Das Spark-Plasma-Sinterverfahren (SPS) ist ein fortschrittliches Sinterverfahren, das die Anwendung von Druck und gepulstem elektrischem Strom kombiniert, um eine schnelle Verdichtung von Materialien zu erreichen.Dieses Verfahren zeichnet sich durch seine Fähigkeit aus, Werkstoffe mit einzigartigen Mikrostrukturen und Eigenschaften bei niedrigeren Temperaturen und kürzeren Verarbeitungszeiten als bei herkömmlichen Sinterverfahren herzustellen.Das SPS-Verfahren arbeitet in einem Vakuum oder kontrollierter Atmosphäre, um Oxidation zu verhindern und die Reinheit des Materials zu gewährleisten.Es umfasst vier Hauptschritte: Entfernen von Gas und Erzeugen eines Vakuums, Anlegen von Druck, Widerstandserhitzen und Abkühlen.Der Schlüsselmechanismus besteht darin, dass durch Funkenentladungen lokal hohe Temperaturen erzeugt werden, die zu Verdampfung und Schmelzen auf der Oberfläche der Pulverteilchen führen, so dass sich um die Kontaktbereiche zwischen den Teilchen Einschnürungen bilden.Dies führt zu einem hohen thermischen Wirkungsgrad und einer schnellen Verdichtung.
Die wichtigsten Punkte werden erklärt:
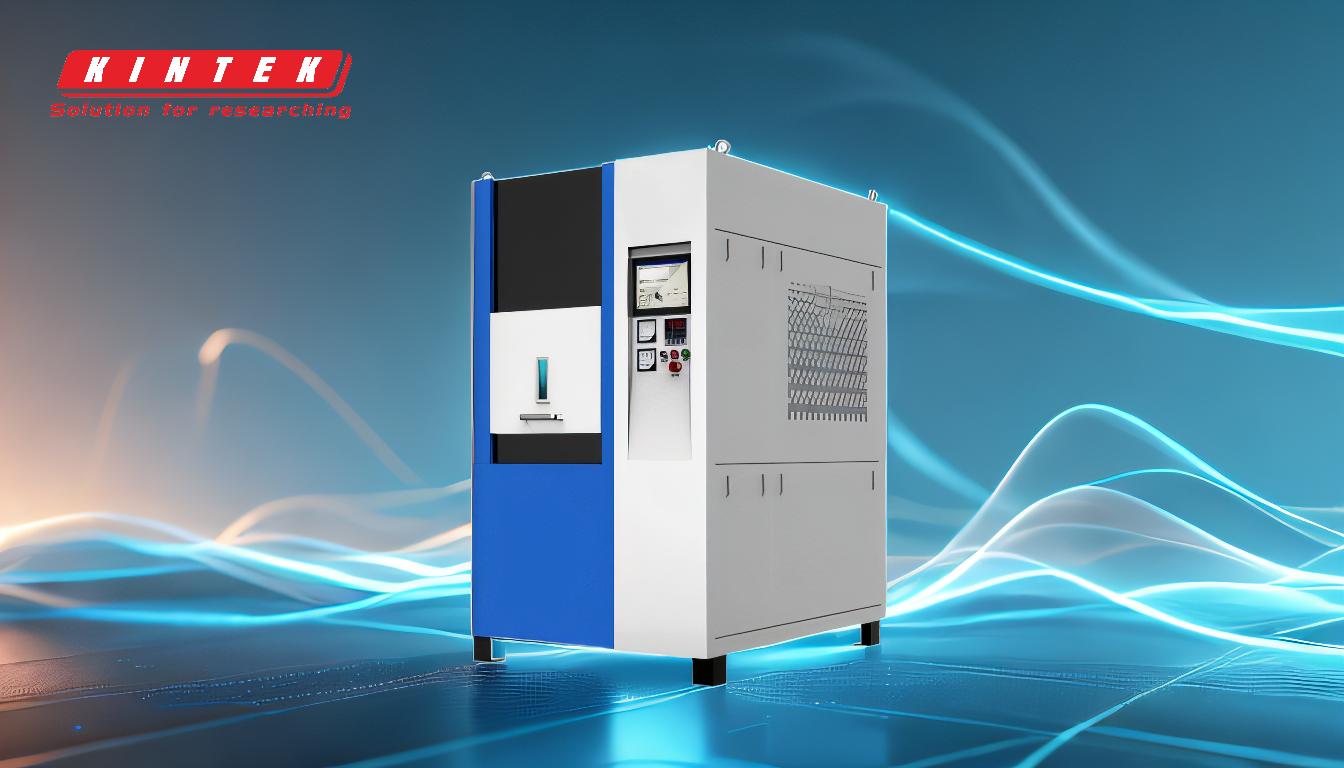
-
Grundlegende Einrichtung und Mechanismus:
- Das SPS-Verfahren basiert auf einem modifizierten Heißpressverfahren, bei dem elektrischer Strom direkt durch das Presswerkzeug (in der Regel Graphit) fließt. Graphit ) und dem Bauteil.
- Dieser Aufbau ermöglicht sehr schnelle Aufheizzeiten und kurze Prozesszyklen durch die Verwendung von gepulsten Strömen und den "Funkenplasmaeffekt".
- Der Funkenplasmaeffekt hemmt das Partikelwachstum und ermöglicht die Herstellung von Materialien mit einzigartigen Zusammensetzungen und Eigenschaften.
-
Etappen des SPS-Prozesses:
- Gas entfernen und ein Vakuum erzeugen:In dieser Phase wird sichergestellt, dass die Umgebung frei von Verunreinigungen und Oxidation ist, was für die Erhaltung der Materialreinheit entscheidend ist.
- Druck ausüben:Auf den Pulverpressling wird Druck ausgeübt, um die Verdichtung zu erleichtern.
- Resistive Erwärmung:Der Pulverpressling wird direkt durch Impulslichtbogenentladungen erhitzt, wodurch ein sehr hoher thermischer Wirkungsgrad und eine schnelle Aufheizung erreicht werden.
- Kühlung:Nach dem Sinterprozess wird das Material abgekühlt, um das Gefüge zu verfestigen.
-
Funkenentladung und örtliche Erwärmung:
- Während des SPS-Prozesses erzeugen Funkenentladungen lokal hohe Temperaturen auf der Oberfläche der Pulverpartikel.
- Diese örtlich begrenzte Erwärmung führt zu Verdampfung und Schmelzen, wobei sich um die Kontaktbereiche zwischen den Partikeln Ränder bilden.
- Die Bildung dieser Ränder ist für den Verdichtungsprozess von entscheidender Bedeutung, da sie die Bindung zwischen den Partikeln verbessert.
-
Vorteile von SPS:
- Hohe Heizraten:Mit dem SPS-Verfahren können sehr hohe Aufheizraten erreicht werden, was die Gesamtverarbeitungszeit erheblich verkürzt.
- Niedrige Sintertemperaturen:Materialien können bei Temperaturen gesintert werden, die 200-500°C niedriger sind als bei herkömmlichen Sinterverfahren.
- Präzise Kontrolle:Das Verfahren erlaubt eine präzise Steuerung von Temperatur, Druck und Heizrate und ermöglicht die Herstellung von Materialien mit einzigartigen Mikrostrukturen und Eigenschaften.
-
Anwendungen und Materialeigenschaften:
- Das SPS-Verfahren wird für die Herstellung einer breiten Palette von Werkstoffen verwendet, darunter Keramik, Metalle und Verbundwerkstoffe.
- Aufgrund der einzigartigen Mikrostrukturen und Eigenschaften, die durch SPS erreicht werden, eignet sich das Verfahren für Anwendungen in der Luft- und Raumfahrt, der Automobilindustrie und der Biomedizin.
- Ein wesentlicher Vorteil des SPS-Verfahrens ist die Möglichkeit, Materialien mit feiner Korngröße und verbesserten mechanischen Eigenschaften herzustellen.
-
Ökologische und betriebliche Erwägungen:
- Das SPS-Verfahren arbeitet im Vakuum oder in einer kontrollierten Atmosphäre, die Oxidation verhindert und die Reinheit des Materials gewährleistet.
- Diese kontrollierte Umgebung ist eine wesentliche Voraussetzung für die Herstellung hochwertiger Materialien mit gleichbleibenden Eigenschaften.
- Das Verfahren zeichnet sich auch durch seinen hohen thermischen Wirkungsgrad aus, der zu seinem schnellen und energieeffizienten Betrieb beiträgt.
Zusammenfassend lässt sich sagen, dass das SPS-Verfahren eine hocheffiziente und vielseitige Sintertechnik ist, die die Kombination von Druck, gepulstem elektrischem Strom und lokaler Erwärmung nutzt, um eine schnelle Verdichtung von Materialien zu erreichen.Seine Fähigkeit, Materialien mit einzigartigen Eigenschaften bei niedrigeren Temperaturen und kürzeren Verarbeitungszeiten herzustellen, macht es zu einem wertvollen Werkzeug für die Herstellung moderner Materialien.
Zusammenfassende Tabelle:
Hauptaspekt | Einzelheiten |
---|---|
Prozess-Übersicht | Kombiniert Druck und gepulsten elektrischen Strom für eine schnelle Materialverdichtung. |
Wichtige Stufen |
1.Gasentfernung und Vakuumerzeugung
2.Druckanwendung 3.Widerstandsheizung 4.Kühlung |
Vorteile |
- Hohe Aufheizraten
- Niedrige Sintertemperaturen - Präzise Steuerung der Parameter |
Anwendungen | Luft- und Raumfahrt, Automobilindustrie, biomedizinische Industrie |
Vorteile für die Umwelt | Arbeitet unter Vakuum/kontrollierter Atmosphäre und gewährleistet Materialreinheit und Effizienz. |
Möchten Sie erfahren, wie Spark Plasma Sintering Ihre Materialherstellung revolutionieren kann? Kontaktieren Sie unsere Experten noch heute!