Das Sintern von keramischen Werkstoffen ist ein kritischer Prozess, bei dem pulverförmige Keramiken durch eine Wärmebehandlung unterhalb des Schmelzpunktes in eine dichte, feste Struktur umgewandelt werden.Dieser Prozess umfasst mehrere Stufen, darunter die Vorbereitung des Pulverpresslings, die Erhitzung zur Entfernung von Bindemitteln und die Hochtemperatursinterung zur Verschmelzung der Partikel.Zu den Schlüsselvariablen, die die Sinterung beeinflussen, gehören Temperatur, Atmosphäre, Druck und Partikelgröße, die zusammen die endgültigen Materialeigenschaften wie Festigkeit, Porosität und Dichte bestimmen.Der Sinterprozess kann durch die Steuerung dieser Parameter optimiert werden, um die gewünschten Eigenschaften des keramischen Endprodukts zu erreichen.
Die wichtigsten Punkte werden erklärt:
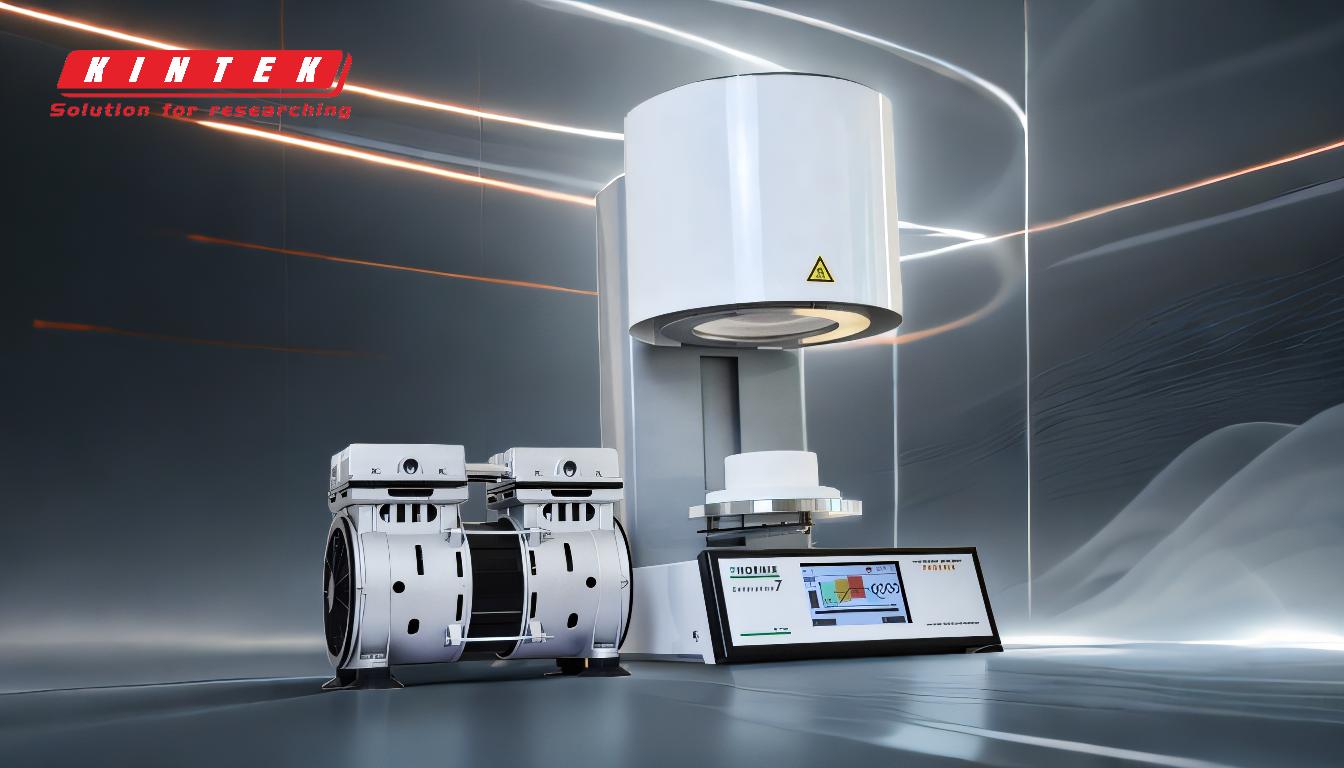
-
Vorbereitung des Pulvers Kompakt:
- Mischen und Aufschlämmung: Das Verfahren beginnt mit dem Mischen von ungebranntem Keramikpulver mit Wasser, Bindemitteln und Entflockungsmitteln, um eine Aufschlämmung zu bilden.Diese Aufschlämmung wird dann sprühgetrocknet, um ein frei fließendes Pulver zu erhalten.
- Pressen zum Grünkörper: Das sprühgetrocknete Pulver wird in eine Form gepresst, um einen "Grünkörper" zu bilden, der ein geformtes, aber ungebranntes Keramikteil ist.Dieser Schritt ist entscheidend, um die gewünschte Form und Anfangsdichte zu erreichen.
-
Entfernung des Bindemittels:
- Erhitzen bei niedriger Temperatur: Der Grünling wird auf eine niedrige Temperatur erhitzt, um das Bindemittel auszubrennen.Dieser Schritt ist wichtig, um Defekte im Endprodukt zu vermeiden, da Bindemittelreste beim Hochtemperatursintern Porosität oder Risse verursachen können.
-
Hochtemperatursintern:
- Erhitzen bis knapp unter den Schmelzpunkt: Der Grünling wird dann auf eine hohe Temperatur erhitzt, die knapp unter dem Schmelzpunkt des keramischen Materials liegt.In diesem Schritt können die Partikel diffundieren und sich miteinander verbinden, wodurch die Porosität verringert und die Dichte erhöht wird.
- Partikelverschmelzung und Verdichtung: Während des Sinterns verdichten sich die Partikel und verschmelzen, was durch Techniken wie das Flüssigphasensintern (LPS) beschleunigt werden kann.Bei diesem Prozess diffundiert das Material von den Partikeloberflächen zu den Kontaktpunkten zwischen den Partikeln, was zur Bildung von Einschnürungen und schließlich zum Verschmelzen führt.
-
Abkühlung und Erstarrung:
- Kontrollierte Abkühlung: Nach dem Sintern wird das Material kontrolliert abgekühlt, damit es zu einer einheitlichen Masse erstarrt.Die Abkühlungsgeschwindigkeit kann das endgültige Mikrogefüge und die Eigenschaften der Keramik beeinflussen.
-
Faktoren, die die Sinterung beeinflussen:
- Temperatur: Höhere Temperaturen erhöhen im Allgemeinen die Sintergeschwindigkeit und verbessern die Materialeigenschaften wie Zugfestigkeit und Kerbschlagarbeit.Zu hohe Temperaturen können jedoch zu unerwünschtem Kornwachstum führen.
- Atmosphäre: Die Sinteratmosphäre (z. B. Luft, Vakuum oder Inertgase wie Argon oder Stickstoff) kann den Oxidationszustand der Keramik und die Geschwindigkeit der Partikeldiffusion beeinflussen.
- Druck: Die Anwendung von Druck während des Sinterns kann die Umlagerung der Partikel fördern und die Porosität verringern, was zu einem dichteren Endprodukt führt.
- Partikelgröße und -zusammensetzung: Kleinere Partikel und homogene Zusammensetzungen begünstigen eine bessere Verdichtung und eine gleichmäßigere Sinterung.Die Wahl des Sinterverfahrens und der Parameter hängt von den gewünschten Eigenschaften des keramischen Endprodukts ab.
-
Optimierung des Sinterprozesses:
- Kontrolle der Parameter: Der Sinterprozess kann durch eine sorgfältige Kontrolle von Parametern wie Sintertemperatur, angewandter Druck und Gasatmosphäre optimiert werden.Feinere Pulver und höhere Temperaturen können die Verdichtung erhöhen, aber die Menge der flüssigen Phase muss sorgfältig gesteuert werden, um Defekte zu vermeiden.
- Endgültige Porosität: Die Endporosität der gesinterten Keramik hängt von der Anfangsporosität des Grünlings sowie von der Temperatur und der Dauer des Sinterprozesses ab.Reine Oxidkeramiken beispielsweise benötigen aufgrund der Festkörperdiffusion längere Sinterzeiten und höhere Temperaturen.
Durch das Verständnis und die Kontrolle dieser Schlüsselaspekte können die Hersteller hochwertige keramische Werkstoffe mit maßgeschneiderten Eigenschaften für verschiedene Anwendungen herstellen.
Zusammenfassende Tabelle:
Stufe | Schlüssel Prozess | Zweck |
---|---|---|
Vorbereitung des Pulvers | Mischen von Keramikpulver mit Bindemitteln, Wasser und Entflockungsmitteln zu einem Schlamm. | Erzeugt ein frei fließendes Pulver für die Formgebung. |
Formung des Grünlings | Pressen des Pulvers in eine Form, um ein ungebranntes Keramikteil zu formen. | Erzielt die gewünschte Form und Ausgangsdichte. |
Entfernung von Bindemitteln | Erhitzen bei niedriger Temperatur zum Abbrennen von Bindemitteln. | Verhindert Defekte wie Porosität oder Rissbildung während des Sinterns. |
Hochtemperatursintern | Erhitzen knapp unter dem Schmelzpunkt, um Partikel zu verschmelzen. | Verringert die Porosität und erhöht die Dichte durch Diffusion der Partikel. |
Kühlung | Kontrollierte Abkühlung zur Verfestigung des Materials. | Beeinflusst das endgültige Mikrogefüge und die Eigenschaften. |
Schlüsselvariablen | Temperatur, Atmosphäre, Druck und Partikelgröße. | Bestimmt die endgültigen Materialeigenschaften wie Festigkeit und Porosität. |
Optimieren Sie Ihren keramischen Sinterprozess für hervorragende Ergebnisse - Kontaktieren Sie unsere Experten noch heute !