Die Vakuumverdampfung ist ein Verfahren, das in verschiedenen Industriezweigen eingesetzt wird, insbesondere bei der Beschichtung und der Abwasserbehandlung, wo Materialien in einer Vakuumumgebung erhitzt werden, um von einer festen oder flüssigen Phase in eine Gasphase überzugehen.Bei dieser Methode werden die Prinzipien der thermischen Energie und der Vakuumbedingungen genutzt, um eine effiziente Materialabscheidung oder -trennung zu erreichen.Das Verfahren wird wegen seiner Präzision, Energieeffizienz und der Fähigkeit, hochwertige Ergebnisse zu erzielen, sehr geschätzt.Im Folgenden werden die wichtigsten Aspekte der Vakuumverdampfung, einschließlich ihrer Mechanismen, Vorteile und Anwendungen, erläutert.
Die wichtigsten Punkte erklärt:
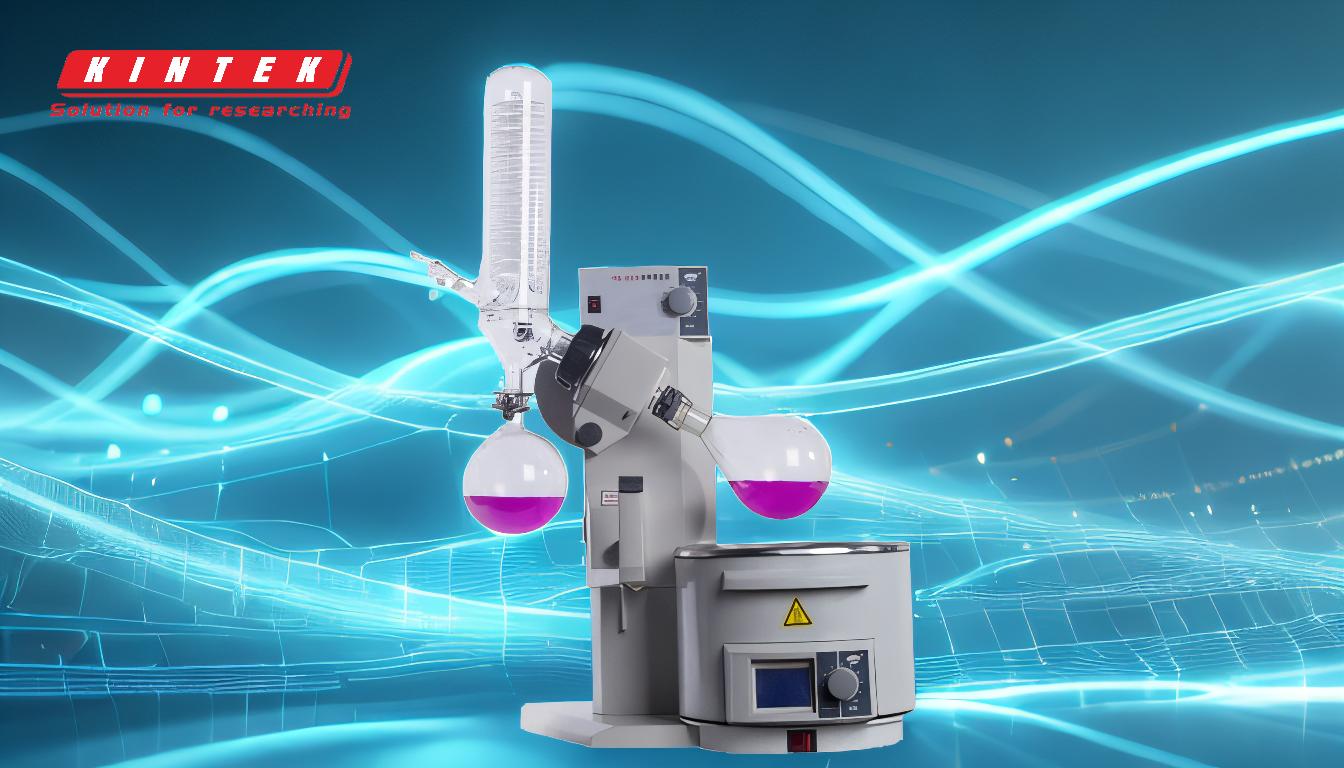
-
Mechanismus der Vakuumverdampfung:
- Heizung und Verdampfung:Bei der Vakuumverdampfung wird das abzuscheidende oder abgetrennte Material erhitzt, bis es eine Temperatur erreicht, bei der sein Dampfdruck signifikant wird.Diese Erhitzung kann durch elektrischen Widerstand oder durch Elektronenstrahlverfahren erfolgen.Das Material geht dann von einem festen oder flüssigen Zustand in eine Gasphase über.
- Vakuum Umgebung:Die Vakuumkammer reduziert den Druck, wodurch der Siedepunkt des Materials gesenkt wird.Dies ermöglicht die Verdampfung bei niedrigeren Temperaturen, wodurch der Energieverbrauch gesenkt und die thermische Schädigung empfindlicher Materialien minimiert wird.
-
Arten der Beheizung bei der Vakuumverdampfung:
- Widerstandsheizung:Bei dieser Methode wird das Material durch elektrischen Widerstand erhitzt.Sie wird in der Regel für Materialien mit niedrigeren Schmelzpunkten verwendet.
- Elektronenstrahl-Erwärmung:Bei dieser Technik wird ein fokussierter Strahl hochenergetischer Elektronen zur Erhitzung des Materials verwendet.Es eignet sich für Materialien mit höherem Schmelzpunkt und ermöglicht eine präzise Steuerung des Verdampfungsprozesses.
-
Kondensation und Abscheidung:
- Sobald das Material verdampft ist, wandert es durch die Vakuumkammer und kondensiert auf einem Substrat.Durch den Kondensationsprozess bildet sich eine dünne, gleichmäßige Schicht des Materials auf dem Substrat, die für Anwendungen in der Beschichtung und Dünnschichtabscheidung entscheidend ist.
-
Vorteile der Vakuumverdampfung:
- Energie-Effizienz:Der reduzierte Druck in der Vakuumkammer senkt den Siedepunkt des Materials, was zu einem geringeren Energieverbrauch führt.
- Hochwertige Beschichtungen:Das Verfahren erzeugt hochwertige, dauerhafte Schichten mit hervorragender Haftung und Gleichmäßigkeit.
- Vorteile für die Umwelt:Die Vakuumverdampfung reduziert das Abwasservolumen um bis zu 95 % und ermöglicht das Recycling der verdampften Produkte.Außerdem werden keine chemischen Zusätze benötigt, was das Verfahren zu einer umweltfreundlichen Option macht.
-
Anwendungen der Vakuumverdampfung:
- Dünnschichtabscheidung:Wird bei der Herstellung von optischen Beschichtungen, Halbleiterbauelementen und Sonnenkollektoren verwendet.
- Behandlung von Abwässern:Wird eingesetzt, um Wasser von Verunreinigungen mit hohem Siedepunkt zu trennen, was zu einer Verringerung des Abfallvolumens und der Rückgewinnung von Wertstoffen führt.
-
Vorteile gegenüber anderen Methoden:
- Präzision und Kontrolle:Die Vakuumumgebung ermöglicht eine präzise Kontrolle der Verdampfungsrate und des Abscheidungsprozesses, was zu konsistenten und zuverlässigen Ergebnissen führt.
- Sicherheit:Niedrigere Betriebstemperaturen verringern das Risiko des thermischen Abbaus und machen das Verfahren sicherer im Umgang mit hochsiedenden Lösungsmitteln.
Zusammenfassend lässt sich sagen, dass die Vakuumverdampfung ein vielseitiges und effizientes Verfahren ist, das thermische Energie und Vakuumbedingungen nutzt, um eine Materialabscheidung oder -trennung zu erreichen.Zu seinen Vorteilen gehören Energieeffizienz, qualitativ hochwertige Ergebnisse und Umweltvorteile, was es zu einer bevorzugten Methode in verschiedenen industriellen Anwendungen macht.
Zusammenfassende Tabelle:
Aspekt | Wichtige Details |
---|---|
Mechanismus | Erhitzen des Materials im Vakuum zum Übergang von der festen/flüssigen in die Gasphase. |
Erhitzungsmethoden | Widerstandsheizung für niedrige Schmelzpunkte; Elektronenstrahl für hohe Schmelzpunkte. |
Kondensation | Das Material kondensiert auf einem Substrat und bildet gleichmäßige Schichten. |
Vorteile | Energieeffizienz, hochwertige Beschichtungen und Umweltvorteile. |
Anwendungen | Dünnschichtabscheidung, Abwasserbehandlung und mehr. |
Entdecken Sie, wie die Vakuumverdampfung Ihre Prozesse revolutionieren kann. Kontaktieren Sie unsere Experten noch heute !