Die Aufheizgeschwindigkeit für Aluminiumoxid hängt von der jeweiligen Anwendung und der Art des verwendeten Ofens ab.Im Allgemeinen liegt die empfohlene Heizrate für Aluminiumoxid-Ofenrohre bei 5-10°C/min, wobei 5°C/min vorzuziehen sind, um einen Temperaturschock zu vermeiden und eine gleichmäßige Sinterung zu gewährleisten.Auch die Abkühlgeschwindigkeit sollte kontrolliert werden, idealerweise unter 10°C/min, wobei 5°C/min optimal sind.Schnelle Temperaturwechsel können thermische Spannungen verursachen, die zu Bruch oder unzureichender Sinterung führen.Für die erste Erwärmung wird eine langsamere Rate von 150-300°C pro Stunde empfohlen, um den thermischen Schock zu minimieren.Diese Richtlinien gewährleisten die Langlebigkeit und Leistung von Aluminiumoxidkomponenten in Hochtemperaturumgebungen.
Die wichtigsten Punkte werden erklärt:
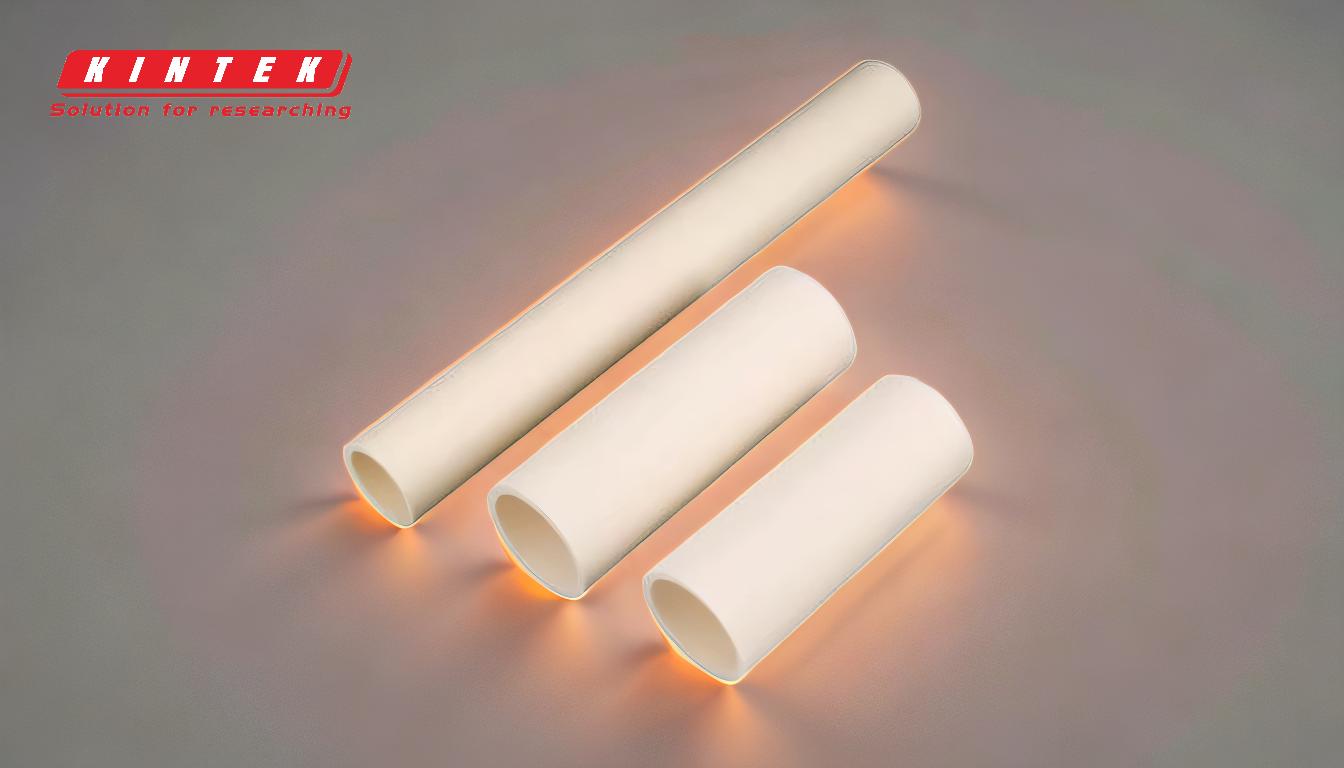
-
Empfohlene Heizrate für Tonerde:
- Die Standardheizrate für Aluminiumoxid-Ofenrohre beträgt 5-10°C/min mit 5°C/min ist die bevorzugte Geschwindigkeit.Dies gewährleistet eine gleichmäßige Erwärmung und minimiert das Risiko eines Temperaturschocks.
- Eine langsamere Erhitzungsrate von 150-300°C pro Stunde wird für die ersten 1-1,5 Stunden empfohlen, um den thermischen Schock zu reduzieren, insbesondere während der ersten Aufwärmphase.
-
Wichtigkeit einer kontrollierten Erwärmung:
- Zu hohe Heizraten (über 10°C/min) können zu unzureichender Sinterung und ungleichmäßige Sinterungsgrade im gesamten Material.Dies führt zu Hochtemperatur-Schmelzspitzen und erhöhter Kristallinität, was die strukturelle Integrität des Aluminiumoxids beeinträchtigen kann.
- Eine kontrollierte Erwärmung gewährleistet eine gleichmäßige Sinterung und verhindert innere Spannungen, die zu Rissen oder Bruch führen könnten.
-
Überlegungen zur Abkühlungsrate:
- Die Abkühlgeschwindigkeit sollte unter 10°C/min mit 5°C/min ist ideal.Schnelles Abkühlen kann zu Thermoschock der zum Versagen des Materials führt.
- Eine allmähliche Abkühlung ist wichtig, um die strukturelle Integrität von Aluminiumoxid zu erhalten, insbesondere nach Hochtemperaturbehandlungen.
-
Empfindlichkeit gegenüber Temperaturschocks:
- Aluminiumoxid ist aufgrund seiner Sprödigkeit sehr empfindlich gegenüber Temperaturschocks.Schnelle Temperaturwechsel können zu Rissen oder Bruch führen.
- Eine langsamere Aufheiz- und Abkühlgeschwindigkeit (z. B. 150-300 °C pro Stunde beim Aufheizen und 75-150 °C pro Stunde beim Abkühlen) wird empfohlen, um dieses Risiko zu verringern.
-
Anwendungsspezifische Empfehlungen:
- Für Tonerde-Ofenrohre Die Aufheiz- und Abkühlraten sollten mit der Konstruktion und den Betriebsanforderungen des Ofens in Einklang stehen.Eine natürliche Abkühlung nach der Wärmebehandlung sollte vermieden werden, da sie zu einem raschen Temperaturabfall und möglichen Schäden führen kann.
- In Drehrohröfen Faktoren wie Neigungswinkel, Rotationsgeschwindigkeit, Rohrlänge und Materialflusseigenschaften beeinflussen den Wärmebehandlungsprozess.Die Anpassung dieser Parameter kann zur Aufrechterhaltung optimaler Erwärmungs- und Abkühlungsraten beitragen.
-
Materialeigenschaften und Langlebigkeit:
- Aluminiumoxid hat eine ausgezeichnete Temperaturwechselbeständigkeit, eine hohe Dichte und ist säure-, laugen- und erosionsbeständig.Aufgrund dieser Eigenschaften eignet es sich für Hochtemperaturanwendungen (bis zu 1800 °C).
- Eine angemessene Aufheiz- und Abkühlrate gewährleistet die Haltbarkeit des Materials und verlängert seine Lebensdauer.
-
Praktische Tipps für Gerätebenutzer:
- Stellen Sie im Ofenprogramm immer eine kontrollierte Abkühlgeschwindigkeit ein; vermeiden Sie ein abruptes Anhalten des Programms bei hohen Temperaturen.
- Verwenden Sie allmähliche Temperaturänderungen, um thermischen Stress zu vermeiden und eine gleichbleibende Materialleistung zu gewährleisten.
- Überwachen Sie den Erwärmungs- und Abkühlungsprozess genau, insbesondere während der anfänglichen Aufwärm- und der abschließenden Abkühlungsphase.
Durch die Einhaltung dieser Richtlinien können die Benutzer die Leistung und Langlebigkeit von Aluminiumoxidkomponenten in Hochtemperaturumgebungen optimieren, gleichbleibende Ergebnisse gewährleisten und das Risiko von Materialversagen minimieren.
Zusammenfassende Tabelle:
Parameter | Empfehlung |
---|---|
Aufheizrate | 5-10°C/min (vorzugsweise 5°C/min) |
Anfängliche Aufheizrate | 150-300°C pro Stunde in den ersten 1-1,5 Stunden |
Abkühlungsrate | Weniger als 10°C/min (idealerweise 5°C/min) |
Empfindlichkeit gegenüber Temperaturschocks | Vermeiden Sie schnelle Temperaturschwankungen, um Risse und Brüche zu verhindern. |
Hauptvorteil | Gewährleistet gleichmäßige Sinterung, Haltbarkeit und Langlebigkeit in Hochtemperaturumgebungen |
Benötigen Sie Hilfe bei der Optimierung Ihres Aluminiumoxid-Wärmebehandlungsprozesses? Kontaktieren Sie noch heute unsere Experten für maßgeschneiderte Lösungen!