Beim Aufdampfen handelt es sich um ein Verfahren zur Herstellung dünner Schichten oder Beschichtungen auf einem Substrat durch Aufbringen von verdampftem Material auf dessen Oberfläche.Diese Technik ist in Branchen wie der Halbleiterindustrie, der Optik und bei Schutzschichten weit verbreitet.Bei diesem Verfahren wird ein festes oder flüssiges Material in einen Dampf umgewandelt, der dann auf einem Substrat kondensiert und eine dünne, gleichmäßige Schicht bildet.Es gibt zwei Hauptarten der Gasphasenabscheidung: die physikalische Gasphasenabscheidung (PVD) und die chemische Gasphasenabscheidung (CVD).Bei der PVD-Beschichtung wird das Material physikalisch verdampft, während die CVD-Beschichtung auf chemischen Reaktionen zur Abscheidung des Materials beruht.Beide Verfahren erfordern kontrollierte Umgebungen, oft mit Vakuumkammern, präziser Temperaturregelung und spezifischen Gasdrücken.Das Ergebnis ist eine äußerst haltbare, korrosionsbeständige und temperaturtolerante Beschichtung.
Die wichtigsten Punkte erklärt:
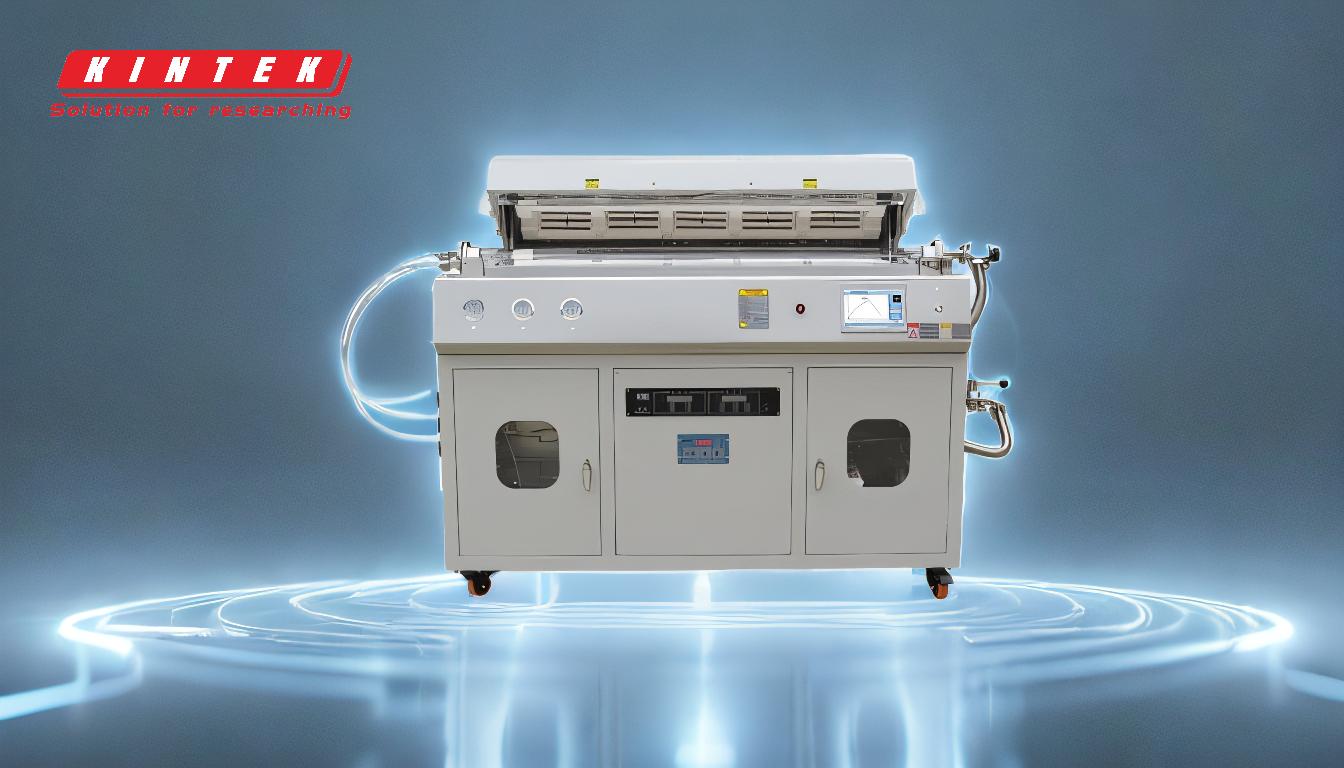
-
Überblick über die Gasphasenabscheidung:
- Das Aufdampfen ist ein Verfahren, bei dem Materialien in Form eines dünnen Films auf ein Substrat aufgebracht werden.
- Das Material wird zunächst verdampft und dann auf dem Substrat kondensiert, wodurch eine gleichmäßige Schicht entsteht.
- Diese Technik ist in Branchen wie Halbleiter, Optik und Schutzbeschichtungen unverzichtbar.
-
Arten der Gasphasenabscheidung:
-
Physikalische Gasphasenabscheidung (PVD):
- Physikalische Verdampfung des Zielmaterials, häufig unter Verwendung von Wärme oder hochenergetischen Ionen.
- Das verdampfte Material wird dann auf das Substrat aufgebracht.
- Zu den gängigen PVD-Verfahren gehören Sputtern und thermisches Verdampfen.
- PVD ist bekannt für die Herstellung haltbarer, korrosionsbeständiger Beschichtungen, die auch hohen Temperaturen standhalten.
-
Chemische Gasphasenabscheidung (CVD):
- Die Abscheidung des Materials auf dem Substrat erfolgt durch chemische Reaktionen.
- Das Substrat wird in eine Reaktionskammer gegeben, die mit einer gasförmigen Form des Beschichtungsmaterials gefüllt ist.
- Das Gas reagiert mit dem Substrat oder zersetzt sich, um eine feste Beschichtung zu bilden.
- Mit CVD können sehr gleichmäßige und konforme Beschichtungen erzeugt werden, was sie ideal für komplexe Geometrien macht.
-
Physikalische Gasphasenabscheidung (PVD):
-
Schlüsselprozesse der Gasphasenabscheidung:
-
Chemische Niederdruck-Gasphasenabscheidung (LPCVD):
- Eine Art von CVD, die mit reduziertem Druck arbeitet, um die Gleichmäßigkeit der Schichten zu verbessern und Verunreinigungen zu reduzieren.
- Wird häufig in der Halbleiterherstellung verwendet.
-
Niederdruck-Plasmaspritzen (LPPS):
- Nutzt Plasma, um reaktive Gase zu aktivieren und Materialien abzuscheiden.
- Wird häufig zur Herstellung von Beschichtungen mit bestimmten mechanischen oder elektrischen Eigenschaften verwendet.
-
Thermische Gasphasenabscheidung:
- Dabei wird ein festes Material in einer Hochvakuumkammer erhitzt, um einen Dampfdruck zu erzeugen.
- Das verdampfte Material kondensiert dann auf dem Substrat und bildet einen dünnen Film.
- Das Verfahren arbeitet in der Regel bei Temperaturen zwischen 250 und 350 Grad Celsius.
-
Chemische Niederdruck-Gasphasenabscheidung (LPCVD):
-
Komponenten eines Dampfabscheidungssystems:
-
Wärmequelle:
- Dient zur Verdampfung des Zielmaterials bei der PVD oder zur Aktivierung chemischer Reaktionen bei der CVD.
-
Vakuumkammer:
- Bietet eine kontrollierte Umgebung mit niedrigem Druck, um Verunreinigungen zu vermeiden und eine gleichmäßige Ablagerung zu gewährleisten.
-
Ziel-Material:
- Das abzuscheidende Material, das ein Metall, ein Halbleiter oder ein anderer Feststoff sein kann.
-
Substrat:
- Die Oberfläche, auf die das Material aufgebracht wird. Sie besteht häufig aus Glas, Silizium oder anderen Materialien.
-
Gasversorgung:
- Bei der CVD werden reaktive Gase in die Kammer eingeleitet, um den Abscheidungsprozess zu erleichtern.
-
Temperaturkontrolle:
- Die genaue Regelung der Substrat- und Kammertemperatur ist entscheidend für das Erreichen der gewünschten Schichteigenschaften.
-
Wärmequelle:
-
Anwendungen der Gasphasenabscheidung:
-
Halbleiter:
- Zur Abscheidung dünner Schichten aus Materialien wie Silizium, Siliziumdioxid und Metallen auf Halbleiterwafern.
-
Optik:
- Zur Herstellung von Antireflexionsbeschichtungen, Spiegeln und anderen optischen Komponenten.
-
Schützende Beschichtungen:
- Bietet verschleißfeste, korrosionsbeständige und thermische Barrierebeschichtungen für Werkzeuge, Luft- und Raumfahrtkomponenten und medizinische Geräte.
-
Dekorative Beschichtungen:
- Wird in der Automobil- und Schmuckindustrie verwendet, um ästhetisch ansprechende Oberflächen zu erzeugen.
-
Halbleiter:
-
Vorteile der Gasphasenabscheidung:
-
Hohe Präzision:
- Ermöglicht die Abscheidung extrem dünner und gleichmäßiger Schichten, oft im Nanomaßstab.
-
Vielseitigkeit:
- Kann eine Vielzahl von Materialien abscheiden, darunter Metalle, Keramiken und Polymere.
-
Dauerhaftigkeit:
- Erzeugt Beschichtungen, die äußerst verschleißfest, korrosionsbeständig und hochtemperaturbeständig sind.
-
Skalierbarkeit:
- Geeignet sowohl für die Forschung in kleinen Labors als auch für die industrielle Produktion in großem Maßstab.
-
Hohe Präzision:
-
Herausforderungen und Überlegungen:
-
Kosten:
- Die Ausrüstungs- und Betriebskosten können hoch sein, insbesondere bei fortgeschrittenen Techniken wie CVD.
-
Komplexität:
- Erfordert eine präzise Steuerung von Parametern wie Temperatur, Druck und Gasfluss.
-
Beschränkungen des Materials:
- Nicht alle Materialien lassen sich mit diesen Methoden leicht verdampfen oder ablagern.
-
Umweltaspekte:
- Einige Verfahren sind mit gefährlichen Gasen oder hohem Energieverbrauch verbunden und erfordern eine sorgfältige Handhabung und Entsorgung.
-
Kosten:
Zusammenfassend lässt sich sagen, dass das Aufdampfen ein vielseitiges und präzises Verfahren zur Herstellung von dünnen Schichten und Beschichtungen mit einem breiten Spektrum an Anwendungen ist.Wenn man die verschiedenen Arten der Aufdampfung, die wichtigsten Prozesse und Systemkomponenten versteht, kann man die Rolle dieser Technologie in der modernen Fertigung und Materialwissenschaft besser einschätzen.
Zusammenfassende Tabelle:
Aspekt | Einzelheiten |
---|---|
Arten | - Physikalische Gasphasenabscheidung (PVD) |
- Chemische Gasphasenabscheidung (CVD) | |
Schlüsselprozesse | - Chemische Niederdruck-Gasphasenabscheidung (LPCVD) |
- Niederdruck-Plasmaspritzen (LPPS)
- Thermische Gasphasenabscheidung | | Anwendungen
- | - Halbleiter
- Optik
- Schützende Beschichtungen Dekorative Beschichtungen | |
- Vorteile
- | Hohe Präzision
- Vielseitigkeit Langlebigkeit Skalierbarkeit |
- |
- Herausforderungen
- | Hohe Kosten
Komplexität Materielle Beschränkungen Umweltaspekte |