Die Herstellung von Dünnschichten durch thermische Verdampfung umfasst eine Reihe kontrollierter Schritte in einer Vakuumumgebung, um eine qualitativ hochwertige Schichtabscheidung zu gewährleisten.Dieser Prozess beginnt mit der Auswahl einer reinen Materialquelle, die dann in einer Vakuumkammer verdampft wird.Das verdampfte Material wandert durch das Vakuum und lagert sich auf einem Substrat ab, wobei ein dünner Film entsteht.Faktoren wie der Vakuumdruck, die Materialeigenschaften und die Substratbedingungen beeinflussen die Qualität und Gleichmäßigkeit der Schicht erheblich.Nach dem Aufdampfen können Verfahren wie das Glühen angewendet werden, um die Schichteigenschaften zu verbessern.Der gesamte Prozess wird sorgfältig kontrolliert, um die gewünschten Schichteigenschaften zu erreichen, was die thermische Verdampfung zu einer präzisen und effektiven Methode für die Herstellung dünner Schichten macht.
Die wichtigsten Punkte werden erklärt:
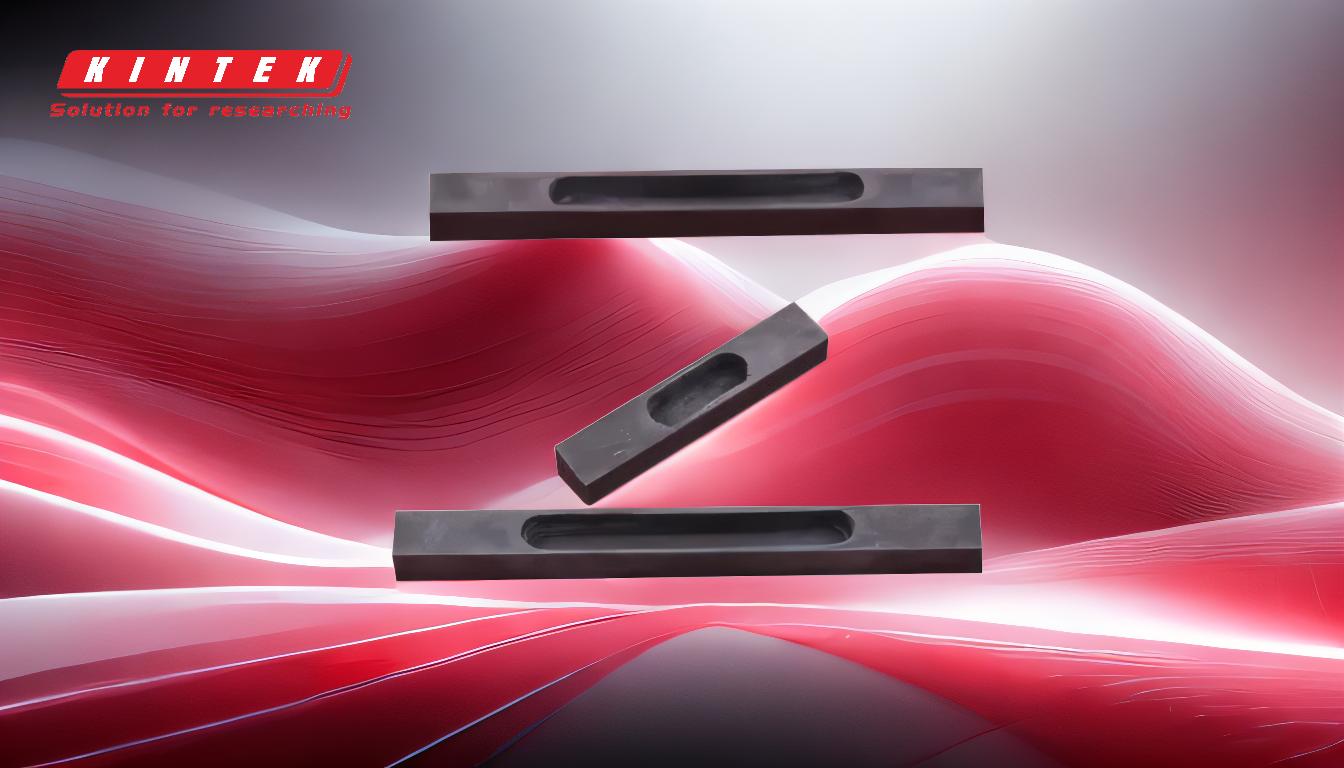
-
Auswahl der Materialquelle:
- Der Prozess beginnt mit der Auswahl einer reinen Materialquelle, die oft als Target bezeichnet wird.Das Material muss mit der thermischen Verdampfung kompatibel sein, d. h. es sollte geeignete Verdampfungseigenschaften und Reinheit aufweisen, um die Qualität der abgeschiedenen Schicht zu gewährleisten.
- Die Wahl des Materials ist entscheidend und hängt von der jeweiligen Anwendung und den gewünschten Filmeigenschaften ab.So können beispielsweise Materialien mit hohem Schmelzpunkt oder spezifischer Reaktivität besondere Überlegungen erfordern.
-
Aufbau der Vakuumkammer:
- Der thermische Verdampfungsprozess findet in einer Vakuumkammer statt, um das Vorhandensein von Verunreinigungen zu minimieren und dem verdampften Material zu ermöglichen, sich frei auf dem Substrat zu bewegen.
- Ein hohes Vakuum ist unerlässlich, da es die mittlere freie Weglänge der verdampften Moleküle vergrößert, die Kollisionen mit Restgasmolekülen verringert und so die Reinheit und Gleichmäßigkeit des Films verbessert.
-
Verdampfung des Materials:
- Die Materialquelle wird mit einem Widerstandsheizelement oder einem Elektronenstrahl bis zum Verdampfungspunkt erhitzt.Die Hitze bewirkt, dass das Material von der festen in die Dampfphase übergeht.
- Die Verdampfungsrate muss sorgfältig kontrolliert werden, um eine gleichmäßige Abscheidungsrate zu gewährleisten, die für das Erreichen einer gleichmäßigen Schichtdicke entscheidend ist.
-
Abscheidung auf dem Substrat:
- Das aufgedampfte Material wandert durch das Vakuum und lagert sich auf der Substratoberfläche ab.Das Substrat ist in der Regel auf einem Halter montiert, der gedreht werden kann, um eine gleichmäßige Beschichtung zu gewährleisten.
- Die Qualität der Substratoberfläche ist von entscheidender Bedeutung; eine glatte Oberfläche fördert eine gleichmäßige Abscheidung, während eine raue Oberfläche zu ungleichmäßiger Schichtdicke und Defekten führen kann.
-
Post-Deposition-Prozesse:
- Nach der Abscheidung kann die dünne Schicht zusätzlichen Behandlungen wie Glühen oder Wärmebehandlung unterzogen werden, um ihre strukturellen und elektrischen Eigenschaften zu verbessern.
- Das Glühen kann dazu beitragen, Spannungen innerhalb der Folie abzubauen, die Haftung zu verbessern und die Kristallinität zu erhöhen, was für die Leistung der Folie in der vorgesehenen Anwendung von wesentlicher Bedeutung ist.
-
Analyse und Qualitätskontrolle:
- Die Eigenschaften der abgeschiedenen Schicht, wie Dicke, Gleichmäßigkeit und Zusammensetzung, werden mit verschiedenen Charakterisierungstechniken analysiert.
- Auf der Grundlage dieser Analyse können die Parameter des Abscheidungsprozesses angepasst werden, um die Qualität der Schicht für bestimmte Anwendungen zu optimieren.
-
Überlegungen zur Material- und Prozessoptimierung:
- Das Molekulargewicht des Ausgangsmaterials und seine Verdampfungsrate sind entscheidende Faktoren, die den Abscheidungsprozess beeinflussen.Materialien mit höherem Molekulargewicht erfordern möglicherweise höhere Verdampfungstemperaturen.
- Die Rotationsgeschwindigkeit des Substrathalters kann sich ebenfalls auf die Gleichmäßigkeit des Films auswirken, wobei schnellere Rotationsgeschwindigkeiten im Allgemeinen zu einer gleichmäßigeren Dickenverteilung führen.
Durch die sorgfältige Kontrolle jedes dieser Faktoren ermöglicht die thermische Verdampfungstechnik die Herstellung hochwertiger dünner Schichten mit präzisen, auf spezifische Anwendungen zugeschnittenen Eigenschaften.Diese Methode wird in vielen Branchen eingesetzt, von der Elektronik bis zur Optik, wo dünne Schichten eine entscheidende Rolle für die Leistung und Funktionalität von Geräten spielen.
Zusammenfassende Tabelle:
Schritt | Beschreibung |
---|---|
Auswahl des Materials | Wählen Sie eine reine Materialquelle mit geeigneten Verdampfungseigenschaften. |
Aufbau der Vakuumkammer | Verwenden Sie eine Hochvakuumumgebung, um Verunreinigungen zu minimieren und eine gleichmäßige Abscheidung zu gewährleisten. |
Verdampfung des Materials | Erhitzen Sie das Material mit Hilfe einer Widerstandsheizung oder eines Elektronenstrahls bis zu seinem Verdampfungspunkt. |
Aufbringen auf ein Substrat | Bringen Sie das aufgedampfte Material auf ein glattes Substrat auf, um eine gleichmäßige Schichtdicke zu erreichen. |
Post-Deposition-Verfahren | Glühen oder Wärmebehandlung zur Verbesserung der Filmeigenschaften wie Haftung und Kristallinität. |
Analyse und Qualitätskontrolle | Analysieren Sie die Filmeigenschaften (Dicke, Gleichmäßigkeit) und optimieren Sie die Prozessparameter. |
Sind Sie bereit, hochwertige dünne Schichten für Ihre Anwendungen herzustellen? Kontaktieren Sie noch heute unsere Experten um loszulegen!