Die chemische Gasphasenabscheidung (Chemical Vapor Deposition, CVD) ist ein vielseitiges Verfahren zur Abscheidung hochwertiger dünner Schichten und Beschichtungen auf verschiedenen Substraten.Das Substrat spielt beim CVD-Verfahren eine entscheidende Rolle, da es den hohen Temperaturen und den damit verbundenen chemischen Reaktionen standhalten muss.Zu den üblichen Substraten gehören Siliziumwafer, Glas, Metalle und Keramik, die je nach ihrer thermischen Stabilität, chemischen Verträglichkeit und ihrem Verwendungszweck ausgewählt werden.Das CVD-Verfahren umfasst Gasphasenreaktionen und Oberflächenreaktionen, die mit verschiedenen Methoden wie aerosolgestützter CVD, direkter Flüssigkeitsinjektion oder plasmabasierten Techniken auf die spezifischen Substratanforderungen zugeschnitten werden können.
Schlüsselpunkte erklärt:
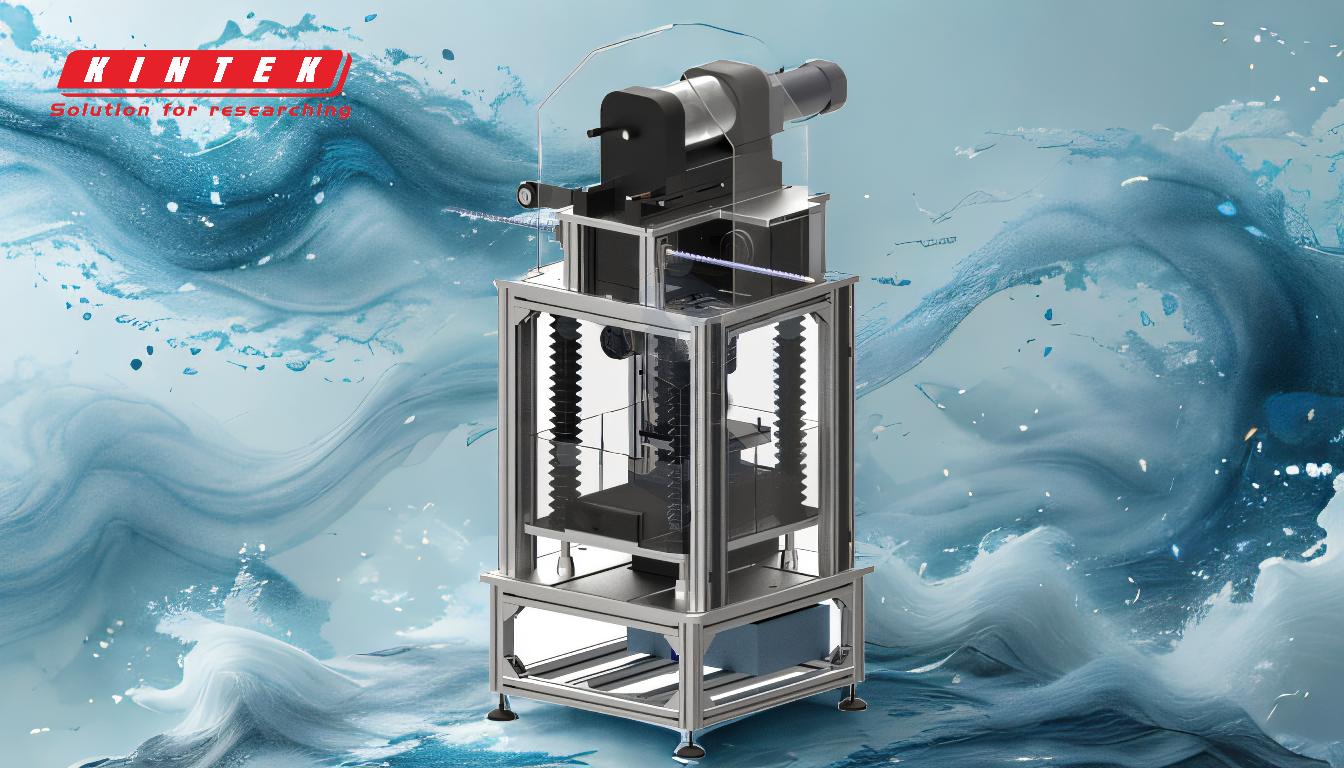
-
Die Rolle der Substrate bei CVD:
- Substrate sind die Grundlage für die Dünnschichtabscheidung im CVD-Verfahren.Sie müssen thermisch stabil, chemisch verträglich und mechanisch robust sein, um den Prozessbedingungen standzuhalten.
- Die Wahl des Substrats hängt von der Anwendung ab, z. B. Halbleiter, Optik oder Schutzschichten.
-
Gängige Substratmaterialien:
- Silizium-Wafer:Aufgrund ihrer hervorragenden thermischen und elektrischen Eigenschaften werden sie häufig in der Halbleiterherstellung verwendet.
- Glas:Wird wegen seiner Transparenz und glatten Oberfläche in optischen und Display-Anwendungen verwendet.
- Metalle:Häufig für Schutzschichten oder als leitende Schichten in elektronischen Geräten verwendet.
- Keramiken:Ausgewählt wegen ihrer hohen thermischen Stabilität und Beständigkeit gegen chemische Reaktionen.
-
Thermische und chemische Kompatibilität:
- CVD erfordert in der Regel hohe Temperaturen (850-1100 °C), so dass die Substrate diesen Bedingungen standhalten müssen, ohne zu zerfallen.
- Durch plasma- oder lasergestütztes CVD kann die Temperatur gesenkt werden, wodurch sich die Palette der geeigneten Substrate erweitert.
-
Arten von CVD und Überlegungen zum Substrat:
- Aerosol-unterstützte CVD:Verwendet aerosolierte Ausgangsstoffe, geeignet für Substrate, die gleichmäßige Beschichtungen erfordern.
- Direkte Flüssigkeitsinjektion CVD:Mit flüssigen Ausgangsstoffen, ideal für Substrate, die eine genaue Kontrolle der Schichtzusammensetzung erfordern.
- Plasma-basiertes CVD:Nutzt Plasma zur Senkung der Abscheidetemperaturen und ermöglicht so die Verwendung von temperaturempfindlichen Substraten.
-
Anwendungen von CVD-Substraten:
- Halbleiter:Siliziumwafer sind das wichtigste Substrat für Mikroelektronik und integrierte Schaltungen.
- Optik:Glassubstrate werden für Antireflexionsbeschichtungen und optische Filter verwendet.
- Schützende Beschichtungen:Metalle und Keramiken werden beschichtet, um die Haltbarkeit und Widerstandsfähigkeit gegen Verschleiß und Korrosion zu erhöhen.
-
Herausforderungen und Lösungen:
- Hohe Temperaturen können die Auswahl an Substraten einschränken.Moderne Techniken wie plasmagestütztes CVD oder lasergestütztes CVD schaffen hier Abhilfe, indem sie die Verarbeitung bei niedrigeren Temperaturen ermöglichen.
- Die Vorbereitung der Substratoberfläche, z. B. die Reinigung und Vorbehandlung, ist entscheidend für eine gute Haftung und die Qualität der Schichten.
Wenn die Hersteller die Eigenschaften und Anforderungen der verschiedenen Substrate kennen, können sie das CVD-Verfahren für bestimmte Anwendungen optimieren und so hochwertige dünne Schichten und Beschichtungen gewährleisten.
Zusammenfassende Tabelle:
Substrat | Wichtige Eigenschaften | Anwendungen |
---|---|---|
Silizium-Wafer | Thermische Stabilität, elektrische Eigenschaften | Halbleiter, Mikroelektronik |
Glas | Transparenz, glatte Oberfläche | Optik, Display-Beschichtungen |
Metalle | Leitfähigkeit, Haltbarkeit | Schutzbeschichtungen, elektronische Geräte |
Keramiken | Thermische Stabilität, chemische Beständigkeit | Hochtemperaturanwendungen, Beschichtungen |
Benötigen Sie Hilfe bei der Auswahl des richtigen Substrats für Ihr CVD-Verfahren? Kontaktieren Sie noch heute unsere Experten für maßgeschneiderte Lösungen!