Die Sputterdeposition ist eine weit verbreitete Technik der physikalischen Gasphasenabscheidung (PVD) zur Erzeugung dünner Schichten auf Substraten.Dabei wird ein Zielmaterial mit hochenergetischen Ionen, in der Regel aus einem Argonplasma, beschossen, um Atome aus dem Zielmaterial in die Gasphase zu schleudern.Diese ausgestoßenen Atome wandern dann durch eine Vakuumkammer und lagern sich auf einem Substrat ab und bilden einen dünnen, gleichmäßigen Film.Das Verfahren ist sehr gut steuerbar, erzeugt dichte und gleichmäßige Beschichtungen und eignet sich für eine breite Palette von Materialien, was es zu einer bevorzugten Methode in Branchen wie der Halbleiter-, Optik- und Solarzellenindustrie macht.
Die wichtigsten Punkte werden erklärt:
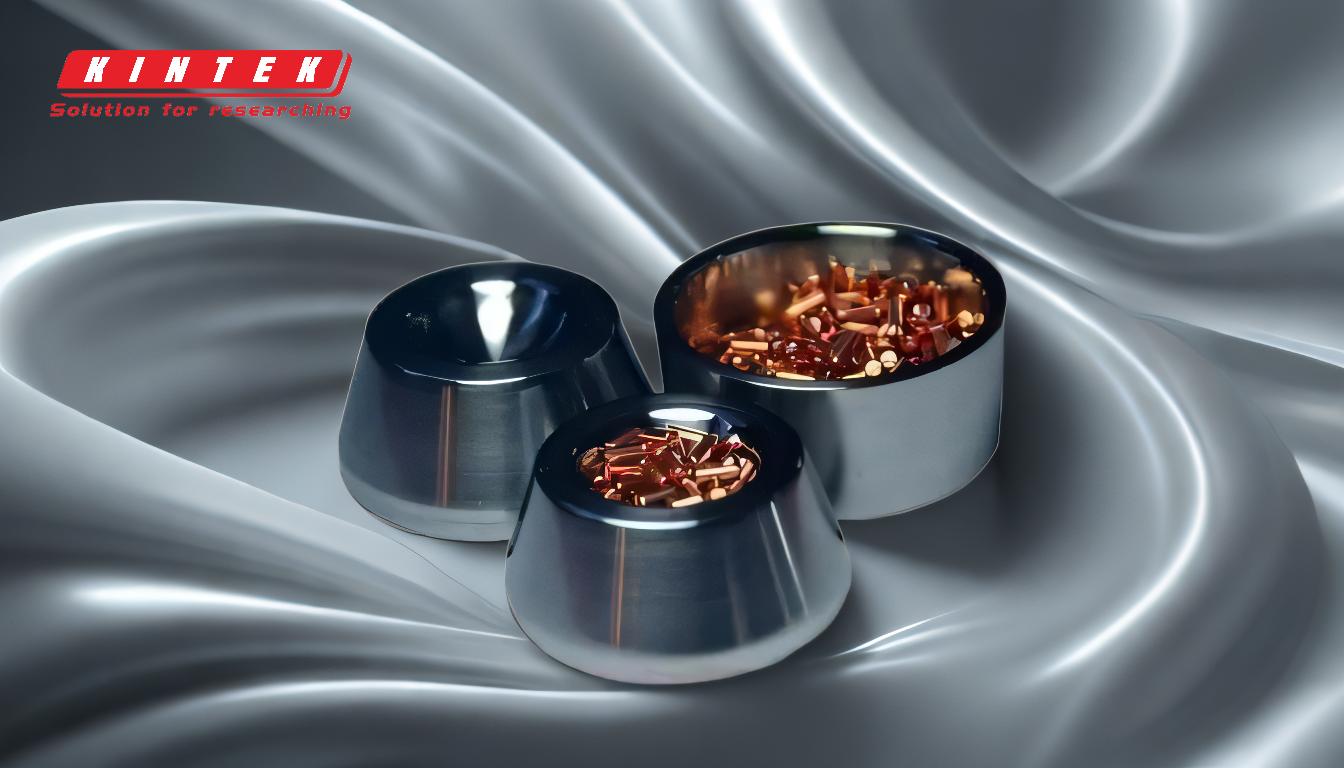
-
Grundlegender Mechanismus der Sputterabscheidung:
- Die Sputterabscheidung beruht auf dem Phänomen des Sputterns, bei dem hochenergetische Ionen (in der Regel Argon-Ionen) auf ein festes Zielmaterial treffen.
- Durch die Kollision wird ein Impuls auf die Zielatome übertragen, so dass sie von der Oberfläche abgestoßen werden und in die Gasphase übergehen.
- Diese ausgestoßenen Atome wandern durch eine Vakuumumgebung und lagern sich auf einem Substrat ab, wobei sie einen dünnen Film bilden.
-
Die Rolle des Plasmas beim Sputtern:
- Ein Plasma wird durch Ionisierung eines Prozessgases, in der Regel Argon, in einer Vakuumkammer erzeugt.
- Das Plasma besteht aus positiv geladenen Argon-Ionen und freien Elektronen.
- Das Zielmaterial ist negativ geladen (Kathode) und zieht die positiv geladenen Ionen aus dem Plasma an.
- Die hochenergetischen Ionen beschießen das Target und stoßen die Atome durch Impulsübertragung aus.
-
Auswurf und Ablagerung von Zielatomen:
- Die aus dem Target ausgestoßenen Atome befinden sich in einem hochenergetischen Zustand, der es ihnen ermöglicht, sich ballistisch durch die Vakuumkammer zu bewegen.
- Diese Atome kondensieren auf dem Substrat und bilden einen dünnen Film mit starker Haftung und Gleichmäßigkeit.
- Das Verfahren ist hochgradig richtungsabhängig und ermöglicht eine präzise Kontrolle der Schichtdicke und -zusammensetzung.
-
Vorteile gegenüber anderen Abscheidungsmethoden:
- Im Vergleich zur thermischen Verdampfung entstehen beim Sputtern Schichten mit besserer Haftung und Dichte aufgrund der höheren Energie der gesputterten Atome.
- Das Verfahren eignet sich für eine breite Palette von Werkstoffen, darunter Metalle, Legierungen und Keramiken.
- Das Verfahren kann für großflächige Beschichtungen skaliert werden und ist mit komplexen Geometrien kompatibel.
-
Magnetron-Sputtern:
- Das Magnetron-Sputtern ist eine fortschrittliche Form der Sputterabscheidung, bei der Magnetfelder eingesetzt werden, um das Plasma in der Nähe der Zieloberfläche zu konzentrieren.
- Dadurch werden die Ionisierungseffizienz und die Sputterrate erhöht, was zu einer schnelleren Abscheidung und besseren Schichtqualität führt.
- Das Magnetronsputtern ist besonders nützlich für die Abscheidung dichter, gleichmäßiger Schichten auf komplexen Substraten.
-
Anwendungen der Sputter-Beschichtung:
- Halbleiter:Wird für die Abscheidung von leitenden und isolierenden Schichten in integrierten Schaltungen verwendet.
- Optik:Beschichtung von Linsen und Spiegeln mit antireflektierenden oder reflektierenden Schichten.
- Solarzellen:Abscheidung von Dünnschichten für photovoltaische Anwendungen.
- Dekorative Beschichtungen:Dauerhafte und ästhetisch ansprechende Beschichtungen auf Konsumgütern.
-
Resputtering und Filmqualität:
- Resputtering tritt auf, wenn die abgeschiedenen Atome durch weiteren Ionenbeschuss wieder aus dem Substrat emittiert werden.
- Dies kann sich auf die Gleichmäßigkeit und die Zusammensetzung der Schicht auswirken, kann aber auch gesteuert werden, um die Schichteigenschaften zu verbessern.
- Die ordnungsgemäße Kontrolle der Prozessparameter, wie Druck, Leistung und Substratvorspannung, ist entscheidend für die Erzielung hochwertiger Filme.
-
Prozesskontrolle und Parameter:
- Zu den wichtigsten Parametern bei der Sputterbeschichtung gehören Gasdruck, Ionenenergie, Targetmaterial und Substrattemperatur.
- Diese Parameter beeinflussen die Zerstäubungsrate, die Schichtdichte und die Haftung.
- Moderne Systeme umfassen häufig eine In-situ-Überwachung und eine Rückkopplungssteuerung zur Optimierung der Schichteigenschaften.
Zusammenfassend lässt sich sagen, dass die Sputterdeposition ein vielseitiges und präzises Verfahren für die Abscheidung dünner Schichten ist, das den physikalischen Prozess des Sputterns nutzt, um hochwertige Beschichtungen herzustellen.Die Fähigkeit, mit einer breiten Palette von Materialien zu arbeiten und dichte, konforme Schichten zu erzeugen, macht es in vielen High-Tech-Industrien unverzichtbar.
Zusammenfassende Tabelle:
Aspekt | Einzelheiten |
---|---|
Mechanismus | Hochenergetische Ionen beschießen ein Ziel und schleudern Atome aus, die sich auf einem Substrat ablagern. |
Die Rolle des Plasmas | Das Argonplasma ionisiert und erzeugt Ionen, die das Zielmaterial zerstäuben. |
Vorteile | Erzeugt dichte, gleichmäßige Schichten; eignet sich für Metalle, Legierungen und Keramiken. |
Magnetron-Zerstäubung | Nutzt Magnetfelder zur Verbesserung der Sputtering-Raten und der Schichtqualität. |
Anwendungen | Halbleiter, Optik, Solarzellen und dekorative Beschichtungen. |
Prozesskontrolle | Schlüsselparameter: Gasdruck, Ionenenergie, Targetmaterial, Substrattemperatur. |
Entdecken Sie, wie die Sputterdeposition Ihre Dünnschichtanwendungen revolutionieren kann. Kontaktieren Sie unsere Experten noch heute !