Die Kosten des Aufkohlens hängen von mehreren Faktoren ab, darunter der Materialart, der gewünschten Härtetiefe, der Aufkohlungsmethode (Atmosphäre oder Vakuum) und dem Produktionsumfang. Während in den Referenzen keine genauen Kosten genannt werden, wird der Prozess durch Zeit, Temperatur und die spezifischen Anforderungen der Anwendung beeinflusst. Atmosphären- und Vakuumaufkohlung haben jeweils einzigartige Vorteile, und die Wahl zwischen ihnen hängt von den Leistungsanforderungen des Produkts und den Herstellungsbeschränkungen ab. Im Folgenden untersuchen wir die Schlüsselfaktoren, die die Aufkohlungskosten beeinflussen, und wie sie die Gesamtpreisgestaltung beeinflussen.
Wichtige Punkte erklärt:
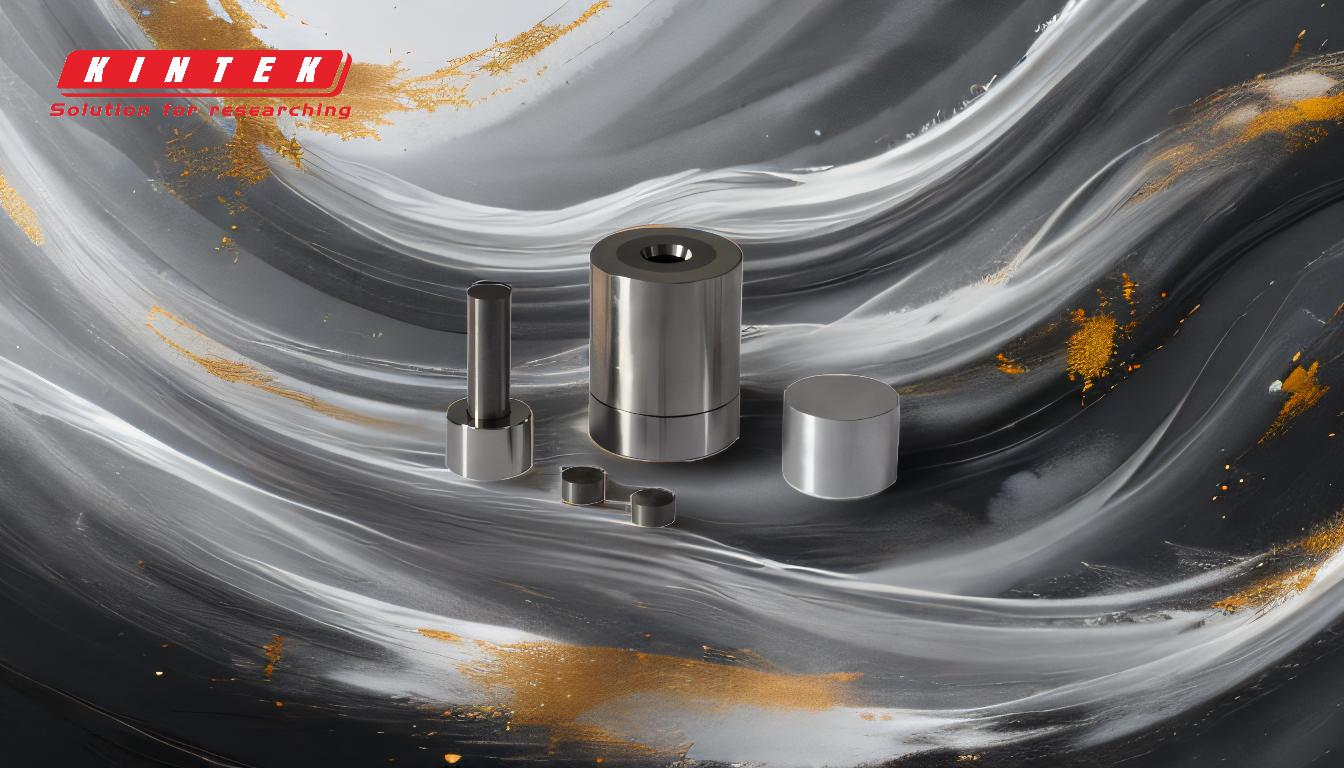
-
Faktoren, die die Aufkohlungskosten beeinflussen
- Materialtyp: Die Kosten variieren je nach Art des aufzukohlenden Materials. Unterschiedliche Legierungen und Metalle erfordern spezifische Bedingungen, die sich auf die Gesamtkosten auswirken können.
- Anforderungen an die Gehäusetiefe: Größere Härtetiefen erfordern längere Belichtungszeiten und höhere Temperaturen, was den Energieverbrauch und die Prozesszeit erhöht.
- Aufkohlungsmethode: Atmosphärenaufkohlung ist im Allgemeinen kostengünstiger als Vakuumaufkohlung, letztere bietet jedoch Vorteile wie geringere Verformungen und eine bessere Kontrolle über den Prozess, was bei bestimmten Anwendungen die höheren Kosten rechtfertigen kann.
-
Zeit und Temperatur
- Der Aufkohlungsprozess ist stark zeit- und temperaturabhängig. Höhere Temperaturen und längere Zeiten führen zu einer größeren Gehäusedicke, erhöhen aber auch die Energiekosten und den Geräteverschleiß.
- Beispielsweise könnte das Erreichen einer Härtetiefe von 0,5 mm bei 925 °C 4 Stunden dauern, während eine tiefere Härtetiefe von 1,5 mm 12 Stunden oder mehr erfordern könnte. Dies wirkt sich direkt auf die Arbeits- und Betriebskosten aus.
-
Aufkohlungsmethoden
- Atmosphärenaufkohlung: Bei dieser Methode wird Kohlenstoff in einer kohlenstoffreichen Atmosphäre in die Metalloberfläche diffundiert. Dies ist für die Produktion in großem Maßstab kostengünstig, erfordert jedoch möglicherweise eine zusätzliche Nachbearbeitung zur Reinigung der Teile.
- Vakuumaufkohlung: Bei dieser Methode wird Kohlenstoff in eine Vakuumumgebung eingebracht, was eine bessere Kontrolle ermöglicht und die Oxidation reduziert. Es ist zwar teurer, eignet sich aber ideal für hochpräzise Komponenten und kann die Nachbearbeitungskosten senken.
-
Produktionsmaßstab
- Größere Produktionsläufe profitieren von Skaleneffekten, da die Stückkosten für die Aufkohlung sinken.
- Bei Kleinserien oder Sonderanfertigungen können aufgrund von Rüstzeiten und einer weniger effizienten Ressourcennutzung höhere Kosten entstehen.
-
Zusätzliche Kosten
- Energieverbrauch: Höhere Temperaturen und längere Verarbeitungszeiten erhöhen den Energieverbrauch, was einen erheblichen Kostenfaktor darstellt.
- Gerätewartung: Häufiger Einsatz bei hohen Temperaturen kann zu Verschleiß führen und erfordert eine regelmäßige Wartung und den Austausch von Teilen.
- Nachbearbeitung: Je nach Anwendung können zusätzliche Schritte wie Abschrecken, Anlassen oder Reinigen erforderlich sein, was die Gesamtkosten erhöht.
-
Kosten schätzen
- Während in den Referenzen keine genauen Preise angegeben sind, kann eine grobe Schätzung für die Atmosphärenaufkohlung je nach den oben genannten Faktoren zwischen 1 und 5 US-Dollar pro Pfund Material liegen.
- Das Vakuumaufkohlen könnte aufgrund der erforderlichen Spezialausrüstung und Prozesskontrolle 20–50 % mehr kosten.
-
Die richtige Methode wählen
- Die Wahl zwischen Atmosphären- und Vakuumaufkohlung sollte auf den spezifischen Anforderungen des Produkts basieren. Vakuumaufkohlen eignet sich beispielsweise ideal für Hochleistungskomponenten, bei denen Präzision und geringer Verzug entscheidend sind, auch wenn dies mit höheren Kosten verbunden ist.
Durch das Verständnis dieser Schlüsselpunkte können Käufer fundierte Entscheidungen über Aufkohlungsprozesse treffen und Kosten mit Leistungsanforderungen in Einklang bringen, um den besten Wert für ihre spezifische Anwendung zu erzielen.
Übersichtstabelle:
Faktor | Auswirkungen auf die Kosten |
---|---|
Materialtyp | Unterschiedliche Legierungen und Metalle erfordern spezifische Bedingungen, die sich auf die Gesamtkosten auswirken. |
Gehäusetiefe | Größere Einarbeitungstiefen erhöhen den Energieverbrauch und die Bearbeitungszeit. |
Aufkohlungsmethode | Vakuumaufkohlen ist teurer, bietet jedoch Präzision und geringere Verzerrungen. |
Produktionsmaßstab | Größere Auflagen reduzieren die Stückkosten; Bei kleinen Chargen können höhere Kosten anfallen. |
Zeit und Temperatur | Höhere Temperaturen und längere Zeiten erhöhen die Energie- und Arbeitskosten. |
Zusätzliche Kosten | Beinhaltet Energieverbrauch, Gerätewartung und Nachbearbeitung. |
Benötigen Sie Hilfe bei der Auswahl der richtigen Aufkohlungsmethode für Ihr Projekt? Kontaktieren Sie noch heute unsere Experten für individuelle Beratung!