Der Druck in einem Sputtercoater ist ein kritischer Parameter, der die Qualität und Effizienz des Sputterprozesses direkt beeinflusst. Typischerweise arbeitet ein Sputtercoater in einem Vakuumbereich von 8 x 10^-2 bis 2 x 10^-2 mbar. Diese Niederdruckumgebung ist wichtig für die Schaffung der notwendigen Bedingungen für das Sputtern, bei dem Atome durch den Beschuss mit energiereichen Ionen aus einem festen Targetmaterial herausgeschleudert werden. Das Vakuum gewährleistet eine minimale Beeinträchtigung durch Luftmoleküle und ermöglicht so eine präzise Kontrolle des Abscheidungsprozesses und die Produktion hochwertiger Dünnfilme. Das Verständnis der Druckanforderungen und ihrer Auswirkungen auf den Sputterprozess ist entscheidend für die Optimierung der Leistung eines Sputtercoaters.
Wichtige Punkte erklärt:
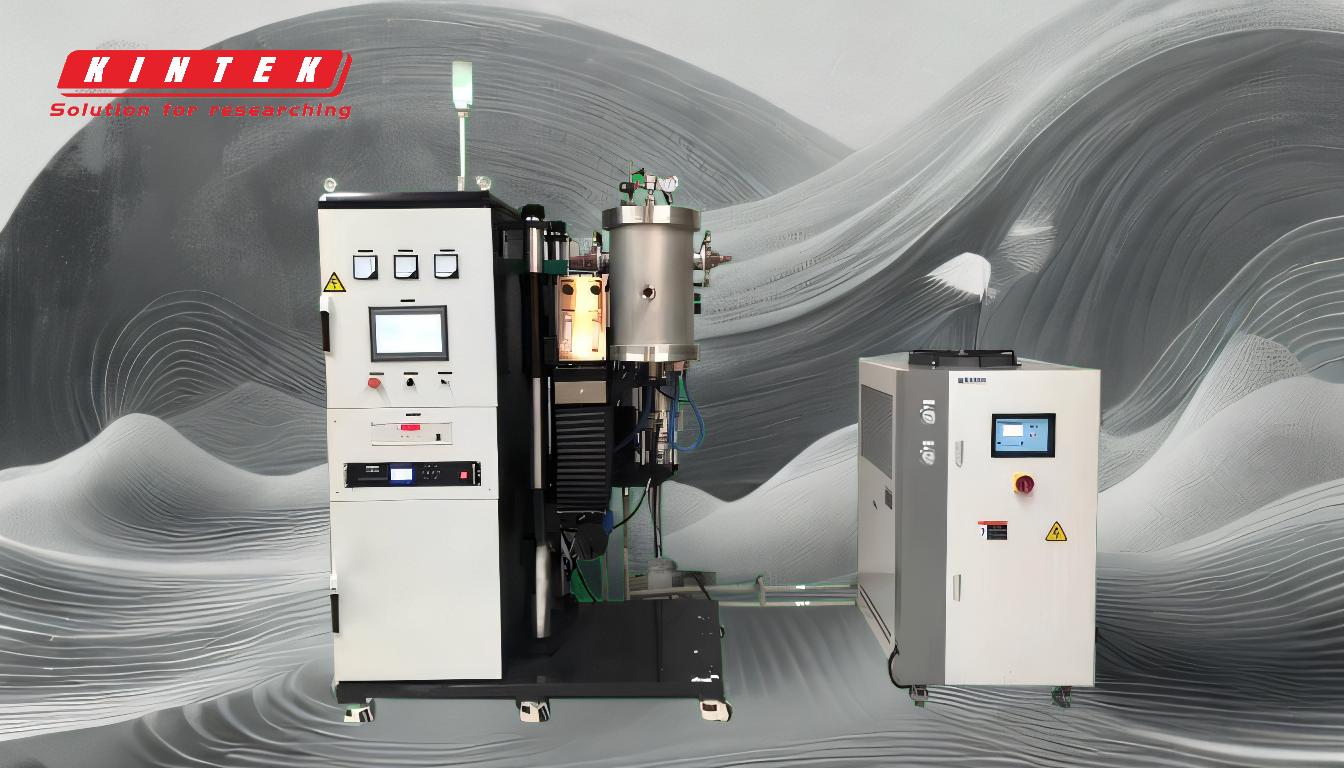
-
Vakuumdruckbereich:
- Der typische Betriebsdruck für einen Sputtercoater liegt zwischen 8 x 10^-2 und 2 x 10^-2 mbar. Diese Niederdruckumgebung ist notwendig, um die Anwesenheit von Luftmolekülen zu reduzieren, die andernfalls den Sputterprozess stören könnten. Das Vakuum stellt sicher, dass die gesputterten Partikel ungehindert vom Target zum Substrat wandern, was zu einem kontrollierteren und effizienteren Abscheidungsprozess führt.
-
Bedeutung des Vakuums beim Sputtern:
- Ein Hochvakuum ist entscheidend für die Aufrechterhaltung der Integrität des Sputterprozesses. Es minimiert Kollisionen zwischen gesputterten Partikeln und Restgasmolekülen, die die Partikel zerstreuen und die Abscheidungsrate verringern können. Darüber hinaus trägt das Vakuum dazu bei, eine Kontamination des dünnen Films zu verhindern und stellt so sicher, dass das abgeschiedene Material rein und von hoher Qualität ist.
-
Auswirkungen auf die Abscheidungsrate und die Filmqualität:
- Der Druck im Sputtercoater hat direkten Einfluss auf die Abscheidungsrate und die Qualität des Dünnfilms. Im optimalen Druckbereich können die gesputterten Partikel direkt zum Substrat wandern, was zu einer höheren Abscheidungsrate und einem gleichmäßigeren Film führt. Abweichungen von diesem Druckbereich können zu langsameren Abscheidungsraten und Filmen mit schlechter Haftung, Dichte oder Kristallinität führen.
-
Kontrolle über Filmdicke und Gleichmäßigkeit:
- Der Betrieb innerhalb des angegebenen Druckbereichs ermöglicht eine präzise Kontrolle der Dicke des abgeschiedenen Films. Durch Anpassen der Sputterzeit und des Zieleingangsstroms ist es möglich, eine hochpräzise Filmdicke zu erreichen. Die Gleichmäßigkeit des Films wird ebenfalls verbessert, da die Niederdruckumgebung dafür sorgt, dass die gesputterten Partikel gleichmäßig über das Substrat verteilt werden.
-
Vorteile der Sputterbeschichtung:
- Die Sputterbeschichtung bietet mehrere Vorteile gegenüber anderen Dünnschichtabscheidungstechniken, wie beispielsweise der Vakuumverdampfung. Dazu gehören eine stärkere Haftung, dichtere Filme und die Möglichkeit, kristalline Filme bei niedrigeren Temperaturen zu erzeugen. Die hohe Keimbildungsdichte bei der Sputterbeschichtung ermöglicht die Herstellung extrem dünner, kontinuierlicher Filme, sogar mit einer Dicke von 10 nm oder weniger. Darüber hinaus tragen die lange Lebensdauer der Targets und die Möglichkeit, sie in verschiedene Formen zu bringen, zur Effizienz und Flexibilität des Sputterprozesses bei.
-
Rolle reaktiver Gase:
- In einigen Fällen können reaktive Gase wie Sauerstoff in den Sputter-Beschichter eingeleitet werden, um Verbund- oder Mischfilme zu erzeugen. Das Vorhandensein dieser Gase kann die Eigenschaften des abgeschiedenen Films verändern, beispielsweise seine elektrische Leitfähigkeit oder seine optischen Eigenschaften. Bei der Verwendung reaktiver Gase muss der Druck in der Kammer sorgfältig kontrolliert werden, um sicherzustellen, dass die gewünschte Filmzusammensetzung erreicht wird.
-
Überlegungen zur Temperatur:
- Auch der Druck im Sputtercoater beeinflusst den Temperaturanstieg während des Sputterprozesses. Die Aufrechterhaltung des Drucks im optimalen Bereich trägt dazu bei, den Temperaturanstieg unter 10 °C zu halten, was wichtig ist, um Schäden an temperaturempfindlichen Substraten zu verhindern. Dieser Niedertemperaturvorgang ist einer der Hauptvorteile der Sputterbeschichtung, da er die Abscheidung dünner Filme auf einer Vielzahl von Materialien ermöglicht, ohne dass es zu einer thermischen Zersetzung kommt.
Zusammenfassend ist der Druck in einem Sputtercoater ein grundlegender Parameter, der die Effizienz, Qualität und Kontrolle des Sputterprozesses beeinflusst. Der Betrieb innerhalb des angegebenen Vakuumbereichs gewährleistet optimale Bedingungen für die Herstellung hochwertiger Dünnfilme mit präziser Dicke und Gleichmäßigkeit. Um die gewünschten Filmeigenschaften zu erreichen und die Leistung des Sputtercoaters zu maximieren, ist es wichtig, den Druck zu verstehen und zu kontrollieren.
Übersichtstabelle:
Aspekt | Einzelheiten |
---|---|
Druckbereich | 8 x 10^-2 bis 2 x 10^-2 mbar |
Bedeutung des Vakuums | Minimiert Störungen durch Luftmoleküle, gewährleistet die Partikelbewegung und verhindert Kontaminationen. |
Auswirkungen auf die Ablagerung | Höhere Abscheidungsraten, gleichmäßige Filme und bessere Haftung bei optimalem Druck. |
Filmdickenkontrolle | Präzise Kontrolle über Dicke und Gleichmäßigkeit durch Druckeinstellungen. |
Vorteile | Starke Haftung, dichte Filme, Betrieb bei niedrigen Temperaturen und lange Lebensdauer des Targets. |
Reaktive Gase | Der kontrollierte Druck gewährleistet die richtige Filmzusammensetzung bei der Verwendung reaktiver Gase. |
Überlegungen zur Temperatur | Die Druckregelung hält den Temperaturanstieg unter 10 °C und schützt so empfindliche Substrate. |
Benötigen Sie Hilfe bei der Optimierung der Leistung Ihres Sputtercoaters? Kontaktieren Sie noch heute unsere Experten für maßgeschneiderte Lösungen!