Beim DC-Sputtern liegt der erforderliche Druck typischerweise zwischen 1 bis 15 mTorr (Millitorr) abhängig von der jeweiligen Anwendung, dem Zielmaterial und den gewünschten Schichteigenschaften.Der Druck spielt eine entscheidende Rolle bei der Bestimmung der Energieverteilung der gesputterten Atome, der Plasmadichte und der Gesamtqualität der abgeschiedenen Schicht.Niedrige Drücke begünstigen hochenergetische ballistische Stöße, während höhere Drücke die Diffusionsbewegung und Thermalisierung der gesputterten Atome fördern.Der optimale Druck muss diese Effekte ausgleichen, um die gewünschte Gleichmäßigkeit, Dichte und Haftung des Films zu erreichen.
Die wichtigsten Punkte erklärt:
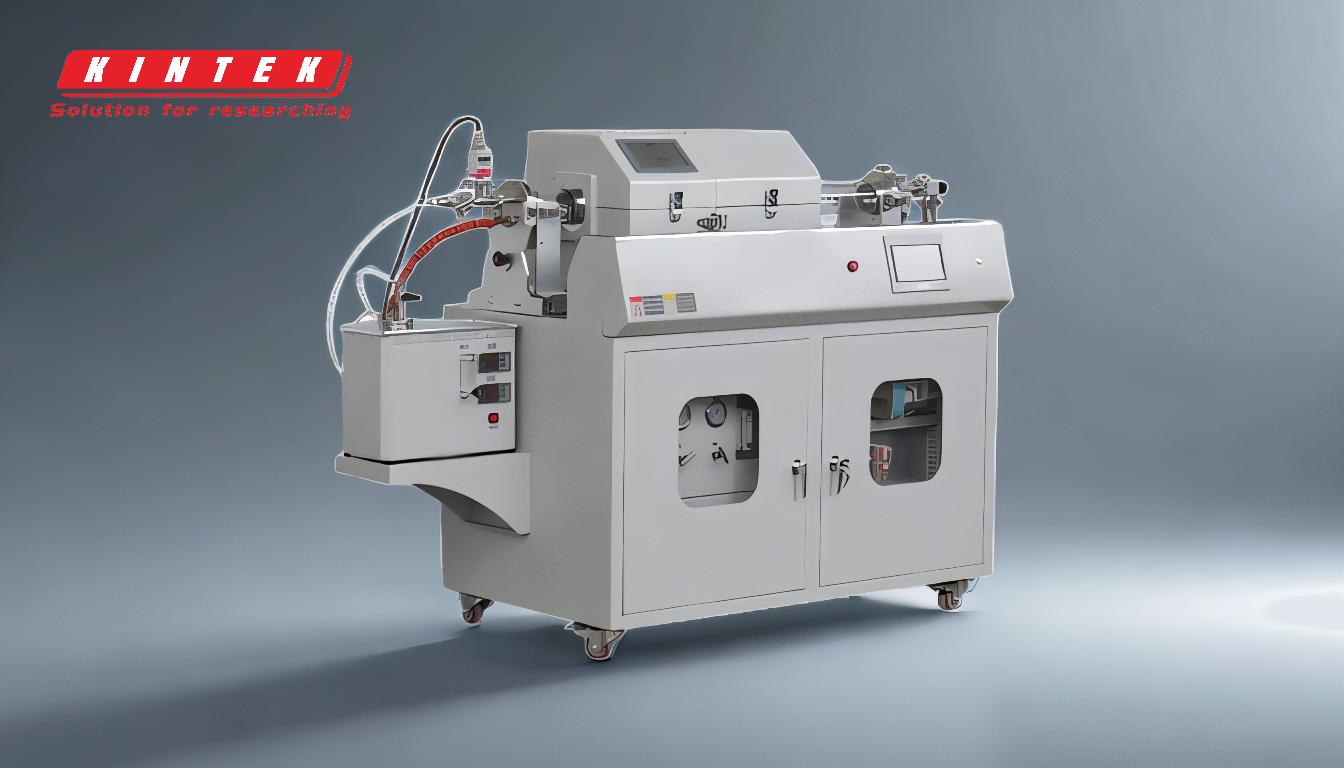
-
Druckbereich beim DC-Sputtern:
- Der typische Betriebsdruck für das DC-Sputtern beträgt 1 bis 15 mTorr .
- Niedrigere Drücke (1-5 mTorr) ermöglichen hochenergetische ballistische Stöße bei denen die gesputterten Atome mit minimalen Kollisionen direkt auf das Substrat gelangen.
- Höhere Drücke (5-15 mTorr) fördern Diffusionsbewegung bei der die gesputterten Atome mehrfach mit den Gasatomen zusammenstoßen, was zu einer eher zufälligen, thermisch bedingten Abscheidung führt.
-
Die Rolle des Drucks beim Sputtern:
- Mittlerer freier Weg:Der Druck bestimmt die mittlere freie Weglänge der gesputterten Atome.Bei niedrigerem Druck ist die mittlere freie Weglänge länger, was eine energiereiche Abscheidung ermöglicht.Bei höheren Drücken verkürzt sich die mittlere freie Weglänge, was zu einer thermischen Bewegung führt.
- Plasma-Dichte:Der Druck beeinflusst die Plasmadichte, die wiederum das Ionisierungsniveau und die Energie der gesputterten Atome beeinflusst.Die Plasmadichte kann mit der folgenden Formel berechnet werden:
- [ n_e = \left(\frac{1}{\lambda_{De}^2}\right) \times \left(\frac{\omega^2 m_e \epsilon_0}{e^2}\right)
-
] wobei (n_e) die Plasmadichte, (\lambda_{De}) die Debye-Länge, (\omega) die Kreisfrequenz, (m_e) die Elektronenmasse, (\epsilon_0) die Dielektrizitätskonstante des freien Raums und (e) die Elementarladung ist.
- Qualität des Films:Die Optimierung des Drucks ist entscheidend für das Erreichen der gewünschten Filmeigenschaften, wie Gleichmäßigkeit, Dichte und Haftung.
- Faktoren, die die Druckauswahl beeinflussen:
- Ziel Material:Verschiedene Materialien erfordern unterschiedliche Drücke, um eine optimale Sputterausbeute zu erzielen.Für schwerere Zielatome können beispielsweise höhere Drücke erforderlich sein, um einen ausreichenden Energietransfer zu gewährleisten.
-
Anforderungen an das Substrat:Die gewünschten Schichteigenschaften (z. B. Dichte, Gleichmäßigkeit) beeinflussen die Wahl des Drucks.Hochenergetische Schläge bei niedrigerem Druck sind ideal für dichte Schichten, während die thermische Abscheidung bei höherem Druck die Deckung auf komplexen Geometrien verbessert.
- Energiequelle
- :Beim DC-Sputtern werden aufgrund von Unterschieden in der Plasmaerzeugung und Ionisierungseffizienz in der Regel niedrigere Drücke als beim RF-Sputtern verwendet.
- Einfluss des Drucks auf die Sputterausbeute
-
: Die Sputterausbeute (Anzahl der pro einfallendem Ion ausgestoßenen Zielatome) hängt von der Energie der Ionen, der Masse der Zielatome und dem Einfallswinkel ab.
- Bei niedrigeren Drücken führen höhere Ionenenergien zu einer höheren Sputterausbeute, aber eine zu hohe Energie kann zu Substratschäden führen. Bei höheren Drücken kann die Sputterausbeute aufgrund von Energieverlusten durch Kollisionen abnehmen, aber die thermische Bewegung verbessert die Gleichmäßigkeit der Schicht.
- Praktische Überlegungen zur Druckregelung:
- Kammer Design:Das Vakuumsystem muss in der Lage sein, den gewünschten Druckbereich konstant zu halten.
-
Gasdurchsatz:Die Durchflussrate des Sputtergases (z. B. Argon) muss optimiert werden, um die gewünschten Druck- und Plasmabedingungen zu erreichen.
- Prozessüberwachung:Die Echtzeit-Überwachung der Druck- und Plasmaparameter gewährleistet eine gleichbleibende Folienqualität und Reproduzierbarkeit des Prozesses.
- Kompromisse bei der Druckauswahl:
Niederdruck
:Zu den Vorteilen gehören die Abscheidung mit hoher Energie, dichte Schichten und schnellere Abscheidungsraten.Zu den Nachteilen gehören mögliche Substratbeschädigungen und schlechte Abdeckung komplexer Geometrien.
Hoher Druck | :Zu den Vorteilen gehören eine gleichmäßigere Schicht und eine bessere Abdeckung auf komplexen Substraten.Zu den Nachteilen gehören geringere Abscheideraten und eine mögliche Porosität des Films. | Durch sorgfältige Auswahl und Steuerung des Drucks beim DC-Sputtern können die Hersteller den Abscheidungsprozess optimieren, um die gewünschten Schichteigenschaften für ihre spezifische Anwendung zu erzielen. |
---|---|---|
Zusammenfassende Tabelle: | Aspekt | Niederdruck (1-5 mTorr) |
Hoher Druck (5-15 mTorr) | Energieverteilung | Ballistische Stöße mit hoher Energie |
Diffusive, thermalisierte Bewegung | Gleichmäßigkeit des Films | Geringer (direkte Aufschläge) |
Höher (randomisierte Ablagerung) | Ablagerungsrate | Schneller |
Langsamer | Substratabdeckung | Schlecht bei komplexen Geometrien |
Besser bei komplexen Geometrien | Dichte der Folie | Dichter |
Potenziell porös Risiko der Beschädigung des Substrats Höher