Das Lichtbogenschmelzen ist ein elektrothermisches metallurgisches Verfahren, bei dem mit Hilfe eines elektrischen Lichtbogens extrem hohe Temperaturen erzeugt werden, die Metalle schmelzen, ohne ihre chemischen Eigenschaften zu verändern. Dabei wird ein Lichtbogen zwischen einer Elektrode und dem zu schmelzenden Material oder zwischen zwei Elektroden mit Hilfe eines Lichtbogenschmelzofens erzeugt. Der Ofen wandelt Hochspannung in Niederspannung und Hochstrom um, so dass der Lichtbogen sich selbst aufrechterhalten und das Metall schmelzen kann. Dieses Verfahren ist in der Industrie zum Schmelzen von Stahlschrott und anderen Metallen weit verbreitet und eignet sich besonders gut für die Herstellung hochreiner Materialien im Vakuum.
Die wichtigsten Punkte werden erklärt:
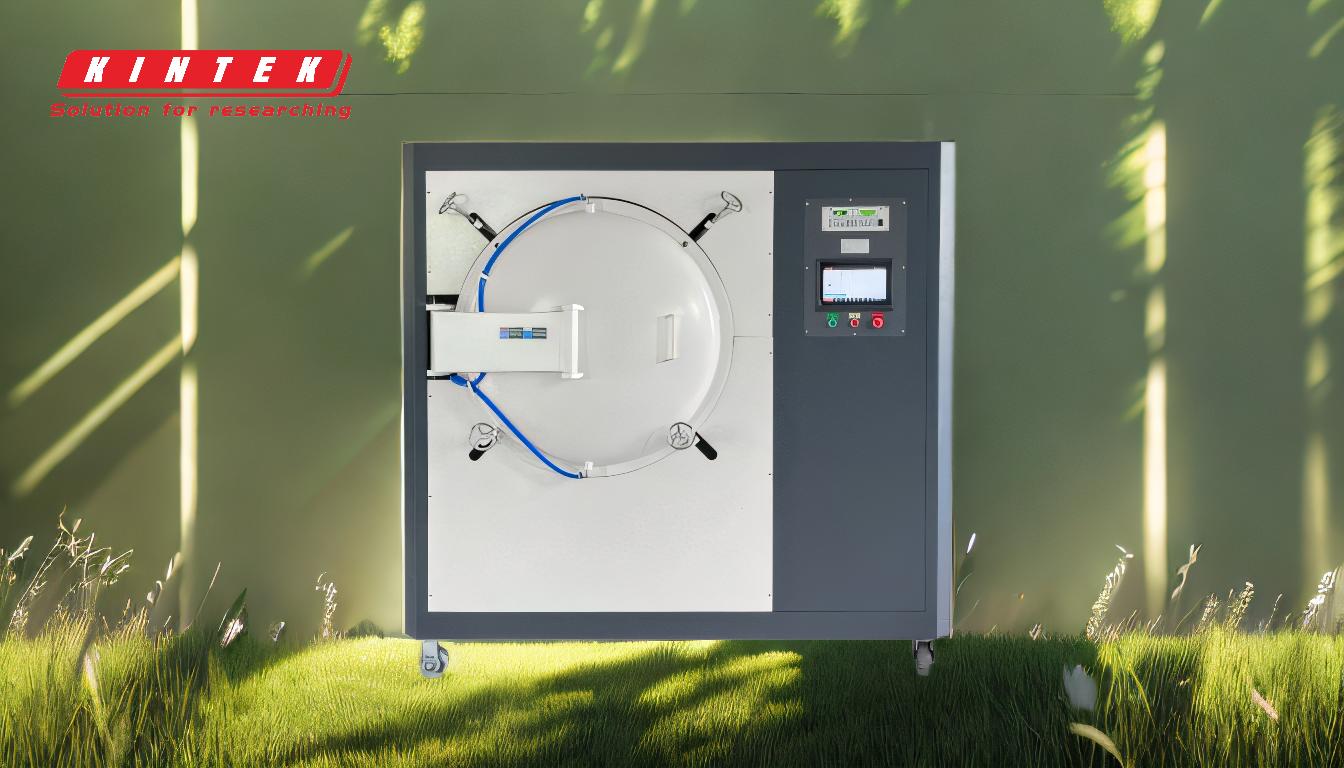
-
Definition und Zweck des Lichtbogenschmelzens:
- Das Lichtbogenschmelzen ist ein elektrothermisches Verfahren, bei dem ein elektrischer Lichtbogen zum Schmelzen von Metallen verwendet wird.
- Der Hauptzweck ist das Schmelzen von Metallen, wie z. B. Stahlschrott, ohne deren chemische Zusammensetzung zu verändern.
- Es wird häufig in der metallurgischen Industrie zur Herstellung hochwertiger Metalle und Legierungen verwendet.
-
Bestandteile eines Lichtbogenschmelzofens:
- Die Hauptkomponente ist das Elektroschweißgerät, das Standardspannungen (220 V oder 380 V) in Niederspannung und Hochstrom umwandelt.
- Der Ofen erzeugt einen elektrischen Lichtbogen, eine sich selbst erhaltende Entladung, die durch den momentanen Kurzschluss des positiven und negativen Pols ausgelöst wird.
- Der Lichtbogen ist ein thermisches Plasma mit extrem hohen Temperaturen, das in der Lage ist, Metalle effizient zu schmelzen.
-
Wie der Lichtbogenschmelzprozess funktioniert:
- Der Prozess beginnt mit der Erzeugung eines Lichtbogens zwischen der Elektrode und dem Material oder zwischen zwei Elektroden.
- Der Lichtbogen erzeugt starke Hitze, die so hoch ist, dass das Metall schmilzt.
- Das geschmolzene Metall wird dann gesammelt oder weiterverarbeitet, je nach Anwendung.
-
Stadien des Vakuum-Lichtbogenschmelzverfahrens:
- Vorbereitungsphase: Der Ofen und die Materialien werden vorbereitet, und die Anlage wird auf ihre Funktionstüchtigkeit überprüft.
- Vakuumstufe: Der Ofen wird evakuiert, um eine Vakuumumgebung zu schaffen, die zur Herstellung hochreiner Metalle beiträgt.
- Schmelzphase: Der Lichtbogen wird erzeugt, und das Metall wird unter kontrollierten Bedingungen geschmolzen.
- Absaugung Gussprobenbühne: Das geschmolzene Metall wird zur weiteren Analyse oder Verwendung in Formen oder Proben gegossen.
- Endphase: Der Prozess ist abgeschlossen, und der Ofen wird abgekühlt und für den nächsten Zyklus gereinigt.
-
Vorteile des Lichtbogenschmelzens:
- Hohe Reinheit: Die Vakuumumgebung minimiert die Verunreinigung, was zu hochreinen Metallen führt.
- Kontrolliertes Schmelzen: Das Verfahren ermöglicht eine genaue Kontrolle der Schmelzbedingungen und gewährleistet eine gleichbleibende Qualität.
- Vielseitigkeit: Das Lichtbogenschmelzen kann für eine breite Palette von Metallen und Legierungen eingesetzt werden und ist damit ein vielseitiges Verfahren in der Metallurgie.
-
Anwendungen des Lichtbogenschmelzens:
- Recycling von Metallschrott: Das Lichtbogenschmelzen wird häufig für das Recycling von Stahlschrott und anderen Metallen verwendet.
- Produktion von Legierungen: Sie wird zur Herstellung hochwertiger Legierungen mit spezifischen Eigenschaften verwendet.
- Forschung und Entwicklung: Das Verfahren wird auch in Labors zur Entwicklung neuer Materialien und zur Untersuchung metallurgischer Eigenschaften eingesetzt.
-
Vergleich mit anderen Schmelzverfahren:
- Schmelzen: Im Gegensatz zum Schmelzen, bei dem Metalle durch chemische Reaktionen aus Erzen gewonnen werden, liegt der Schwerpunkt beim Lichtbogenschmelzen auf dem Schmelzen der bereits gewonnenen Metalle.
- Induktives Schmelzen: Beim Induktionsschmelzen wird die Wärme durch elektromagnetische Induktion erzeugt, während beim Lichtbogenschmelzen ein elektrischer Lichtbogen verwendet wird.
- Suspensionsschmelzen: Beim Suspensionsschmelzen werden Materialien in einem schwebenden Zustand geschmolzen, während beim Lichtbogenschmelzen in der Regel ein stationäres Schmelzbad vorliegt.
Wenn man diese Schlüsselpunkte versteht, kann man die Effizienz und Vielseitigkeit des Lichtbogenschmelzverfahrens in verschiedenen Industrie- und Forschungsanwendungen schätzen.
Zusammenfassende Tabelle:
Hauptaspekt | Einzelheiten |
---|---|
Definition | Elektrothermisches Verfahren, bei dem ein elektrischer Lichtbogen zum Schmelzen von Metallen verwendet wird. |
Zweck | Schmilzt Metalle wie Stahlschrott, ohne deren chemische Zusammensetzung zu verändern. |
Komponenten | Elektroschweißgerät, Lichtbogenerzeugung und thermisches Plasma. |
Etappen | Vorbereitung, Vakuumerzeugung, Schmelzen, Gießen und Abkühlen. |
Vorteile | Hohe Reinheit, kontrolliertes Schmelzen und Vielseitigkeit. |
Anwendungen | Schrottrecycling, Legierungsherstellung sowie Forschung und Entwicklung. |
Vergleich | Unterscheidet sich vom Schmelzen, Induktionsschmelzen und Suspensionsschmelzen. |
Interessieren Sie sich für Lösungen zum Lichtbogenschmelzen? Kontaktieren Sie unsere Experten noch heute um mehr zu erfahren!