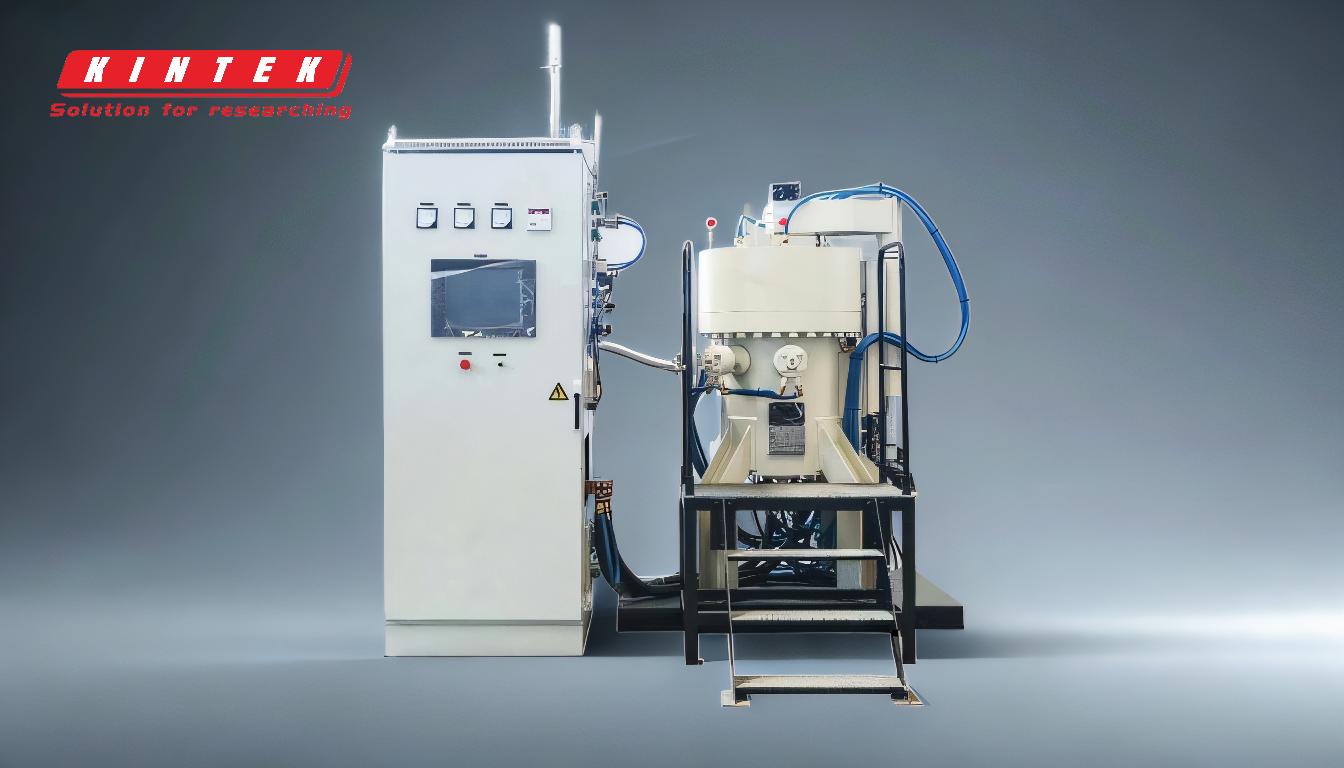
-
Temperatur:
- Rolle:Die Temperatur ist einer der wichtigsten Parameter beim Sintern.Sie bestimmt die Kinetik des Sinterprozesses und hat direkten Einfluss auf die Eigenschaften des Materials, wie Dichte und Festigkeit.
- Schlagzähigkeit:Höhere Temperaturen erhöhen im Allgemeinen die Geschwindigkeit der Partikelbindung und Verdichtung.Die Temperatur muss jedoch sorgfältig kontrolliert werden, um ein Schmelzen des Materials zu vermeiden, was zu einer Verformung oder einem Verlust der gewünschten Eigenschaften führen könnte.
- Optimierung:Die optimale Sintertemperatur ist je nach Material unterschiedlich.So erfordern Metalle mit hohem Schmelzpunkt wie Wolfram höhere Sintertemperaturen als Keramiken oder Kunststoffe.
-
Verweilzeit:
- Rolle:Die Verweilzeit ist die Dauer, während der das Material bei der Sintertemperatur gehalten wird.
- Aufprall:Längere Verweilzeiten ermöglichen eine vollständigere Diffusion der Atome über die Partikelgrenzen hinweg, was zu einer besseren Bindung und Verdichtung führt.Zu lange Verweilzeiten können jedoch zu Kornwachstum führen, was die mechanischen Eigenschaften des Materials beeinträchtigen kann.
- Optimierung:Die Verweilzeit muss ausgewogen sein, um eine ausreichende Verdichtung zu erreichen, ohne übermäßiges Kornwachstum zu verursachen.Dieses Gleichgewicht wird häufig durch experimentelle Versuche ermittelt.
-
Druck:
- Rolle:Während des Sinterns wird Druck ausgeübt, um die Umstrukturierung der Partikel zu fördern und die Porosität zu beseitigen.
- Aufprall:Höherer Druck kann die Dichte und Festigkeit des Sinterprodukts verbessern, indem er die Partikel in engeren Kontakt zwingt und die Bindung fördert.Ein zu hoher Druck kann jedoch zu Verformungen oder Rissen führen.
- Optimierung:Der angewandte Druck muss sorgfältig kontrolliert werden, um die gewünschte Dichte zu erreichen, ohne die Integrität des Materials zu beeinträchtigen.
-
Partikelgröße:
- Rolle:Die Größe der zu sinternden Partikel beeinflusst das Sinterverhalten erheblich.
- Aufprall:Kleinere Partikel haben ein größeres Verhältnis von Oberfläche zu Volumen, was eine schnellere Diffusion und bessere Verdichtung fördert.Sehr feine Partikel können jedoch zu Problemen wie Agglomeration führen, die eine gleichmäßige Sinterung behindern können.
- Optimierung:Die Partikelgrößenverteilung sollte optimiert werden, um eine gleichmäßige Sinterung zu gewährleisten und die gewünschten Materialeigenschaften zu erzielen.
-
Zusammensetzung:
- Rolle:Die Zusammensetzung des Pulvers, einschließlich etwaiger Zusatzstoffe oder Verstärkungen, beeinflusst den Sinterprozess.
- Aufprall:Homogene Zusammensetzungen fördern im Allgemeinen eine bessere Verdichtung und einheitlichere Eigenschaften.Zusatzstoffe können verwendet werden, um bestimmte Eigenschaften wie Festigkeit oder Wärmeleitfähigkeit zu verbessern, sie müssen jedoch mit dem Grundmaterial kompatibel sein.
- Optimierung:Die Zusammensetzung sollte sorgfältig ausgewählt werden, um die gewünschten Eigenschaften zu erzielen und gleichzeitig die negativen Auswirkungen auf den Sinterprozess zu minimieren.
-
Gasförmige Atmosphäre:
- Rolle:Die Atmosphäre, in der das Sintern stattfindet, kann den Prozess und die endgültigen Eigenschaften des Materials beeinflussen.
- Aufprall:Eine inerte oder reduzierende Atmosphäre kann Oxidation und andere unerwünschte Reaktionen verhindern.In manchen Fällen kann ein bestimmtes Gas verwendet werden, um bestimmte Eigenschaften zu verbessern, wie z. B. Härte oder Verschleißfestigkeit.
- Optimierung:Die Wahl der Atmosphäre hängt von dem zu sinternden Material und den gewünschten Eigenschaften des Endprodukts ab.Zu den üblichen Atmosphären gehören Stickstoff, Argon und Wasserstoff.
-
Heizrate:
- Rolle:Die Geschwindigkeit, mit der das Material auf die Sintertemperatur erhitzt wird, kann den Verdichtungsprozess beeinflussen.
- Aufprall:Eine kontrollierte Erwärmungsrate gewährleistet eine gleichmäßige Temperaturverteilung und minimiert thermische Spannungen, die zu Rissen oder Verformungen führen können.Ein schnelles Aufheizen kann zu einer ungleichmäßigen Sinterung führen, während ein zu langsames Aufheizen den Prozess unnötig verlängern kann.
- Optimierung:Die Heizrate sollte auf der Grundlage der thermischen Eigenschaften des Materials und des gewünschten Ergebnisses optimiert werden.
Zusammenfassend lässt sich sagen, dass der Sinterprozess durch ein komplexes Zusammenspiel von Parametern bestimmt wird, von denen jeder sorgfältig gesteuert werden muss, um die gewünschten Eigenschaften des Endprodukts zu erreichen.Das Verständnis und die Optimierung dieser Parameter sind von entscheidender Bedeutung für die Herstellung hochwertiger Sinterwerkstoffe, die in verschiedenen Anwendungen eingesetzt werden.
Zusammenfassende Tabelle:
Parameter | Rolle | Auswirkungen | Optimierung |
---|---|---|---|
Temperatur | Bestimmt die Kinetik und beeinflusst Eigenschaften wie Dichte und Festigkeit | Höhere Temperaturen erhöhen die Bindung, müssen aber Schmelzen vermeiden | Je nach Material unterschiedlich; bei Metallen wie Wolfram höher |
Verweilzeit | Dauer des Haltens bei Sintertemperatur | Längere Zeiten verbessern die Bindung, können aber Kornwachstum verursachen | Ausgewogene Verdichtung bei minimalem Kornwachstum |
Druck | Verbessert die Umlagerung von Partikeln und verringert die Porosität | Höherer Druck verbessert die Dichte, kann aber Verformungen verursachen | Kontrollieren Sie den Druck, um die Dichte ohne Beeinträchtigung der Integrität zu erreichen. |
Partikelgröße | Beeinflusst das Sinterverhalten | Kleinere Partikel begünstigen eine schnellere Diffusion, können aber zur Agglomeration führen | Optimieren Sie die Größenverteilung für eine gleichmäßige Sinterung |
Zusammensetzung | Beeinflusst den Sinterprozess und die endgültigen Eigenschaften | Homogene Zusammensetzungen fördern eine bessere Verdichtung | Auswahl der Zusammensetzung zur Erzielung der gewünschten Eigenschaften bei gleichzeitiger Minimierung der negativen Auswirkungen |
Gasförmige Atmosphäre | Beeinflusst Prozess und Endeigenschaften | Inerte oder reduzierende Atmosphären verhindern Oxidation | Auswahl der Atmosphäre (z. B. Stickstoff, Argon, Wasserstoff) je nach Material und Zielsetzung |
Aufheizrate | Beeinflusst den Verdichtungsprozess | Kontrollierte Raten minimieren thermische Spannungen; schnelles Erhitzen verursacht Ungleichmäßigkeiten | Optimieren Sie auf der Grundlage der thermischen Eigenschaften des Materials |
Optimieren Sie Ihren Sinterprozess für eine überlegene Materialleistung - Kontaktieren Sie unsere Experten noch heute !