Allgemeine Überlegungen zur Magnetronzerstäubung
Wartung der Vakuumumgebung
Die Magnetronzerstäubung erfordert eine einwandfrei gewartete Vakuumumgebung, um die schädlichen Auswirkungen von Verunreinigungen in der Luft auf die Qualität der Schicht zu verhindern. Die Vakuumumgebung ist nicht nur eine Kulisse, sondern eine entscheidende Komponente, die die Integrität und Präzision des Sputterprozesses gewährleistet.
In Vakuumöfen werden die mechanischen Komponenten, wie Dichtungen und Lötverbindungen, streng gewartet, um den leckfreien Zustand des Vakuums aufrechtzuerhalten. Diese sorgfältige Wartung ist unerlässlich, da selbst kleine Leckagen das Vakuum beeinträchtigen können, was sich wiederum auf die Qualität des Endprodukts auswirkt. Das Aufspüren und Beheben dieser Lecks ist zeit- und arbeitsintensiv, was die Bedeutung einer vorbeugenden Wartung unterstreicht.
Darüber hinaus können Verunreinigungen der Ofeneinbauten aus verschiedenen Quellen stammen, darunter Restgase und Partikel, die bei Wartungsarbeiten in das System eindringen können. Solche Verunreinigungen können zu uneinheitlichen Filmeigenschaften führen und machen gründliche Reinigungs- und Validierungsprotokolle erforderlich, um sicherzustellen, dass die Vakuumumgebung makellos bleibt.
Aspekt der Wartung | Wichtigkeit |
---|---|
Integrität der Dichtung | Gewährleistet leckagefreies Vakuum; entscheidend für die Aufrechterhaltung des Betriebsvakuumniveaus. |
Hartlötverbindungen | Erfordern regelmäßige Inspektion und Wartung, um Lecks zu vermeiden. |
Innere Teile des Ofens | Muss frei von Verunreinigungen gehalten werden, um die Filmqualität zu erhalten. |
Zusammenfassend lässt sich sagen, dass die Wartung der Vakuumumgebung ein Eckpfeiler des Magnetron-Sputterprozesses ist. Sie erfordert akribische Aufmerksamkeit für Details und strenge Präventivmaßnahmen, um die Produktion hochwertiger Schichten zu gewährleisten.
Kontrolle der Abscheidungsrate
Die Abscheidungsrate ist ein kritischer Parameter im Magnetron-Sputterprozess, der sowohl die Qualität als auch die Dicke der Schicht erheblich beeinflusst. Sie bestimmt, wie schnell das Material vom Target auf das Substrat übertragen wird, und wirkt sich damit auf die Gleichmäßigkeit, die Dichte und die endgültigen Eigenschaften der abgeschiedenen Schicht aus.
Um optimale Ergebnisse zu erzielen, muss die Abscheiderate sorgfältig kontrolliert und an die jeweiligen Bedingungen angepasst werden. Faktoren wie die Art des Zielmaterials, die gewünschte Schichtdicke und die spezifischen Eigenschaften, die für die Anwendung erforderlich sind, spielen eine Rolle bei der Bestimmung der geeigneten Abscheidungsrate. Eine höhere Abscheiderate kann beispielsweise für Anwendungen geeignet sein, die dickere Schichten erfordern, sie kann aber auch zu Problemen wie schlechter Haftung oder Ungleichmäßigkeit führen, wenn sie nicht richtig gesteuert wird.
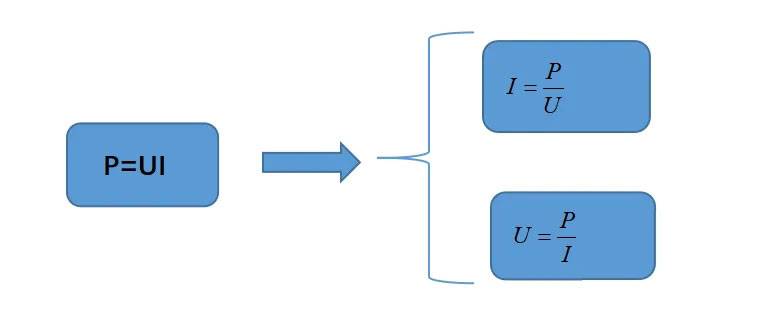
Faktor | Auswirkung auf die Abscheiderate |
---|---|
Zielmaterial | Verschiedene Materialien haben eine unterschiedliche Sputterausbeute, was sich auf die Abscheiderate auswirkt. |
Temperatur des Substrats | Höhere Temperaturen können die Schichthaftung verbessern, aber auch die Abscheiderate verändern. |
Sputterleistung | Eine höhere Leistung führt in der Regel zu einer höheren Abscheidungsrate, muss aber mit anderen Parametern abgeglichen werden. |
Zusammenfassend lässt sich sagen, dass eine genaue Kontrolle der Abscheidungsrate für die Herstellung hochwertiger PZT-Schichten unerlässlich ist. Dadurch wird sichergestellt, dass die Schicht nicht nur die geforderte Dicke aufweist, sondern auch die gewünschten Eigenschaften, wie elektrische Leitfähigkeit und mechanische Festigkeit.
Kontrolle der Sputterleistung und -zeit
Die Sputterleistung und die Sputterzeit sind kritische Parameter, die die Qualität der Schicht maßgeblich beeinflussen. Diese Faktoren müssen genauestens auf die spezifischen Eigenschaften und Anforderungen des zu verarbeitenden Materials abgestimmt werden. Die Leistung während des Sputterns beeinflusst die Energie, die auf das Zielmaterial einwirkt, was wiederum die Geschwindigkeit bestimmt, mit der die Atome ausgestoßen und auf dem Substrat abgeschieden werden. Höhere Leistungen führen im Allgemeinen zu schnelleren Abscheidungsraten, können aber auch zu erhöhter Hitze und Belastung des Substrats führen, was möglicherweise Defekte verursacht oder die gewünschten Schichteigenschaften verändert.
Umgekehrt wirkt sich die Dauer des Sputterprozesses, die Sputterzeit, direkt auf die Dicke und Gleichmäßigkeit der abgeschiedenen Schicht aus. Längere Sputterzeiten können dickere Schichten ergeben, aber sie erhöhen auch das Risiko einer Verunreinigung und die Wahrscheinlichkeit, dass eine ungleichmäßige Schichtdicke auf dem Substrat erreicht wird. Daher ist es wichtig, die Sputterleistung und die Sputterzeit aufeinander abzustimmen, um eine optimale Schichtqualität zu erreichen.
Zur Veranschaulichung der Bedeutung dieser Parameter dient die folgende Tabelle:
Sputterleistung (W) | Sputterzeit (min) | Schichtdicke (nm) | Filmqualität (Bewertung 1-10) |
---|---|---|---|
100 | 30 | 200 | 8 |
150 | 20 | 250 | 7 |
200 | 15 | 300 | 6 |
In diesem Beispiel führen eine höhere Leistung und kürzere Zeiten zwar zu dickeren Schichten, aber die Schichtqualität nimmt aufgrund erhöhter Spannung und möglicher Defekte ab. Daher ist die Auswahl der geeigneten Sputterleistung und -zeit ein differenzierter Prozess, der eine sorgfältige Berücksichtigung sowohl der Materialeigenschaften als auch der gewünschten Schichtmerkmale erfordert.
Targetmaterial und Oberflächenvorbereitung
Auswahl eines geeigneten Targetmaterials
Die Auswahl des Targetmaterials ist ein kritischer Schritt im Magnetron-Sputterprozess, der die Qualität und Leistung der entstehenden Schicht erheblich beeinflusst. Die Wahl des Targetmaterials wirkt sich direkt auf die chemische Zusammensetzung, die strukturelle Integrität und die funktionellen Eigenschaften der abgeschiedenen Schicht aus. Daher ist es wichtig, ein Targetmaterial zu wählen, das den spezifischen Anforderungen und den gewünschten Ergebnissen der Schicht entspricht.
Bei der Auswahl eines Targetmaterials müssen mehrere Faktoren berücksichtigt werden:
-
Chemische Zusammensetzung: Das Targetmaterial sollte der gewünschten chemischen Zusammensetzung des Films entsprechen. Bei der Herstellung von Blei-Zirkonat-Titanat (PZT)-Filmen beispielsweise sollte das Target idealerweise aus einer homogenen Mischung von Blei-, Zirkonium- und Titanoxiden bestehen.
-
Reinheit: Ein hoher Reinheitsgrad des Targetmaterials ist von entscheidender Bedeutung, um zu vermeiden, dass Verunreinigungen in die Folie gelangen, die deren Eigenschaften beeinträchtigen können. Verunreinigungen können zu Defekten führen, die Dichte der Folie verringern und ihre Gesamtleistung beeinträchtigen.
-
Physikalische Eigenschaften: Die physikalischen Eigenschaften des Targets, wie seine Dichte und Wärmeleitfähigkeit, können den Sputterprozess und die Eigenschaften der entstehenden Schicht beeinflussen. So führt beispielsweise ein dichteres Targetmaterial in der Regel zu einer gleichmäßigeren Abscheidungsrate.
-
Zustand der Oberfläche: Die Oberfläche des Targetmaterials muss glatt und frei von Defekten sein, um eine effiziente und gleichmäßige Zerstäubung zu gewährleisten. Um die erforderliche Ebenheit und Sauberkeit zu erreichen, kann eine Oberflächenbehandlung erforderlich sein.
In der nachstehenden Tabelle sind die wichtigsten Überlegungen zur Auswahl eines geeigneten Targetmaterials zusammengefasst:
Überlegung | Wichtigkeit |
---|---|
Chemische Zusammensetzung | Gewährleistet die gewünschten chemischen Eigenschaften der Folie. |
Reinheit | Verhindert Verunreinigungen und erhält die Qualität der Folie. |
Physikalische Eigenschaften | Beeinflusst die Sputtering-Effizienz und die Gleichmäßigkeit des Films. |
Oberflächenbeschaffenheit | Sorgt für eine effiziente und gleichmäßige Zerstäubung und vermeidet Defekte in der Schicht. |
Zusammenfassend lässt sich sagen, dass die Auswahl des Targetmaterials eine vielschichtige Entscheidung ist, die eine sorgfältige Abwägung verschiedener Faktoren erfordert, um qualitativ hochwertige und leistungsstarke Schichten zu erzielen.
Sicherstellung der Reinheit und Ebenheit der Target-Oberfläche
Die Reinheit und Ebenheit der Target-Oberfläche sind entscheidende Faktoren, die den Sputterprozess und die daraus resultierende Schichtqualität erheblich beeinflussen. Jegliche Verunreinigungen oder Unregelmäßigkeiten auf der Target-Oberfläche können zu Unregelmäßigkeiten bei der Abscheidung der PZT-Schicht führen und deren Gesamtleistung und Gleichmäßigkeit beeinträchtigen.
Um optimale Ergebnisse zu erzielen, muss die Oberfläche des Targets strengen Oberflächenbehandlungs- und Prüfprotokollen unterzogen werden. Dies beinhaltet:
-
Reinigung der Oberfläche: Beseitigung aller Verunreinigungen wie Staub, Öle oder Oxide, die die Reinheit des Targets beeinträchtigen könnten. Üblicherweise werden Techniken wie Ultraschallreinigung, chemisches Ätzen und Ionenstrahlreinigung eingesetzt.
-
Ebenheitsprüfung: Mit modernen Messgeräten wie Profilometern und Interferometern wird die Oberflächentopografie gemessen. Alle Abweichungen von der gewünschten Ebenheit müssen durch Polieren oder andere Korrekturmaßnahmen korrigiert werden.
Oberflächenbehandlung | Zweck | Übliche Techniken |
---|---|---|
Reinigung der Oberfläche | Entfernen von Verunreinigungen | Ultraschallreinigung, chemisches Ätzen, Ionenstrahlreinigung |
Ebenheitsprüfung | Prüfen der Gleichmäßigkeit der Oberfläche | Profilometer, Interferometer |
Durch die sorgfältige Einhaltung dieser Verfahren kann die Reinheit und Ebenheit der Zieloberfläche gewährleistet werden, wodurch die Qualität und Konsistenz der durch Magnetronsputtern hergestellten PZT-Schichten verbessert wird.
Kontrolle des Substrats und der Umgebung
Kontrolle der Temperatur des Substrats
Die Substrattemperatur spielt eine entscheidende Rolle bei der Bestimmung der endgültigen Eigenschaften der abgeschiedenen Schicht, wie Kristallinität, Dichte und Oberflächenrauhigkeit. Diese Eigenschaften sind ausschlaggebend für die Leistung und Funktionalität der Schicht, weshalb eine präzise Temperaturregelung ein wesentlicher Aspekt des Magnetron-Sputterprozesses ist.
Wenn die Substrattemperatur zu niedrig ist, kann die Schicht eine schlechte Kristallinität und eine geringe Dichte aufweisen, was zu einer erhöhten Oberflächenrauheit führt. Umgekehrt kann eine zu hohe Temperatur zu unerwünschten Phasenveränderungen oder sogar zu einer thermischen Schädigung des Substrats führen. Daher muss die Temperatur sorgfältig auf die spezifischen Eigenschaften und Anforderungen des aufzubringenden Materials abgestimmt werden.
Bei Blei-Zirkonat-Titanat-Schichten (PZT) beispielsweise kann die optimale Substrattemperatur je nach der gewünschten Phasenstruktur und den ferroelektrischen Eigenschaften erheblich variieren. Normalerweise werden Temperaturen zwischen 400°C und 600°C verwendet, um die gewünschte Perowskit-Phase und eine optimale piezoelektrische Reaktion zu erreichen.
Um eine präzise Steuerung zu gewährleisten, sind moderne Sputtersysteme häufig mit fortschrittlichen Temperaturüberwachungs- und -steuerungsmechanismen ausgestattet, z. B. mit Infrarotthermometern und PID-Reglern. Diese Instrumente ermöglichen Echtzeitanpassungen und gewährleisten, dass die Substrattemperatur während des gesamten Abscheidungsprozesses im optimalen Bereich bleibt.
Temperaturbereich | Eigenschaften des Films |
---|---|
< 400°C | Schlechte Kristallinität, niedrige Dichte, hohe Rauhigkeit |
400°C - 600°C | Gewünschte Perowskitphase, optimale piezoelektrische Reaktion |
> 600°C | Mögliche Phasenveränderungen, thermische Schäden |
Zusammenfassend lässt sich sagen, dass die Steuerung der Substrattemperatur ein kritischer Parameter im Magnetron-Sputterprozess ist, der sich direkt auf die Qualität und Leistung der abgeschiedenen Schicht auswirkt. Eine ordnungsgemäße Temperaturregelung stellt sicher, dass die Schicht die erforderlichen Spezifikationen erfüllt und ihre allgemeine Funktionalität verbessert.
Sicherstellung der Vakuum- und Atmosphärenkontrolle
Das Sputtering-Verfahren zur Herstellung von Blei-Zirkonat-Titanat-Schichten (PZT) reagiert sehr empfindlich auf die Umgebungsbedingungen. Um optimale Ergebnisse zu erzielen, muss er in einer sorgfältig kontrollierten Hochvakuumumgebung durchgeführt werden. Diese strenge Anforderung ist nicht verhandelbar, da sie sich direkt auf die Integrität und Leistung der PZT-Schichten auswirkt.
In einer Hochvakuumumgebung wird durch das Fehlen von atmosphärischen Gasen das Risiko einer Verunreinigung erheblich reduziert. Partikel in der Luft, Feuchtigkeit und andere Verunreinigungen können Defekte in die Folie einbringen und ihre strukturellen und elektrischen Eigenschaften beeinträchtigen. Durch die Aufrechterhaltung des Vakuums werden diese potenziellen Verunreinigungen effektiv eliminiert, so dass eine makellose Abscheidungsoberfläche gewährleistet ist.
Außerdem geht die Kontrolle der atmosphärischen Bedingungen über die bloße Aufrechterhaltung des Vakuums hinaus. Es geht auch darum, Oxidation zu verhindern, die die chemische Zusammensetzung der PZT-Schicht verändern kann. Oxidation kann zu Veränderungen in der Stöchiometrie der Schicht führen, was sich auf ihre ferroelektrischen und piezoelektrischen Eigenschaften auswirkt. Daher ist die Aufrechterhaltung einer kontrollierten Atmosphäre von entscheidender Bedeutung, um die gewünschten chemischen und physikalischen Eigenschaften des PZT-Films zu bewahren.
Um diese Hochvakuumumgebung zu erreichen und aufrechtzuerhalten, werden moderne Vakuumsysteme eingesetzt. Diese Systeme umfassen hocheffiziente Pumpen, Leckdetektoren und Drucksensoren, die zusammenarbeiten, um das erforderliche Vakuumniveau aufrechtzuerhalten. Die regelmäßige Überwachung und Kalibrierung dieser Systeme ist unerlässlich, um eine kontinuierliche und zuverlässige Vakuumkontrolle zu gewährleisten.
Zusammenfassend lässt sich sagen, dass die Kontrolle des Vakuums und der Atmosphäre ein entscheidender Aspekt des Magnetron-Sputterprozesses zur Herstellung von PZT-Schichten ist. Sie schützt nicht nur vor Verunreinigung und Oxidation, sondern gewährleistet auch die Konsistenz und Qualität der abgeschiedenen Schicht. Diese sorgfältige Kontrolle ist ein Eckpfeiler des gesamten Prozesses und bildet die Grundlage für die erfolgreiche Herstellung von Hochleistungs-PZT-Schichten.
Kontrolle der Gleichmäßigkeit
Gleichmäßigkeit ist eine kritische Eigenschaft dünner Schichten, insbesondere im Zusammenhang mit der Herstellung von Blei-Zirkonat-Titanat (PZT)-Schichten durch Magnetron-Sputtern. Das Erreichen einer gleichmäßigen Schichtabscheidung ist für die Gewährleistung einer gleichmäßigen Leistung und Zuverlässigkeit über das gesamte Substrat hinweg von entscheidender Bedeutung. Diese Gleichmäßigkeit wird in erster Linie durch eine sorgfältige Kontrolle des Sputterprozesses erreicht, der mehrere Schlüsselparameter und -techniken umfasst.
Erstens spielen die Positionierung und Ausrichtung sowohl der Sputterquelle als auch des Substrats eine entscheidende Rolle für eine gleichmäßige Schichtabscheidung. Die Sputterquelle, in der Regel ein Targetmaterial, sollte in einem optimalen Abstand zum Substrat platziert werden, um sicherzustellen, dass die aus dem Target ausgestoßenen Atome oder Partikel gleichmäßig über die Oberfläche verteilt werden. Außerdem muss der Winkel, in dem diese Teilchen auf das Substrat treffen, sorgfältig kontrolliert werden, um eine Richtungsabhängigkeit des Abscheidungsprozesses zu vermeiden.
Zweitens kann der Einsatz fortschrittlicher Techniken wie der Substratrotation die Gleichmäßigkeit erheblich verbessern. Durch die Drehung des Substrats während des Sputterprozesses wird die Schicht gleichmäßiger abgeschieden, wodurch die Auswirkungen örtlicher Schwankungen in der Leistung der Sputterquelle abgeschwächt werden. Diese Methode stellt sicher, dass jeder Teil des Substrats eine gleichmäßige Materialmenge erhält, was zu einer gleichmäßigeren Endschicht führt.
Steuerungsparameter | Auswirkung auf die Gleichmäßigkeit |
---|---|
Position der Sputtering-Quelle | Sorgt für eine gleichmäßige Verteilung der Partikel |
Winkel des Substrats | Verhindert Richtungsfehler bei der Abscheidung |
Drehung des Substrats | Verbessert die gleichmäßige Verteilung des Materials |
Zusammenfassend lässt sich sagen, dass das Erreichen der Gleichmäßigkeit bei der Abscheidung von Dünnschichten eine Kombination aus präziser Steuerung der Sputterquelle und des Substrats sowie den strategischen Einsatz von Techniken wie der Substratrotation erfordert. Diese Maßnahmen tragen gemeinsam zur Herstellung hochwertiger, gleichmäßiger PZT-Schichten bei, die für die vorgesehenen Anwendungen unerlässlich sind.
Prozessüberwachung und Nachbehandlung
Überwachung und Einstellung der Sputterleistung
Die Sputterleistung ist ein kritischer Parameter im Magnetron-Sputterprozess, der die Dicke und Zusammensetzung der abgeschiedenen Schicht maßgeblich beeinflusst. Die Leistung wirkt sich direkt auf die Energie der Ionen aus, die das Targetmaterial beschießen, was wiederum die Geschwindigkeit bestimmt, mit der das Material ausgestoßen und auf dem Substrat abgeschieden wird. So führt eine höhere Sputterleistung in der Regel zu schnelleren Abscheidungsraten, kann aber auch zu einer erhöhten Rauheit und Ungleichmäßigkeit der Schicht führen, wenn sie nicht richtig gesteuert wird.
Um eine optimale Schichtqualität zu gewährleisten, ist es wichtig, die Sputterleistung dynamisch zu überwachen und anzupassen. Dazu werden fortschrittliche Überwachungssysteme eingesetzt, die Echtzeitdaten zu Leistung, Abscheideraten und Schichteigenschaften liefern können. Durch die Korrelation dieser Messgrößen können die Bediener die Sputterleistung feinabstimmen, um die gewünschten Schichteigenschaften zu erreichen. Weicht beispielsweise die Schichtdicke von der Zielvorgabe ab, kann die Sputterleistung angepasst werden, um dies auszugleichen und eine gleichmäßige Schichtdicke auf dem gesamten Substrat zu gewährleisten.
Auch die Zusammensetzung der Schicht kann durch die Sputterleistung beeinflusst werden. Unterschiedliche Leistungen können dazu führen, dass verschiedene Elemente in einem Multikomponenten-Target in unterschiedlichem Maße zerstäubt werden, was zu Veränderungen in der Stöchiometrie der Schicht führt. Daher ist eine präzise Steuerung der Sputterleistung erforderlich, um die gewünschte chemische Zusammensetzung der Schicht zu erhalten. Dies ist besonders wichtig bei der Herstellung komplexer Oxidschichten wie Blei-Zirkonat-Titanat (PZT), bei denen das richtige Verhältnis von Blei, Zirkonium und Titan entscheidend ist, um die gewünschten elektrischen und mechanischen Eigenschaften zu erhalten.
Zusammenfassend lässt sich sagen, dass es bei der Überwachung und Einstellung der Sputterleistung nicht nur darum geht, die Abscheidungsrate zu kontrollieren, sondern auch darum, das richtige Gleichgewicht zwischen Dicke, Gleichmäßigkeit und Zusammensetzung der Schicht zu erreichen. Diese dynamische Steuerung gewährleistet, dass das Endprodukt die strengen Anforderungen für Anwendungen in der Elektronik, Optik und anderen High-Tech-Bereichen erfüllt.
Nachbehandlung von Folien
Nachbehandlungsprozesse sind entscheidende Schritte bei der Herstellung von Blei-Zirkonat-Titanat (PZT)-Folien, um deren Eigenschaften zu verbessern und eine langfristige Stabilität zu gewährleisten. Diese Behandlungen umfassen häufigGlühen undOxidierendie dazu dienen, die Mikrostruktur der Schicht zu verfeinern und ihre mechanischen und elektrischen Eigenschaften zu verbessern.
Glühen
Beim Glühen wird die Folie auf eine bestimmte Temperatur erhitzt und dann langsam abgekühlt. Dieses Verfahren kann:
- Verbesserung der Kristallinität: Durch die Förderung des Wachstums größerer, gleichmäßigerer Kristalle kann das Glühen die strukturelle Integrität der Folie erheblich verbessern.
- Spannungen vermindern: Innere Spannungen in der Folie können abgebaut werden, was zu einem stabileren und haltbareren Material führt.
- Verbesserung der elektrischen Eigenschaften: Die Dielektrizitätskonstante und die ferroelektrischen Eigenschaften der Folie können durch kontrolliertes Tempern optimiert werden.
Oxidieren
Bei der Oxidation wird die Schicht einer sauerstoffreichen Umgebung ausgesetzt, was Folgendes bewirkt
- Stabilisierung der Oxidschicht: Durch eine gleichmäßige und stabile Oxidschicht an der Oberfläche der Folie können Probleme wie Delamination und Degradation im Laufe der Zeit verhindert werden.
- Verbesserung der chemischen Beständigkeit: Eine oxidierte Oberfläche ist weniger anfällig für chemische Angriffe und macht die Folie in verschiedenen Umgebungen robuster.
- Kontrolle der Oberflächenrauhigkeit: Die Oxidation kann dazu beitragen, Unregelmäßigkeiten auf der Folienoberfläche zu glätten und so die Gesamtqualität und Leistung der Folie zu verbessern.
Sowohl das Glühen als auch das Oxidieren sind bei der Nachbehandlung von entscheidender Bedeutung, da sie nicht nur unmittelbare Qualitätsprobleme beheben, sondern auch zur langfristigen Leistung und Zuverlässigkeit der Folie beitragen.
Qualitätskontrolle und Prüfung
Die vorbereiteten Folien werden einer strengen Qualitätskontrolle und -prüfung unterzogen, um sicherzustellen, dass sie die strengen Anforderungen erfüllen, die für die vorgesehenen Anwendungen erforderlich sind. Dieser Prozess umfasst mehrere Aspekte, die jeweils sorgfältig geprüft werden, um die Integrität und Leistung der Folien zu gewährleisten.
Schlüsselparameter für die Qualitätskontrolle
-
Morphologie der Oberfläche: Die Oberfläche der Folie wird unter hochauflösenden Mikroskopen untersucht, um etwaige Mängel wie Risse, Nadellöcher oder Unebenheiten zu erkennen. Dieser Schritt ist von entscheidender Bedeutung, da Oberflächenmängel die Funktionalität der Folie erheblich beeinträchtigen können.
-
Messung der Schichtdicke: Die Dicke der Folie wird mit Präzisionsinstrumenten wie Ellipsometern oder Profilometern gemessen. Eine gleichbleibende Dicke ist entscheidend für einheitliche elektrische und mechanische Eigenschaften der gesamten Folie.
-
Analyse der Zusammensetzung: Die chemische Zusammensetzung der Folie wird mit Techniken wie Röntgenbeugung (XRD) und energiedispersiver Röntgenspektroskopie (EDS) analysiert. Auf diese Weise wird sichergestellt, dass die Zusammensetzung der Folie der gewünschten Stöchiometrie entspricht, was für die beabsichtigte Verwendung entscheidend ist.
-
Elektrische Eigenschaften: Elektrische Tests, einschließlich Messungen des spezifischen Widerstands, der Kapazität und der Dielektrizitätskonstante, werden durchgeführt, um die Leistung der Folie in elektrischen Anwendungen zu bewerten. Diese Eigenschaften werden direkt von der Struktur und Zusammensetzung der Folie beeinflusst.
Prüfmethoden und -geräte
Parameter | Prüfmethode | Verwendetes Instrument |
---|---|---|
Morphologie der Oberfläche | Mikroskopie | Rasterelektronenmikroskop (SEM) |
Dickenmessung | Optische und mechanische Techniken | Ellipsometer, Profilometer |
Analyse der Zusammensetzung | Spektroskopische Techniken | Röntgenbeugung (XRD), EDS |
Elektrische Eigenschaften | Elektrische Messungen | LCR-Meter, Impedanz-Analysator |
Durch die systematische Bewertung dieser Parameter stellt der Qualitätskontrollprozess sicher, dass jeder Film die vorgegebenen Standards erfüllt, wodurch die Zuverlässigkeit und Leistung des Endprodukts gewährleistet wird.
Kontinuierliche Verbesserung und Umweltaspekte
Kontinuierliche Verbesserung und Optimierung
Die Vorbereitung von Dünnschichten ist ein iterativer Prozess, der eine kontinuierliche Überprüfung und Verfeinerung erfordert, um optimale Ergebnisse zu erzielen. Der Aufbereitungsprozess, von der anfänglichen Einrichtung bis zum Endprodukt, erfordert eine sorgfältige Analyse und Verbesserung, um sowohl die Qualität als auch die Effizienz der Folie zu verbessern. Diese kontinuierliche Verbesserung umfasst mehrere Schlüsselaspekte:
-
Überwachung der Prozessparameter: Regelmäßige Überwachung und Anpassung kritischer Parameter wie Sputterleistung, Abscheidungsrate und Substrattemperatur sind unerlässlich. Diese Parameter haben einen erheblichen Einfluss auf die Eigenschaften der Schicht, einschließlich ihrer Dicke, Gleichmäßigkeit und Gesamtqualität.
-
Technologische Upgrades: Der Einsatz fortschrittlicher Technologien und Methoden kann zu erheblichen Verbesserungen führen. So kann beispielsweise der Einsatz automatisierter Systeme zur Echtzeitüberwachung und -steuerung menschliche Fehler reduzieren und die Prozesskonsistenz verbessern.
-
Qualitätskontrolle: Strenge Maßnahmen zur Qualitätskontrolle sind unerlässlich. Dazu gehören umfassende Tests der Oberflächenmorphologie, der Dicke, der Zusammensetzung und der elektrischen Eigenschaften der Folie, um sicherzustellen, dass sie den erforderlichen Standards entspricht.
-
Feedback-Schleifen: Die Einrichtung effektiver Rückkopplungsschleifen ermöglicht die schnelle Erkennung und Korrektur von Abweichungen von den gewünschten Ergebnissen. Dieser iterative Ansatz gewährleistet, dass jeder Zyklus der Folienvorbereitung besser ist als der letzte.
-
Umweltaspekte: Neben der Verbesserung der Filmqualität ist es auch wichtig, die Umweltauswirkungen des Vorbereitungsprozesses zu berücksichtigen. Die Einführung energieeffizienter Methoden und die Minimierung von Abfällen können zu einem nachhaltigeren Produktionszyklus beitragen.
Durch die kontinuierliche Analyse und Verfeinerung dieser Aspekte kann der Aufbereitungsprozess optimiert werden, um qualitativ hochwertige Folien mit verbesserter Effizienz und geringerem ökologischen Fußabdruck zu erzeugen.
Umweltschutz und Energieverbrauch
Bei der Suche nach nachhaltigen Praktiken innerhalb des Magnetron-Sputterprozesses muss besonderes Augenmerk auf den Umweltschutz und den Energieverbrauch gelegt werden. Die herkömmlichen Sputterverfahren sind zwar effektiv, haben aber oft erhebliche umwelt- und energiebezogene Nachteile. Um diese abzumildern, ist der Einsatz umweltfreundlicherer und energieeffizienterer Präparationsverfahren nicht nur eine Empfehlung, sondern eine Notwendigkeit.
Ein Ansatz, um dies zu erreichen, ist die Optimierung der Sputtering-Parameter. Durch die Feinabstimmung von Faktoren wie Sputterleistung, Abscheidungsrate und Substrattemperatur lässt sich der Gesamtenergiebedarf des Prozesses verringern. So können beispielsweise niedrigere Sputterleistungen eingesetzt werden, ohne die Qualität der Schicht zu beeinträchtigen, wodurch Energie gespart wird. Darüber hinaus kann der Einsatz fortschrittlicher Vakuumtechnologien dazu beitragen, die Umwelt sauberer zu halten, indem die Freisetzung von schädlichen Gasen und Partikeln in die Atmosphäre minimiert wird.
Darüber hinaus spielt die Auswahl der Materialien eine entscheidende Rolle für die ökologische Nachhaltigkeit. Die Wahl von Materialien, die weniger giftig sind und eine geringere Umweltbelastung aufweisen, kann die Umweltfreundlichkeit des Prozesses erheblich verbessern. Dadurch wird nicht nur die Umwelt geschützt, sondern auch die Einhaltung der immer strengeren Umweltvorschriften gewährleistet.
Zusammenfassend lässt sich sagen, dass das Hauptaugenmerk beim Magnetronsputtern zwar auf der Qualität und Leistung der PZT-Schicht liegt, dass aber die Einbeziehung von Umwelt- und Energieaspekten in den Vorbereitungsprozess ebenso wichtig ist. Dieser ganzheitliche Ansatz stellt sicher, dass die Fortschritte in der Schichttechnologie mit den allgemeinen Zielen des Umweltschutzes und der Nachhaltigkeit in Einklang gebracht werden.
Kontaktieren Sie uns für eine kostenlose Beratung
Die Produkte und Dienstleistungen von KINTEK LAB SOLUTION werden von Kunden auf der ganzen Welt anerkannt. Unsere Mitarbeiter helfen Ihnen gerne bei allen Fragen weiter. Kontaktieren Sie uns für eine kostenlose Beratung und sprechen Sie mit einem Produktspezialisten, um die am besten geeignete Lösung für Ihre Anwendungsanforderungen zu finden!