Dünnschichtabscheidungsverfahren wie die physikalische Gasphasenabscheidung (PVD) oder die chemische Gasphasenabscheidung (CVD) erfordern eine Vakuumumgebung, um hochwertige, reine und fehlerfreie Schichten zu gewährleisten.Das Vakuum dient mehreren wichtigen Zwecken, darunter der Verringerung von Verunreinigungen, der Ermöglichung einer kontrollierten Partikelbewegung und der Erleichterung eines präzisen Materialauftrags.Durch die Schaffung einer Niederdruckumgebung minimiert das Vakuum unerwünschte Wechselwirkungen zwischen verdampften Atomen und Restgasen und sorgt dafür, dass die abgeschiedene Schicht gut haftet und ihre gewünschten Eigenschaften beibehält.Dies ist besonders wichtig in Branchen wie der Halbleiterherstellung, wo selbst mikroskopisch kleine Verunreinigungen die Produktleistung beeinträchtigen können.
Die wichtigsten Punkte werden erklärt:
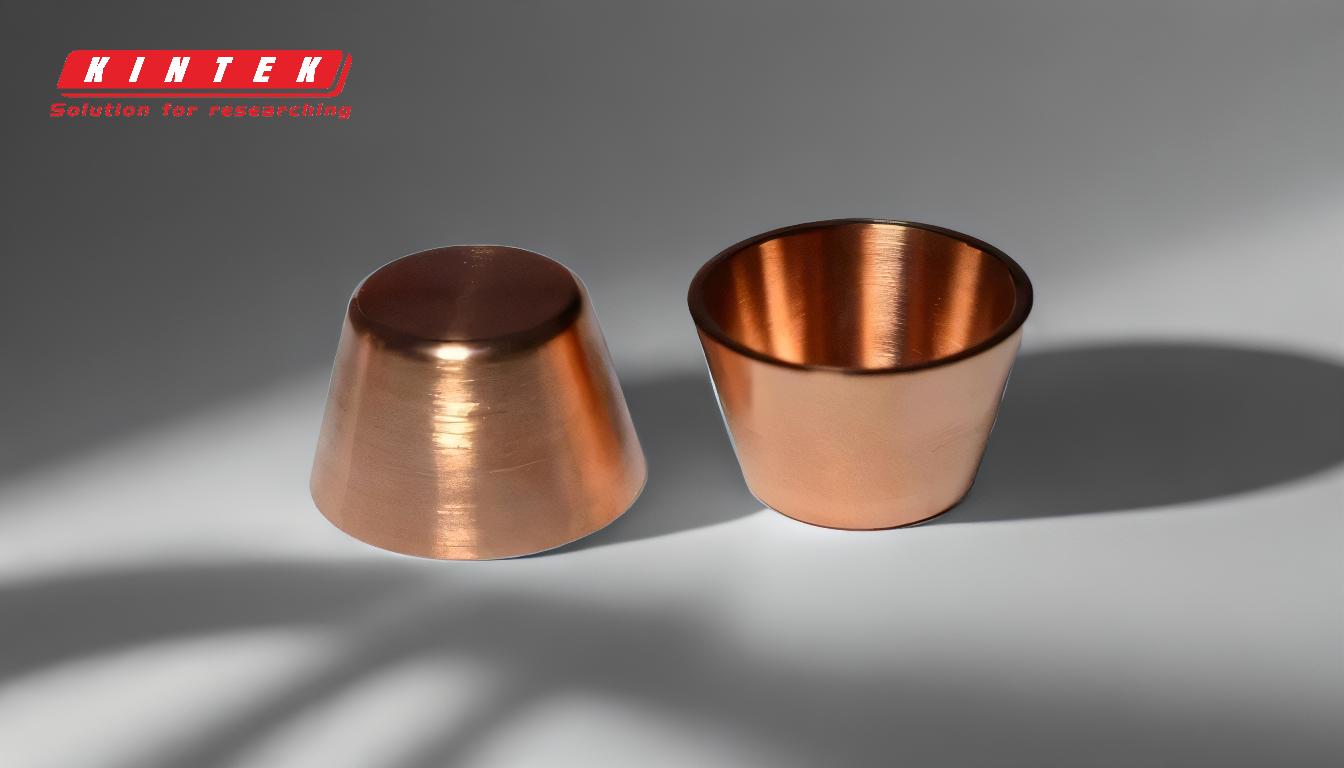
-
Verringerung der Kontamination:
- In einer Vakuumumgebung ist das Vorhandensein von Verunreinigungen wie Sauerstoff, Stickstoff, Kohlendioxid und anderen Gasen, die mit dem Folienmaterial reagieren können, deutlich geringer.
- Diese Verunreinigungen können die Klebefähigkeit der Folie schwächen, ihre chemische Zusammensetzung verändern oder Defekte wie Oxidation oder Nitridbildung verursachen.
- Bei der Herstellung von Mikrochips zum Beispiel können selbst Spuren von Verunreinigungen zu Schaltkreisausfällen führen, weshalb ein Hochvakuum für die Aufrechterhaltung der Reinheit unerlässlich ist.
-
Langer mittelfreier Weg für verdampfte Atome:
- Im Vakuum ist der Gasdruck geringer, so dass die verdampften Atome längere Strecken zurücklegen können, ohne mit anderen Teilchen zusammenzustoßen.
- Dieser lange mittelfreie Weg sorgt dafür, dass die Atome das Substrat gleichmäßig erreichen, und verhindert die Keimbildung in der Dampfphase, die sonst Ruß oder ungleichmäßige Ablagerungen bilden könnte.
- Ein kontrollierter mittelfreier Weg ist entscheidend für eine gleichmäßige Schichtdicke und gleichbleibende Materialeigenschaften.
-
Kontrolle der Gas- und Dampfzusammensetzung:
- Eine Vakuumumgebung ermöglicht eine genaue Kontrolle über die Zusammensetzung der Gase und Dämpfe in der Beschichtungskammer.
- Diese Kontrolle ist für Verfahren wie CVD unerlässlich, bei denen spezifische chemische Reaktionen erforderlich sind, um die gewünschte Schicht zu bilden.
- Durch die Minimierung unerwünschter Gase stellt das Vakuum sicher, dass nur die beabsichtigten Reaktionen stattfinden, was zu qualitativ hochwertigen Schichten führt.
-
Niederdruck-Plasma-Umgebung:
- Viele Verfahren zur Dünnschichtabscheidung, wie z. B. das Sputtern, beruhen auf der Erzeugung eines Plasmas in einer Vakuumkammer.
- Eine Niederdruckumgebung ist notwendig, um das Plasma aufrechtzuerhalten und eine effiziente Ionisierung des Zielmaterials zu gewährleisten.
- Diese Plasmaumgebung erhöht die Energie und die Richtungsabhängigkeit der verdampften Atome und verbessert so die Haftung und Dichte des Films.
-
Effizienz der thermischen Verdampfung:
- Bei thermischen Verdampfungsprozessen verringert ein Vakuum die Dichte der Atome in der Kammer und ermöglicht so höhere Verdampfungsraten.
- Ohne Vakuum würden die vorhandenen Luftmoleküle Energie aus dem verdampfenden Material absorbieren, was die Effizienz verringert und möglicherweise die Eigenschaften des Films verändert.
- Ein Hochvakuum gewährleistet, dass das Material sauber verdampft und sich gleichmäßig auf dem Substrat ablagert.
-
Minimierung der gasförmigen Verunreinigung:
- Eine Vakuumumgebung minimiert die Dichte unerwünschter Atome, z. B. aus Restgasen, die sonst in den Film eindringen könnten.
- Dies ist besonders wichtig für Anwendungen, die hochreine Schichten erfordern, wie z. B. optische Beschichtungen oder Halbleiterschichten.
- Durch die Verringerung der gasförmigen Verunreinigung stellt das Vakuum sicher, dass die optischen, elektrischen oder mechanischen Eigenschaften der Schicht den strengen Anforderungen entsprechen.
-
Kontrolle des Massenflusses:
- Ein Vakuum ermöglicht eine präzise Steuerung des Massenstroms in die Prozesskammer, wodurch sichergestellt wird, dass die richtige Menge an Material abgeschieden wird.
- Diese Kontrolle ist entscheidend für das Erreichen der gewünschten Schichtdicke und Gleichmäßigkeit, insbesondere bei mehrschichtigen Abscheidungsprozessen.
- Ohne Vakuum könnten Schwankungen im Gasdruck zu einer ungleichmäßigen Schichtqualität führen.
-
Anwendungen, die Hochvakuum erfordern:
- Branchen wie die Halbleiterherstellung, die optische Beschichtung und die Datenspeicherung (z. B. CDs und DVDs) sind auf Hochvakuumumgebungen angewiesen, um fehlerfreie Produkte herzustellen.
- Bei diesen Anwendungen können selbst Defekte im Nanometerbereich das Produkt unbrauchbar machen, so dass ein Vakuum für die Aufrechterhaltung von Qualität und Leistung unerlässlich ist.
Zusammenfassend lässt sich sagen, dass ein Vakuum für die Abscheidung von Dünnschichten unerlässlich ist, da es eine kontrollierte, verunreinigungsfreie Umgebung schafft, die eine präzise Materialabscheidung, eine gleichmäßige Schichtbildung und qualitativ hochwertige Ergebnisse ermöglicht.Ob für die Mikroelektronik, die Optik oder die Datenspeicherung, das Vakuum sorgt dafür, dass die abgeschiedenen Schichten den strengen Anforderungen der modernen Technologie entsprechen.
Zusammenfassende Tabelle:
Hauptnutzen | Erläuterung |
---|---|
Reduktion von Verunreinigungen | Minimiert Verunreinigungen wie Sauerstoff und Stickstoff und gewährleistet die Reinheit des Films. |
Langer mittelfreier Pfad | Ermöglicht eine gleichmäßige Bewegung der Atome und verhindert ungleichmäßige Ablagerungen. |
Kontrolle der Gaszusammensetzung | Gewährleistet präzise chemische Reaktionen für hochwertige Filme. |
Niederdruck-Plasma | Verbessert die Plasmaerzeugung für eine bessere Schichthaftung und Dichte. |
Effizienz der thermischen Verdampfung | Erhöht die Verdampfungsraten und gewährleistet eine gleichmäßige Ablagerung. |
Minimierung der gasförmigen Verunreinigung | Reduziert Restgase für hochreine Filme. |
Massenflusskontrolle | Ermöglicht präzisen Materialauftrag für gleichbleibende Schichtdicke. |
Anwendungen | Entscheidend für Halbleiter, optische Beschichtungen und Datenspeicherung. |
Sie benötigen eine Vakuumlösung für die Dünnschichtabscheidung? Kontaktieren Sie noch heute unsere Experten um hochwertige Ergebnisse zu erzielen!