Die Abscheiderate bei Sputterprozessen wird durch eine Vielzahl von Faktoren beeinflusst, darunter die Eigenschaften des Zielmaterials, die während des Prozesses eingesetzten Methoden und die Leistung des Sputtersystems selbst.Das Verständnis dieser Faktoren ist entscheidend für die Optimierung der Abscheiderate und das Erreichen der gewünschten Schichtqualität.Im Folgenden werden die Schlüsselelemente, die sich auf die Abscheidungsrate auswirken, im Detail untersucht.
Die wichtigsten Punkte werden erklärt:
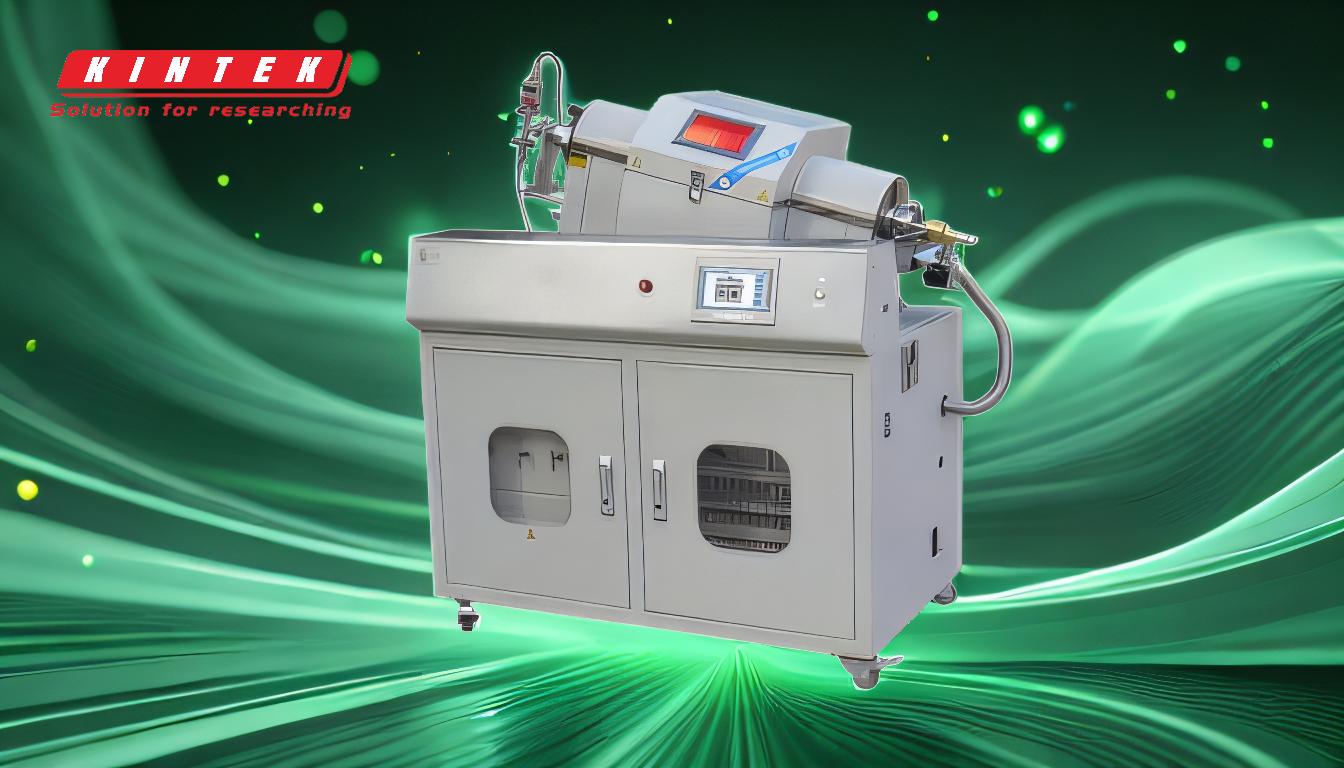
-
Eigenschaften des Zielmaterials:
- Materialzusammensetzung:Die Art des gesputterten Materials hat einen erheblichen Einfluss auf die Abscheiderate.Verschiedene Materialien haben unterschiedliche Sputtering-Ausbeuten, d. h. die Anzahl der pro einfallendem Ion aus dem Target ausgestoßenen Atome.Zum Beispiel haben Metalle im Allgemeinen eine höhere Sputterausbeute als Isolatoren.
- Reinheit und Dichte:Hochreine Targets haben in der Regel gleichmäßigere und besser vorhersehbare Abscheidungsraten.Verunreinigungen können zu Unregelmäßigkeiten im Sputterprozess führen und die Geschwindigkeit und Qualität der abgeschiedenen Schicht beeinträchtigen.
- Zustand der Oberfläche:Auch die Oberflächenrauheit und -reinheit des Zielmaterials kann die Abscheiderate beeinflussen.Eine glattere und sauberere Oberfläche führt in der Regel zu einer gleichmäßigeren und höheren Abscheiderate.
-
Prozess-Methoden:
- Sputtering Power:Die dem Sputtersystem zugeführte Leistung wirkt sich direkt auf die Abscheiderate aus.Höhere Leistungen erhöhen die Energie der Ionen, die das Target beschießen, was zu einer höheren Sputterausbeute und damit zu einer höheren Abscheiderate führt.
- Gasdruck und -zusammensetzung:Die Art und der Druck des Sputtergases (in der Regel Argon) spielen eine entscheidende Rolle.Ein optimaler Gasdruck gewährleistet einen effizienten Ionenbeschuss, während Abweichungen entweder zu einer unzureichenden Zerstäubung oder einer übermäßigen Streuung der zerstäubten Atome führen können.
- Temperatur des Substrats:Die Temperatur des Substrats kann die Mobilität der abgeschiedenen Atome beeinflussen, was sich auf die Wachstumsrate und die Qualität der Schicht auswirkt.Höhere Temperaturen verbessern im Allgemeinen die Beweglichkeit der Atome, was zu einer besseren Schichtqualität führt, aber möglicherweise die Abscheidungsrate beeinträchtigt.
-
Leistung des Sputtering-Systems:
- Magnetisches Feld Konfiguration:Bei Magnetron-Sputteranlagen wirkt sich die Magnetfeldkonfiguration auf die Plasmadichte und folglich auf die Abscheiderate aus.Ein gut optimiertes Magnetfeld kann die Ionisierung des Sputtergases verbessern, was zu einer höheren Abscheiderate führt.
- Target-zu-Substrat-Abstand:Der Abstand zwischen dem Target und dem Substrat kann die Abscheiderate beeinflussen.Ein kürzerer Abstand führt im Allgemeinen zu einer höheren Abscheiderate, da die Streuung der gesputterten Atome verringert wird, muss aber ausgeglichen werden, um eine ungleichmäßige Schichtabscheidung zu vermeiden.
- System-Vakuumpegel:Die Höhe des Vakuums in der Sputterkammer ist entscheidend.Ein hohes Vakuum reduziert das Vorhandensein von Verunreinigungen und gewährleistet eine effiziente Sputterung.Schlechte Vakuumbedingungen können zu Verunreinigungen in der Schicht und zu einer geringeren Abscheiderate führen.
Zusammenfassend lässt sich sagen, dass die Abscheiderate bei Sputterprozessen ein komplexes Zusammenspiel von Eigenschaften des Zielmaterials, Prozessmethoden und der Leistung des Sputtersystems ist.Durch eine sorgfältige Kontrolle dieser Faktoren ist es möglich, die Abscheidungsrate zu optimieren und qualitativ hochwertige Schichten zu erzielen.Das Verständnis dieser Elemente ermöglicht eine bessere Prozessgestaltung und Fehlersuche, was letztlich zu effizienteren und effektiveren Sputterverfahren führt.
Zusammenfassende Tabelle:
Faktor | Details zum Schlüssel |
---|---|
Eigenschaften des Zielmaterials | - Materialzusammensetzung:Metalle haben eine höhere Sputtering-Ausbeute als Isolatoren. |
- Reinheit und Dichte:Hochreine Targets gewährleisten konstante Abscheideraten. | |
- Oberflächenbeschaffenheit:Glattere, sauberere Oberflächen ergeben höhere Abscheideraten. | |
Prozess-Methoden | - Sputterleistung: Höhere Leistung erhöht die Abscheiderate. |
- Gasdruck und -zusammensetzung:Ein optimaler Argondruck gewährleistet eine effiziente Zerstäubung. | |
- Temperatur des Substrats:Höhere Temperaturen verbessern die Atommobilität und die Schichtqualität. | |
Leistung des Sputtering-Systems | - Magnetische Feldkonfiguration:Optimierte Felder erhöhen die Plasmadichte. |
- Abstand zwischen Ziel und Substrat:Kürzere Abstände verringern die Streuung der Atome. | |
- Systemvakuum: Hochvakuum gewährleistet effizientes Sputtern und reduziert Verunreinigungen. |
Optimieren Sie Ihren Sputterprozess noch heute - Kontaktieren Sie unsere Experten für maßgeschneiderte Lösungen!