Das RF-Sputtern ist ein Verfahren zur Abscheidung von Dünnschichten, das unter bestimmten Druckbedingungen arbeitet, um eine effiziente Ionisierung des Gases und eine effektive Zerstäubung des Zielmaterials zu gewährleisten.Der Kammerdruck liegt normalerweise zwischen 0,5 bis 10 mTorr der ein entscheidender Parameter für die Steuerung der Energieverteilung und der Bewegung der gesputterten Ionen ist.Dieser Druckbereich ermöglicht ein Gleichgewicht zwischen hochenergetischen ballistischen Stößen und niederenergetischen thermischen Bewegungen, je nach den gewünschten Abscheidungseigenschaften.Das RF-Sputtern eignet sich besonders für dielektrische Materialien und beinhaltet abwechselnde Zyklen positiver und negativer Vorspannung, um Ionenansammlungen auf isolierenden Targets zu verhindern.Das Verfahren wird von einer HF-Stromquelle angetrieben, die mit 13,56 MHz und einer Spitze-Spitze-Spannung von 1000 V arbeitet, was eine gleichmäßige Ionisierung und Abscheidungsrate gewährleistet.
Die wichtigsten Punkte erklärt:
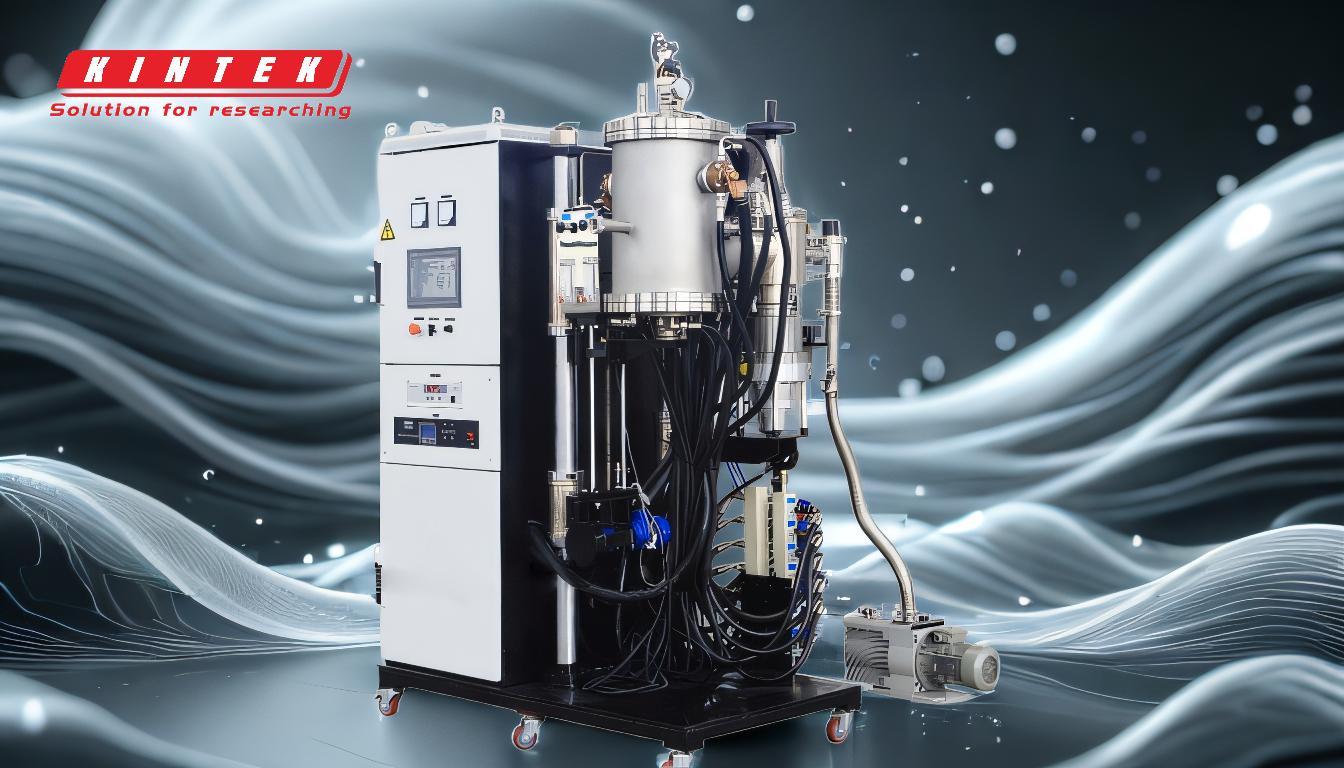
-
Druckbereich beim RF-Sputtern
- Der Kammerdruck beim RF-Sputtern liegt typischerweise im Bereich von 0,5 bis 10 mTorr .
- Dieser Druckbereich ist entscheidend für die Aufrechterhaltung der Ionisierung des Sputtergases (in der Regel Argon) und die Gewährleistung einer effizienten Zerstäubung des Zielmaterials.
- Bei niedrigeren Drücken (näher bei 0,5 mTorr) bewegen sich die gesputterten Ionen ballistisch mit hoher Energie, was zu einer direkten und energiereichen Abscheidung auf dem Substrat führt.
- Bei höheren Drücken (näher an 10 mTorr) stoßen die Ionen häufiger mit Gasatomen zusammen, was zu einer diffusiven, zufälligen Bewegung vor der Abscheidung führt.Dadurch wird die Energie der Ionen gedämpft, was zu einem thermischeren Abscheidungsprozess führt.
-
Die Rolle des Drucks bei der Energieverteilung
- Der Druck beeinflusst direkt die mittlere freie Weglänge der gesputterten Ionen, die bestimmt, wie weit ein Ion reisen kann, bevor es mit einem anderen Gasatom zusammenstößt.
- Eine niedrigere mittlere freie Weglänge (bei höherem Druck) erhöht die Wahrscheinlichkeit von Kollisionen, verringert die Energie der Ionen und fördert eine gleichmäßigere Abscheidung mit niedriger Energie.
- Eine höhere mittlere freie Weglänge (bei niedrigerem Druck) ermöglicht es den Ionen, ihre Energie beizubehalten, was zu energiereichen Stößen führt, die die Filmdichte und Haftung verbessern können.
-
Auswirkungen auf die Abscheidungseigenschaften
- Die Wahl des Drucks beeinflusst die Abscheiderate , Filmqualität und Einheitlichkeit .
- Höhere Drücke (z. B. 10 mTorr) werden häufig für die Abscheidung empfindlicher oder isolierender Materialien verwendet, da die moderierte Ionenenergie das Risiko einer Beschädigung des Substrats oder Targets verringert.
- Niedrigere Drücke (z. B. 0,5 mTorr) werden für Anwendungen bevorzugt, die dichte, hochwertige Schichten erfordern, da die hochenergetischen Ionen die Schichthaftung verbessern und die Porosität verringern.
-
Druck und Mechanismus des RF-Sputterns
- Beim RF-Sputtern werden abwechselnde Zyklen positiver und negativer Vorspannung verwendet, um Ionenansammlungen auf isolierenden Targets zu verhindern.
- Der Druck muss sorgfältig kontrolliert werden, um sicherzustellen, dass das Sputtergas ionisiert bleibt und das Targetmaterial gleichmäßig gesputtert wird.
- Im optimalen Druckbereich (0,5-10 mTorr) ionisiert die HF-Stromquelle (13,56 MHz) das Gas effektiv und erzeugt ein stabiles Plasma, das eine gleichmäßige Zerstäubung ermöglicht.
-
Vergleich mit anderen Sputtering-Techniken
- Die RF-Sputtertechnik arbeitet mit niedrigeren Drücken als einige andere Techniken, wie z. B. DC-Sputtern bei dem für leitfähige Targets höhere Drücke verwendet werden können.
- Der niedrigere Druckbereich beim HF-Sputtern ist besonders für dielektrische Materialien von Vorteil, da er die Lichtbogenbildung minimiert und eine gleichmäßige Abscheidung gewährleistet.
-
Praktische Überlegungen für Anlagenkäufer
- Bei der Auswahl von Anlagen für das HF-Sputtern ist darauf zu achten, dass das Vakuumsystem den erforderlichen Druckbereich (0,5-10 mTorr) mit hoher Präzision einhalten kann.
- Berücksichtigen Sie die Kompatibilität der Kammerkonstruktion mit dem gewünschten Druckbereich, da sich dies auf die Effizienz des Sputterprozesses auswirken wird.
- Prüfen Sie die Kostenauswirkungen des Betriebs bei niedrigeren Drücken, da das Erreichen und Aufrechterhalten eines hohen Vakuums möglicherweise fortschrittlichere Pumpsysteme erfordert.
-
Druck und Größe des Substrats
- Das RF-Sputtern wird in der Regel für kleinere Substrate verwendet, da die Kosten für die Aufrechterhaltung der erforderlichen Druck- und RF-Leistungspegel höher sind.
- Der Druckbereich muss sorgfältig für die Substratgröße optimiert werden, um eine gleichmäßige Abscheidung zu gewährleisten und Kanteneffekte oder eine ungleichmäßige Schichtdicke zu vermeiden.
-
Druck und Abscheiderate
- Die Abscheiderate beim HF-Sputtern ist im Allgemeinen niedriger als beim DC-Sputtern, was zum Teil auf den niedrigeren Druckbereich und die wechselnden Vorspannungszyklen zurückzuführen ist.
- Der kontrollierte Druck sorgt jedoch für qualitativ hochwertige Schichten und macht das HF-Sputtern ideal für Anwendungen, die präzise und gleichmäßige Beschichtungen erfordern.
Wenn man die Rolle des Drucks beim RF-Sputtern versteht, können die Käufer von Anlagen und Verbrauchsmaterialien fundierte Entscheidungen über Systemspezifikationen und Prozessparameter treffen, um optimale Ergebnisse für ihre spezifischen Anwendungen zu erzielen.
Zusammenfassende Tabelle:
Aspekt | Einzelheiten |
---|---|
Druckbereich | 0,5-10 mTorr |
Schlüsselrolle | Steuert Ionisierung, Energieverteilung und Abscheidungseigenschaften |
Niedriger Druck (0,5 mTorr) | Hochenergetische ballistische Stöße für dichte, hochwertige Filme |
Hoher Druck (10 mTorr) | Niederenergetische thermische Bewegung für empfindliche oder isolierende Materialien |
RF-Stromquelle | 13,56 MHz, 1000 V Spitze-zu-Spitze |
Anwendungen | Ideal für dielektrische Materialien und präzise, gleichmäßige Beschichtungen |
Sind Sie bereit, Ihren RF-Sputterprozess zu optimieren? Kontaktieren Sie noch heute unsere Experten für maßgeschneiderte Lösungen!