Die physikalische Gasphasenabscheidung (PVD) wird im Hochvakuum durchgeführt, um die Reinheit, Qualität und Präzision der abgeschiedenen dünnen Schichten zu gewährleisten.Die Hochvakuumumgebung eliminiert Restgase und Verunreinigungen, die den Abscheidungsprozess stören könnten, und gewährleistet, dass das Material das Substrat mit minimaler Behinderung erreicht.Diese Umgebung ermöglicht auch eine längere mittlere freie Weglänge der Partikel, wodurch Kollisionen reduziert werden und eine gleichmäßigere und besser haftende Schicht gewährleistet wird.Darüber hinaus minimiert das Vakuum die Verunreinigung, sorgt für einen kontrollierten und wiederholbaren Prozess und ist unerlässlich für Anwendungen, die extrem saubere Umgebungen erfordern, wie z. B. die Mikrochip-Herstellung.
Die wichtigsten Punkte erklärt:
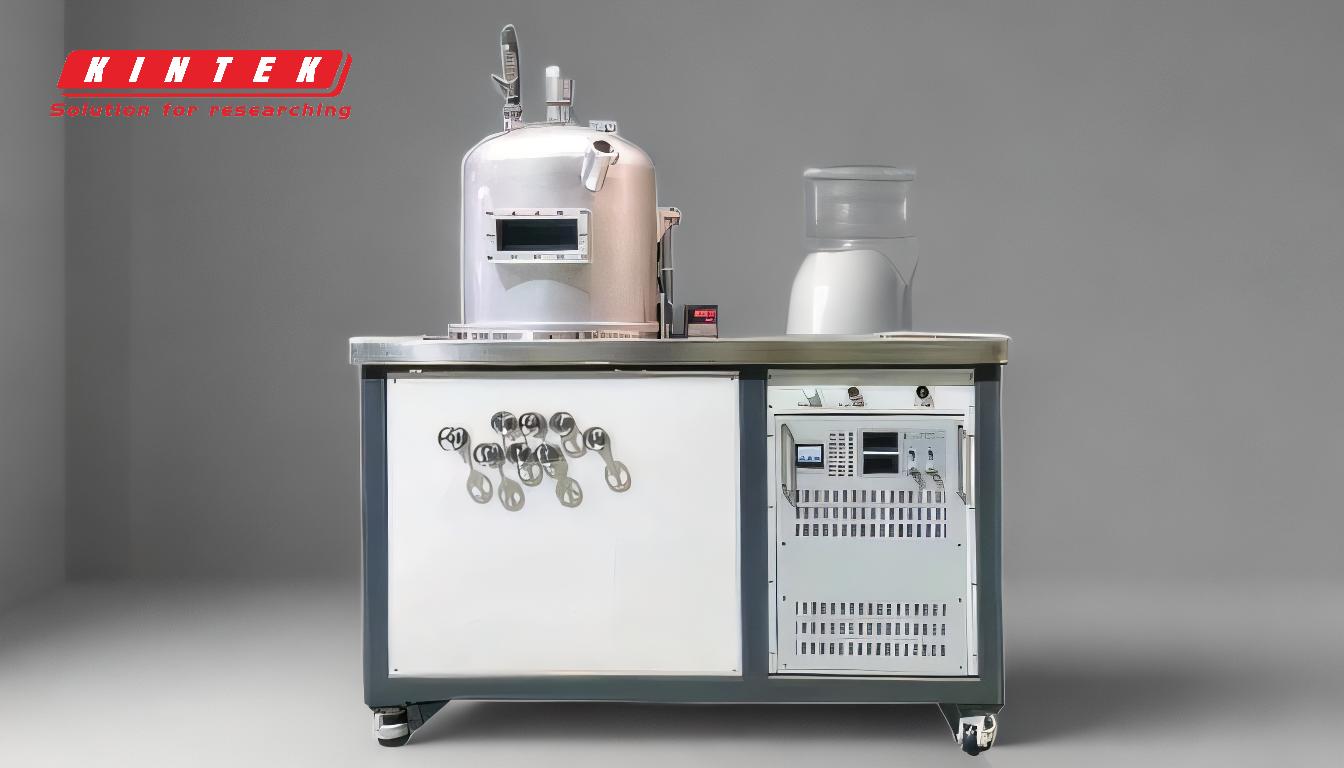
-
Beseitigung von Restgasen und Verunreinigungen:
- In einer Hochvakuumumgebung werden Restgase wie Sauerstoff, Stickstoff und Kohlendioxid entfernt, die den Abscheidungsprozess stören können.
- Diese Gase können die Bewegung der Schichtteilchen behindern, die Haftfähigkeit der Schicht schwächen oder unerwünschte chemische Reaktionen auslösen.
- Ein Hochvakuum reduziert das Vorhandensein von Verunreinigungen und gewährleistet so die Bildung hochreiner dünner Schichten.
-
Längerer mittlerer freier Weg:
- Im Hochvakuum ist die mittlere freie Weglänge der Teilchen (die durchschnittliche Entfernung, die ein Teilchen zurücklegt, bevor es mit einem anderen zusammenstößt) erheblich größer.
- Dadurch verringert sich die Wahrscheinlichkeit von Zusammenstößen zwischen den Partikeln, so dass sie ohne Streuung direkt auf das Substrat gelangen können.
- Eine längere mittlere freie Weglänge ist entscheidend für eine gleichmäßige und hochwertige Schichtabscheidung.
-
Verbesserte Haftung und Filmqualität:
- Die Vakuumumgebung sorgt dafür, dass das Material das Substrat mit mehr Energie erreicht, was zu einer stärkeren Haftung führt.
- Ohne Luft oder andere Flüssigkeiten, die die Partikel verlangsamen, können sie sich fester mit dem Substrat verbinden.
- Das Ergebnis sind dünne Schichten mit besseren mechanischen und chemischen Eigenschaften.
-
Kontrollierter und wiederholbarer Prozess:
- Ein Hochvakuum bietet eine kontrollierte Umgebung, in der Variablen wie Druck und Gaszusammensetzung präzise gesteuert werden können.
- Diese Wiederholbarkeit ist für industrielle Anwendungen, bei denen Konsistenz und Qualität entscheidend sind, unerlässlich.
- Sie ermöglicht auch eine bessere Steuerung des Massenstroms und die Schaffung von Niederdruck-Plasmaumgebungen, die häufig bei PVD-Prozessen verwendet werden.
-
Verringerung der gasförmigen Verunreinigung:
- Durch das Vakuum wird die Dichte unerwünschter Atome und Moleküle minimiert, was das Risiko einer Verunreinigung verringert.
- Dies ist besonders wichtig für Anwendungen wie die Mikrochip-Herstellung, bei der schon Spuren von Verunreinigungen zu Defekten führen können.
- Eine saubere Umgebung gewährleistet die Produktion von elektronischen Hochleistungsbauteilen.
-
Effizienz der thermischen Verdampfung:
- Beim PVD-Verfahren durch thermische Verdampfung sorgt ein Hochvakuum dafür, dass die mittlere freie Weglänge der verdampften Atome viel länger ist als der Abstand von der Quelle zum Target.
- Dies verhindert die Streuung durch Restgasmoleküle und sorgt dafür, dass die Atome ohne Energieverlust auf dem Substrat ankommen.
- Es trägt auch zur Erhaltung sauberer Oberflächen bei, da verdampfte Atome besser am Substrat haften können.
-
Anwendungen, die ultra-saubere Umgebungen erfordern:
- Branchen wie die Halbleiterherstellung, optische Beschichtungen und die Datenspeicherung (z. B. CDs und DVDs) erfordern extrem saubere Umgebungen.
- Ein Hochvakuum stellt sicher, dass auch die kleinsten Partikel entfernt werden, wodurch Defekte vermieden und die Zuverlässigkeit des Endprodukts gewährleistet wird.
Durch die Durchführung von PVD im Hochvakuum können Hersteller dünne Schichten mit hervorragender Reinheit, Haftung und Konsistenz erzielen, was dieses Verfahren zu einem wesentlichen Bestandteil fortschrittlicher technologischer Anwendungen macht.
Zusammenfassende Tabelle:
Hauptnutzen | Beschreibung |
---|---|
Beseitigung von Restgasen | Entfernt Gase wie Sauerstoff und Stickstoff und sorgt so für hochreine dünne Schichten. |
Längerer mittlerer freier Weg | Reduziert Partikelkollisionen und gewährleistet eine gleichmäßige und hochwertige Abscheidung. |
Verbesserte Adhäsion und Filmqualität | Die Partikel verbinden sich fest mit dem Substrat und verbessern die mechanischen und chemischen Eigenschaften. |
Kontrollierter und wiederholbarer Prozess | Sorgt für Konsistenz und Präzision bei industriellen Anwendungen. |
Verringerung der gasförmigen Verunreinigung | Minimiert die Verunreinigung, was für die Mikrochip-Herstellung von entscheidender Bedeutung ist. |
Effizienz der thermischen Verdampfung | Verhindert Streuung, so dass die Atome das Substrat ohne Energieverlust erreichen. |
Ultrareine Umgebungen | Unverzichtbar für die Halbleiterfertigung, optische Beschichtungen und Datenspeicherung. |
Erfahren Sie, wie Hochvakuum-PVD Ihren Fertigungsprozess verbessern kann. Kontaktieren Sie unsere Experten noch heute !