Fused Deposition Modeling (FDM) ist ein weit verbreitetes additives Fertigungsverfahren, bei dem thermoplastisches Material durch eine beheizte Düse extrudiert und Schicht für Schicht aufgetragen wird, um ein dreidimensionales Objekt zu erzeugen.Das Verfahren beinhaltet eine präzise horizontale Bewegung der Düse und eine vertikale Bewegung der Bauplattform und ermöglicht die Herstellung komplexer Geometrien.FDM ist bekannt für seine Einfachheit, Kosteneffizienz und Vielseitigkeit bei der Materialverwendung, was es zu einer beliebten Wahl für das Prototyping, Funktionstests und die Produktion von Teilen für den Endverbrauch macht.
Die wichtigsten Punkte erklärt:
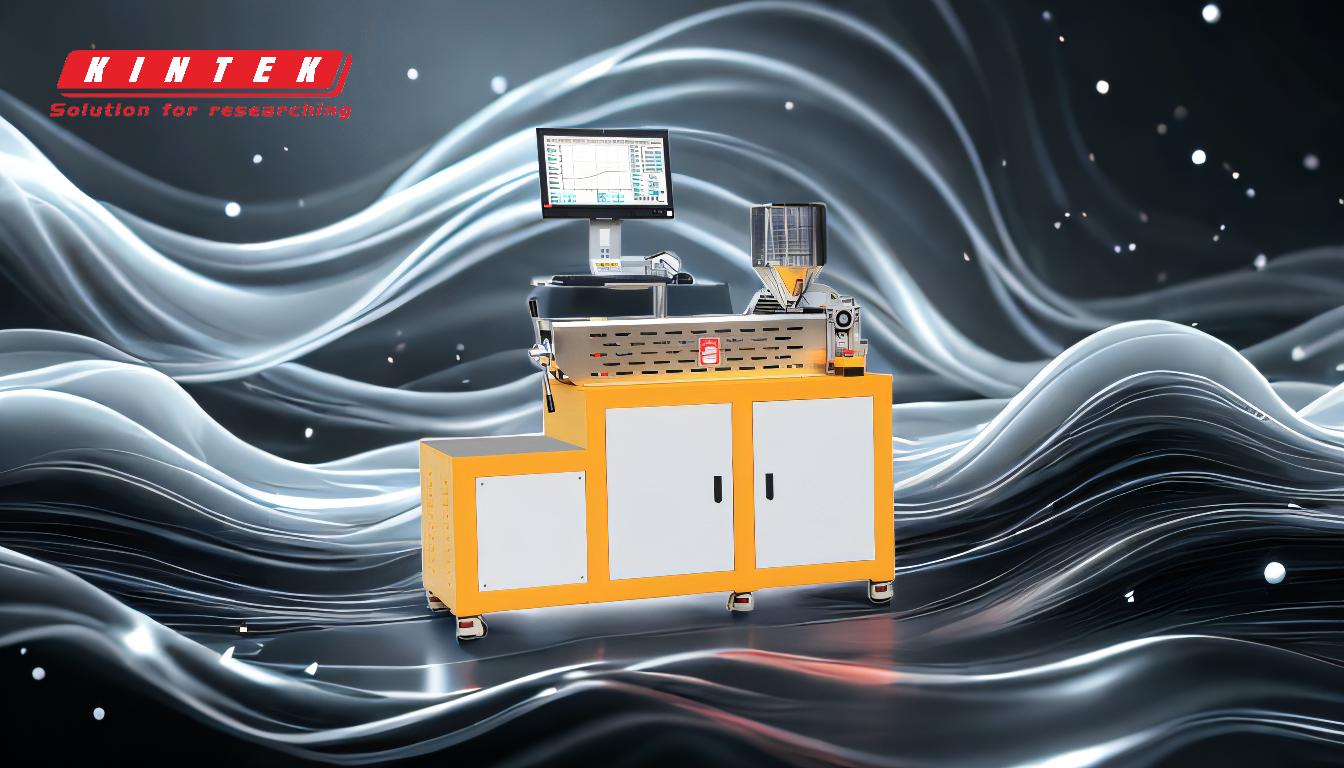
-
Definition und Überblick über FDM:
- Fused Deposition Modeling (FDM) ist eine Art von additivem Fertigungsverfahren, bei dem Objekte Schicht für Schicht aus thermoplastischen Materialien aufgebaut werden.
- Es ist ein Markenzeichen von Stratasys, aber der Begriff wird oft allgemein verwendet, um ähnliche extrusionsbasierte 3D-Drucktechnologien zu beschreiben.
-
Material-Extrusionsverfahren:
- Das Verfahren beginnt mit einem thermoplastischen Filament, das in eine beheizte Düse eingeführt wird.
- Die Düse erhitzt das Material bis zu seinem Schmelzpunkt, so dass es in einem halbflüssigen Zustand extrudiert werden kann.
- Das extrudierte Material wird kontrolliert auf eine Bauplattform aufgebracht und folgt dabei einem vordefinierten Pfad, der auf dem 3D-Modell basiert.
-
Schicht-für-Schicht-Abscheidung:
- Die Düse bewegt sich horizontal, um Material in Form der aktuellen Schicht aufzutragen.
- Nach Fertigstellung jeder Schicht bewegt sich die Bauplattform nach unten (oder die Düse nach oben), um die Ablagerung der nächsten Schicht zu ermöglichen.
- Dieses schichtweise Vorgehen wird fortgesetzt, bis das gesamte Objekt vollständig geformt ist.
-
Bewegung und Präzision:
- Die Düse ist in der Lage, eine präzise horizontale Bewegung auszuführen, die von Schrittmotoren oder Servomotoren gesteuert wird und eine genaue Materialplatzierung gewährleistet.
- Die vertikale Bewegung der Bauplattform ist ebenso präzise und ermöglicht eine gleichbleibende Schichtdicke und allgemeine Maßgenauigkeit.
-
Bei FDM verwendete Materialien:
- Zu den gängigen Materialien gehören ABS (Acrylnitril-Butadien-Styrol), PLA (Polymilchsäure), PETG (Polyethylenterephthalat-Glykol) und verschiedene technische Thermoplaste.
- Diese Materialien werden aufgrund ihrer mechanischen Eigenschaften, ihrer thermischen Stabilität und ihrer leichten Extrusionsfähigkeit ausgewählt.
-
Anwendungen von FDM:
- Prototyping:FDM wird aufgrund seiner Schnelligkeit und Kosteneffizienz häufig für die Herstellung von Prototypen verwendet.
- Funktionale Prüfung:Mit FDM hergestellte Teile können für Funktionstests verwendet werden, da die Materialien die Eigenschaften der endgültigen Produktionsteile imitieren können.
- Teile für den Endgebrauch:In einigen Fällen wird FDM für die Herstellung von Endverbrauchsteilen verwendet, insbesondere wenn es sich um kundenspezifische oder Kleinserienfertigung handelt.
-
Vorteile von FDM:
- Kostengünstig:FDM ist eine der erschwinglichsten 3D-Drucktechnologien, die auch für kleine Unternehmen und Hobbyanwender zugänglich ist.
- Material Vielseitigkeit:Es kann eine breite Palette thermoplastischer Materialien verwendet werden, was eine hohe Flexibilität bei den Materialeigenschaften ermöglicht.
- Einfacher Gebrauch:FDM-Drucker sind relativ einfach zu bedienen und zu warten, so dass sie sich für Anwender mit unterschiedlichem Kenntnisstand eignen.
-
Beschränkungen von FDM:
- Oberfläche:Mit FDM hergestellte Teile haben oft eine raue Oberfläche, die aus ästhetischen oder funktionalen Gründen nachbearbeitet werden muss.
- Schichthaftung:Die Festigkeit von FDM-Teilen kann durch die Adhäsion zwischen den Schichten begrenzt sein, was die mechanische Gesamtleistung beeinträchtigen kann.
- Geschwindigkeit:FDM ist zwar schneller als einige andere 3D-Druckverfahren, kann aber im Vergleich zu herkömmlichen Herstellungsverfahren für große oder komplexe Teile immer noch langsamer sein.
-
Nachbearbeitung:
- Schleifen und Polieren:Um die Oberfläche zu verbessern, können FDM-Teile geschliffen und poliert werden.
- Lackierung und Beschichtung:Teile können lackiert oder beschichtet werden, um ihr Aussehen zu verbessern oder zusätzlichen Schutz zu bieten.
- Glühen:Einige Materialien können von einem Glühen profitieren, einem Wärmebehandlungsverfahren, das die mechanischen Eigenschaften verbessern kann.
-
Zukünftige Entwicklungen bei FDM:
- Werkstoff-Innovationen:Die laufende Forschung konzentriert sich auf die Entwicklung neuer Materialien mit verbesserten Eigenschaften, wie höhere Festigkeit, bessere Wärmebeständigkeit und bessere Biokompatibilität.
- Multi-Material-Druck:Die Fortschritte in der FDM-Technologie ermöglichen die Verwendung mehrerer Materialien in einem einzigen Druckvorgang, wodurch komplexere und funktionellere Teile möglich werden.
- Verstärkte Automatisierung:Zukünftige FDM-Systeme könnten eine stärkere Automatisierung beinhalten, z. B. einen automatischen Materialwechsel und eine automatische Teileentnahme, um den Herstellungsprozess weiter zu rationalisieren.
Zusammenfassend lässt sich sagen, dass das FDM-Verfahren (Fused Deposition Modeling) eine vielseitige und kostengünstige 3D-Drucktechnologie ist, bei der Objekte mittels Thermoplast-Extrusion Schicht für Schicht aufgebaut werden.Die Einfachheit, die Vielseitigkeit der Materialien und das breite Anwendungsspektrum machen es zu einer beliebten Wahl sowohl für das Prototyping als auch für die Produktion von Teilen für den Endgebrauch.Allerdings gibt es Einschränkungen, z. B. bei der Oberflächenqualität und der Schichthaftung, die durch Nachbearbeitung und ständige technologische Weiterentwicklungen behoben werden können.
Zusammenfassende Tabelle:
Aspekt | Einzelheiten |
---|---|
Verfahren | Schichtweise Extrusion von thermoplastischen Kunststoffen mit einer beheizten Düse. |
Werkstoffe | ABS, PLA, PETG und Thermoplaste in technischer Qualität. |
Anwendungen | Prototyping, Funktionstests und Produktion von Endverbrauchsteilen. |
Vorteile | Kostengünstig, vielseitiges Material und einfache Anwendung. |
Beschränkungen | Raue Oberflächengüte, Probleme mit der Schichthaftung und langsamere Geschwindigkeit bei großen Teilen. |
Nachbearbeitungen | Schleifen, Polieren, Lackieren, Beschichten und Glühen. |
Zukünftige Entwicklungen | Neue Materialien, Multimaterialdruck und verstärkte Automatisierung. |
Entdecken Sie, wie FDM Ihren Prototyping-Prozess verändern kann. Kontaktieren Sie uns noch heute für eine fachkundige Beratung!