Das Induktionsglühen ist ein Wärmebehandlungsverfahren, bei dem Materialien, in der Regel Metalle, durch elektromagnetische Induktion auf eine bestimmte Temperatur erhitzt werden, um ihre physikalischen und mechanischen Eigenschaften zu verändern.Die Temperatur für das Induktionsglühen variiert je nach dem zu behandelnden Material, liegt aber bei den meisten Metallen zwischen 500°C und 900°C.Das Verfahren zielt darauf ab, die Duktilität zu erhöhen und die Härte zu verringern, indem die Versetzungen in der Kristallstruktur des Materials reduziert werden, so dass es besser bearbeitbar und weniger spröde wird.Die genaue Temperatur ist entscheidend und muss sorgfältig kontrolliert werden, um die gewünschten Materialeigenschaften zu erreichen, ohne dass es zu Überhitzung oder anderen Defekten kommt.
Die wichtigsten Punkte werden erklärt:
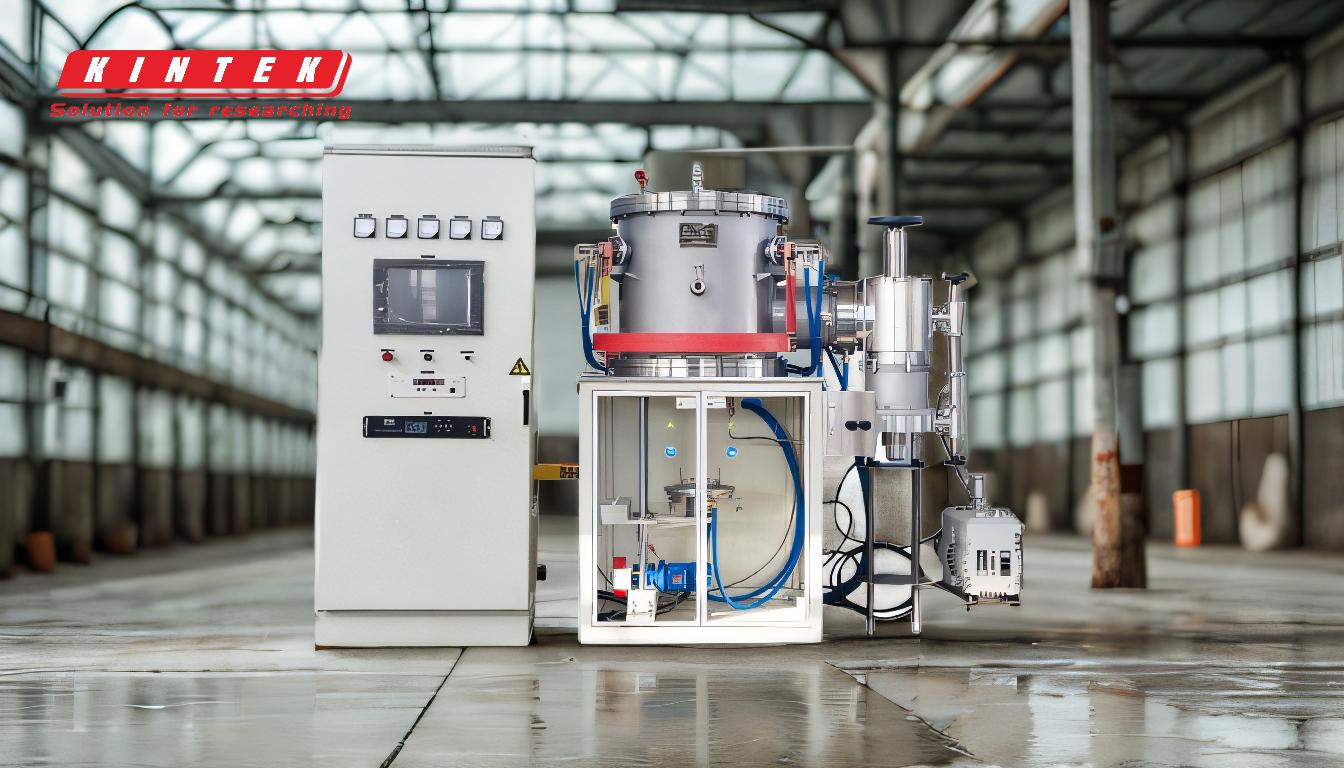
-
Definition des Induktionsglühens:
- Das Induktionsglühen ist ein Wärmebehandlungsverfahren, bei dem Materialien, in der Regel Metalle, durch elektromagnetische Induktion auf eine bestimmte Temperatur erhitzt werden, um ihre physikalischen und mechanischen Eigenschaften zu verändern.
- Das Verfahren wird eingesetzt, um die Duktilität zu erhöhen und die Härte zu verringern, wodurch das Material besser bearbeitbar und weniger spröde wird.
-
Temperaturbereich für das Induktionsglühen:
- Die Temperatur für das Induktionsglühen variiert je nach dem zu behandelnden Material.
- Bei den meisten Metallen liegt der Temperaturbereich in der Regel zwischen 500°C und 900°C.
- Die genaue Temperatur ist von entscheidender Bedeutung und muss sorgfältig kontrolliert werden, um die gewünschten Materialeigenschaften zu erreichen, ohne dass es zu Überhitzung oder anderen Defekten kommt.
-
Die Bedeutung der Temperaturkontrolle:
- Die Temperaturkontrolle ist beim Induktionsglühen von entscheidender Bedeutung, um sicherzustellen, dass das Material die gewünschten Eigenschaften erreicht.
- Eine Überhitzung kann zu unerwünschten Veränderungen im Mikrogefüge des Materials führen, wie z. B. Kornwachstum oder Phasenumwandlungen, die sich negativ auf die Leistung des Materials auswirken können.
- Bei Unterhitzung wird möglicherweise nicht die gewünschte Verringerung der Härte und Erhöhung der Duktilität erreicht.
-
Werkstoffspezifische Überlegungen:
- Verschiedene Materialien haben unterschiedliche Anforderungen an die Glühtemperatur.
- Stahl beispielsweise erfordert in der Regel Glühtemperaturen zwischen 700°C und 900°C, während Aluminiumlegierungen niedrigere Temperaturen von etwa 300°C bis 500°C erfordern.
- Die spezifische Temperatur für ein bestimmtes Material wird durch dessen Zusammensetzung, Mikrostruktur und die gewünschten Endeigenschaften bestimmt.
-
Prozess-Parameter:
- Neben der Temperatur sind beim Induktionsglühen auch andere Prozessparameter wie die Erwärmungsgeschwindigkeit, die Haltezeit und die Abkühlgeschwindigkeit wichtig.
- Die Erwärmungsrate sollte kontrolliert werden, um eine gleichmäßige Erwärmung zu gewährleisten und thermische Spannungen zu vermeiden.
- Die Haltezeit bei der Glühtemperatur ermöglicht die notwendigen mikrostrukturellen Veränderungen.
- Die Abkühlungsgeschwindigkeit kann die endgültigen Materialeigenschaften beeinflussen, wobei langsamere Abkühlungsgeschwindigkeiten im Allgemeinen zu weicheren und duktileren Materialien führen.
-
Vorteile des Induktionsglühens:
- Das Induktionsglühen bietet gegenüber dem herkömmlichen Ofenglühen mehrere Vorteile, wie z. B. schnellere Erwärmungsraten, präzise Temperaturregelung und örtlich begrenzte Erwärmung.
- Das Verfahren kann leicht automatisiert und in Produktionslinien integriert werden, wodurch es sich für die Herstellung großer Mengen eignet.
- Das Induktionsglühen senkt außerdem den Energieverbrauch und minimiert das Risiko von Oxidation und Verunreinigung im Vergleich zum Glühen im Ofen.
-
Anwendungen des Induktionsglühens:
- Das Induktionsglühen ist in verschiedenen Industriezweigen weit verbreitet, unter anderem in der Automobil-, Luft- und Raumfahrt- und Elektronikindustrie.
- Zu den üblichen Anwendungen gehören das Glühen von Drähten, Rohren und Blechen sowie die Wärmebehandlung von Komponenten wie Zahnrädern, Lagern und Befestigungselementen.
- Das Verfahren wird auch bei der Herstellung von Halbleitern und anderen elektronischen Bauteilen eingesetzt, bei denen eine präzise Temperaturregelung unerlässlich ist.
Zusammenfassend lässt sich sagen, dass das Induktionsglühen ein vielseitiges und effizientes Wärmebehandlungsverfahren ist, das eine präzise Temperatursteuerung erfordert, um die gewünschten Materialeigenschaften zu erzielen.Der Temperaturbereich für das Induktionsglühen liegt in der Regel zwischen 500°C und 900°C, je nach dem zu behandelnden Material.Die richtige Steuerung der Prozessparameter, einschließlich der Erwärmungsrate, der Haltezeit und der Abkühlungsrate, ist für den Erfolg des Glühprozesses unerlässlich.Das Induktionsglühen bietet mehrere Vorteile gegenüber herkömmlichen Verfahren, wie z. B. schnellere Erwärmungsraten, präzise Temperaturregelung und geringerer Energieverbrauch, was es zu einer wertvollen Technik für verschiedene industrielle Anwendungen macht.
Zusammenfassende Tabelle:
Aspekt | Einzelheiten |
---|---|
Temperaturbereich | 500°C-900°C (variiert je nach Material) |
Wesentliche Vorteile | Schnellere Erwärmung, präzise Steuerung, geringerer Energieverbrauch, minimale Verunreinigung |
Anwendungen | Automobilindustrie, Luft- und Raumfahrt, Elektronik, Glühen von Drähten und Rohren |
Prozess-Parameter | Aufheizgeschwindigkeit, Haltezeit, Abkühlgeschwindigkeit |
Materialspezifische Anforderungen | Stahl: 700°C-900°C; Aluminium: 300°C-500°C |
Optimieren Sie Ihren Wärmebehandlungsprozess mit Induktionsglühen - Kontaktieren Sie noch heute unsere Experten !