Die Vakuumbeschichtung ist ein Verfahren zur Abscheidung dünner Materialschichten auf einer Oberfläche in einer kontrollierten Umgebung, in der Regel unter Hochvakuumbedingungen.Das Prinzip beruht auf der Verdampfung oder Sublimation eines Ausgangsmaterials, das dann auf einem Substrat kondensiert und einen dünnen Film bildet.Dieses Verfahren gewährleistet eine minimale Verunreinigung und ermöglicht eine genaue Kontrolle über die Dicke und die Eigenschaften der abgeschiedenen Schicht.Die wichtigsten Schritte sind die Erzeugung eines Vakuums zur Beseitigung von Verunreinigungen, das Erhitzen des Ausgangsmaterials, um die Verdampfung einzuleiten, und die Kondensation des verdampften Materials auf dem Substrat.Üblich sind Verfahren wie die physikalische Gasphasenabscheidung (PVD) und die chemische Gasphasenabscheidung (CVD), die jeweils spezifische Anwendungen und Vorteile haben.
Die wichtigsten Punkte werden erklärt:
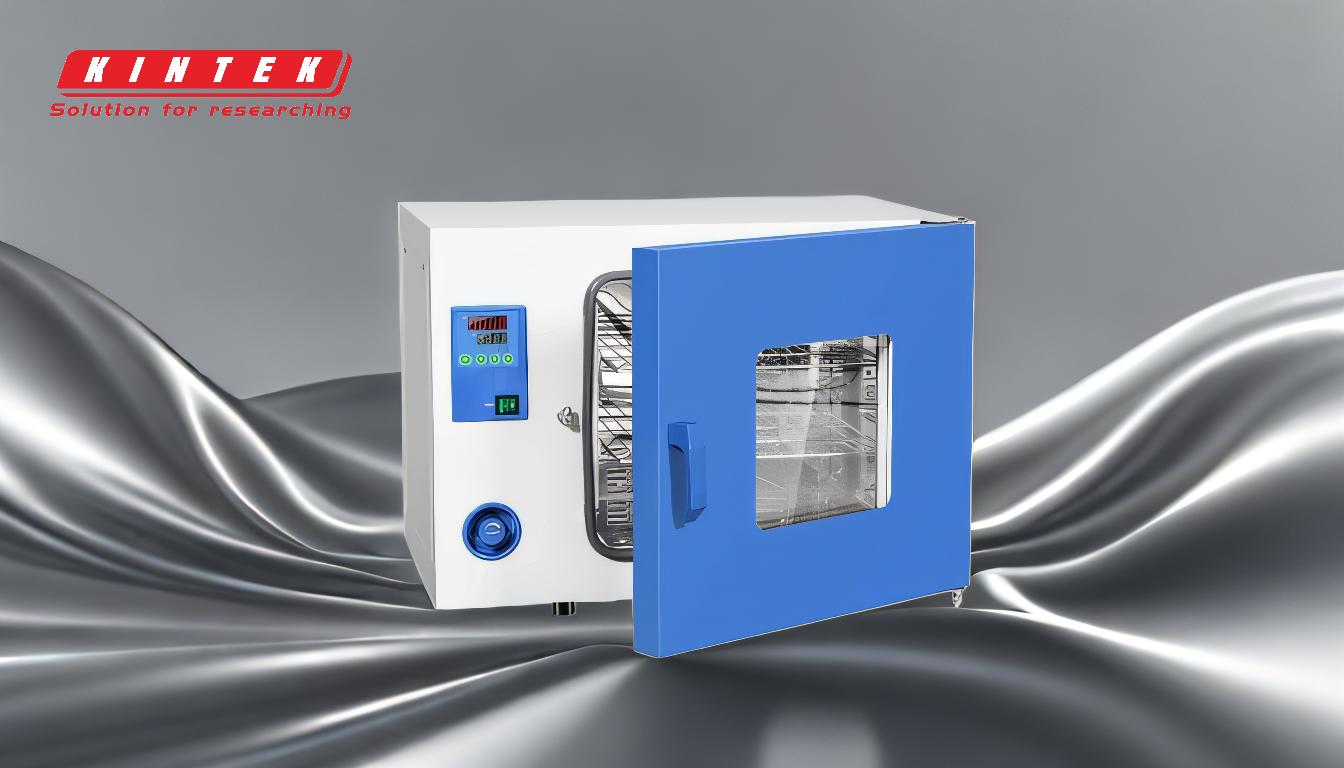
-
Definition und Zweck der Vakuumbeschichtung:
- Die Vakuumbeschichtung ist eine Technik, bei der dünne Materialschichten in einer Vakuumumgebung auf ein Substrat aufgebracht werden.
- Der Hauptzweck ist die Erzeugung von Schutz- oder Funktionsschichten auf Oberflächen, wie z. B. Metallen, um deren Eigenschaften zu verbessern (z. B. Korrosionsbeständigkeit, Leitfähigkeit oder optische Eigenschaften).
-
Die Rolle des Vakuums bei diesem Verfahren:
- Eine Vakuumumgebung ist unerlässlich, um Luft und andere Gase zu eliminieren, die den Beschichtungsprozess verunreinigen könnten.
- Die Abwesenheit von Gasmolekülen gewährleistet, dass das verdampfte Material ungehindert auf das Substrat gelangt, was zu einer gleichmäßigen und qualitativ hochwertigen Schicht führt.
-
Verdampfung und Kondensation:
- Das Ausgangsmaterial wird bis zu einem Punkt erhitzt, an dem es verdampft oder sublimiert und sich in einen Dampf verwandelt.
- Dieser Dampf wandert dann durch das Vakuum und kondensiert auf dem kühleren Substrat und bildet einen dünnen Film.
- Die Dicke des Films kann je nach Anwendung von einer einzelnen Atomschicht bis zu mehreren Mikrometern reichen.
-
Wärmequelle und Verdampfung:
- Eine Wärmequelle, z. B. ein Elektronenstrahl oder eine Widerstandsheizung, wird verwendet, um die für das Verdampfen des Ausgangsmaterials erforderliche Energie bereitzustellen.
- Die Wahl der Wärmequelle hängt von dem aufzubringenden Material und den gewünschten Eigenschaften der Schicht ab.
-
Arten von Vakuumbeschichtungsprozessen:
- Physikalische Gasphasenabscheidung (PVD):Es handelt sich dabei um die physikalische Übertragung von Material von der Quelle auf das Substrat.Zu den gängigen PVD-Verfahren gehören Sputtern und thermisches Verdampfen.
- Chemische Gasphasenabscheidung (CVD):Chemische Reaktionen zur Abscheidung eines dünnen Films.Das Verfahren findet in der Regel bei niedrigem Druck statt und kann reaktive Gase verwenden, um das gewünschte Material auf dem Substrat zu bilden.
- Niederdruck-Plasmaspritzen (LPPS):Eine Variante des Plasmaspritzens unter Vakuumbedingungen, die die Abscheidung hochwertiger Schichten mit minimaler Oxidation ermöglicht.
-
Anwendungen der Vakuumbeschichtung:
- Schutzbeschichtungen:Werden verwendet, um die Haltbarkeit und Beständigkeit von Metallteilen gegen Verschleiß, Korrosion und Oxidation zu verbessern.
- Optische Beschichtungen:Wird bei Linsen und Spiegeln angewendet, um das Reflexionsvermögen oder die Antireflexionseigenschaften zu verbessern.
- Herstellung von Halbleitern:Unverzichtbar für die Abscheidung dünner Schichten bei der Herstellung von integrierten Schaltkreisen und anderen elektronischen Bauteilen.
- Dekorative Beschichtungen:Zum Aufbringen dünner Schichten von Metallen wie Gold oder Chrom zu ästhetischen Zwecken.
-
Vorteile der Vakuumbeschichtung:
- Hohe Reinheit:Die Vakuumumgebung minimiert die Verunreinigung, was zu hochreinen Filmen führt.
- Präzise Kontrolle:Das Verfahren ermöglicht eine präzise Kontrolle der Schichtdicke und der Zusammensetzung.
- Vielseitigkeit:Es kann eine Vielzahl von Materialien abgeschieden werden, darunter Metalle, Keramiken und Polymere.
-
Herausforderungen und Überlegungen:
- Ausrüstung Kosten:Vakuumabscheidungssysteme können teuer sein, da sie Hochvakuumkammern und spezielle Heizquellen benötigen.
- Komplexität:Das Verfahren erfordert eine sorgfältige Kontrolle von Parametern wie Temperatur, Druck und Abscheidungsrate, um die gewünschten Schichteigenschaften zu erreichen.
- Skalierbarkeit:Das Verfahren ist zwar für Anwendungen in kleinem Maßstab geeignet, kann aber für die Produktion in großem Maßstab eine Herausforderung darstellen.
Wenn man diese Schlüsselpunkte versteht, kann man die komplizierte, aber hocheffektive Natur der Vakuumbeschichtung verstehen, die sie zu einer Eckpfeilertechnologie in verschiedenen Industrien macht.
Zusammenfassende Tabelle:
Aspekt | Einzelheiten |
---|---|
Definition | Ein Verfahren zur Abscheidung dünner Materialschichten auf einem Substrat unter Vakuum. |
Zweck | Verbessert die Oberflächeneigenschaften wie Korrosionsbeständigkeit und Leitfähigkeit. |
Schlüsseltechniken | Physikalische Gasphasenabscheidung (PVD), chemische Gasphasenabscheidung (CVD), LPPS. |
Anwendungen | Schutzbeschichtungen, optische Beschichtungen, Halbleiterherstellung, usw. |
Vorteile | Hohe Reinheit, präzise Kontrolle und Vielseitigkeit bei der Materialabscheidung. |
Herausforderungen | Hohe Anlagenkosten, komplexe Prozesse und Probleme mit der Skalierbarkeit. |
Entdecken Sie, wie die Vakuumbeschichtung Ihre Projekte verbessern kann. Kontaktieren Sie unsere Experten noch heute !