Sintern ist ein Prozess, bei dem Atome durch die Mikrostruktur eines Materials diffundieren, angetrieben durch ein Gefälle im chemischen Potenzial, um die Porosität zu verringern und die Materialeigenschaften wie Festigkeit, Leitfähigkeit und Wärmeleistung zu verbessern.Diese Diffusion findet statt, wenn sich Atome von Bereichen mit höherem chemischem Potenzial zu Bereichen mit niedrigerem chemischem Potenzial bewegen, was zu einer Verdichtung und Bindung von Partikeln führt.Der Prozess wird von verschiedenen Faktoren beeinflusst, darunter Temperatur, Druck, Partikelgröße, Zusammensetzung und Sinteratmosphäre.Die optimalen Sinterbedingungen hängen von den gewünschten Eigenschaften des Endprodukts ab, wobei feinere Pulver und höhere Temperaturen im Allgemeinen die Verdichtung verbessern, aber eine sorgfältige Kontrolle der flüssigen Phase erfordern.Das Sintern ist entscheidend für die Herstellung von Hochleistungswerkstoffen, insbesondere von solchen mit hohem Schmelzpunkt, ohne dass ein vollständiges Aufschmelzen erforderlich ist.
Die wichtigsten Punkte erklärt:
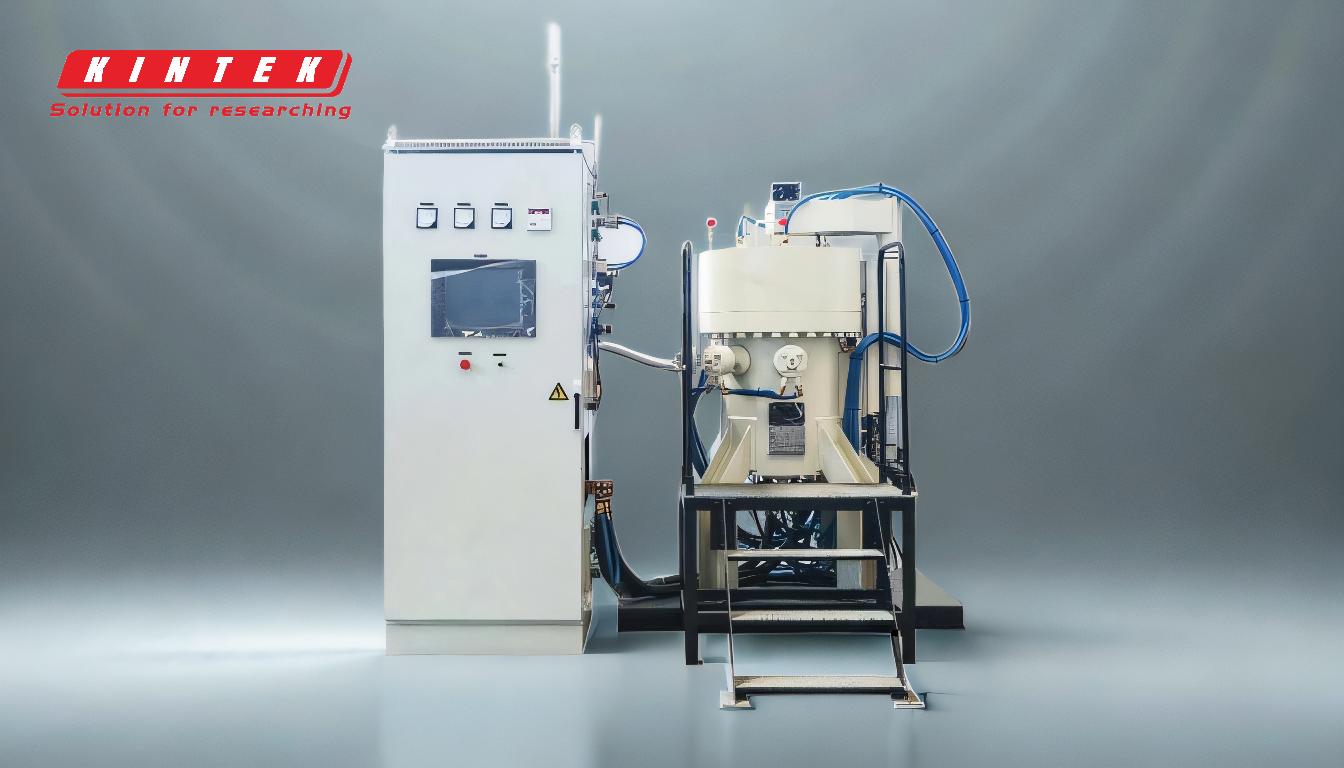
-
Atomare Diffusion und chemisches Potentialgefälle:
- Die Sinterung erfolgt durch die Diffusion von Atomen durch die Mikrostruktur eines Materials.
- Diese Diffusion wird durch ein Gefälle im chemischen Potenzial angetrieben, bei dem sich die Atome von Bereichen mit höherem chemischem Potenzial zu Bereichen mit niedrigerem chemischem Potenzial bewegen.
- Diese Bewegung führt zur Bindung von Partikeln und zur Verringerung der Porosität, was zu einem dichteren und festeren Material führt.
-
Faktoren, die die Sinterung beeinflussen:
- Temperatur:Höhere Temperaturen erhöhen die Atomdiffusionsrate, verbessern die Sinterkinetik und die Materialeigenschaften wie Zugfestigkeit und Schlagenergie.
- Druck:Angewandter Druck hilft bei der Umlagerung der Partikel und der Beseitigung von Porosität, was zu einer besseren Verdichtung führt.
- Partikelgröße:Kleinere Partikel haben ein größeres Verhältnis von Oberfläche zu Volumen, was eine schnellere Diffusion und bessere Verdichtung fördert.
- Zusammensetzung:Homogene Zusammensetzungen erleichtern eine gleichmäßige Sinterung, während heterogene Zusammensetzungen zu einer ungleichmäßigen Verdichtung führen können.
- Atmosphäre:Die Sinteratmosphäre (z. B. Luft, Vakuum, Argon oder Stickstoff) kann die chemischen Reaktionen und die endgültigen Eigenschaften des Materials beeinflussen.
-
Parameter des Sinterprozesses:
- Sintertemperatur und Sinterzeit:Diese hängen vom Material und der gewünschten Dichte des Endprodukts ab.Höhere Temperaturen führen im Allgemeinen zu einer besseren Verdichtung, müssen aber sorgfältig kontrolliert werden, um übermäßiges Kornwachstum oder Schmelzen zu vermeiden.
- Aufheizrate:Eine kontrollierte Heizrate ist entscheidend, um eine gleichmäßige Verdichtung zu gewährleisten und Defekte zu vermeiden.
- Schichtdicke und Maschinengeschwindigkeit:Beim industriellen Sintern werden Parameter wie die Schichtdicke (in der Regel 250-500 mm) und die Maschinengeschwindigkeit (1,5-4 m/min) kontrolliert, um sicherzustellen, dass das Material gleichmäßig gesintert wird und den gewünschten Endpunkt erreicht.
-
Vorteile des Sinterns:
- Stärke und Integrität:Die Sinterung verleiht den Materialien mechanische Festigkeit und strukturelle Integrität.
- Reduzierte Porosität:Das Verfahren verringert die Porosität erheblich und verbessert Eigenschaften wie elektrische Leitfähigkeit, Wärmeleitfähigkeit und Transluzenz.
- Materialien mit hohem Schmelzpunkt:Das Sintern ermöglicht die Herstellung von Produkten aus Metallen und Keramiken mit hohem Schmelzpunkt, ohne dass ein vollständiges Einschmelzen erforderlich ist.
-
Techniken und Ausrüstung:
- Je nach Material und gewünschten Eigenschaften werden verschiedene Sintertechniken (z. B. druckunterstütztes Sintern, Funkenplasmasintern) eingesetzt.
- Das Sintern erfolgt in der Regel in kontrollierten Umgebungen mit Hilfe von Anlagen wie Förderbändern, Stoßöfen oder Chargenöfen.
-
Industrielle Erwägungen:
- Luftmenge und Vakuum:Beim industriellen Sintern werden Faktoren wie die Luftmenge (z. B. 3200 m³ pro Tonne Sintererz) und das Vakuum zur Optimierung des Prozesses gesteuert.
- Endpunkt der Sinterung:Der Prozess wird sorgfältig überwacht, um sicherzustellen, dass das Material den gewünschten Endpunkt der Sinterung erreicht, der für das Erreichen der erforderlichen Eigenschaften entscheidend ist.
Zusammenfassend lässt sich sagen, dass das Sintern ein komplexer Prozess ist, der von zahlreichen Faktoren beeinflusst wird, von denen jeder einzelne sorgfältig kontrolliert werden muss, um die gewünschten Materialeigenschaften zu erzielen.Das Verständnis dieser Faktoren und ihrer Wechselwirkungen ist für die Optimierung des Sinterprozesses und die Herstellung hochwertiger Werkstoffe unerlässlich.
Zusammenfassende Tabelle:
Hauptaspekt | Beschreibung |
---|---|
Atomare Diffusion | Angetrieben durch chemische Potentialgradienten, die zu Partikelbindung und Verdichtung führen. |
Beeinflussende Faktoren | Temperatur, Druck, Partikelgröße, Zusammensetzung und Sinteratmosphäre. |
Prozess-Parameter | Sintertemperatur, Zeit, Heizrate, Schichtdicke und Maschinengeschwindigkeit. |
Vorteile | Erhöhte Festigkeit, verringerte Porosität und Herstellung von Materialien mit hohem Schmelzpunkt. |
Techniken und Ausrüstung | Druckunterstütztes Sintern, Funkenplasmasintern, Bandförderer und Öfen. |
Industrielle Erwägungen | Luftmenge, Vakuumniveau und Überwachung des Sinterendpunkts. |
Optimieren Sie Ihre Materialeigenschaften mit professionellen Sinterlösungen. Kontaktieren Sie uns noch heute um mehr zu erfahren!