Die Abschmelzleistung beim Schweißen wird durch mehrere Faktoren beeinflusst, darunter die Art des Schweißverfahrens, die Geräteeinstellungen, die Materialeigenschaften und die Betriebsparameter.Beim Laserstrahl-Auftragschweißen beispielsweise hängt die Abschmelzleistung von der Laserleistung, der Vorschubgeschwindigkeit und der Verfahrgeschwindigkeit ab.Beim Sputtern spielen Faktoren wie Eigenschaften des Zielmaterials, Stromstärke und Strahlenergie eine Rolle.Beim Drahtelektrodenschweißen wirken sich Variablen wie Drahtgröße, Stromstärke und Schweißposition erheblich auf die Auftragungsrate aus.Die Kenntnis dieser Faktoren hilft bei der Optimierung von Schweißprozessen im Hinblick auf Effizienz und Qualität.
Die wichtigsten Punkte erklärt:
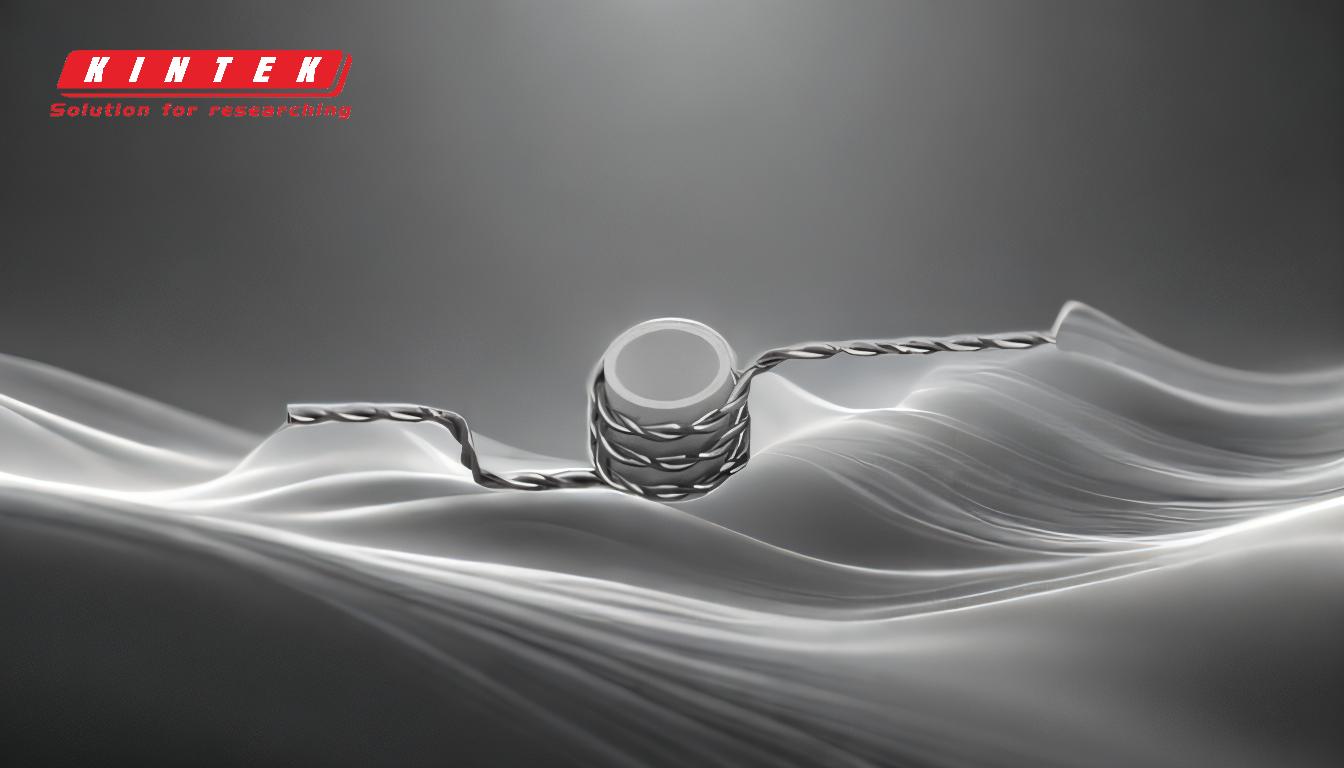
-
Laserleistung beim Laserauftragschweißen:
- Die Laserleistung wirkt sich direkt auf den Energieeintrag in das Material aus und beeinflusst die Schmelzrate und die Abscheidungseffizienz.
- Eine höhere Laserleistung erhöht in der Regel die Abscheidungsrate, muss aber ausgewogen sein, um Defekte wie Überhitzung oder Verformung zu vermeiden.
-
Vorschubgeschwindigkeiten beim Laserstrahl-Auftragschweißen:
- Die Geschwindigkeit, mit der das Material (z. B. Pulver oder Draht) in die Schweißzone zugeführt wird, wirkt sich auf die Auftragungsrate aus.
- Optimale Vorschubgeschwindigkeiten gewährleisten eine gleichmäßige Materialzufuhr ohne Unter- oder Überversorgung, was zu Defekten führen kann.
-
Verfahrgeschwindigkeit beim Laserauftragsschweißen:
- Die Verfahrgeschwindigkeit bestimmt, wie schnell sich der Laser über das Werkstück bewegt.
- Schnellere Verfahrgeschwindigkeiten können die Abscheideleistung verringern, aber die Produktivität verbessern, während langsamere Geschwindigkeiten die Abscheideleistung erhöhen, aber zu einem übermäßigen Wärmeeintrag führen können.
-
Plasmaeigenschaften bei der Plasmaabscheidung:
- Plasmatemperatur, -zusammensetzung und -dichte beeinflussen die Abscheiderate und -qualität.
- Die Überwachung dieser Parameter gewährleistet die gewünschten Materialeigenschaften und minimiert die Verunreinigung.
-
Zielmaterialeigenschaften beim Sputtern:
- Die physikalischen Eigenschaften des Zielmaterials, wie Dichte und Schmelzpunkt, beeinflussen, wie leicht es gesputtert und abgeschieden werden kann.
- Materialien mit niedrigerem Schmelzpunkt und höherer Sputterausbeute haben im Allgemeinen höhere Abscheideraten.
-
Strom und Strahlenergie beim Sputtern:
- Ein höherer Strom und eine höhere Strahlenergie erhöhen die Sputterrate, was zu höheren Abscheideraten führt.
- Eine zu hohe Energie kann jedoch das Target oder das Substrat beschädigen, so dass eine Optimierung entscheidend ist.
-
Drahtelektrodengröße beim Schweißen:
- Größere Drahtelektroden können mehr Material pro Zeiteinheit abscheiden, was die Abscheidungsrate erhöht.
- Eine 1,4 mm Drahtelektrode mit 250 Ampere hat beispielsweise eine Abscheidungsrate von 3,5 kg/Stunde in flachen oder horizontalen Positionen.
-
Stromstärke beim Schweißen:
- Eine höhere Stromstärke erhöht die Wärmezufuhr und die Schmelzrate, was zu höheren Abschmelzraten führt.
- Die richtige Wahl der Stromstärke gewährleistet einen effizienten Auftrag ohne Beeinträchtigung der Schweißqualität.
-
Position beim Schweißen:
- Die Position (z. B. flach, horizontal, vertikal, über Kopf) beeinflusst den Einfluss der Schwerkraft auf das Schmelzbad und damit die Abscheideraten.
- Flache und horizontale Positionen ermöglichen in der Regel höhere Abscheideraten als vertikale oder Über-Kopf-Positionen.
-
Materialzusammensetzung und Verunreinigung:
- Die Sicherstellung der richtigen Elementzusammensetzung im Schweißprozess ist entscheidend für das Erreichen der gewünschten Materialeigenschaften.
- Verunreinigungen können die Abschmelzleistung verringern und die Integrität der Schweißnaht beeinträchtigen, weshalb eine Überwachung unerlässlich ist.
Wenn Schweißer und Ingenieure diese Faktoren verstehen und optimieren, können sie höhere Abschmelzraten erzielen und gleichzeitig die Qualität und Effizienz der Schweißung erhalten.
Zusammenfassende Tabelle:
Faktor | Einfluss auf die Abscheiderate |
---|---|
Laserleistung (Laser Cladding) | Höhere Leistung erhöht die Abscheidungsrate, birgt aber die Gefahr von Überhitzung oder Verformung. |
Vorschubgeschwindigkeiten (Laserauftragsschweißen) | Optimale Vorschubgeschwindigkeiten gewährleisten eine gleichmäßige Materialzugabe ohne Fehler. |
Verfahrgeschwindigkeit (Laserauftragsschweißen) | Höhere Geschwindigkeiten verringern die Abscheideraten, verbessern aber die Produktivität. |
Plasma-Eigenschaften | Temperatur, Zusammensetzung und Dichte beeinflussen die Abscheidequalität. |
Eigenschaften des Zielmaterials | Niedrigere Schmelzpunkte und höhere Sputterausbeuten erhöhen die Abscheideraten. |
Strom und Strahlenergie | Höhere Energie erhöht die Sputtering-Raten, muss aber optimiert werden, um Schäden zu vermeiden. |
Größe der Drahtelektrode | Größere Drähte scheiden mehr Material pro Zeiteinheit ab, was die Abscheidungsrate erhöht. |
Stromstärke | Eine höhere Stromstärke erhöht die Wärmezufuhr und die Schmelzrate und steigert die Abscheidungsrate. |
Position beim Schweißen | Flache und horizontale Positionen ermöglichen höhere Auftragungsraten als vertikale oder Überkopfpositionen. |
Materialzusammensetzung | Die richtige Zusammensetzung gewährleistet die gewünschten Eigenschaften; Verunreinigungen verringern die Ablagerungsraten. |
Sind Sie bereit, Ihren Schweißprozess zu optimieren? Kontaktieren Sie noch heute unsere Experten für maßgeschneiderte Lösungen!