Spark Plasma Sintering (SPS) ist ein fortschrittliches Sinterverfahren, das gepulsten elektrischen Gleichstrom mit einachsigem Druck kombiniert, um eine schnelle Verdichtung von Werkstoffen zu erreichen.Bei diesem Verfahren wird ein gepulster Gleichstrom durch eine leitfähige Graphitmatrize und ggf. durch das Material selbst geleitet.Dadurch werden lokal hohe Temperaturen, Plasma und Joule-Erwärmung erzeugt, die die Partikeloberflächen aktivieren und eine schnelle Bindung und Verdichtung fördern.SPS ermöglicht deutlich niedrigere Sintertemperaturen, schnellere Aufheiz- und Abkühlraten und kürzere Haltezeiten im Vergleich zu herkömmlichen Sinterverfahren.Das Ergebnis sind hochdichte Werkstoffe mit verbesserten Eigenschaften, die häufig eine Dichte von 99 % überschreiten.
Die wichtigsten Punkte werden erklärt:
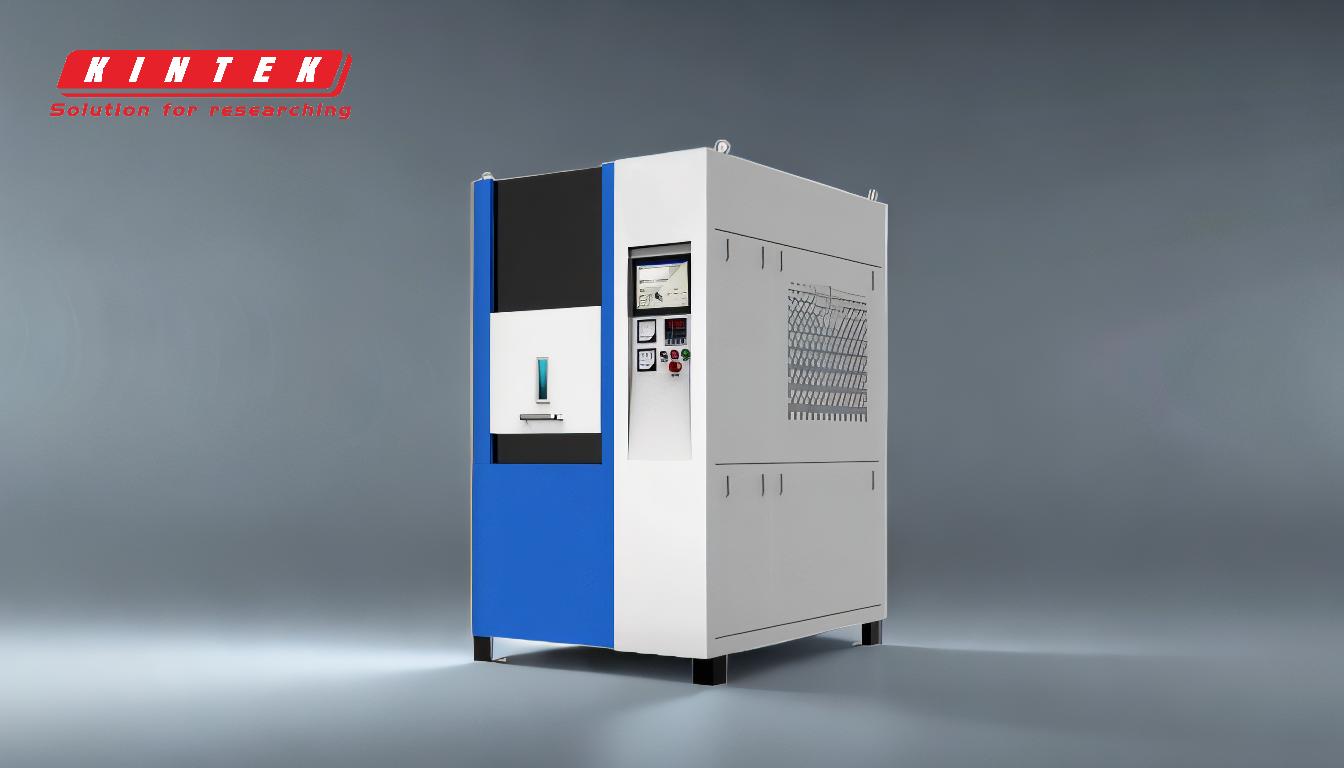
-
Anwendung von gepulstem Gleichstrom:
- Bei SPS wird ein gepulster Gleichstrom verwendet, der durch eine leitfähige Graphitmatrize und in einigen Fällen direkt durch das zu sinternde Material geleitet wird.
- Der gepulste Strom (Ein- und Ausschaltzyklen) erzeugt lokal hohe Temperaturen und ein Plasma zwischen den Partikeln, was die Oberflächenaktivierung und die Bindung verbessert.
-
Erzeugung von Plasma und Hochtemperaturen:
- Der gepulste Strom erzeugt ein Funkenplasma zwischen den Partikeln, das extrem hohe Temperaturen erreicht (bis zu 10.000°C oder 18.032°F).
- Diese hohen Temperaturen bewirken, dass Oberflächenverunreinigungen oxidieren oder verdampfen und gleichzeitig die Partikeloberflächen schmelzen und miteinander verschmelzen, so dass "Nacken" entstehen, die sich schließlich zu dichten Strukturen entwickeln.
-
Joule-Erwärmung und gleichmäßige Wärmeverteilung:
- Die Joule-Erwärmung tritt auf, wenn der elektrische Strom durch das Material fließt, wodurch im Sinterkörper gleichmäßig Wärme erzeugt wird.
- Diese gleichmäßige Erwärmung erleichtert die schnelle Verdichtung, indem sie die Oberflächendiffusion und die Diffusion von Grenzdefekten fördert, die für den Sinterprozess entscheidend sind.
-
Uniaxialer Druck Anwendung:
- Zusätzlich zum elektrischen Strom wird während des Sintervorgangs ein einachsiger Druck auf das Material ausgeübt.
- Die Kombination aus Druck und elektrischem Strom verbessert die Partikelbindung und verringert die Porosität, was zu einer höheren Materialdichte führt.
-
Schnelle Verdichtung und niedrigere Sintertemperaturen:
- SPS ermöglicht schnelle Aufheiz- und Abkühlraten sowie kürzere Haltezeiten im Vergleich zu herkömmlichen Sinterverfahren.
- Das Verfahren ermöglicht eine Verdichtung bei deutlich niedrigeren Temperaturen (oft Hunderte von Grad niedriger), was dazu beiträgt, die Mikrostruktur und die Eigenschaften des Materials zu erhalten.
-
Mechanismen der Partikelbindung:
- Der gepulste Strom erzeugt Entladungsstoßdruck und elektrische Felddiffusion, die die Partikeloberflächen aktivieren und die Bindung fördern.
- Die Grenzflächen der Partikel schmelzen und verbinden sich miteinander und bilden dichte Strukturen mit minimaler Porosität.
-
Alternative Bezeichnungen und Missverständnisse:
- Trotz des Namens "Spark Plasma Sintering" weisen Forschungsergebnisse darauf hin, dass bei diesem Verfahren nicht immer ein Plasma vorhanden ist.
- Alternative Bezeichnungen für das Verfahren sind Field Assisted Sintering Technique (FAST), Electric Field Assisted Sintering (EFAS) und Direct Current Sintering (DCS), was die primäre Rolle des elektrischen Feldes in diesem Prozess widerspiegelt.
-
Vorteile von SPS:
- Hohe Dichte:Mit SPS können Materialdichten von über 99 % erreicht werden, was das Verfahren ideal für die Herstellung von Hochleistungskeramik und Metallen macht.
- Wirkungsgrad:Die schnellen Aufheiz- und Abkühlraten in Verbindung mit niedrigeren Sintertemperaturen reduzieren den Energieverbrauch und die Verarbeitungszeit.
- Kontrolle der Mikrostruktur:Die niedrigeren Temperaturen und kürzeren Prozesszeiten tragen dazu bei, dass feine Mikrostrukturen erhalten bleiben, die beim herkömmlichen Sintern oft verloren gehen.
-
Anwendungen von SPS:
- SPS findet breite Anwendung bei der Herstellung von Hochleistungskeramik, Metallen und Verbundwerkstoffen.
- Es ist besonders wertvoll für Materialien, die eine hohe Dichte, eine feine Korngröße und verbesserte mechanische Eigenschaften erfordern, wie z. B. Schneidwerkzeuge, Luft- und Raumfahrtkomponenten und biomedizinische Implantate.
-
Beschränkungen und Überlegungen:
- Das Verfahren erfordert eine spezielle Ausrüstung, einschließlich eines leitfähigen Graphitstempels und eines Leistungssteuerungsgeräts, das gepulste Gleichströme erzeugen kann.
- Die hohen Anfangskosten der SPS-Ausrüstung können den Einsatz in einigen Branchen einschränken, obwohl die Vorteile bei Hochleistungsanwendungen die Kosten oft überwiegen.
Zusammenfassend lässt sich sagen, dass das Spark-Plasma-Sintern eine hocheffiziente und effektive Sintertechnik ist, die gepulsten Gleichstrom, Plasmaerzeugung und einachsigen Druck nutzt, um eine schnelle Verdichtung von Werkstoffen bei niedrigeren Temperaturen zu erreichen.Seine Fähigkeit, dichte Hochleistungswerkstoffe mit feinen Mikrostrukturen herzustellen, macht es zu einem wertvollen Werkzeug für die moderne Fertigung und die Materialwissenschaft.
Zusammenfassende Tabelle:
Hauptaspekt | Beschreibung |
---|---|
Gepulster Gleichstrom | Erzeugt örtlich begrenzte hohe Temperaturen und Plasma für eine verbesserte Partikelbindung. |
Plasma und hohe Temperaturen | Erreicht bis zu 10.000°C und schmilzt und verschmilzt Partikeloberflächen zur Verdichtung. |
Joulesche Heizung | Gewährleistet eine gleichmäßige Wärmeverteilung für eine schnelle Verdichtung. |
Uniaxialer Druck | Verbessert die Partikelbindung und verringert die Porosität. |
Vorteile | Hohe Dichte (>99%), Effizienz und feine Mikrostrukturkontrolle. |
Anwendungen | Hochleistungskeramik, Metalle, Verbundwerkstoffe, Luft- und Raumfahrt und biomedizinische Implantate. |
Beschränkungen | Erfordert eine spezielle Ausrüstung und hat hohe Anfangskosten. |
Erfahren Sie, wie Spark Plasma Sintering Ihre Materialproduktion revolutionieren kann. Kontaktieren Sie uns noch heute !