Die physikalische Gasphasenabscheidung (PVD) wird bei niedrigem Druck durchgeführt, um eine kontrollierte und saubere Umgebung zu schaffen, die einen effizienten Materialtransfer von der Quelle zum Substrat gewährleistet.Durch den niedrigen Druck werden unerwünschte Gasphasenreaktionen minimiert, die Verunreinigung verringert und die Gleichmäßigkeit des abgeschiedenen Materials erhöht.Außerdem wird die mittlere freie Weglänge der Atome verlängert, was eine höhere Energieübertragung und eine bessere Haftung des Materials auf dem Substrat ermöglicht.Darüber hinaus ist eine Vakuumumgebung von entscheidender Bedeutung für Anwendungen, die eine hohe Präzision erfordern, wie z. B. bei der Herstellung von Mikrochips, bei denen selbst geringe Verunreinigungen erhebliche Fehler verursachen können.
Die wichtigsten Punkte erklärt:
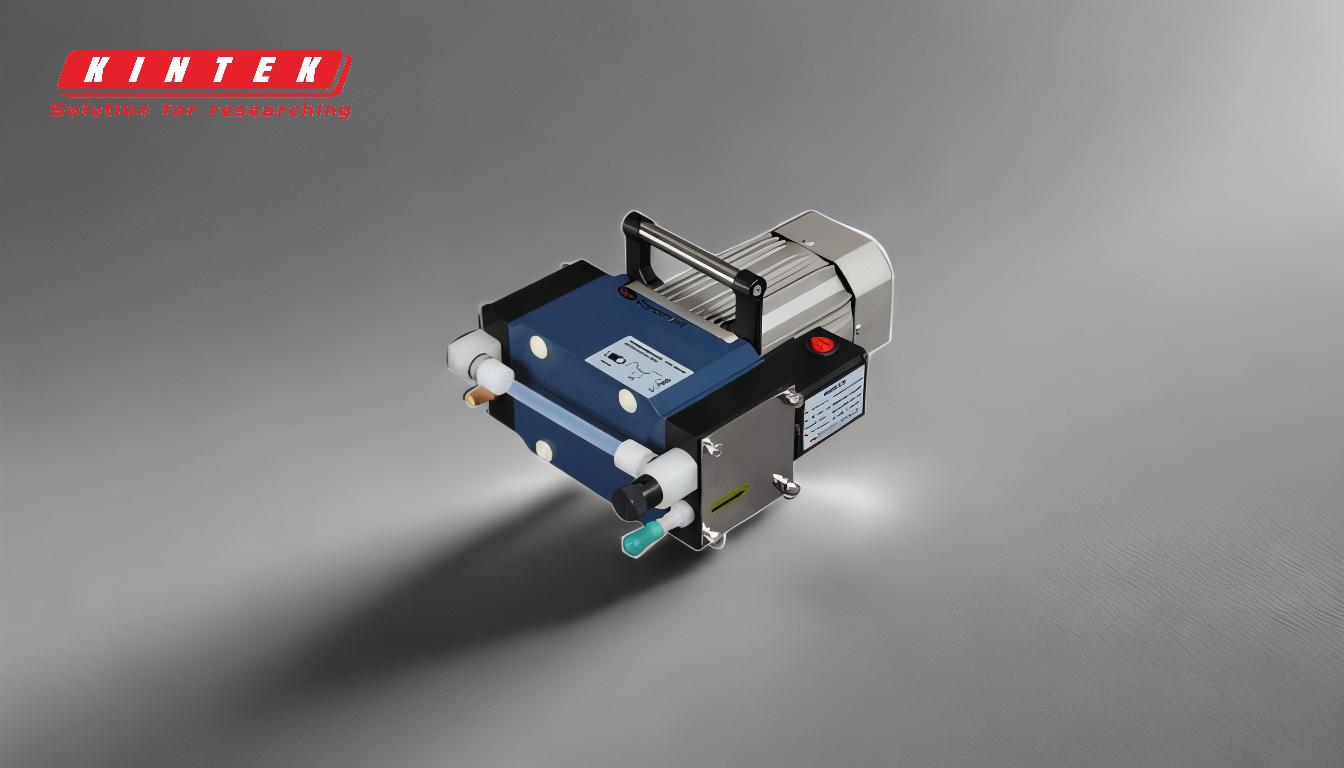
-
Minimierung von unerwünschten Gasphasenreaktionen:
- Der niedrige Druck verringert die Wahrscheinlichkeit unerwünschter chemischer Reaktionen zwischen dem verdampften Material und den Restgasen in der Kammer.
- Dadurch wird sichergestellt, dass das abgeschiedene Material rein bleibt und auf dem Substrat anhaftet, ohne dass sich unerwünschte Verbindungen bilden.
-
Erhöhte Gleichmäßigkeit über das gesamte Substrat:
- Eine Umgebung mit niedrigem Druck ermöglicht eine gleichmäßigere Verteilung des verdampften Materials über das Substrat.
- Diese Gleichmäßigkeit ist entscheidend für Anwendungen, die eine gleichbleibende Dicke und gleichbleibende Eigenschaften erfordern, wie z. B. bei der Halbleiterherstellung.
-
Verbesserte Materialübertragung und Haftung:
- Im Vakuum stößt das verdampfte Material auf weniger Widerstand durch Luft oder andere Gase, so dass es sich effizienter zum Substrat bewegen kann.
- Die erhöhte Energie der Partikel führt zu einer stärkeren Haftung auf dem Substrat und verbessert die Haltbarkeit und Qualität der Beschichtung.
-
Verringerung der Verschmutzung:
- Eine Hochvakuumumgebung minimiert das Vorhandensein von Verunreinigungen wie Staub oder Feuchtigkeit, die sich negativ auf die Qualität der Abscheidung auswirken können.
- Dies ist besonders wichtig in Branchen wie der Mikroelektronik, wo selbst winzige Partikel zu erheblichen Mängeln führen können.
-
Kontrollierter und wiederholbarer Abscheidungsprozess:
- Der niedrige Druck sorgt für eine stabile und vorhersehbare Umgebung, die eine präzise Kontrolle des Abscheidungsprozesses ermöglicht.
- Diese Wiederholbarkeit ist für die Erzielung konsistenter Ergebnisse bei Hochpräzisionsanwendungen unerlässlich.
-
Längerer mittlerer freier Weg der Atome:
- Im Vakuum ist die mittlere freie Weglänge der Atome (die durchschnittliche Entfernung, die ein Atom zurücklegt, bevor es mit einem anderen Atom zusammenstößt) erheblich größer.
- Dadurch können die Atome direkt zum Substrat gelangen, ohne gestreut zu werden, was einen effizienteren und gezielteren Abscheidungsprozess ermöglicht.
-
Hohe thermische Verdampfungsrate:
- Der niedrige Druck ermöglicht eine höhere thermische Verdampfungsrate, die für die Verdampfung des Ausgangsmaterials erforderlich ist.
- Dadurch wird sichergestellt, dass das Material effizient und rechtzeitig auf das Substrat übertragen wird.
-
Verhinderung von gasförmiger Kontamination:
- Durch die Aufrechterhaltung einer Niederdruckumgebung wird die Dichte unerwünschter Atome oder Moleküle auf ein Minimum reduziert.
- Dadurch verringert sich das Risiko, dass Verunreinigungen in das abgeschiedene Material eindringen, was eine sauberere und hochwertigere Beschichtung gewährleistet.
-
Flexibilität bei der Initiierung chemischer Reaktionen:
- Während PVD in der Regel chemische Reaktionen vermeidet, können durch die kontrollierte Zufuhr reaktiver Gase (wie Sauerstoff) spezielle Beschichtungen, wie z. B. Oxide, erzeugt werden.
- Diese Flexibilität ermöglicht die Anpassung der Materialeigenschaften an die jeweiligen Anwendungsanforderungen.
-
Entscheidend für Hochpräzisionsanwendungen:
- Branchen wie die Mikroelektronik, die Optik und die Datenspeicherung (z. B. CDs, DVDs) erfordern extrem saubere und kontrollierte Umgebungen, um fehlerfreie Produkte herzustellen.
- Die Niederdruckbedingungen bei der PVD sind für die Einhaltung der strengen Qualitätsstandards dieser Branchen unerlässlich.
Wenn man diese Schlüsselpunkte versteht, wird klar, warum Niederdruck eine grundlegende Voraussetzung für erfolgreiche PVD-Verfahren ist.Er gewährleistet hochwertige, gleichmäßige und kontaminationsfreie Beschichtungen, die für eine Vielzahl industrieller Anwendungen unerlässlich sind.
Zusammenfassende Tabelle:
Hauptnutzen | Erläuterung |
---|---|
Minimierte Gasphasenreaktionen | Reduziert unerwünschte chemische Reaktionen und gewährleistet eine reine Materialabscheidung. |
Gleichmäßige Verteilung der Beschichtung | Sorgt für gleichmäßige Dicke und Eigenschaften auf dem gesamten Substrat. |
Verbesserte Materialhaftung | Erhöht die Partikelenergie für stärkere, haltbarere Beschichtungen. |
Reduzierte Verunreinigung | Minimiert Staub, Feuchtigkeit und Verunreinigungen für sauberere Beschichtungen. |
Kontrollierter Abscheidungsprozess | Bietet eine stabile Umgebung für wiederholbare, hochpräzise Ergebnisse. |
Längerer mittlerer freier Weg der Atome | Ermöglicht eine effiziente, direkte Materialübertragung auf das Substrat. |
Hohe thermische Verdampfungsrate | Ermöglicht eine schnellere Verdampfung und einen schnelleren Materialtransfer. |
Verhinderung von gasförmiger Verunreinigung | Reduziert Verunreinigungen und sorgt für hochwertige Beschichtungen. |
Flexibilität bei chemischen Reaktionen | Ermöglicht die individuelle Gestaltung von Beschichtungen mit reaktiven Gasen. |
Entscheidend für Hochpräzisionsanwendungen | Unverzichtbar für Branchen wie Mikroelektronik und Optik, die fehlerfreie Produkte benötigen. |
Benötigen Sie eine auf Ihre Bedürfnisse zugeschnittene PVD-Lösung? Kontaktieren Sie noch heute unsere Experten um mehr zu erfahren!