Die thermische Vakuumverdampfung ist eine weit verbreitete Technik bei der Herstellung von Dünnschichten, bei der ein festes Material in einer Hochvakuumumgebung erhitzt wird, bis es verdampft. Der entstehende Dampfstrom durchläuft dann die Vakuumkammer und lagert sich auf einem Substrat ab, wobei eine dünne, gleichmäßige Schicht entsteht. Bei diesem Verfahren werden durch thermische Energie atomare Bindungen im Material aufgebrochen, wodurch eine Dampfwolke entsteht, die aufgrund molekularer Potenzialunterschiede am Substrat haftet. Es ist eine Art der physikalischen Gasphasenabscheidung (PVD) und wird für seine Zuverlässigkeit und Beständigkeit bei der Herstellung hochwertiger dünner Schichten geschätzt.
Die wichtigsten Punkte werden erklärt:
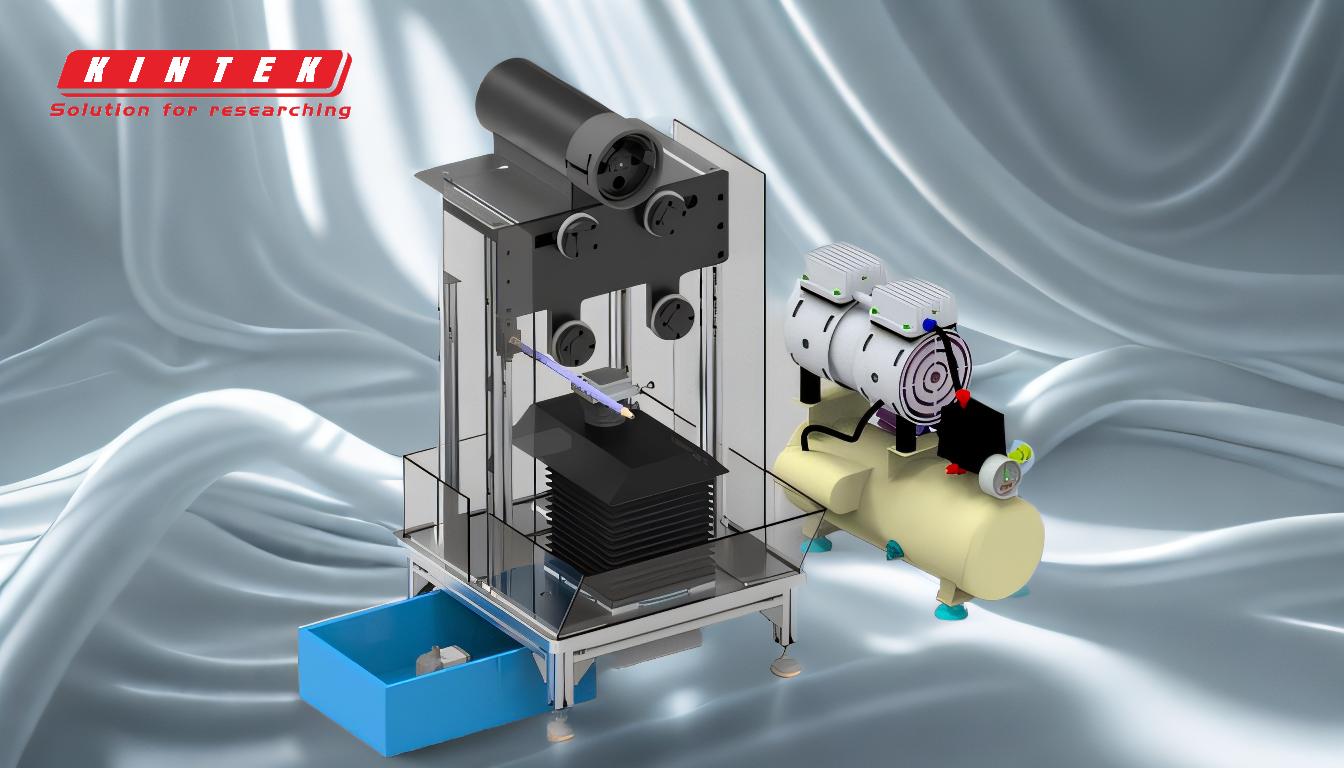
-
Definition und Zweck der thermischen Vakuumverdampfung (Vacuum Thermal Evaporation Deposition):
- Die thermische Vakuumverdampfung ist ein PVD-Verfahren (Physical Vapor Deposition), das zur Herstellung dünner Schichten auf Substraten verwendet wird.
- Dabei wird ein festes Material in einer Hochvakuumkammer erhitzt, bis es verdampft und einen Dampfstrom bildet, der sich auf dem Substrat ablagert.
-
Die Rolle des Vakuums in diesem Prozess:
- Die Vakuumumgebung ist von entscheidender Bedeutung, da sie die Wechselwirkungen zwischen den verdampften Partikeln und den Luftmolekülen minimiert und so einen sauberen und effizienten Abscheidungsprozess gewährleistet.
- Ein Hochvakuum reduziert den Druck, so dass auch bei niedrigen Dampfdrücken eine ausreichende Dampfwolke für die Abscheidung entsteht.
-
Mechanismus der Heizung:
- Das Material wird mit Hilfe eines Glühfadens, eines Schiffchens oder eines Korbes erhitzt, oft durch Widerstandserhitzung mit hohen elektrischen Strömen.
- Die Temperatur muss den Schmelzpunkt des Materials erreichen oder darüber hinausgehen, damit ein ausreichender Dampfdruck für die Verdampfung entsteht.
-
Verdampfung und Ablagerung:
- Wenn das Material erhitzt wird, bricht die Wärmeenergie die atomaren Bindungen auf und löst einzelne Atome oder Moleküle aus der festen Matrix.
- Diese verdampften Partikel bilden einen Dampfstrom, der durch die Vakuumkammer fließt und auf dem Substrat haftet.
-
Beschichtung des Substrats:
- Der Dampfstrom kondensiert auf dem Substrat und bildet einen dünnen, gleichmäßigen Film.
- Die Adhäsion des Films wird durch molekulare Potentialunterschiede zwischen dem verdampften Material und dem Substrat bestimmt.
-
Vorteile der Technik:
- Hohe Reinheit: Die Vakuumumgebung verhindert Verunreinigungen und gewährleistet eine hohe Qualität der dünnen Schichten.
- Einheitlichkeit: Das Verfahren erzeugt gleichmäßige und zuverlässige Beschichtungen.
- Vielseitigkeit: Es kann für eine Vielzahl von Materialien verwendet werden, einschließlich Metallen, Halbleitern und Dielektrika.
-
Anwendungen:
- Wird bei der Herstellung von optischen Beschichtungen, Halbleitergeräten und Solarzellen verwendet.
- Wird häufig bei der Herstellung von Dünnschichttransistoren, Sensoren und Schutzschichten verwendet.
-
Vergleich mit anderen PVD-Techniken:
- Im Gegensatz zum Sputtern oder zur gepulsten Laserabscheidung wird bei der thermischen Verdampfung ausschließlich Wärmeenergie zur Verdampfung genutzt.
- Sie ist für viele Anwendungen einfacher und kostengünstiger, kann aber bei Materialien, die einen extrem hohen Schmelzpunkt erfordern, Einschränkungen aufweisen.
-
Wichtige Überlegungen zu Ausrüstung und Verbrauchsmaterial:
- Vakuumkammer: Es muss ein hohes Vakuum aufrechterhalten werden, um eine effiziente Verdampfung und Abscheidung zu gewährleisten.
- Heizelemente: Filamente, Schiffchen oder Körbe müssen hohen Temperaturen standhalten und mit dem zu verdampfenden Material kompatibel sein.
- Substrat-Halterungen: Sollte eine gleichmäßige Einwirkung des Dampfstroms ermöglichen.
- Materielle Reinheit: Hochreine Ausgangsmaterialien sind unerlässlich, um Verunreinigungen zu vermeiden und die Filmqualität zu gewährleisten.
-
Herausforderungen und Beschränkungen:
- Materielle Beschränkungen: Einige Materialien können sich zersetzen oder benötigen zu hohe Temperaturen für die Verdunstung.
- Dickensteuerung: Das Erreichen einer präzisen Schichtdicke kann ohne fortschrittliche Überwachungssysteme eine Herausforderung sein.
- Skalierbarkeit: Während sie für kleine Anwendungen effektiv sind, kann die Erweiterung für großflächige Beschichtungen erhebliche Änderungen an den Anlagen erfordern.
Wenn die Käufer von Anlagen und Verbrauchsmaterialien diese wichtigen Punkte kennen, können sie fundierte Entscheidungen über die Komponenten und Materialien treffen, die für Systeme zur thermischen Vakuumverdampfung benötigt werden, um eine optimale Leistung und eine hochwertige Dünnschichtproduktion zu gewährleisten.
Zusammenfassende Tabelle:
Aspekt | Einzelheiten |
---|---|
Definition | Ein PVD-Verfahren zur Herstellung dünner Schichten durch Erhitzen von Materialien im Vakuum. |
Schlüsselrolle des Vakuums | Minimiert Wechselwirkungen, gewährleistet eine saubere Abscheidung und unterstützt die Verdampfung. |
Mechanismus der Heizung | Verwendet Glühfäden, Schiffchen oder Körbe mit Widerstandsheizung. |
Vorteile | Hohe Reinheit, Einheitlichkeit und Vielseitigkeit für verschiedene Materialien. |
Anwendungen | Optische Beschichtungen, Halbleiter, Solarzellen und Schutzschichten. |
Herausforderungen | Materialbeschränkungen, Dickenkontrolle und Fragen der Skalierbarkeit. |
Sind Sie bereit, Ihren Dünnschicht-Herstellungsprozess zu verbessern? Kontaktieren Sie unsere Experten noch heute für maßgeschneiderte Lösungen!