Vakuum ist für die Abscheidung dünner Schichten unerlässlich, da es eine Umgebung schafft, die Verunreinigungen minimiert, eine hochwertige Schichtbildung gewährleistet und eine präzise Steuerung des Abscheidungsprozesses ermöglicht.Durch die Verringerung der Partikeldichte und die Erhöhung der mittleren freien Weglänge der verdampften Atome sorgt eine Vakuumumgebung dafür, dass das Material effizient auf dem Substrat abgeschieden wird, ohne dass unerwünschte Gase oder Partikel stören.Das Ergebnis sind Schichten mit hoher Reinheit, starker Haftung und gleichbleibenden Eigenschaften, die für Anwendungen in der Elektronik, Optik und Beschichtung entscheidend sind.
Die wichtigsten Punkte werden erklärt:
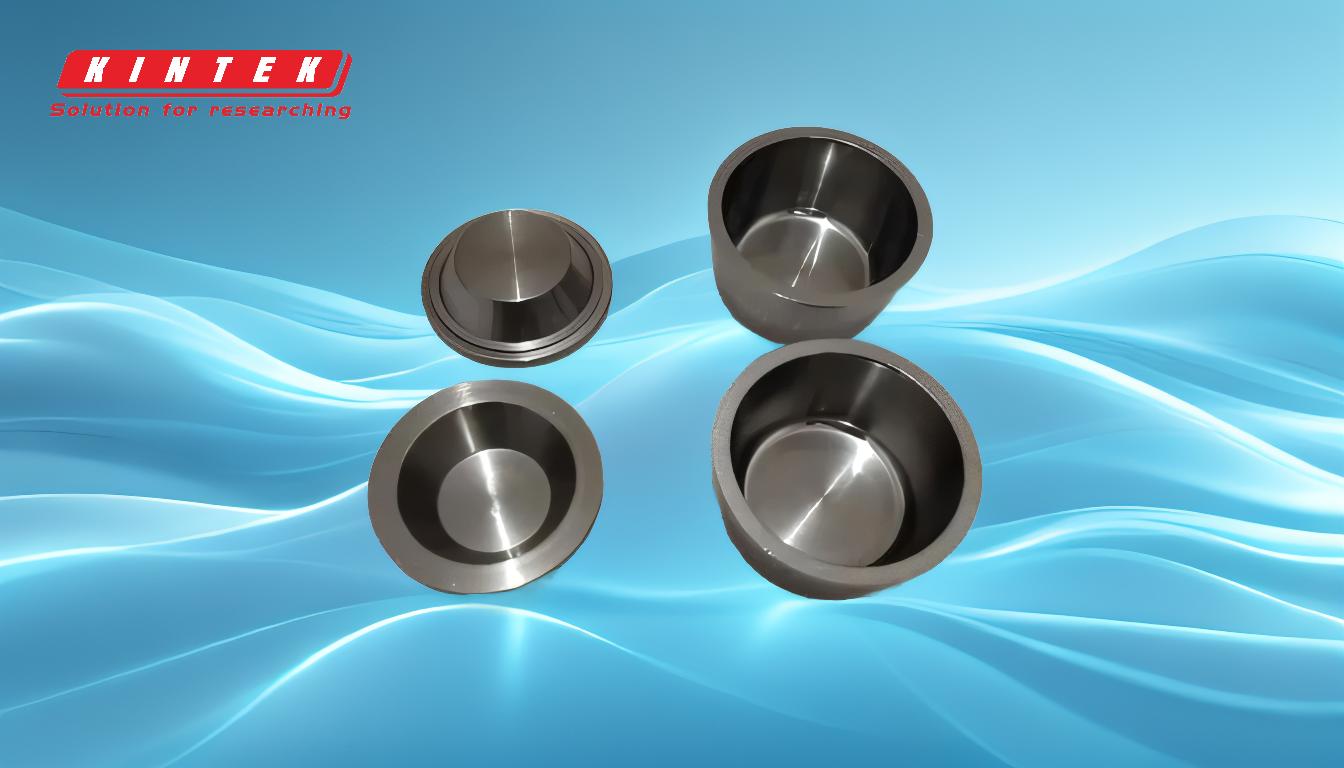
-
Verringerung der Verunreinigung
- Eine Vakuumumgebung reduziert das Vorhandensein unerwünschter Stoffe wie Sauerstoff, Stickstoff, Kohlendioxid und Wasserdampf erheblich.Diese Verunreinigungen können mit dem Filmmaterial reagieren und zu Verunreinigungen, Oxidation oder anderen chemischen Veränderungen führen, die die Qualität des Films beeinträchtigen.
- Bei PVD-Prozessen (Physical Vapor Deposition) beispielsweise wird durch die Aufrechterhaltung eines Vakuumdrucks von weniger als 10^-5 Torr sichergestellt, dass das Zielmaterial ohne Beeinträchtigung durch atmosphärische Gase verdampft, transportiert und kondensiert wird.
-
Erhöhter mittlerer freier Weg
- Die mittlere freie Weglänge ist die durchschnittliche Entfernung, die ein Atom oder Molekül zurücklegt, bevor es mit einem anderen Teilchen zusammenstößt.Im Vakuum können die verdampften Atome aufgrund der geringeren Teilchendichte längere Strecken ohne Zusammenstöße zurücklegen, so dass sie das Substrat effizient erreichen.
- Dies ist besonders wichtig bei Verfahren wie der Elektronenstrahlabscheidung, bei denen eine hohe mittlere freie Weglänge sicherstellt, dass der größte Teil des verdampften Materials auf dem Substrat abgeschieden wird, was die Verluste minimiert und die Abscheidungseffizienz verbessert.
-
Kontrolle über Gas- und Dampfzusammensetzung
- Eine Vakuumumgebung ermöglicht eine genaue Kontrolle über die Gas- und Dampfzusammensetzung in der Beschichtungskammer.Dies ist entscheidend für Verfahren, die bestimmte Gasmischungen oder Plasmabedingungen erfordern, um die gewünschten Schichteigenschaften zu erzielen.
- Beim Sputtern oder der plasmagestützten Abscheidung beispielsweise ermöglicht das Vakuum die Schaffung einer Niederdruck-Plasmaumgebung, die für die Ionisierung der Gase und die Steuerung der Energieverteilung der Partikel unerlässlich ist.
-
Minimierung der gasförmigen Verunreinigung
- Durch die Aufrechterhaltung eines Vakuums wird die Wahrscheinlichkeit gasförmiger Verunreinigungen verringert, was für die Herstellung hochreiner dünner Schichten von entscheidender Bedeutung ist.Verunreinigungen können die Haftfähigkeit des Films schwächen oder dazu führen, dass sich das Filmmaterial mit anderen Substanzen in der Luft verbindet, was zu Defekten führt.
- Bei Vakuumverdampfungsprozessen ist in der Regel ein Vakuumgrad von mehr als 6 x 10^-2 Pa erforderlich, um sicherzustellen, dass sich die verdampfenden Atome oder Moleküle störungsfrei auf dem Substrat absetzen.
-
Verbesserte Filmhaftung und Reinheit
- Ein Hochvakuum sorgt dafür, dass das Filmmaterial fest auf dem Substrat haftet und seine Reinheit beibehält.Ohne Vakuum können Luftmoleküle die Bewegung der Filmpartikel behindern, was zu schlechter Haftung und uneinheitlichen Filmeigenschaften führt.
- Dies ist besonders wichtig für Anwendungen, die Hochleistungsfilme erfordern, wie z. B. bei Halbleitern oder optischen Beschichtungen, bei denen selbst geringe Verunreinigungen die Leistung erheblich beeinträchtigen können.
-
Verbesserte Prozesskontrolle
- Die Vakuumbedingungen ermöglichen eine präzise Steuerung des Abscheidungsprozesses, einschließlich der Steuerung des Massenstroms, des Gasdrucks und der Plasmabedingungen.Dieses Maß an Kontrolle ist unerlässlich, um eine gleichmäßige Schichtdicke, Zusammensetzung und Eigenschaften auf dem Substrat zu erreichen.
- Bei Sputterprozessen beispielsweise ermöglicht die Vakuumumgebung eine präzise Regulierung des Gasdrucks und der Plasmadichte, die sich direkt auf die Abscheiderate und die Schichtqualität auswirken.
-
Einfluss auf Plasma und Energieverteilung
- Bei Plasmaprozessen wie dem Sputtern oder der plasmagestützten chemischen Gasphasenabscheidung (PECVD) beeinflusst die Vakuumumgebung die Enthalpie, die Dichte der geladenen und ungeladenen Teilchen und die Energieverteilung im Plasma.
- Diese Kontrolle ist entscheidend für die Optimierung des Abscheidungsprozesses und die Gewährleistung, dass die Schicht die gewünschten mechanischen, elektrischen oder optischen Eigenschaften aufweist.
Anhand dieser Schlüsselpunkte wird deutlich, dass das Vakuum nicht nur eine technische Voraussetzung, sondern ein grundlegender Aspekt der Dünnschichtabscheidung ist, der sich direkt auf die Qualität, Leistung und Zuverlässigkeit des Endprodukts auswirkt.
Zusammenfassende Tabelle:
Hauptnutzen | Erläuterung |
---|---|
Verringerung der Verunreinigung | Minimiert unerwünschte Substanzen wie Sauerstoff und Wasserdampf und gewährleistet so eine hohe Reinheit. |
Erhöhter mittlerer freier Weg | Ermöglicht es den verdampften Atomen, sich ohne Kollisionen weiter zu bewegen, was die Effizienz verbessert. |
Kontrolle über die Gaszusammensetzung | Ermöglicht präzise Gas- und Dampfkontrolle für gewünschte Filmeigenschaften. |
Minimierung von Verunreinigungen | Verringert gasförmige Verunreinigungen und verbessert die Filmhaftung und Reinheit. |
Verbesserte Filmhaftung | Gewährleistet eine starke Haftung und gleichbleibende Filmeigenschaften. |
Verbesserte Prozesskontrolle | Ermöglicht eine präzise Regelung der Abscheidungsparameter für eine gleichmäßige Schichtqualität. |
Beeinflussung des Plasmas | Optimiert die Plasmabedingungen für mechanische, elektrische oder optische Eigenschaften. |
Sind Sie bereit für die Herstellung hochwertiger dünner Schichten? Kontaktieren Sie noch heute unsere Experten für maßgeschneiderte Lösungen!