PVD (Physical Vapour Deposition) und CVD (Chemical Vapour Deposition) sind zwei weit verbreitete Techniken zur Abscheidung dünner Filme auf Substraten, sie unterscheiden sich jedoch erheblich in ihren Prozessen, Betriebsbedingungen und resultierenden Beschichtungseigenschaften. PVD umfasst die physikalische Verdampfung fester Materialien, typischerweise im Vakuum, und deren Abscheidung auf einem Substrat bei niedrigeren Temperaturen (250 °C bis 500 °C). Im Gegensatz dazu beruht CVD auf chemischen Reaktionen zwischen gasförmigen Vorläufern und dem Substrat bei höheren Temperaturen (450 °C bis 1050 °C). Diese Unterschiede führen zu Schwankungen in der Schichtdicke, Gleichmäßigkeit, Beanspruchung und Anwendungseignung. PVD wird oft wegen seiner Fähigkeit zur Abscheidung einer breiteren Palette von Materialien, einschließlich Metallen und Keramiken, bevorzugt, während CVD sich durch die Herstellung dichterer, gleichmäßigerer Beschichtungen, insbesondere für Keramiken und Polymere, auszeichnet. Die Wahl zwischen PVD und CVD hängt von Faktoren wie den gewünschten Beschichtungseigenschaften, dem Substratmaterial und den Anwendungsanforderungen ab.
Wichtige Punkte erklärt:
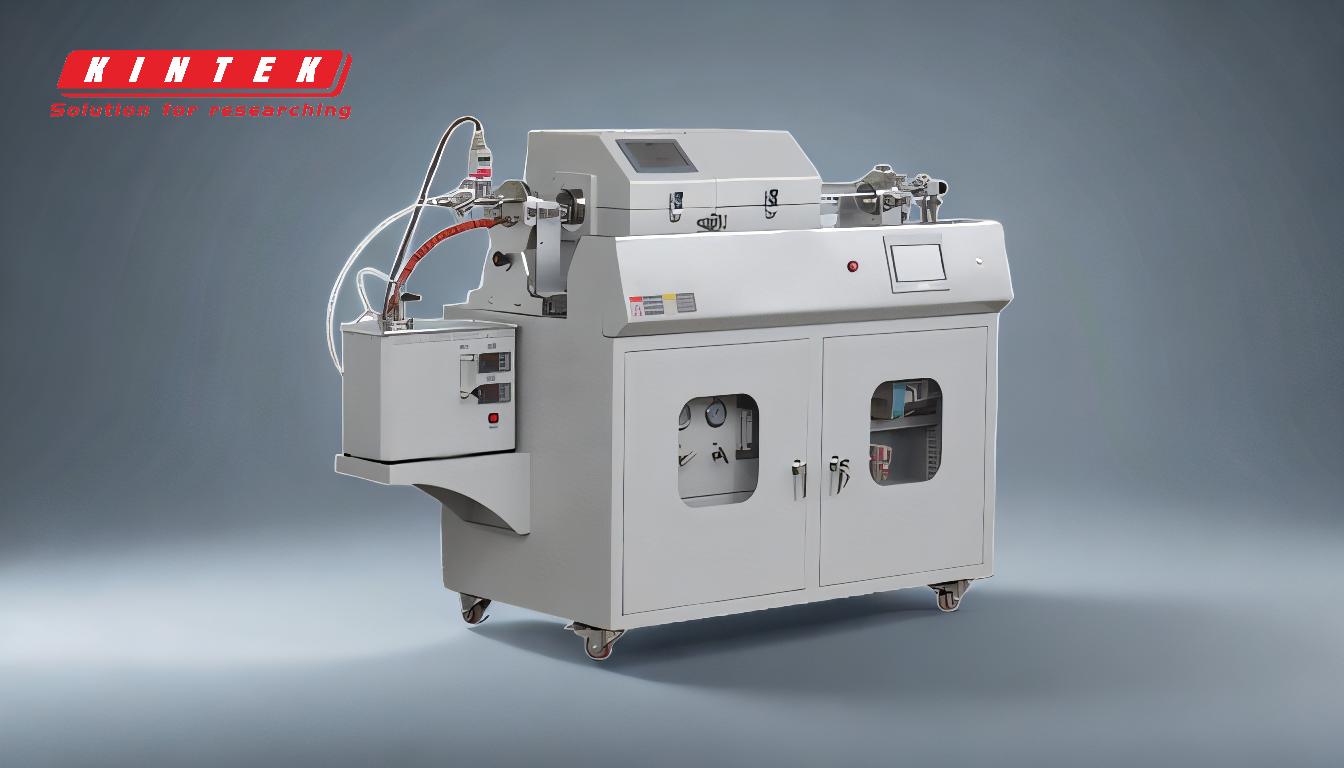
-
Ablagerungsmechanismus:
- PVD: Beinhaltet die physikalische Verdampfung fester Materialien (z. B. Metalle, Legierungen oder Keramik) durch Prozesse wie Sputtern oder Verdampfen. Die verdampften Atome lagern sich dann direkt auf dem Substrat ab.
- CVD: Beruht auf chemischen Reaktionen zwischen gasförmigen Vorläufern und dem Substrat. Die gasförmigen Moleküle reagieren auf der Substratoberfläche und bilden durch einen multidirektionalen Abscheidungsprozess eine feste Beschichtung.
-
Betriebstemperatur:
- PVD: Funktioniert bei relativ niedrigeren Temperaturen, typischerweise zwischen 250 °C und 500 °C. Dadurch ist es für temperaturempfindliche Untergründe geeignet.
- CVD: Erfordert höhere Temperaturen im Bereich von 450 °C bis 1050 °C, was die Verwendung bei bestimmten Materialien einschränken kann, aber die Bildung dichterer Beschichtungen ermöglicht.
-
Schichtdicke und Gleichmäßigkeit:
- PVD: Erzeugt dünnere Beschichtungen (3–5 μm), die im Vergleich zu CVD weniger dicht und weniger gleichmäßig sind. Der Prozess ist schneller, kann jedoch beim Abkühlen zu Druckspannungen führen.
- CVD: Ergibt dickere Beschichtungen (10–20 μm), die dichter und gleichmäßiger sind. Durch die hohe Verarbeitungstemperatur kann es jedoch zu Zugspannungen und feinen Rissen kommen.
-
Beschichtungsmaterialien:
- PVD: Kann ein breiteres Spektrum an Materialien abscheiden, darunter Metalle, Legierungen und Keramik. Aufgrund dieser Vielseitigkeit eignet es sich für Anwendungen, die unterschiedliche Materialeigenschaften erfordern.
- CVD: Hauptsächlich auf Keramik und Polymere beschränkt, daher ideal für Anwendungen, die eine hohe chemische Stabilität und thermische Beständigkeit erfordern.
-
Beschichtungsabdeckung:
- PVD: Die Sichtlinienabscheidung bedeutet, dass sie für die Beschichtung komplexer Geometrien oder verborgener Oberflächen weniger effektiv ist.
- CVD: Die multidirektionale Abscheidung ermöglicht eine bessere Abdeckung komplexer Formen und verborgener Bereiche und macht sie dadurch vielseitiger für komplizierte Komponenten.
-
Anwendungen:
- PVD: Wird häufig in Branchen verwendet, die verschleißfeste, korrosionsbeständige oder dekorative Beschichtungen erfordern, wie z. B. Schneidwerkzeuge, medizinische Geräte und Unterhaltungselektronik.
- CVD: Bevorzugt für Anwendungen, die Hochleistungsbeschichtungen erfordern, wie z. B. Halbleiterfertigung, Luft- und Raumfahrtkomponenten und Hochtemperaturumgebungen.
-
Vor- und Nachteile:
-
PVD-Vorteile:
- Niedrigere Betriebstemperaturen.
- Schnellere Abscheidungsraten.
- Möglichkeit zur Ablagerung einer breiten Palette von Materialien.
-
PVD-Nachteile:
- Weniger gleichmäßige Beschichtungen.
- Begrenzte Abdeckung für komplexe Geometrien.
-
CVD-Vorteile:
- Dichtere und gleichmäßigere Beschichtungen.
- Bessere Abdeckung für komplexe Formen.
-
CVD-Nachteile:
- Höhere Betriebstemperaturen.
- Längere Abscheidungszeiten.
-
PVD-Vorteile:
Zusammenfassend hängt die Wahl zwischen PVD und CVD von den spezifischen Anforderungen der Anwendung ab, einschließlich der gewünschten Beschichtungseigenschaften, des Substratmaterials und der Betriebsbedingungen. PVD ist ideal für Anwendungen, die Vielseitigkeit und niedrigere Temperaturen erfordern, während CVD besser für Hochleistungsbeschichtungen auf komplexen Geometrien geeignet ist.
Übersichtstabelle:
Aspekt | PVD | CVD |
---|---|---|
Ablagerungsmechanismus | Physikalische Verdampfung fester Materialien (z. B. Sputtern, Verdampfen). | Chemische Reaktionen zwischen gasförmigen Vorläufern und dem Substrat. |
Betriebstemperatur | 250°C~500°C (niedriger, geeignet für empfindliche Untergründe). | 450°C~1050°C (höher, ermöglicht dichtere Beschichtungen). |
Beschichtungsdicke | Dünner (3–5 μm), weniger dicht und weniger gleichmäßig. | Dicker (10–20 μm), dichter und gleichmäßiger. |
Beschichtungsmaterialien | Metalle, Legierungen und Keramik (breiteres Spektrum). | Hauptsächlich Keramik und Polymere (begrenzte Auswahl). |
Beschichtungsabdeckung | Sichtlinie, weniger effektiv bei komplexen Geometrien. | Multidirektional, bessere Abdeckung für komplexe Formen. |
Anwendungen | Verschleißfeste, korrosionsbeständige, dekorative Beschichtungen. | Hochleistungsbeschichtungen (z. B. Halbleiter, Luft- und Raumfahrt). |
Vorteile | Niedrigere Temperaturen, schnellere Abscheidung, vielseitige Materialoptionen. | Dichtere Beschichtungen, gleichmäßige Abdeckung, ideal für komplexe Geometrien. |
Nachteile | Weniger gleichmäßige Beschichtungen, begrenzte Abdeckung für komplexe Formen. | Höhere Temperaturen, längere Abscheidungszeiten. |
Benötigen Sie Hilfe bei der Auswahl zwischen PVD und CVD für Ihre Anwendung? Kontaktieren Sie noch heute unsere Experten !