Das Lasersintern ist ein Verfahren der additiven Fertigung (3D-Druck), bei dem ein Hochleistungslaser verwendet wird, um pulverförmiges Material zu einer festen Struktur zu verschmelzen.Es wird häufig in Branchen wie der Luft- und Raumfahrt, der Automobilindustrie und dem Gesundheitswesen zur Herstellung komplexer, hochpräziser Teile eingesetzt.Bei diesem Verfahren wird pulverförmiges Material aufgeschichtet und selektiv mit einem Laser gesintert, um das gewünschte Objekt Schicht für Schicht aufzubauen.Dieses Verfahren ist besonders vorteilhaft für die Herstellung von Teilen mit komplizierten Geometrien, hoher Festigkeit und ausgezeichneter Oberflächengüte.Außerdem ist es energie- und kosteneffizient, da es den Materialabfall minimiert und die Verwendung von Materialien mit hohem Schmelzpunkt ermöglicht, ohne diese vollständig zu schmelzen.
Die wichtigsten Punkte erklärt:
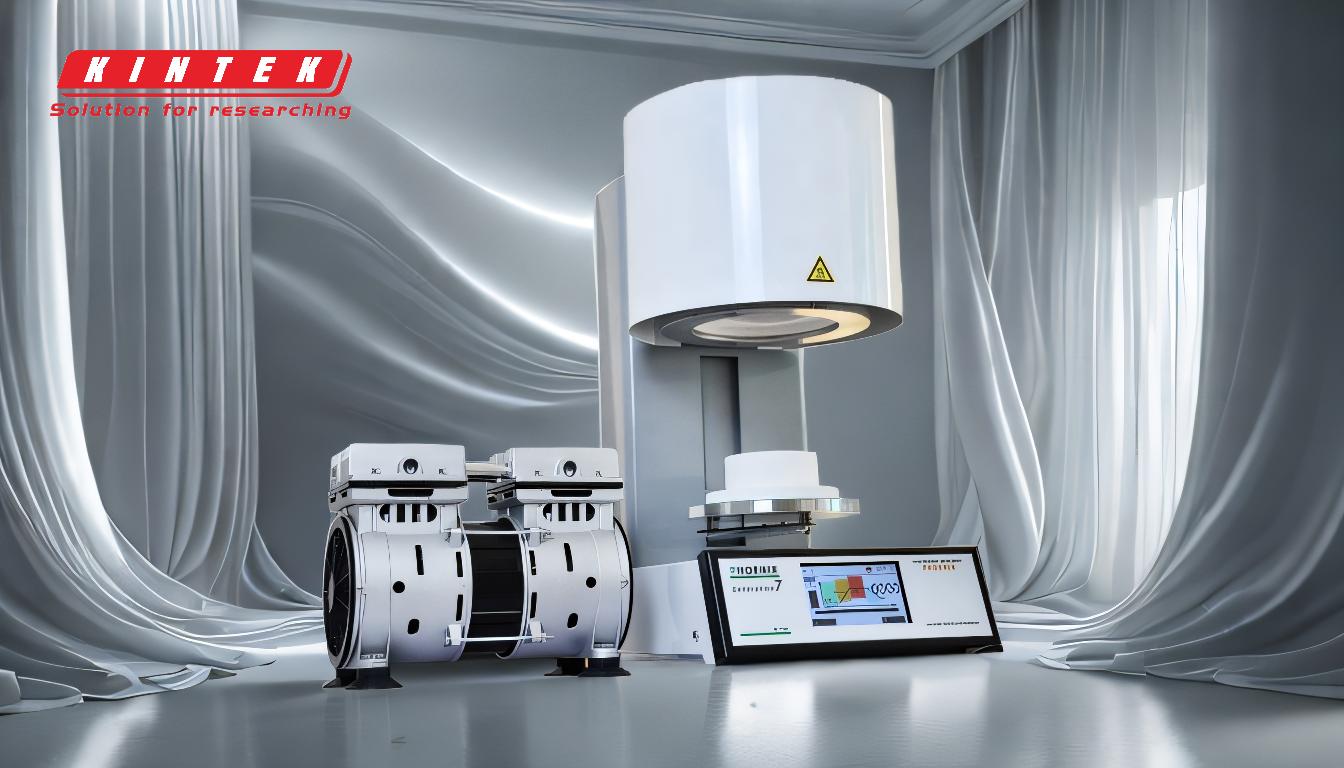
-
Definition des Laser-Sinterns:
- Das Lasersintern ist ein additives Fertigungsverfahren, bei dem ein Laser verwendet wird, um pulverförmiges Material zu einer festen Struktur zu verschmelzen.
- Es handelt sich um ein schichtweises Verfahren, bei dem jede Pulverschicht selektiv gesintert wird, um das endgültige 3D-Objekt zu erzeugen.
-
Beim Laser-Sintern verwendete Materialien:
- Zu den gebräuchlichen Materialien gehören Metalle (z. B. Titan, Aluminium, Edelstahl), Polymere (z. B. Nylon, Polyamid) und Keramiken.
- Die Wahl des Materials hängt von den gewünschten Eigenschaften des Endprodukts ab, wie Festigkeit, Haltbarkeit und Wärmebeständigkeit.
-
Prozess-Übersicht:
- Schritt 1: Vorbereitung:Ein 3D-Modell des Teils wird mit einer CAD-Software erstellt und in dünne Schichten zerlegt.
- Schritt 2: Pulverbeschichtung:Eine dünne Schicht des pulverförmigen Materials wird gleichmäßig auf der Bauplattform verteilt.
- Schritt 3: Laser-Sintern:Ein Hochleistungslaser tastet das Pulverbett ab und sintert das Pulver selektiv entsprechend dem Design des 3D-Modells.
- Schritt 4: Hinzufügen von Schichten:Die Bauplattform senkt sich, und eine neue Schicht Pulver wird über die vorherige Schicht aufgetragen.Der Vorgang wiederholt sich, bis das Teil fertig ist.
- Schritt 5: Nachbearbeitung:Nach der Herstellung des Teils kann es weiteren Prozessen wie Kühlung, Reinigung und Oberflächenbearbeitung unterzogen werden.
-
Vorteile des Laser-Sinterns:
- Materialkonservierung:Das Lasersintern minimiert den Materialabfall, da nur das benötigte Pulver gesintert wird.
- Energie-Effizienz:Das Verfahren benötigt weniger Energie als herkömmliche Herstellungsmethoden, da nicht das gesamte Material geschmolzen werden muss.
- Kosten-Nutzen-Verhältnis:Geringerer Materialabfall und Energieverbrauch führen zu niedrigeren Produktionskosten.
- Flexibilität bei der Gestaltung:Das Lasersintern ermöglicht die Herstellung komplexer Geometrien und komplizierter Designs, die mit herkömmlichen Verfahren nur schwer oder gar nicht zu realisieren wären.
- Hohe Präzision und Konsistenz:Das Verfahren bietet eine hervorragende Kontrolle über den Sinterprozess, was zu Teilen mit hoher Maßgenauigkeit und gleichbleibender Qualität führt.
- Verbesserte Materialeigenschaften:Gesinterte Teile weisen aufgrund des kontrollierten Sinterprozesses häufig bessere mechanische Eigenschaften auf, wie z. B. eine höhere Festigkeit und Härte.
-
Anwendungen des Laser-Sinterns:
- Luft- und Raumfahrt:Zur Herstellung leichter, hochfester Komponenten wie Turbinenschaufeln und Strukturteile.
- Automobilindustrie:Anwendung bei der Herstellung von kundenspezifischen Teilen, Prototypen und komplexen Komponenten wie Motorteilen und Halterungen.
- Gesundheitswesen:Für die Herstellung von patientenspezifischen Implantaten, Prothesen und chirurgischen Instrumenten mit hoher Präzision.
- Konsumgüter:Wird bei der Herstellung von Schmuck, Brillen und anderen Konsumgütern mit komplizierten Designs verwendet.
-
Herausforderungen und Überlegungen:
- Materielle Beschränkungen:Nicht alle Materialien sind für das Lasersintern geeignet, und einige erfordern spezielle Pulver oder Nachbehandlungen.
- Oberflächengüte:Beim Lasersintern entstehen zwar Teile mit guter Oberflächengüte, aber für Anwendungen, die extrem glatte Oberflächen erfordern, kann eine zusätzliche Nachbearbeitung erforderlich sein.
- Kosten der Ausrüstung:Die Anfangsinvestitionen für Lasersinteranlagen können hoch sein, was für kleine Hersteller ein Hindernis darstellen kann.
- Prozesskontrolle:Um konsistente Ergebnisse zu erzielen, müssen Parameter wie Laserleistung, Scangeschwindigkeit und Pulverschichtdicke präzise gesteuert werden.
Zusammenfassend lässt sich sagen, dass das Lasersintern ein vielseitiges und effizientes additives Fertigungsverfahren ist, das zahlreiche Vorteile bietet, darunter Materialeinsparung, Energieeffizienz und die Möglichkeit, komplexe, hochpräzise Teile herzustellen.Trotz einiger Herausforderungen wird es in vielen Branchen eingesetzt, da es die Herstellung langlebiger, hochwertiger Komponenten mit minimalem Abfall ermöglicht.
Zusammenfassende Tabelle:
Aspekt | Einzelheiten |
---|---|
Definition | Additive Fertigung, bei der ein Laser verwendet wird, um pulverförmiges Material Schicht für Schicht zu verschmelzen. |
Werkstoffe | Metalle (Titan, Aluminium), Polymere (Nylon), Keramiken. |
Prozess-Schritte | Vorbereitung, Pulverbeschichtung, Lasersintern, Schichtzugabe, Nachbearbeitung. |
Vorteile | Materialeinsparung, Energieeffizienz, Kosteneffizienz, Designflexibilität, hohe Präzision. |
Anwendungen | Luft- und Raumfahrt, Automobilindustrie, Gesundheitswesen, Konsumgüter. |
Herausforderungen | Materialbeschränkungen, Oberflächengüte, Anlagenkosten, Prozesskontrolle. |
Sind Sie bereit zu erfahren, wie das Lasersintern Ihren Produktionsprozess verbessern kann? Kontaktieren Sie uns noch heute um mehr zu erfahren!