Um eine inerte Atmosphäre für das Schweißen zu schaffen, werden üblicherweise Gase wie Argon, Stickstoff und Helium verwendet.Diese Gase sind chemisch inert, d. h. sie reagieren nicht mit den zu schweißenden Materialien und verhindern so Oxidation und andere unerwünschte chemische Reaktionen.Argon ist beim Schweißen besonders beliebt, da es den Schweißbereich wirksam vor Verunreinigungen abschirmt.Auch Stickstoff ist weit verbreitet, vor allem in Hochtemperaturbereichen, wo er über spezielle Anschlüsse eingeleitet werden kann, um eine schützende Umgebung zu schaffen.Die Wahl des Gases hängt von dem jeweiligen Schweißverfahren und den verwendeten Werkstoffen ab, um optimale Ergebnisse und qualitativ hochwertige Schweißnähte zu gewährleisten.
Die wichtigsten Punkte erklärt:
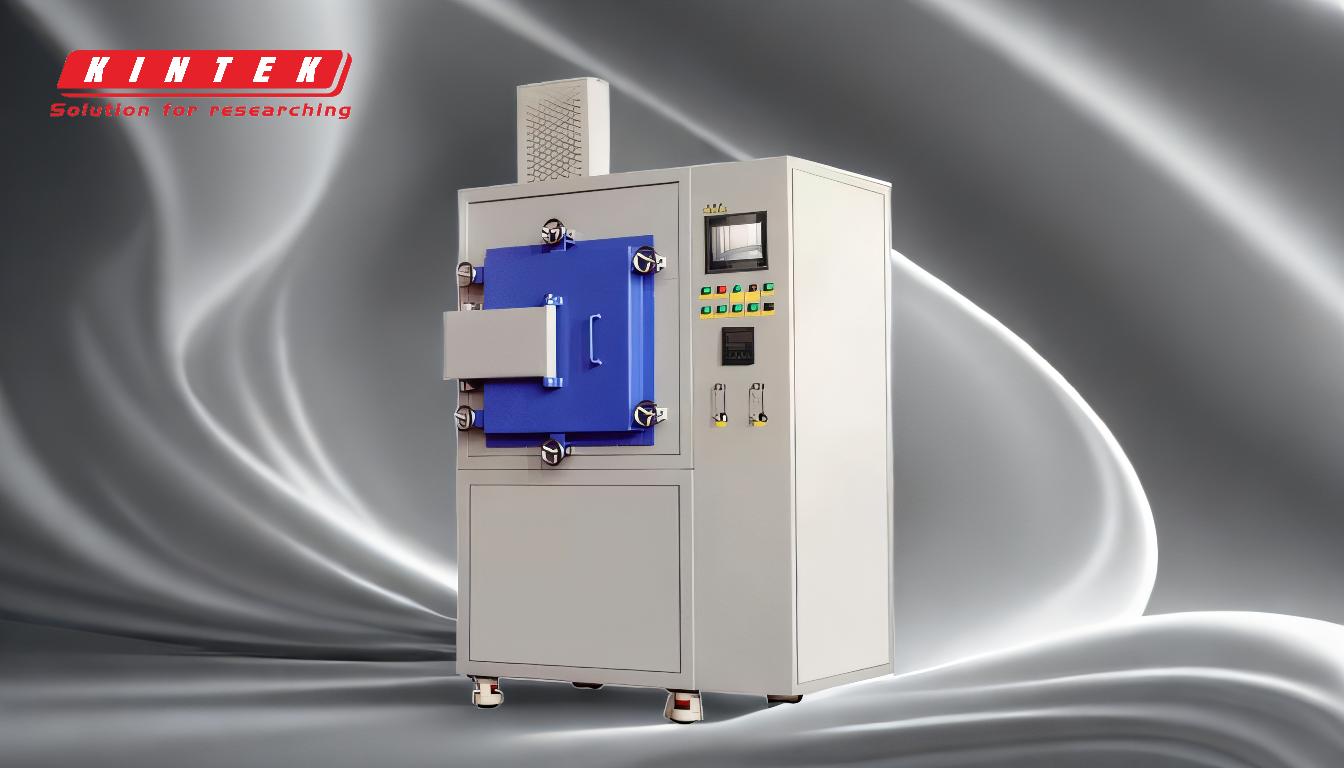
-
Argon als bevorzugtes Inertgas:
- Argon ist ein Edelgas, das chemisch inert ist und sich ideal für Schweißanwendungen eignet.Es schirmt das Schweißbad wirksam vor atmosphärischen Gasen wie Sauerstoff und Stickstoff ab, die Defekte wie Porosität und Oxidation verursachen können.
- Es wird häufig bei Verfahren wie WIG (Wolfram-Inertgas)-Schweißen und MIG (Metall-Inertgas)-Schweißen verwendet, da es einen stabilen Lichtbogen aufrechterhält und saubere Schweißnähte erzeugt.
-
Stickstoff für Hochtemperaturanwendungen:
- Stickstoff ist ein weiteres weit verbreitetes Inertgas, insbesondere in Hochtemperatur-Schweißumgebungen.Es kann durch winkelmäßig eingestellte Öffnungen oder als Stickstoff-"Vorhang" unter Verwendung einer fortschrittlichen Gasinjektionstechnologie eingespritzt werden.
- Dadurch werden transversale laminare Strahlströme erzeugt, die den Sauerstoff aus der Umgebung entfernen, Oxidation verhindern und eine saubere Schweißnaht gewährleisten.
-
Helium und andere Inertgase:
- Helium wird manchmal beim Schweißen verwendet, insbesondere bei Materialien, die eine höhere Wärmezufuhr erfordern.Es hat eine höhere Wärmeleitfähigkeit als Argon, was die Durchdringung der Schweißnaht und die Geschwindigkeit verbessern kann.
- Kohlendioxid wird ebenfalls als Option genannt, obwohl es aufgrund seiner Reaktivität im Vergleich zu Edelgasen weniger häufig für die Schaffung von Schutzgasatmosphären verwendet wird.
-
Industrielle Anwendungen und Gasauswahl:
- In der Industrie werden gereinigtes Argon und Stickstoff häufig für die Herstellung von Schutzgasatmosphären in Öfen und bei Schweißprozessen verwendet.Ihr hohes natürliches Vorkommen und ihre chemisch inaktiven Eigenschaften machen sie kostengünstig und zuverlässig.
- Die Auswahl des Gases hängt von den spezifischen Anforderungen des Schweißprozesses ab, einschließlich der Art des Materials, der gewünschten Schweißqualität und der Betriebsbedingungen.
-
Vorteile von Schutzgasatmosphären beim Schweißen:
- Verhindert Oxidation und Verunreinigung des Schweißbades.
- Sorgt für gleichbleibende und hochwertige Schweißnähte durch Aufrechterhaltung einer stabilen Umgebung.
- Verringert das Risiko von Fehlern wie Porosität, Rissen und Einschlüssen.
Durch die Verwendung dieser Schutzgase können Schweißer präzise und zuverlässige Ergebnisse erzielen, was sie sowohl für industrielle als auch für spezielle Schweißanwendungen unverzichtbar macht.
Zusammenfassende Tabelle:
Inertes Gas | Wichtige Eigenschaften | Gemeinsame Anwendungen |
---|---|---|
Argon | Chemisch inert, schirmt Schweißbad ab | TIG-Schweißen, MIG-Schweißen |
Stickstoff | Hohe Temperaturstabilität | Hochwärmeschweißzonen |
Helium | Hohe Wärmeleitfähigkeit | Materialien, die eine höhere Wärmezufuhr erfordern |
Kohlendioxid | Weniger verbreitet, reaktiv | Begrenzte Verwendung in Schutzgasatmosphären |
Erzielen Sie makellose Schweißnähte mit dem richtigen Schutzgas - Kontaktieren Sie noch heute unsere Experten für maßgeschneiderte Lösungen!