Obwohl das Hartlöten eine weit verbreitete Verbindungstechnik ist, weist es mehrere Nachteile auf, die sich auf die Qualität, Effizienz und Kosten des Prozesses auswirken können. Diese Nachteile variieren je nach Art der verwendeten Lötmethode, beispielsweise Vakuumlöten oder Handlöten. Zu den Hauptproblemen zählen eine verringerte Materialhärte, hohe technische und verfahrenstechnische Anforderungen, Energieverbrauch, lange Verarbeitungszeiten sowie Herausforderungen im Zusammenhang mit Oxidation und Flussmittelrückständen. Das Verständnis dieser Nachteile ist für jeden, der Löten als Verbindungsmethode in Betracht zieht, von entscheidender Bedeutung, da sie sich auf die Leistung des Endprodukts und den gesamten Produktionsprozess auswirken können.
Wichtige Punkte erklärt:
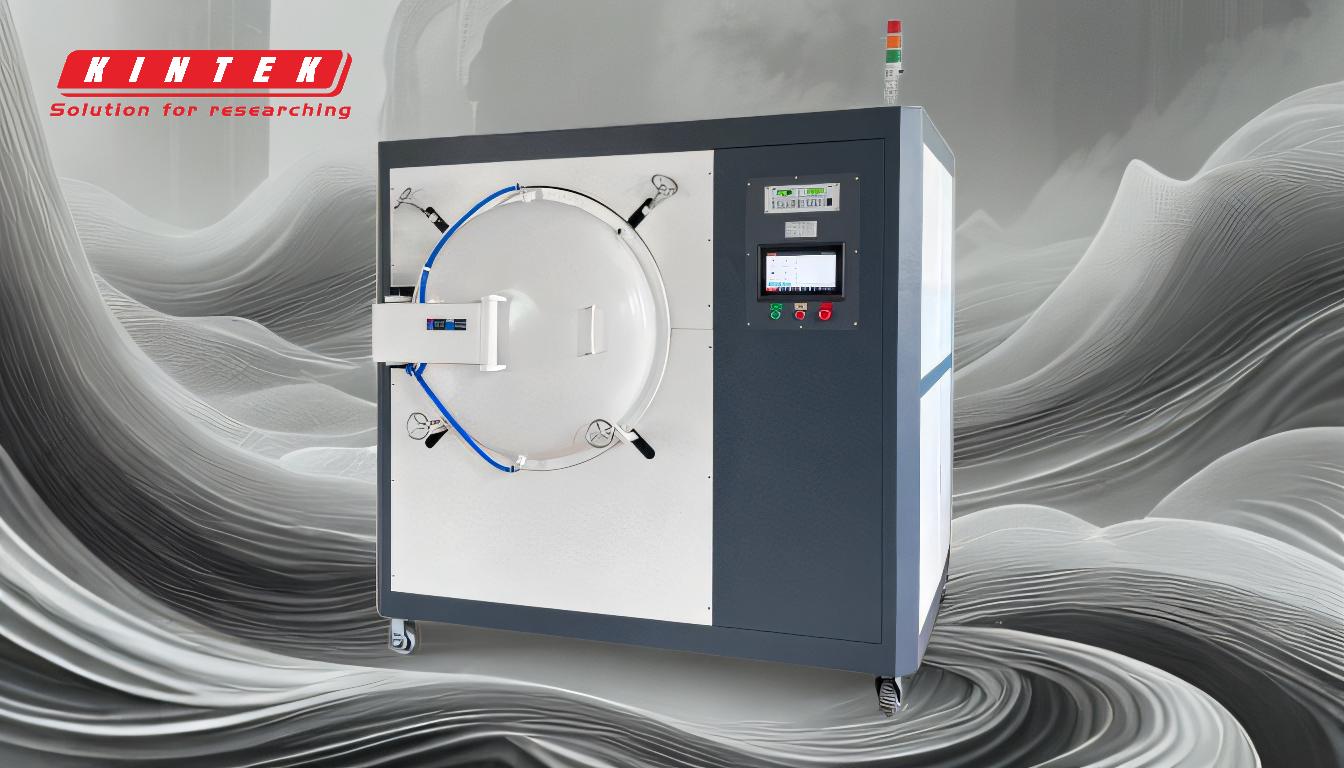
-
Reduzierte Materialhärte nach Hochtemperaturschweißen:
- Beim Vakuumlöten können die hohen Temperaturen, die zum Schmelzen des Zusatzwerkstoffs erforderlich sind, zu einer Verringerung der Härte des Grundmetalls führen. Dies ist besonders problematisch für Materialien, deren Härte für strukturelle Integrität oder Verschleißfestigkeit von entscheidender Bedeutung ist. Die Erweichung des Materials kann die Festigkeit und Haltbarkeit der Verbindung beeinträchtigen und sie für Anwendungen mit hoher Beanspruchung weniger geeignet machen.
-
Hohe Prozessanforderungen und technische Schwierigkeiten:
- Beim Hartlöten, insbesondere beim Vakuumlöten, ist eine präzise Kontrolle der Temperatur, der Atmosphäre und der Platzierung des Füllmaterials erforderlich. Dies erfordert spezielle Ausrüstung und erfahrene Bediener, was die Komplexität und Kosten des Prozesses erhöht. Die Notwendigkeit einer kontrollierten Umgebung, beispielsweise eines Vakuums oder einer Inertgasatmosphäre, erhöht die technischen Herausforderungen und schränkt die Zugänglichkeit des Prozesses für kleinere Betriebe ein.
-
Hoher Energieverbrauch:
- Der Lötprozess, insbesondere das Vakuumlöten, verbraucht aufgrund der Notwendigkeit hoher Temperaturen und kontrollierter Umgebungen eine erhebliche Menge Energie. Dies erhöht nicht nur die Betriebskosten, sondern hat auch Auswirkungen auf die Umwelt und macht es im Vergleich zu anderen Verbindungsmethoden weniger nachhaltig.
-
Lange Bearbeitungszeit:
- Beim Hartlöten sind häufig längere Heiz- und Kühlzyklen erforderlich, um eine ordnungsgemäße Verbindungsbildung sicherzustellen und thermische Spannungen zu vermeiden. Dies kann zu längeren Produktionszeiten führen, was den Durchsatz und die Effizienz verringert. In Branchen, in denen Zeit ein entscheidender Faktor ist, kann dies ein erheblicher Nachteil sein.
-
Hohe Reinigungs- und Umweltschutzkosten:
- Vor dem Löten müssen Materialien häufig gründlich gereinigt werden, um Oxide, Öle und andere Verunreinigungen zu entfernen, die die Verbindungsqualität beeinträchtigen könnten. Darüber hinaus kann die Verwendung von Flussmitteln bei einigen Lötprozessen Rückstände hinterlassen, die nach dem Löten gereinigt werden müssen. Diese Schritte erhöhen die Gesamtkosten und die Komplexität des Prozesses, und die Entsorgung von Reinigungsmitteln und Flussmittelrückständen kann Auswirkungen auf die Umwelt haben.
-
Überhitzung und Schwächung des Grundmetalls beim Handlöten:
- Beim manuellen Löten mit einem Brenner in offener Umgebung besteht die Gefahr einer Überhitzung des Grundmetalls. Dies kann zu einer lokalen Schwächung und Oxidation führen, was zu einer Verbindung führt, die sowohl mechanisch schwächer als auch optisch weniger ansprechend ist. Durch die ungleichmäßige Erwärmung kann es außerdem zu Verformungen oder Verwerfungen der Bauteile kommen.
-
Oxidations- und Flussmittelrückstände:
- Beim Freiluftlöten ist die Oxidation des Grundmetalls ein häufiges Problem, das die Verbindung schwächen und ihre ästhetische Qualität beeinträchtigen kann. Um Oxidation vorzubeugen, werden häufig Flussmittel eingesetzt, diese können jedoch schwer entfernbare Rückstände hinterlassen und zu Hohlräumen in der Fuge führen. Diese Hohlräume können als Spannungskonzentratoren wirken und die Festigkeit der Verbindung weiter verringern.
Zusammenfassend lässt sich sagen, dass das Hartlöten zwar mehrere Vorteile bietet, wie z. B. die Möglichkeit, unterschiedliche Materialien zu verbinden und starke, dichte Verbindungen herzustellen, aber auch erhebliche Nachteile mit sich bringt. Dazu gehören Materialerweichung, hohe technische und energetische Anforderungen, lange Verarbeitungszeiten sowie Probleme im Zusammenhang mit Oxidation und Flussmittelrückständen. Das Verständnis dieser Nachteile ist wichtig, um fundierte Entscheidungen darüber treffen zu können, ob Hartlöten die richtige Verbindungsmethode für eine bestimmte Anwendung ist.
Übersichtstabelle:
Nachteil | Beschreibung |
---|---|
Reduzierte Materialhärte | Hohe Temperaturen beim Vakuumlöten machen das Grundmetall weicher und verringern die Festigkeit. |
Hohe Prozessanforderungen | Erfordert eine präzise Temperaturkontrolle, spezielle Ausrüstung und qualifizierte Arbeitskräfte. |
Hoher Energieverbrauch | Ein erheblicher Energieverbrauch erhöht die Kosten und die Umweltbelastung. |
Lange Bearbeitungszeit | Längere Heiz- und Kühlzyklen verringern die Produktionseffizienz. |
Hohe Reinigungs- und Umweltkosten | Die Reinigung vor und nach dem Löten erhöht die Komplexität und die Kosten. |
Überhitzung beim Handlöten | Beim manuellen Brennerlöten besteht die Gefahr, dass das Grundmetall geschwächt wird und sich verzieht. |
Oxidations- und Flussmittelrückstände | Beim Freilöten kommt es zu Oxidation; Flussmittelrückstände schwächen die Gelenke. |
Benötigen Sie Hilfe bei der Entscheidung, ob Hartlöten für Ihre Anwendung geeignet ist? Kontaktieren Sie noch heute unsere Experten für individuelle Beratung!