Reaktives Sputtern ist ein spezielles Verfahren zur Abscheidung von Dünnschichten, bei dem ein reaktives Gas, z. B. Sauerstoff oder Stickstoff, in eine Vakuumkammer eingeleitet wird, die ein Targetmaterial und ein Inertgas wie Argon enthält. Das reaktive Gas geht mit den gesputterten Atomen des Zielmaterials eine chemische Wechselwirkung ein und bildet Verbindungen wie Oxide oder Nitride, die dann als dünne Schichten auf einem Substrat abgeschieden werden. Dieses Verfahren ermöglicht eine präzise Steuerung der Schichtzusammensetzung und -eigenschaften und eignet sich daher ideal für Anwendungen, die bestimmte funktionelle Eigenschaften erfordern, z. B. Sperrschichten oder optische Beschichtungen. Es erfordert jedoch eine sorgfältige Steuerung von Parametern wie Gasflussraten und Partialdrücken, um Probleme wie Hysterese zu vermeiden und eine optimale Schichtqualität zu gewährleisten.
Die wichtigsten Punkte werden erklärt:
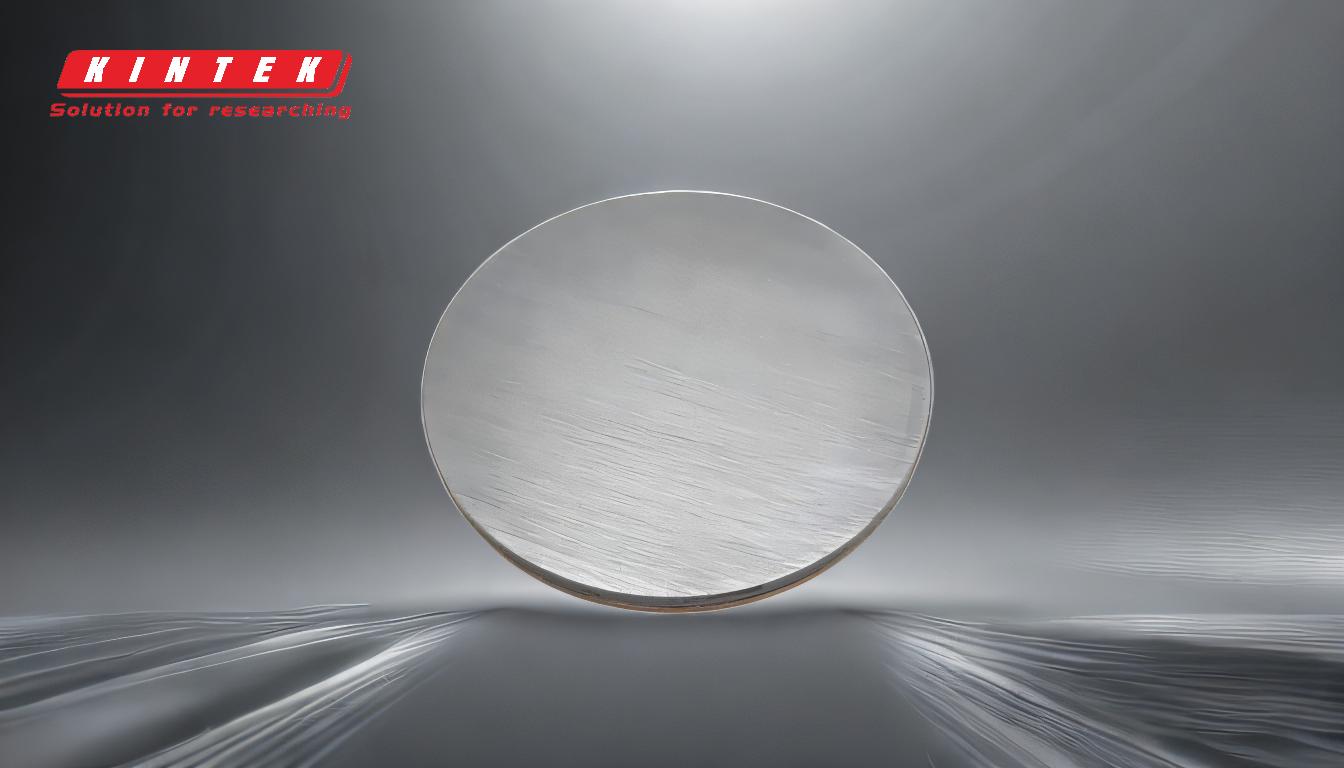
-
Grundlegender Mechanismus des reaktiven Sputterns:
- Beim reaktiven Sputtern wird ein reaktives Gas (z. B. Sauerstoff, Stickstoff) zusammen mit einem Inertgas (z. B. Argon) in eine Vakuumkammer eingeleitet.
- Das Targetmaterial wird mit Ionen aus dem Inertgas beschossen, wodurch Atome aus dem Target herausgeschleudert (gesputtert) werden.
- Diese zerstäubten Atome reagieren dann mit dem reaktiven Gas in der Kammer und bilden Verbindungen wie Oxide oder Nitride.
- Die resultierende Verbindung wird als dünner Film auf dem Substrat abgeschieden.
-
Die Rolle von reaktiven und inerten Gasen:
- Inertes Gas (Argon): Liefert die zum Sputtern des Zielmaterials erforderlichen Ionen. Argon wird in der Regel verwendet, da es chemisch inert ist und nicht mit dem Target oder dem Substrat reagiert.
- Reaktives Gas (Sauerstoff, Stickstoff): Reagiert chemisch mit den gesputterten Targetatomen und bildet Verbindungen wie Titanoxid (TiO₂) oder Titannitrid (TiN).
- Das Verhältnis von inertem zu reaktivem Gas ist entscheidend für die Steuerung der Stöchiometrie und der Eigenschaften der abgeschiedenen Schicht.
-
Chemische Reaktionen in der Kammer:
- Das reaktive Gas wird in der vom Inertgas geschaffenen Plasmaumgebung ionisiert.
- Diese Ionen reagieren mit den gesputterten Zielatomen und bilden molekulare Verbindungen.
- Beim Sputtern von Silizium in Gegenwart von Sauerstoff entsteht beispielsweise Siliziumoxid (SiO₂), während beim Sputtern von Titan in Gegenwart von Stickstoff Titannitrid (TiN) entsteht.
-
Kontrolle der Filmzusammensetzung und -eigenschaften:
- Die Zusammensetzung der abgeschiedenen Schicht kann durch die Einstellung der Partialdrücke der reaktiven und inerten Gase genau kontrolliert werden.
- Diese Kontrolle ist für die Optimierung der funktionellen Eigenschaften wie Spannung, Brechungsindex und elektrische Leitfähigkeit von entscheidender Bedeutung.
- Das Berg-Modell wird häufig zur Vorhersage der Auswirkungen des Reaktivgases auf die Targeterosion und die Abscheideraten verwendet und hilft so bei der Prozessoptimierung.
-
Herausforderungen und Komplexität:
- Hysterese-Verhalten: Die Einführung eines reaktiven Gases kann zu einem nichtlinearen Verhalten im Abscheidungsprozess führen, was eine sorgfältige Kontrolle von Parametern wie Gasflussraten und Partialdrücken erfordert.
- Target-Vergiftung: Ein Übermaß an reaktivem Gas kann eine Verbindungsschicht auf der Oberfläche des Targets bilden, die die Sputtereffizienz verringert. Dies wird durch einen ausgeglichenen Reaktivgasfluss und die Aufrechterhaltung eines stabilen Plasmas verhindert.
- Prozessstabilität: Um gleichbleibende Schichteigenschaften zu erzielen, ist eine präzise Steuerung der reaktiven Sputterumgebung erforderlich, einschließlich Gasverhältnis, Druck und Stromversorgung.
-
Anwendungen des reaktiven Sputterns:
- Barriereschichten: Reaktives Sputtern wird zur Abscheidung dünner Schichten verwendet, die als Diffusionsbarrieren in der Mikroelektronik dienen, z. B. Titannitrid (TiN)-Schichten in Halbleiterbauelementen.
- Optische Beschichtungen: Schichten wie Siliziumoxid (SiO₂) und Titanoxid (TiO₂) werden aufgrund ihrer einstellbaren Brechungsindizes in optischen Anwendungen eingesetzt.
- Verschleißfeste Beschichtungen: Titannitrid (TiN) und ähnliche Verbindungen werden auf Werkzeuge und Bauteile aufgetragen, um deren Haltbarkeit und Verschleißfestigkeit zu erhöhen.
-
Varianten des reaktiven Sputterns:
- DC Reaktives Sputtern: Zur Erzeugung des Plasmas wird Gleichstrom verwendet. Es ist einfacher, kann aber zu einer Vergiftung des Targets führen.
- RF (Hochfrequenz) Reaktives Sputtern: Verwendet hochfrequenten Wechselstrom, der sich besser für isolierende Materialien eignet und die Vergiftung des Targets verringern kann.
-
Vorteile gegenüber dem nicht-reaktiven Sputtern:
- Ermöglicht die Abscheidung von Verbundschichten mit präziser Stöchiometrie und maßgeschneiderten Eigenschaften.
- Erweitert die Palette der Materialien, die abgeschieden werden können, einschließlich Oxide, Nitride und Karbide.
- Bietet eine größere Flexibilität bei der Abstimmung der Schichteigenschaften auf bestimmte Anwendungen.
Durch das Verständnis dieser Schlüsselpunkte können Käufer von Anlagen und Verbrauchsmaterialien die technischen Feinheiten des reaktiven Sputterns besser einschätzen und fundierte Entscheidungen über dessen Einsatz in ihren Verfahren treffen.
Zusammenfassende Tabelle:
Hauptaspekt | Beschreibung |
---|---|
Mechanismus | Reaktives Gas reagiert mit den gesputterten Zielatomen und bildet Verbindungen (z. B. Oxide, Nitride). |
Verwendete Gase | Inertgas (Argon) zum Sputtern; reaktives Gas (Sauerstoff, Stickstoff) zur Bildung von Verbindungen. |
Anwendungen | Barriereschichten, optische Beschichtungen, verschleißfeste Beschichtungen. |
Herausforderungen | Hysterese, Target-Vergiftung, Prozessstabilität. |
Vorteile | Präzise Schichtzusammensetzung, maßgeschneiderte Eigenschaften, erweitertes Materialspektrum. |
Entdecken Sie, wie reaktives Sputtern Ihre Prozesse verbessern kann. Kontaktieren Sie uns noch heute für eine fachkundige Beratung!