Das zweistufige Sinterverfahren (TSS) ist eine fortschrittliche Sintertechnik zur Herstellung feinkörniger keramischer Werkstoffe mit hoher Verdichtung und hervorragenden mechanischen Eigenschaften.Im Gegensatz zum herkömmlichen Sintern, bei dem ein einziger Erhitzungszyklus durchgeführt wird, werden beim TSS-Verfahren zwei unterschiedliche Temperaturstufen verwendet, um das Kornwachstum zu kontrollieren und gleichzeitig eine vollständige Verdichtung zu erreichen.Diese Methode ist besonders effektiv für Keramiken, einschließlich Strukturkeramik, Biokeramik, Ferrite, piezoelektrische Keramiken und Elektrolytkeramiken.TSS ermöglicht die Herstellung von Werkstoffen mit gleichmäßiger Korngrößenverteilung, erhöhter Hochtemperaturfestigkeit und verbesserten mechanischen Eigenschaften (z. B. Vickers-Härte) bei gleichzeitiger Wahrung der Kosten- und Energieeffizienz.
Die wichtigsten Punkte werden erklärt:
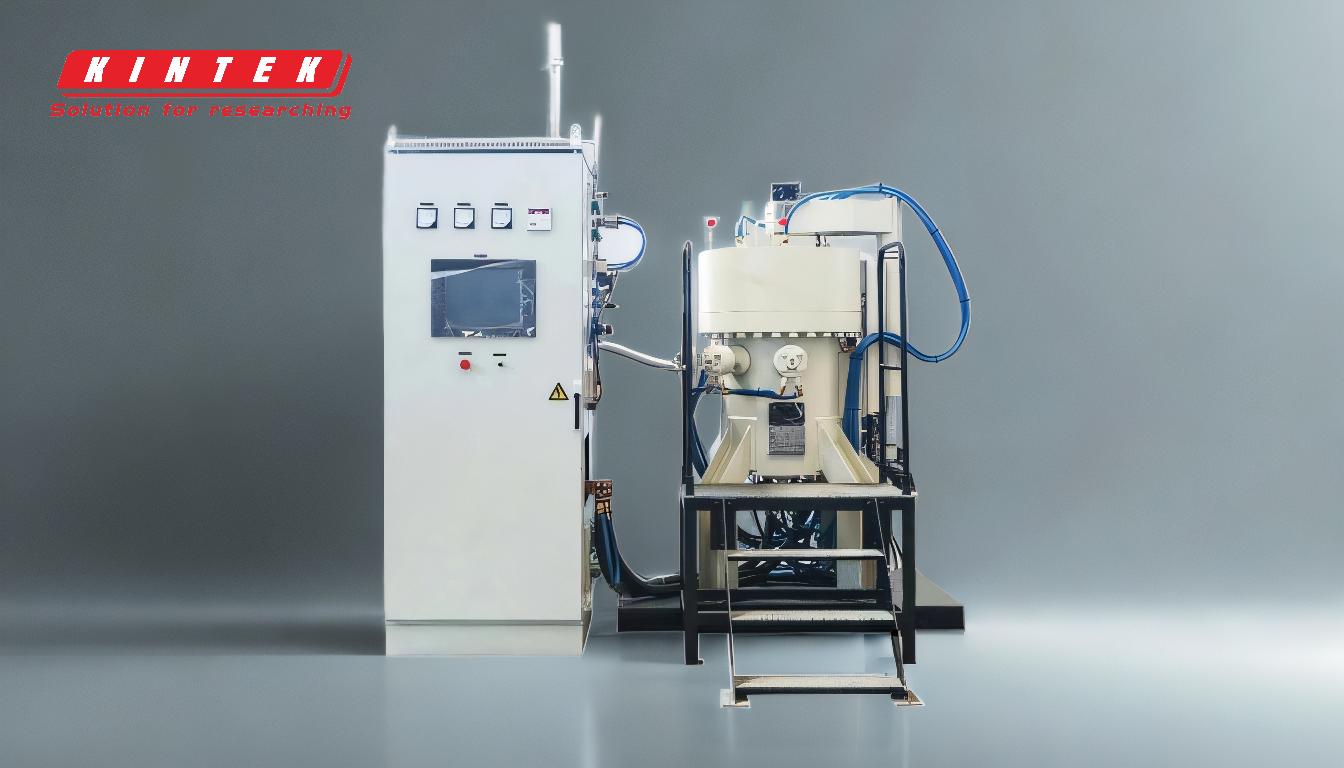
-
Definition und Verfahren des Zwei-Schritt-Sinterns:
- Das zweistufige Sintern (TSS) ist ein Sinterverfahren, das zwei unterschiedliche Temperaturstufen umfasst.In der ersten Stufe wird das Material auf eine höhere Temperatur erhitzt, um die Verdichtung einzuleiten, während in der zweiten Stufe das Material auf einer niedrigeren Temperatur gehalten wird, um die Verdichtung abzuschließen, ohne ein übermäßiges Kornwachstum zuzulassen.
- Dieses Verfahren steht im Gegensatz zum herkömmlichen Sintern, bei dem in der Regel ein einziger Erhitzungszyklus durchgeführt wird.TSS ist darauf ausgelegt, eine hohe Verdichtung zu erreichen und gleichzeitig das Kornwachstum zu minimieren, was zu feinkörnigen Mikrostrukturen führt.
-
Anwendungen des Zwei-Schritt-Sinterns:
-
TSS wird in großem Umfang für die Herstellung verschiedener Keramiken verwendet, darunter
- Strukturkeramiken: Für hochfeste und verschleißfeste Anwendungen.
- Bio-Keramik: Für medizinische Implantate und Prothetik.
- Ferrite: Für magnetische Anwendungen.
- Piezoelektrische Keramiken: Für Sensoren und Aktuatoren.
- Elektrolyt-Keramik: Für Brennstoffzellen und Batterien.
- Das Verfahren ist vielseitig und kann auf eine breite Palette keramischer Werkstoffe angewendet werden, was es zu einer wertvollen Technik in der Materialwissenschaft und -technik macht.
-
TSS wird in großem Umfang für die Herstellung verschiedener Keramiken verwendet, darunter
-
Vorteile des Zwei-Schritt-Sinterns:
- Feinkörniges Mikrogefüge: TSS ermöglicht die Herstellung von Keramiken mit gleichmäßiger und feiner Korngröße, die für eine hohe mechanische Festigkeit und Haltbarkeit entscheidend ist.
- Hohe Verdichtung: Das zweistufige Verfahren stellt sicher, dass das Material nahezu die theoretische Dichte erreicht, was zu verbesserten mechanischen und elektrischen Eigenschaften führt.
- Kosteneffizienz: Mit TSS lassen sich ähnliche oder bessere Ergebnisse erzielen als mit herkömmlichen Sinterverfahren, allerdings bei niedrigeren Temperaturen und mit geringerem Energieverbrauch.
- Verbesserte Hochtemperaturfestigkeit: Das Vorhandensein einer Glasphase und einer gleichmäßigen Korngrößenverteilung in den Kornzwischenräumen erhöht die Hochtemperatur-Biegefestigkeit des Materials und verzögert den Abfall der Festigkeit unter Hochtemperaturbedingungen.
-
Vergleich mit dem traditionellen Sintern:
- Beim herkömmlichen Sintern wird oft nur ein einziger Heizzyklus durchgeführt, was zu übermäßigem Kornwachstum und schlechteren mechanischen Eigenschaften führen kann.
- Im Gegensatz dazu steuert das TSS das Kornwachstum, indem es den Verdichtungsprozess in zwei Stufen aufteilt, was zu feineren Körnern und besseren Gesamteigenschaften des Materials führt.
- Mit TSS hergestellte Siliziumnitridproben weisen beispielsweise eine ähnliche Korngröße, Phasenzusammensetzung und Vickershärte (HV 1478) auf wie Proben, die 8 Stunden lang bei 1800 °C gesintert wurden, jedoch mit potenziell geringerem Energieverbrauch und geringeren Kosten.
-
Mechanische Eigenschaften und Leistung:
- Das durch TSS erzielte feinkörnige Gefüge führt zu verbesserten mechanischen Eigenschaften, wie z. B. einer höheren Vickershärte und einer verbesserten Hochtemperaturfestigkeit.
- Die gleichmäßige Korngrößenverteilung und das Vorhandensein einer Glasphase in den Kornzwischenräumen tragen dazu bei, dass das Material seine Festigkeit unter Hochtemperaturbedingungen beibehält.
- Aufgrund dieser Eigenschaften eignet sich TSS-Keramik für anspruchsvolle Anwendungen wie Turbinenschaufeln, bei denen es auf hohe Festigkeit und Haltbarkeit ankommt.
-
Energieeffizienz und Kostenaspekte:
- TSS ist energieeffizienter als herkömmliche Sinterverfahren, da es in der zweiten Stufe mit niedrigeren Temperaturen arbeitet und so den Gesamtenergieverbrauch senkt.
- Das Verfahren ermöglicht auch eine bessere Kontrolle des Verdichtungsprozesses, was zu qualitativ hochwertigeren Materialien mit weniger Defekten führt.
- Diese Faktoren tragen zur Kosteneffizienz des TSS-Verfahrens bei und machen es zu einer attraktiven Option für die großtechnische Herstellung von Hochleistungskeramik.
-
Vergleich mit anderen Sintertechniken:
- Heißpressen und Sintern: Beim Heißpresssintern werden zwar auch Werkstoffe mit hoher Dichte und feinem Korngefüge hergestellt, doch sind dafür spezielle Anlagen und höhere Drücke erforderlich.Beim TSS hingegen werden ähnliche Ergebnisse mit einfacheren Anlagen und geringeren Druckanforderungen erzielt.
- Hochtemperatursintern: Das Hochtemperatursintern kann die Materialeigenschaften erheblich verbessern, ist aber aufgrund des Bedarfs an speziellen Öfen teurer.TSS bietet eine kostengünstigere Alternative, bei der dennoch hervorragende Materialeigenschaften erzielt werden.
-
Zukunftsperspektiven und Forschungsrichtungen:
- Die laufende Forschung konzentriert sich auf die Optimierung des TSS-Verfahrens für verschiedene Keramiktypen und die Erkundung seines Potenzials für neue Anwendungen.
- Es wird erwartet, dass Fortschritte bei der Prozesssteuerung und -automatisierung, wie etwa der Einsatz von IT-Technologie, die Effizienz und Reproduzierbarkeit des TSS weiter verbessern werden.
- Die Entwicklung neuer keramischer Werkstoffe und Verbundwerkstoffe mit Hilfe des TSS könnte zu Durchbrüchen in Bereichen wie Energiespeicherung, Elektronik und Biomedizintechnik führen.
Zusammenfassend lässt sich sagen, dass das zweistufige Sinterverfahren eine äußerst wirksame Technik zur Herstellung feinkörniger Keramiken mit hoher Verdichtung und hervorragenden mechanischen Eigenschaften ist.Ihre Fähigkeit, das Kornwachstum zu kontrollieren, den Energieverbrauch zu reduzieren und die Produktionskosten zu senken, macht sie zu einem wertvollen Werkzeug auf dem Gebiet der Materialwissenschaft.Da Forschung und Technologie weiter voranschreiten, wird das TSS wahrscheinlich eine immer wichtigere Rolle bei der Entwicklung der nächsten Generation von keramischen Werkstoffen spielen.
Zusammenfassende Tabelle:
Aspekt | Einzelheiten |
---|---|
Verfahren | Zwei verschiedene Temperaturstufen: hohe Temperatur für die Verdichtung, niedrige Temperatur für die Kornkontrolle. |
Anwendungen | Strukturkeramiken, Biokeramiken, Ferrite, piezoelektrische Keramiken, Elektrolytkeramiken. |
Vorteile | Feinkörniges Gefüge, hohe Verdichtung, Kosteneffizienz, verbesserte Hochtemperaturfestigkeit. |
Vergleich mit dem herkömmlichen Sintern | Kontrolliertes Kornwachstum, feinere Körner, geringerer Energieverbrauch. |
Mechanische Eigenschaften | Hohe Vickers-Härte, gleichmäßige Korngröße, verbesserte Hochtemperaturfestigkeit. |
Energie-Effizienz | Niedrigere Temperaturen in der zweiten Stufe senken den Energieverbrauch. |
Zukunftsperspektiven | Optimierung des TSS für neue Materialien, Fortschritte bei der Prozesssteuerung und Automatisierung. |
Erfahren Sie, wie das zweistufige Sinterverfahren Ihre Keramikproduktion revolutionieren kann - Kontaktieren Sie unsere Experten noch heute !