Das PVD-Beschichtungsverfahren (Physical Vapor Deposition) ist ein hochentwickeltes Verfahren, mit dem dünne, haltbare und stark haftende Schichten auf verschiedene Substrate aufgebracht werden können.Das Verfahren umfasst im Allgemeinen mehrere kritische Schritte, darunter die Vorbereitung des Substrats, die Schaffung einer Hochvakuumumgebung, die Verdampfung des Zielmaterials, den Transport der verdampften Atome, die Reaktion mit Gasen, falls erforderlich, und die Abscheidung auf dem Substrat.Diese Schritte gewährleisten die Bildung einer gleichmäßigen, qualitativ hochwertigen Beschichtung, die die Eigenschaften des Substrats, wie Verschleißfestigkeit, Korrosionsbeständigkeit und Ästhetik, verbessert.Im Folgenden werden die wichtigsten Schritte und ihre Bedeutung im Detail erläutert.
Die wichtigsten Punkte werden erklärt:
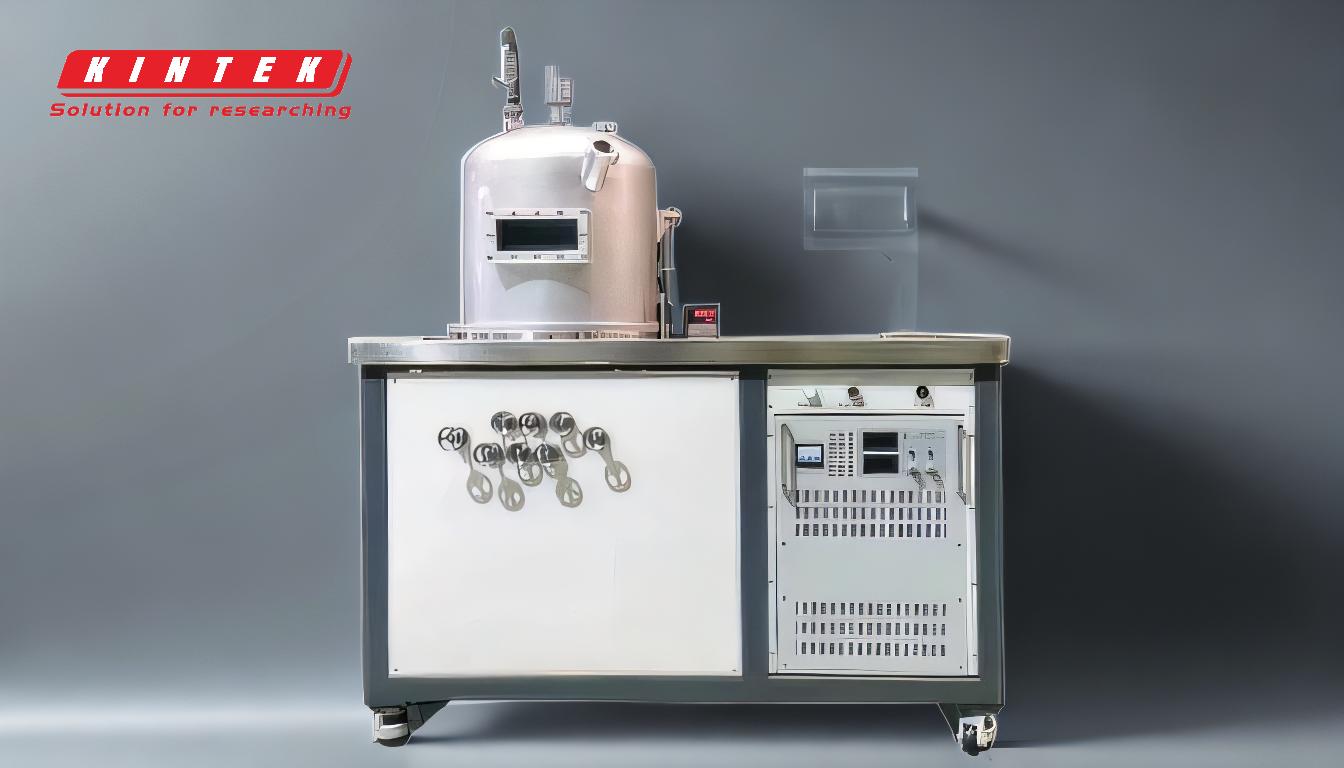
-
Vorbereitung des Substrats
- Reinigung:Das Substrat muss gründlich gereinigt werden, um alle Verunreinigungen wie Öle, Staub oder Oxide zu entfernen, die die Haftung der Beschichtung beeinträchtigen könnten.Dies geschieht in der Regel durch chemische Reinigung, Ultraschallreinigung oder Plasmareinigung.
- Vorbehandlung:Vorbehandlungsverfahren wie Ionenätzung oder Oberflächenaktivierung werden häufig eingesetzt, um die Oberflächenenergie des Substrats zu verbessern und die Haftung der Beschichtung zu erhöhen.
-
Schaffung einer Hochvakuumumgebung
- Das Substrat und das Zielmaterial werden in eine Vakuumkammer gelegt, die dann evakuiert wird, um eine Hochvakuumumgebung zu schaffen.Dieser Schritt ist entscheidend, um eine Verunreinigung durch atmosphärische Gase zu verhindern und einen sauberen Abscheidungsprozess zu gewährleisten.
- Der Vakuumdruck wird während des gesamten Prozesses sorgfältig kontrolliert und aufrechterhalten, um die Bedingungen für die Verdampfung und Abscheidung zu optimieren.
-
Verdampfung des Zielmaterials
- Das Zielmaterial (z. B. Titan, Chrom oder Aluminium) wird mit hochenergetischen Quellen wie Elektronen, Ionen oder Photonen beschossen, um Atome von seiner Oberfläche zu lösen.Dieser Vorgang wird als Verdampfung oder Ablation bezeichnet.
- Die verdampften Atome bilden in der Vakuumkammer eine Materialwolke, die zum Transport auf das Substrat bereit ist.
-
Transport der verdampften Atome
- Die verdampften Atome werden durch die Vakuumkammer vom Zielmaterial zum Substrat transportiert.Dieser Schritt ist entscheidend für eine gleichmäßige Verteilung des Beschichtungsmaterials.
- Der Transportprozess wird durch Faktoren wie die Geometrie der Kammer, den Abstand zwischen Target und Substrat und die Energie der verdampften Atome beeinflusst.
-
Reaktion mit Gasen (optional)
- In einigen Fällen reagieren die verdampften Metallatome mit eingeleiteten Gasen wie Stickstoff, Sauerstoff oder Acetylen, um Verbindungen wie Metallnitride, -oxide oder -karbide zu bilden.Dieser Schritt ist für die Erzeugung spezifischer Beschichtungseigenschaften, wie Härte oder Farbe, unerlässlich.
- Die Reaktion wird sorgfältig kontrolliert, um die gewünschte chemische Zusammensetzung und Beschichtungseigenschaften zu erreichen.
-
Abscheidung auf dem Substrat
- Die verdampften Atome oder Verbindungen kondensieren auf dem Substrat und bilden einen dünnen, gleichmäßigen Film.Der Abscheidungsprozess wird von Faktoren wie der Substrattemperatur, der Abscheidungsrate und der Energie der einfallenden Atome beeinflusst.
- Die Beschichtung verbindet sich fest mit dem Substrat und bildet eine dauerhafte und haftende Schicht, die die Leistung des Substrats verbessert.
-
Post-Deposition-Verfahren
- Spülen:Nach der Abscheidung wird die Kammer mit Inertgasen, z. B. Argon, gespült, um Restdämpfe zu entfernen und Verunreinigungen zu vermeiden.
- Endbearbeitung:Zur Verbesserung des Aussehens oder der Leistung der Beschichtung können zusätzliche Veredelungsverfahren wie Polieren oder Glühen angewandt werden.
- Qualitätskontrolle:Das beschichtete Substrat wird strengen Qualitätskontrollen unterzogen, um sicherzustellen, dass die Beschichtung den Spezifikationen für Dicke, Haftung und andere Eigenschaften entspricht.
Durch die Einhaltung dieser Schritte erzeugt das PVD-Beschichtungsverfahren hochwertige Beschichtungen, die in Branchen wie der Luft- und Raumfahrt, der Automobilindustrie, der Medizintechnik und der Unterhaltungselektronik weit verbreitet sind.Die Präzision und Vielseitigkeit des Verfahrens machen es zu einer bevorzugten Methode, um funktionelle und dekorative Beschichtungen auf eine Vielzahl von Materialien aufzubringen.
Zusammenfassende Tabelle:
Schritt | Beschreibung |
---|---|
1.Vorbereitung des Substrats | - Reinigung:Entfernt Verunreinigungen für eine bessere Haftung. |
- Vorbehandlung:Verbessert die Oberflächenenergie für eine bessere Beschichtungshaftung. | |
2.Hoch-Vakuum-Umgebung | - Schafft eine kontaminationsfreie Umgebung für die Abscheidung. |
3.Verdampfung | - Das Zielmaterial wird mit Hilfe von Hochenergiequellen verdampft. |
4.Transport | - Die verdampften Atome werden zur gleichmäßigen Verteilung auf das Substrat transportiert. |
5.Reaktion mit Gasen | - Optionaler Schritt zur Erzeugung bestimmter Beschichtungseigenschaften (z. B. Härte, Farbe). |
6.Abscheidung | - Die Atome kondensieren auf dem Substrat und bilden eine dauerhafte, haftende Beschichtung. |
7.Post-Deposition | - Spülung, Endbearbeitung und Qualitätskontrolle stellen sicher, dass die Beschichtung den Spezifikationen entspricht. |
Entdecken Sie, wie der PVD-Beschichtungsprozess die Leistung Ihres Produkts steigern kann. Kontaktieren Sie uns noch heute für eine fachkundige Beratung!