Die PVD-Beschichtung (Physical Vapor Deposition) ist ein Verfahren, bei dem ein festes Material im Vakuum verdampft und auf ein Substrat aufgebracht wird, um eine dünne, haltbare und funktionelle Schicht zu bilden. Bei diesem Verfahren werden verschiedene Gase verwendet, darunter Inertgase wie Argon und reaktive Gase wie Sauerstoff, Stickstoff und Methan. Diese Gase spielen eine entscheidende Rolle bei der Erzeugung der gewünschten Beschichtungseigenschaften. Inerte Gase wie Argon werden verwendet, um eine chemisch unreaktive Atmosphäre aufrechtzuerhalten, während reaktive Gase mit Metallatomen interagieren und Verbindungen wie Metalloxide, Nitride und Karbide bilden. Das Ergebnis sind Beschichtungen mit erhöhter Härte, Verschleißfestigkeit und anderen funktionellen Eigenschaften. Das PVD-Verfahren wird in einer Vakuumkammer bei extrem niedrigem Druck durchgeführt, wodurch eine saubere und kontrollierte Umgebung für hochwertige Beschichtungen gewährleistet wird.
Die wichtigsten Punkte erklärt:
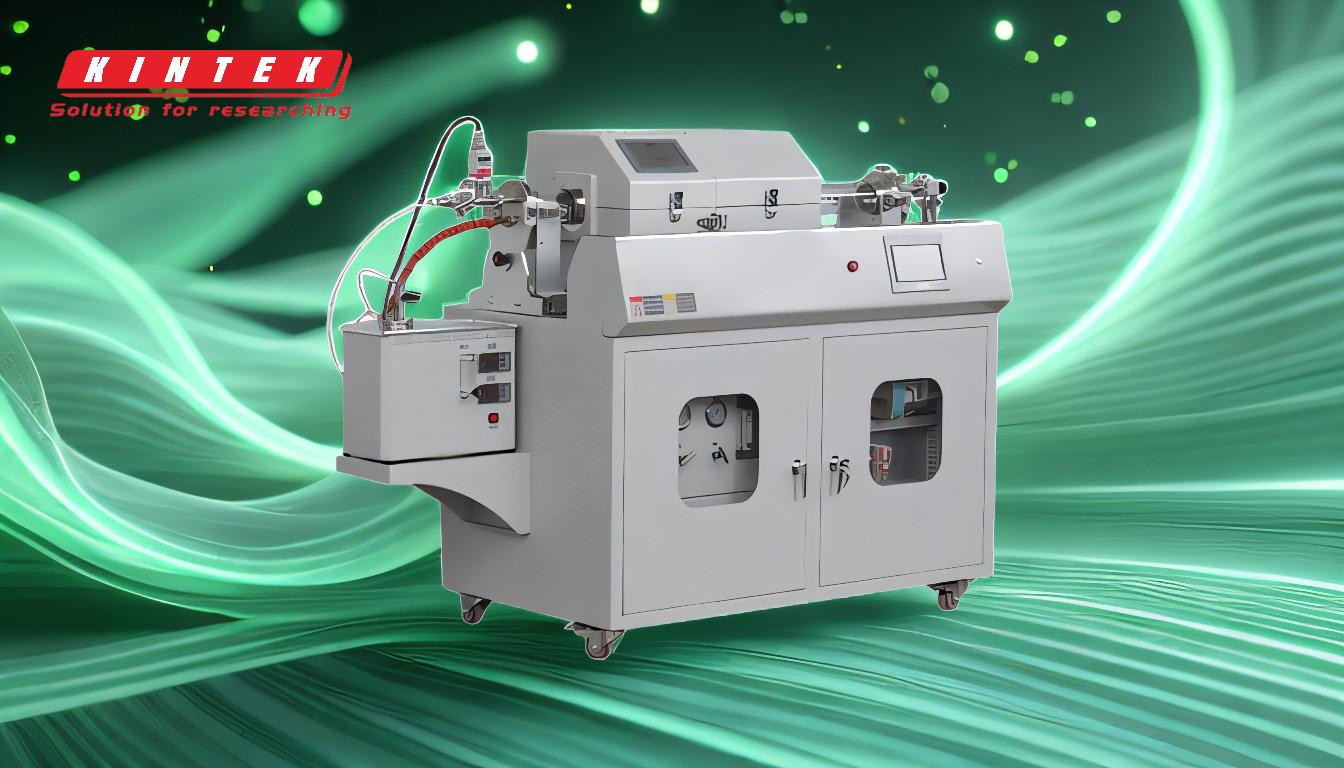
-
Inertgase bei der PVD-Beschichtung:
- Argon ist das in der PVD-Beschichtung am häufigsten verwendete Inertgas.
- Es schafft eine chemisch unreaktive Atmosphäre, die für die Aufrechterhaltung der Reinheit des Beschichtungsprozesses unerlässlich ist.
- Argon wird auch beim Sputtern verwendet, wo es das Zielmaterial ionisiert und beschießt, so dass es verdampft.
- Durch die Verwendung von Inertgasen wird sichergestellt, dass das verdampfte Material während des Beschichtungsprozesses nicht kontaminiert wird.
-
Reaktive Gase bei der PVD-Beschichtung:
- Sauerstoff, Stickstoff und Methan sind die wichtigsten reaktiven Gase, die bei der PVD-Beschichtung verwendet werden.
-
Diese Gase reagieren während der Transportphase des PVD-Verfahrens mit Metallatomen und bilden Verbindungen wie z. B.:
- Metalloxide (z. B. Titandioxid, Aluminiumoxid), wenn Sauerstoff verwendet wird.
- Metallnitride (z. B. Titannitrid, Chromnitrid), wenn Stickstoff verwendet wird.
- Metallkarbide (z. B. Titankarbid, Wolframkarbid), wenn Methan verwendet wird.
- Diese Verbindungen verbessern die funktionellen Eigenschaften der Beschichtung, wie Härte, Verschleißfestigkeit und Korrosionsbeständigkeit.
-
Die Rolle der Gase im PVD-Prozess:
- Verdampfung: Das Zielmaterial wird mit Techniken wie Elektronenstrahl, Ionenbeschuss oder kathodischem Lichtbogen verdampft. Inertgase wie Argon werden häufig zur Unterstützung dieses Schritts verwendet.
- Transport: Das verdampfte Material wird durch die Vakuumkammer transportiert. In diesem Stadium werden reaktive Gase zugeführt, um die Zusammensetzung des verdampften Materials zu verändern.
- Kondensation: Das verdampfte Material kondensiert auf dem Substrat und bildet eine dünne, fest haftende Schicht. Die reaktiven Gase sorgen für die Bildung bestimmter Verbindungen (z. B. Oxide, Nitride, Karbide), die die Eigenschaften der Beschichtung verbessern.
-
Vakuumumgebung:
- Das PVD-Verfahren findet in einer Vakuumkammer bei extrem niedrigem Druck statt (normalerweise 10^-3 bis 10^-9 Torr).
- Diese Vakuumumgebung gewährleistet, dass das verdampfte Material sauber und frei von Verunreinigungen bleibt.
- Die Niederdruckbedingungen erleichtern auch den effizienten Transport und die Abscheidung des verdampften Materials.
-
Vorteile der Verwendung von Gasen bei der PVD-Beschichtung:
- Anpassbare Beschichtungen: Durch die Auswahl bestimmter reaktiver Gase können die Zusammensetzung und die Eigenschaften der Beschichtung auf die jeweiligen Anforderungen zugeschnitten werden.
- Verbesserte Eigenschaften: Reaktive Gase ermöglichen die Bildung von harten, verschleißfesten und korrosionsbeständigen Beschichtungen.
- Vorteile für die Umwelt: PVD ist eine umweltfreundlichere Beschichtungstechnologie als herkömmliche Verfahren, da sie nur minimale Abfälle und Emissionen erzeugt.
-
Anwendungen von PVD-Beschichtungen:
- Industrielle Werkzeuge: PVD-Beschichtungen werden häufig eingesetzt, um die Haltbarkeit und Leistung von Schneidwerkzeugen, Formen und Gesenken zu verbessern.
- Luft- und Raumfahrt: Beschichtungen mit hoher Verschleißfestigkeit und thermischer Stabilität werden auf Flugzeugkomponenten aufgebracht.
- Medizinische Geräte: Biokompatible Beschichtungen werden für Implantate und chirurgische Instrumente verwendet.
- Dekorative Oberflächen: PVD-Beschichtungen bieten attraktive, dauerhafte Oberflächen für Schmuck, Uhren und architektonische Komponenten.
-
Prozessschritte, an denen Gase beteiligt sind:
- Evakuierung: Die Vakuumkammer wird evakuiert, um eine Hochvakuumumgebung zu schaffen.
- Einleiten von Gasen: Inerte und reaktive Gase werden je nach Bedarf in die Kammer eingeleitet.
- Verdampfung: Das Zielmaterial wird mit Energiequellen wie Elektronenstrahlen oder Ionenbeschuss verdampft.
- Transport und Reaktion: Reaktive Gase reagieren mit dem verdampften Material und bilden die gewünschten Verbindungen.
- Abscheidung: Das verdampfte Material kondensiert auf dem Substrat und bildet eine dünne, fest haftende Schicht.
- Spülen: Die Kammer wird mit Inertgas gespült, um Restdämpfe zu entfernen und eine saubere Umgebung zu gewährleisten.
Wer die Rolle der Gase im PVD-Beschichtungsprozess versteht, kann fundierte Entscheidungen über die Beschichtungsarten und Materialien treffen, die seinen Anforderungen am besten entsprechen. Der Einsatz von Inert- und Reaktivgasen ermöglicht die Herstellung von Hochleistungsbeschichtungen mit maßgeschneiderten Eigenschaften und macht PVD zu einer vielseitigen und wertvollen Technologie für verschiedene Branchen.
Zusammenfassende Tabelle:
Blickwinkel | Einzelheiten |
---|---|
Inerte Gase | Argon sorgt für eine chemisch unreaktive Atmosphäre und gewährleistet die Reinheit der Beschichtung. |
Reaktive Gase | Sauerstoff, Stickstoff und Methan bilden Verbindungen wie Oxide, Nitride und Karbide. |
Wichtige Eigenschaften | Erhöhte Härte, Verschleißfestigkeit und Korrosionsbeständigkeit. |
Prozess-Schritte | Verdampfung, Transport, Kondensation und Spülung. |
Anwendungen | Industriewerkzeuge, Luft- und Raumfahrt, medizinische Geräte und dekorative Oberflächen. |
Vorteile für die Umwelt | Minimale Abfälle und Emissionen, was PVD umweltfreundlich macht. |
Sind Sie bereit, Ihre Produkte mit PVD-Beschichtungen zu veredeln? Kontaktieren Sie uns noch heute um mehr zu erfahren!