Beim Sintern von Beschichtungen wird das Material, in der Regel ein Pulver, auf eine Temperatur unterhalb seines Schmelzpunktes erhitzt, um die Partikelbindung und -verdichtung zu erleichtern, was zu einer kohäsiven und dauerhaften Beschichtung führt.Dieses Verfahren ist in verschiedenen Industriezweigen weit verbreitet, um Schutz- oder Funktionsschichten auf Bauteilen zu erzeugen.Zu den wichtigsten Schritten gehören die Vorbereitung des Pulvers, die Verdichtung, das Erhitzen und das Abkühlen, wobei je nach Material und Anwendung spezielle Techniken wie das Flüssigphasensintern oder das Vakuumsintern zum Einsatz kommen.Das Verfahren gewährleistet die Bildung einer gleichmäßigen, dichten und mechanisch robusten Beschichtung.
Die wichtigsten Punkte werden erklärt:
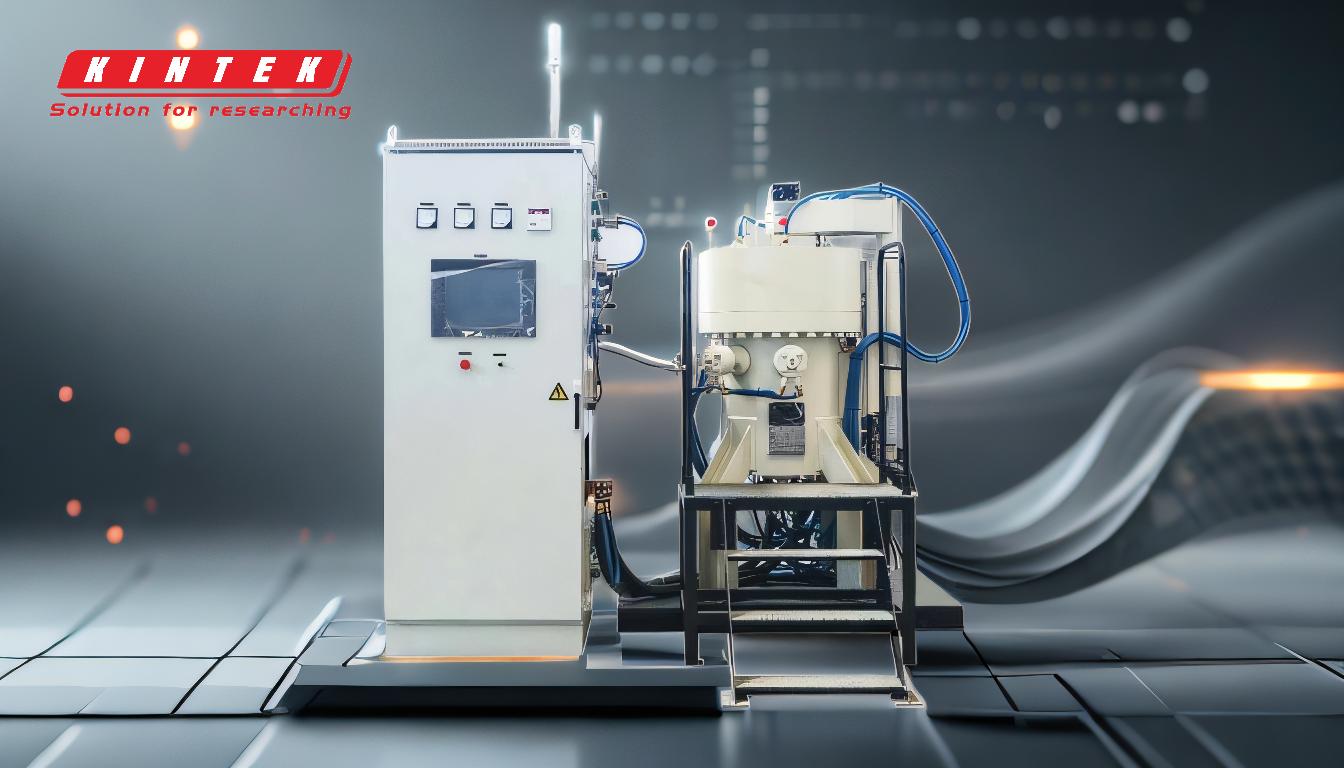
-
Vorbereitung des Pulvers oder Materials:
- Das Verfahren beginnt mit der Vorbereitung des Materials, oft in Pulverform.Bei diesem Pulver kann es sich um ein einzelnes Metall, eine Legierung oder einen Verbundwerkstoff handeln.
- Das Pulver kann mit Zusätzen, Bindemitteln oder Legierungselementen gemischt werden, um Eigenschaften wie Festigkeit, Verschleißfestigkeit oder Wärmeleitfähigkeit zu verbessern.
- Bei Beschichtungen wird das Pulver mit Methoden wie Sprühen, Tauchen oder elektrostatischem Auftragen auf das Substrat aufgebracht.
-
Verdichtung:
- Nach dem Auftragen wird das Pulver verdichtet, um Gleichmäßigkeit zu gewährleisten und Hohlräume zu beseitigen.Dies kann mit mechanischem Druck, Presswerkzeugen oder atmosphärischem Druck in einer kontrollierten Umgebung geschehen.
- Die Verdichtung trägt dazu bei, die gewünschte Form und Dichte der Beschichtung zu erreichen, so dass sie gut auf dem Substrat haftet.
-
Erhitzung und Sinterung:
- Das verdichtete Material wird dann in einem Sinterofen auf eine Temperatur knapp unter seinem Schmelzpunkt erhitzt.Diese Temperatur ist von entscheidender Bedeutung, da sie es den Partikeln ermöglicht, sich zu verbinden, ohne vollständig zu schmelzen.
- Während des Erhitzens diffundieren die Partikel, was zur Bildung von Einschnürungen und zur Verdichtung führt.Diese Phase ist entscheidend für das Erreichen der gewünschten mechanischen Eigenschaften und die Verringerung der Porosität.
- Techniken wie Flüssigphasensintern (LPS) oder Vakuumsintern können eingesetzt werden, um die Partikelbindung zu beschleunigen und die Qualität der Beschichtung zu verbessern.
-
Abkühlung und Erstarrung:
- Nach dem Sintern wird das Material allmählich abgekühlt, damit es sich zu einer festen und kohäsiven Struktur verfestigen kann.
- Die kontrollierte Abkühlung verhindert Risse oder Verformungen und gewährleistet, dass die Beschichtung ihre gewünschten Eigenschaften behält.
-
Nachbearbeiten:
- Je nach Anwendung kann die gesinterte Beschichtung zusätzlichen Nachbearbeitungsschritten wie Bearbeitung, Polieren oder Oberflächenbehandlung unterzogen werden, um ihre Leistung oder ihr Aussehen zu verbessern.
-
Anwendungen und Vorteile:
- Das Sinterverfahren ist in Branchen wie der Automobil-, Luft- und Raumfahrt- sowie der Elektronikindustrie weit verbreitet, um Beschichtungen herzustellen, die Korrosionsbeständigkeit, Wärmeisolierung oder elektrische Leitfähigkeit bieten.
- Das Verfahren bietet Vorteile wie eine hohe Materialausnutzung, die Möglichkeit, komplexe Formen zu schaffen, und die Herstellung von Beschichtungen mit hervorragenden mechanischen Eigenschaften.
Durch die Einhaltung dieser Schritte gewährleistet das Sinterverfahren die Herstellung hochwertiger Beschichtungen, die den strengen Anforderungen moderner industrieller Anwendungen entsprechen.
Zusammenfassende Tabelle:
Schritt | Beschreibung |
---|---|
Pulverzubereitung | Aufbereitung von Material in Pulverform, oft mit Zusatzstoffen zur Verbesserung der Eigenschaften gemischt. |
Verdichtung | Verdichten des Pulvers, um Gleichmäßigkeit zu gewährleisten und Hohlräume für eine bessere Haftung zu beseitigen. |
Erhitzen & Sintern | Erhitzen des Materials unter den Schmelzpunkt, um die Partikel zu verbinden, unter Verwendung von Techniken wie LPS. |
Abkühlen | Langsam abkühlen, um die Beschichtung zu verfestigen und Risse oder Verformungen zu vermeiden. |
Nachbearbeitung | Zusätzliche Behandlungen wie Bearbeitung oder Polieren zur Leistungssteigerung. |
Anwendungen | Einsatz in der Automobil-, Luft- und Raumfahrtindustrie sowie in der Elektronik für Korrosionsbeständigkeit usw. |
Entdecken Sie, wie das Sintern Ihre Beschichtungen verbessern kann. Kontaktieren Sie noch heute unsere Experten für maßgeschneiderte Lösungen!